Авторы: С.В. Афанасьев, Ю.Н. Шевченко, М.В. Кравцова (Тольяттинский госуниверситет), С.П. Сергеев (ОАО «ГИАП»), К.Г. Ярославцев (ОАО «Тольяттиазот»).
Опубликовано в журнале Химическая техника №12/2016
Изотермические резервуары (ИР), используемые для хранения сжиженного аммиака, представляют собой объекты повышенной опасности, разрушение которых может привести к техногенной катастрофе.
Так, в ПО «Азот» в г. Ионаве (Литва) 20 марта 1989 г. произошла авария на изотермическом хранилище, в результате которой резервуар был оторван от днища и отброшен в сторону на 25 м. При этом оказались разрушенными железобетонный стакан и эстакада с трубопроводами, среди которых находился трубопровод с природным газом. После разрушения железобетонного ограждения сжиженный аммиак беспрепятственно разлился по территории завода, образовав озеро ядовитой жидкости с поверхностью испарения около 10 000 м2 [1], а в результате возгорания склада с нитрофоской произошло выделение ядовитых газов (аммиака, окислов азота и хлора и т.д.).
При анализе были определены две возможные основные причины этой аварии [2, 3]:
- превышение в хранилище избыточного давления;
- образование микротрещин в месте сварки цилиндра и днища резервуара.
На территории РФ имеется более 20 единиц изотермических хранилищ жидкого аммиака. Эксплуатационный срок многих ИР превышает 30 лет, следовательно, риск развития коррозии, свищей, пор, трещин основных элементов возрастает.
Конструктивно многие действующие резервуары представляют собой оболочковую конструкцию, сваренную из листов следующей толщины: цилиндрическая стенка – от 32 мм (нижний пояс) до 8,6 мм (14 пояс); плоское днище – 5,2 мм, окрайка днища – 11,2 мм; сферическая крыша (настил) – 8 и 16 мм (см. рисунок).
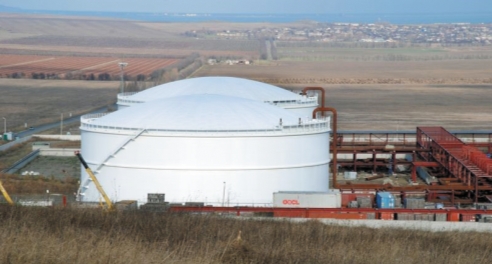
Материал: сталь E.355IFP AFNOR A.36201 (соответствует стали 16ГС по ГОСТ 5520) и сталь A131CS ASTMA.131.73 (соответствует стали ВСт3сп по ГОСТ 380).
Сложность конструкции, наличие большого количества швов, их труднодоступность для проведения обследования требует ответственного подхода к диагностическому мониторингу изотермических резервуаров.
Причины возникающих дефектов могут быть классифицированы на несколько основных групп:
- пластическая деформация, включающая движение дислокаций;
- разрушение материала, зарождение и распространение трещин;
- фазовые превращения, под которыми подразумевают мартенситное превращение, затвердевание расплава;
- разновидности коррозии (точечная коррозия, водородное охрупчивание, коррозионная усталость, коррозионное растрескивание под напряжением);
- нарушение технологии сварки и сварочные дефекты (трещины, включения и пористость).
В результате многолетнего наблюдения за эксплуатацией резервуаров удалось выявить основные дефекты, развитие которых при условии непринятия мер может привести к отказу ИГ (аварии или разрушению):
Причина | Число случаев/% |
Дефекты, обнаруженные и ликвидированные | |
при осмотре резервуаров | 63/29 |
Не обнаруженные (скрытые) дефекты, проявившиеся через некоторое время | |
после планового осмотра ИР | 61/28 |
Усталостные явления | 52/24 |
Коррозия | 30/14 |
Другие причины, включая ползучесть | 10/5 |
Как известно, риск нежелательного события является вероятностной характеристикой и рассчитывается по формуле R = PV (здесь Р – вероятность или показатель частоты нежелательного события в течение года; V – ущерб от последствий аварии, инцидента, т.е. длительность нахождения оборудования в нерабочем состоянии. Вероятность Р рассчитывается на основе многолетних наблюдений за эксплуатацией резервуаров).
