Авторы: С.В. Афанасьев, О.С. Рощенко (ПАО «Тольяттиазот»), С.П. Сергеев (ОАО «ГИАП»), В.А. Волков (ООО «Дельта-пром инновации»)
Опубликовано на портале «Химическая техника», сентябрь 2019
Введение
На российских и зарубежных предприятиях по выпуску аммиака в технологических процессах выделения диоксида углерода из конвертированного газа, как правило, применяют водные растворы поташных и этаноламинных абсорбентов с концентрацией активного компонента до 40 % мас. [1–5]. Системы с более высокой концентрацией использовать нецелесообразно по следующим причинам: ускоряются побочные процессы, увеличивается вязкость раствора, что ухудшает смачивание абсорбционной насадки и снижается коэффициент абсорбции.
Общепринятая система очистки СО2 -содержащих смесей включает стадию абсорбции диоксида углерода в колонных аппаратах различной конструкции с последующей десорбцией и возвратом очищенного абсорбента [6–8].
Наряду с СО2 происходит поглощение и других кислых газов – сероводорода, сернистого газа [9]. Обе эти реакции обратимы и экзотермичны, при этом карбонаты этаноламина легко разлагаются при нагревании с выделением диоксида углерода, что позволяет осуществлять очистку конвертированного газа в циклическом режиме. Процесс проводят при температуре 35…50 °С и давлении около 3 МПа в насадочных или тарельчатых колоннах.
Существенным недостатком реализованного в промышленных масштабах технологического процесса является окислительная и термическая деструкция (деградация) моноэтаноламина, происходящая на стадии терморегенерации абсонта [10–12].
В процессе этаноламиновой очистки газа от СО2 выявлены многочисленные параллельные реакции, вызывающие необратимые изменения состава раствора, приводящие к потерям абсорбента. В качестве побочных продуктов методом ЯМР идентифицированы 1-(2-оксиэтил) имидазолидон-2, 1–(2-оксиэтил) этилендиамин. Наряду с ними отмечено появление в эксплуатируемом абсорбенте и других соединений, в частности, N,N/-ди-(2–гидроксиэтил)-мочевины, щавелевой и муравьиной кислот [13–15].
Их образование вызывает коррозионное разрушение оборудования в определённых условиях, особенно при высоких степенях насыщения кислыми газами [16]. Подобно растворам аммиака, они негативно действуют на медь, цинк и их сплавы. В кипящих водных растворах МЭА малоуглеродистые стали также подвергаются коррозии под действием СО2. Присутствие в растворах этаноламинов посторонних примесей увеличивает скорость коррозии стальных аппаратов и трубопроводов. В связи с этим необходимо применять возможно более чистый моноэтаноламин и систематически подвергать очистке поглотительный раствор путём его перегонки в присутствии щёлочи. При накоплении примесей в абсорбенте проблема решается его заменой свежим МЭА.
Образовавшийся отход достаточно опасен для окружающей среды, и его утилизацию проводят методом сжигания в специальных печах.
Аналогичные проблемы возникают и при замене моноэтаноламина на N-метилдиэтаноламин (МДЭА).
Представляло интерес разработать альтернативные экологически безопасные способы утилизации отходов этаноламинов, образующихся на агрегатах аммиака. В качестве объектов исследования взяты водные растворы моноэтаноламина и метилдиэтаноламина, проработавшие длительный срок на узле очистки диоксида углерода, содержащемся в конвертированном газе, с целью его последующего использования на других технологических установках.
Методика проведения эксперимента
Известно, что процесс получения карбамидоформальдегидных смол на основе формалина и карбамида имеет ряд особенностей из-за повышенной реакционной способности композиции на стадии кислой стадии поликонденсации. Это объясняется пониженным содержанием примесей в формальдегидсодержащем продукте, выполняющих функции буферной системы и препятствующих резкому снижению уровня рН при вводе кислого агента. По указанной причине авторами [17] был разработан и впервые реализован на практике способ получения смолы с использованием карбамидоформальдегидного концентрата марки КФК- 85 (КФК-85) – продукта конденсации раствора карбамида с газообразным формальдегидом, выпускаемый по ТУ 2223-009-00206492–07. Он предусматривает ввод небольших количеств модификатора перед загрузкой первой порции карбамида соответственно на щелочной стадии и при завершающей доконденсации. Исследования проводились по следующей методике.
В колбу вместимостью 0,5 л загружали 100 г карбамидоформальдегидного концентрата КФК-85, содержащего (60 ± 0.5) % мас. формальдегида во всех формах, (25 ± 0.2) % мас. карбамида, вода – остальное. Дополнительно вводили 22 г воды и 0,1 г модификатора. Содержимое нагревали до 40 оС и загружали первую порцию карбамида до достижения мольного соотношения карбамид: формальдегид, равного 1: 2.