Методика оценки риска соответствует требованиям РД 03-418–01 «Методические указания по проведению анализа риска опасных производственных объектов».
Наиболее вероятный и наиболее опасный сценарий – нарушение в работе агрегата компримирования аммиака, приводящее к его остановке, повышению температуры в резервуаре и росту внутреннего давления до значения, в 2–3 раза превышающего расчетное. За этим следует разрушение резервуара по двум сценариям: либо происходит обрыв анкеров при недостаточной их прочности, недопустимая деформация корпуса и разрушение сварного соединения стенки с днищем, либо (при повышенной прочности анкеров) разрушение сварного соединения стенки с крышей.
Фактическая частота аварий изотермического резервуара с одной силовой стенкой по причине роста внутреннего давления Р1 = 2,6·10–4 год–1.
Анализ показывает, что продолжение аварии с отрывом стенки наружного резервуара от днища и полным проливом аммиака во внешнюю среду невозможен при выполнении любого из двух условий:
- при своевременном вводе компрессора в работу после его остановки и прекращении дальнейшего развития аварии и/или при надежной работе предохранительных клапанов;
- при повышенной прочности анкеров.
Традиционно применяется периодическое техническое освидетельствование, включающее внутренний осмотр и гидроиспытание. Недостатками этого метода являются необходимость технической подготовки ИР к мониторингу, невозможность получения объективных и качественных результатов для оценки состояния металла при проведении внутреннего осмотра, экономические потери из-за простоя.
Объективной альтернативой периодически проводимому техническому освидетельствованию является применение средств неразрушающего контроля, использующих явление акустической эмиссии (АЭ). Этот метод позволяет проводить одновременное тестирование всего корпуса ИР с фиксацией не только самих дефектов, но и с указанием места их локализации.
Применение АЭ позволяет сократить время технических освидетельствований с одновременным повышением точности и качества прогноза возможности дальнейшей эксплуатации изотермического хранилища с определением остаточного ресурса.
Уровень развития современной компьютерной техники позволяет использовать высоконагруженные алгоритмы, обрабатывающие сигналы повышенной точности в кратчайшие сроки в режиме реального времени. «Точками» мониторинга должны быть наиболее уязвимые места, например сварочные швы. При этом необходимо использовать два вида сигналов : дискретные (для определения трещин, коррозии) и непрерывные (питтинговая коррозия, дислокационное скольжение) [4, 5].
Как в процессе эксплуатации изотермического хранилища, так и при аварийном повышении давления большая часть поверхности резервуарного стакана, кроме узких зон высотой по 0,5 м от днища и крыши, находится в слабо напряженном состоянии. Из этого следует, что контролировать нужно только узкие зоны сопряжения стенки с днищем и крышей.
Для такого контроля состояния металла достаточно разместить небольшое количество датчиков (преобразователей АЭ) равномерно по периметру наружной стенки на высоте ~0,5…1 м от днища и на таком же удалении от крыши. Это существенно сократит затраты средств на организацию мониторинга складов жидкого аммиака.
На сегодняшний день имеющаяся законодательная и нормативная база вполне достаточна для внедрения системы мониторинга промышленной безопасности на всех изотермических хранилищах сжиженных газов.
Применение комплексов мониторинга существенно повышает промышленную безопасность, эффективность эксплуатации ИР, сберегает их ресурс, увеличивает работоспособность опасных производств.
Список литературы
- https://ru.wikipedia.org/wiki/Ионава
- Бесчастнов М.В. Промышленные взрывы. Оценка и предупреждение. М.:1991. 432 с.
- Афанасьев С.В. Пожарная безопасность технологических процессов. Уч. пособие. Самара. Сам. научн. центр РАН, 2015. 520 с.
- Martin J PEACOCK .Improving the Noise Discrimination for an Ammonia Tank AE Test//30th European Conference on Acoustic Emission Testing & 7th International Conference on Acoustic Emission University of Granada. 12–15 September, 2012.
- Азаров Н.И., Богатов Н.Д., Массарский Ю.З., Пучков С.М., Разуваев И.В. Опыт обеспечения промышленной безопасности изотермических хранилищ сжиженных газов при их эксплуатации по фактическому техническому состоянию//Безопасность труда в промышленности. 2011. №5. С. 7–10.