Конденсационный раствор при интенсивном перемешивании нагревали до 90 оС и выдерживали 10 мин. По завершении щелочной стадии конденсации температуру реакционной смеси снижали до 80 оС и в смесь вводили 10%-ный водный раствор хлористого аммония (кислый агент) для снижения рН до 5,2 ± 0,2. Конец кислой стадии поликонденсации определяли по технологической пробе: в химический стакан с 50 мл воды, охлаждённой до 12…14 оС, прибавляли 3 мл реакционной смеси. Конденсацию прекращали после появления устойчивой мути, которой соответствует условная вязкость ~30…35 с, полученная на вискозиметре ВЗ-4 с соплом 4 мм при 20 оС. Благодаря использованию добавки модификатора время кислой стадии поликонденсации увеличивается до 15…50 мин., что позволяет избежать преждевременного перехода раствора смолы в твёрдое состояние до окончания её синтеза.
Исследование свойств синтетических олиф с добавкой аминного модификатора АМ-1 осуществляли по методикам, приведённым в ГОСТ 32389–2013. Олифы. Общие технические условия.
Эффективность разработанных поглотителей сероводорода определяли хроматографическим методом по ГОСТ 50802–95 на хроматографе «Кристалл-5000.2», с пламенно-фотохимическим детектором.
В качестве объекта исследования была выбрана безводная высокосернистая нефть плотностью 0,865 г/см3. До введения нейтрализатора содержание сероводорода в ней составляло 160 ppm. Эксперимент состоял из обширной серии опытов с пробами нефти, в которую вводили разное количество нейтрализатора. Каждую пробу перемешивали в реакционной герметичной колбе с мешалкой в течение 3 ч при комнатной температуре (25±2оС) и в углеводородной фазе определяли содержание сероводорода. Погрешность измерений не превышала ±3%.
Результаты исследования
Среди изученных соединений в качестве модификаторов синтеза карбамидоформальдегидных смол наилучшие результаты удалось достичь при использовании тетрабората натрия и аминного модификатора марки АМ-1, вырабатываемого по ТУ 2423-017-00206492–2002.
Характеристика аминного модификатора марки АМ-1
Внешний вид | Однородная вязкая жидкость от коричневого до темного цвета |
Растворимость в воде | В любом соотношении |
Доля МЭА и продуктов его превращения, мас. %, не менее | 80 |
Содержание воды, мас. %, не более | 20 |
рН, не менее | 12 |
Гарантийный срок хранения, месяцев, не менее | 6 |
Экспериментально установлено, что входящие в его состав химические продукты способны реагировать с метилольными группами с образованием метиленэфирных звеньев.
Добавка модификаторов в количестве 0,05–0,15 мас. % в расчете на 100 мас. % КФК-85 на щелочной стадии получения карбамидоформальдегидной смолы позволила свести к минимуму вероятность неконтролируемого перехода карбамидоформальдегидного олигомера в твердое состояние.
При детальном изучении данного процесса было установлено, что роль тетрабората натрия и других соединений сводится не только к стабилизации кислотно-основного равновесия в реакционной смеси. Согласно полученным экспериментальным данным, при отсутствии модификатора зависимость вязкости конденсационного раствора от продолжительности кислой стадии носит экспоненциальный характер. При этом кинетическую кривую можно условно разбить на два участка. Первый участок соответствует стадии формирования молекулярных структур определенной длины и разветвленности с высокой функциональностью по метилольным группам. Вследствие этого карбамидоформальдегидные олигомеры обладают достаточной растворимостью в воде [18–20].Второй участок кривой (стадия кислотной поликонденсации) описывает этап гелеобразования и сшивку гелевых структур в пространственно-развитую полимерную сетку. При этом наблюдается резкое уменьшение функциональности композиции по метилольным группам с потерей ее растворимости в воде.
При осуществлении процесса в присутствии буферной добавки зависимость вязкости конденсационного раствора от длительности кислой стадии существенно меняется. Наряду с увеличением продолжительности кислой стадии поликонденсации удается существенно повысить вязкость композиции, а также избежать преждевременного образования широко разветвленных нерастворимых структур (см. рисунок, табл. 1).
Другим интересным направлением утилизации отработанного моноэтаноламина является изготовление лакокрасочных материалов, в частности синтетических олиф. В указанном случае он выступает в качестве модификатора и вводится в реакционную смесь в определённом количестве на завершающей стадии процесса [21].
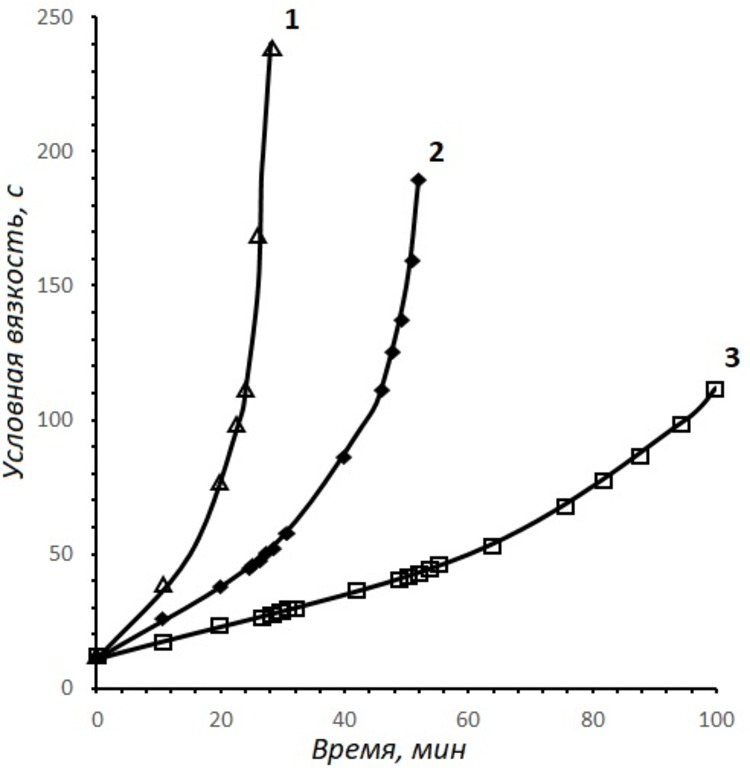
Таблица 1
Влияние количества добавленного модификатора аминного марки АМ-1 на продолжительность кислой стадии поликонденсации при синтезе клеевой карбамидоформальдегидной смолы
Количество АМ-1, введённого в карбамидоформальдегидный концентрат, мас. ч. | 0.05 | 0.07 | 0,10 | 0.15 | 0.20 |
Время кислой стадии поликонденсации, мин. | 10 | 15 | 25 | 38 | 45 |
Полученные при этом результаты иллюстрируются данными, приведенными в табл. 2.
Таблица 2
Влияние вводимого АМ-1 на свойства получаемых олиф
Наименование показателя | Значение показателя по примерам | ||||
1 | Контрольный | 3 | 4 | Контрольный | |
Олифа | Натуральная | Синтетическая | |||
Количество модификатора, мас. %, на 100 мас. % олифы | 5 | – | 4,5 | 6.5 | – |
Цвет по иодометрической шкале, мг J2/100 см3 | Менее 500 | Более 800 | |||
Условная вязкость по вискозиметру типа ВЗ-246 с диаметром сопла 4 мм при температуре (20 ± 0.5) °С, с | 20 | 16 | 24,5 | 26 | 19,2 |
Кислотное число, мг КОН | 8 | 8 | 8,2 | 8,2 | 8,1 |
Содержание нелетучих, мас. % | 56,2 | 57,0 | 56,1 | 56,0 | 56,0 |
Отстой по объему, мас. %, | 1 | ||||
Прозрачность | Полная | ||||
Время высыхания до степени 3 при температуре (20± 2) °С, ч, не более | 24 | 24 | 36 | 32 | 48 |
Как видно, частичная замена дорогостоящих реагентов аминным модификатором АМ-1 при изготовлении синтетической и натуральной олиф позволяет сохранить на высоком уровне комплекс их рабочих свойств.
Важным направлением применения отработанных этаноламинов может стать подготовка нефти перед её отправкой на нефтеперерабатывающий завод. Для эффективного управления содержанием H2S в углеводородах и в продуктах их переработки в нашей стране и за рубежом используются поглотители сероводорода (ПСВ) [21]. Нами предпринята попытка разработать эффективный ПСВ, используя отработанный абсорбент на основе метилдиэтаноламина (МДЭА) с отделения абсорбционной очистки диоксида углерода [22]. Суммарное содержание МДЭА и смолистых соединений в нём находится в диапазоне 30–35 %.
Для усиления синергического эффекта в состав композиции включен N-метилпирролидон (N-МП) в концентрации не более 10% мас. (табл. 3).
Таблица 3
Состав исследованных поглотителей сероводорода
Композиция | Концентрация ингредиентов, % мас. | Плотность,
г/см3 |
рН | Температура застывания,
оС, не выше |
||||
МДЭА | КФК-85 | этанол | N-МП | вода | ||||
Дельта НС-1 | 37,0 | – | – | – | 63,0 | 1,088 | 8,7 | –20 |
Дельта НС-4 | 22,2 | 40.0 | – | 10 | 27.8 | 1,166 | 8,5 | –25 |
Дельта НС-5 | – | 40,0 | 60,0 | – | – | 0,975 | 7,7 | –35 |
Исследования показали, что для указанной нефти с содержанием в ней сероводорода 160 ppm расход наиболее эффективного Дельта НС-4, необходимый для достижения в ней концентрации Н2S в 20 ppm, составляет 1,29 кг/т очищаемой нефти.
Поскольку нефти отличаются по содержанию сероводорода, и такой показатель не является универсальным, расход ПСВ необходимо относить не к количеству нефти, а к количеству растворённого в ней сероводорода. В этом случае он составит 9,3 г/г (грамм ПСВ на грамм сероводорода) для достижения его содержания в 20 ppm. В случае полной нейтрализации это количество должно быть увеличено на 0,1 г «Дельта НС- 4».
Основные результаты и выводы
В результате проведённого исследования разработаны эффективные способы переработки токсичных отходов этаноламинов производства аммиака и сведено к минимуму их негативное воздействие на окружающую среду:
Создан аминный модификатор карбамидоформальдегидных смол марки АМ-1, позволяющий на стадии их синтеза регулировать реакционную способность и предотвратить преждевременное отверждение.
Показана возможность использования отработанного МЭА при получении олиф, что обеспечивает замену дорогостоящих плёнкообразующих и снижает тем самым себестоимость готового продукта.
Предложена высокоэффективная композиция на основе отхода метилдиэтаноламина для очистки нефти от сероводорода.
Список литературы
- Rochelle G. T. // Science. 2009. V. 325. P. 1652–
- Новицкий Э.Г., Василевский В.П., Васильева В.И. и др.// ЖПХ. 2018. Т. 91. № 5. С. 700–708.
- Bailey B. W., Feron P. H. M. // OGST. 2005. V. 60. P. 461–
- Liang Z., Rongwong W., Liu H. et al. // Int. J. Greenh. Gas Con. 2015. V. 40. P. 26–
- Sreenivasulu B., Gayatri D. V., Sreedhar I., Raghavan K. V. // Renewable Sustainable Energy Rev. 2015. V. 41. P. 1324–
- Mangalapally H. P., Notz R., Asprion N. et al. // Int. J. Greenh. Gas Con. 2012. 8. P. 205–216.
- Abu-Zahra M. R. M., Niederer J. P. M., Feron P. H. M., Versteeg G. F. // Int. J. Greenh. Gas Con. 2007. V. 1. P. 135–
- Touhara H., Okazaki S., Okino F. et al. // J. Chem. Thermodyn. 1982. V. 14. P. 145–156.
- Davis J., Rochelle G. // Energy Procedia. 2009. V. 1. P. 327–
- Dumee L., Scholes C., Stevens G., Kentish S. // Int. J. Greenh. Gas Con. 2012. V. 10. P. 443–
- Бутина Н.М., Широкова Г.С.// Химическая промышленность. 2006. № 8. С. 17–19.
- Chi S., Rochelle G. T. // Ind. Eng. Res. 2002. V. 41. P. 4178–4186.
- Voice A. K., Rochelle G. T. // Int. J. Greenh. Gas Con. 2013. V. 12. P. 472–
- Рощенко О.С.//Химическая промышленность сегодня. 2011.№12. С.21–25.
- Заболоцкий В. И., Гнусин Н. П., Письменский В. Ф., Омельченко Ю. Н. // ЖПХ. 1982. Т. 55. № 5. С. 1105–1110.
- Moser P., Schmidt S., Stahl K. // Energy Procedia. 2011. V. 4. P. 473–479.
- Пат. РФ 2418008 (опубл. 2011). Способ получения карбамидоформальдегидного концентрата.
- Nair B.R., Francis D.J. // Polumer.1983. №24. P. 626–630.
- Sebenik A., Osredkar U., Zigon M., Vizovisek I. // Angew. Chem. 1982. №102. P. 81–85.
- Kumlin K., Simonson R. // Angew. Chem. 1978. №72. P. 67–74.
- Пат. РФ 2370508. Нейтрализатор сероводорода и способ его использования.
- Афанасьев С.В., Волков В.А., Турапин А.Н., и др.// Нефть. Газ. Новации. 2014. №4. С.99–102.