Автор: Е.В. Бычков (НГТУ им. Р.Е. Алексеева).
Опубликовано в журнале Химическая техника №4/2018
Задачи энергосбережения и повышения энергоэффективности топливно-энергетического комплекса (ТЭК) России [1–3] предписывают на регулярной основе обеспечивать реализацию комплексных программ реконструкции и технического перевооружения объектов с целью повышения эффективности существующих технологических установок [4–6]. Выполнение этих программ позволит снизить энергоемкость ТЭК за счет применения современного энергетического оборудования, сократить эмиссию парниковых газов при использовании высокотехнологических систем с газотурбинными установками (ГТУ), повысить надежность и снизить технологические потери при транспортировке на значительные расстояния [2, 7].
В этой связи основными задачами реконструкции объектов ТЭК являются, в том числе, поддержание наивысшего технического уровня техники с максимально возможными энергетическими характеристиками по использованию энергоисточников, производительности, надежности и экологичности работы компрессорных станций (КС) во всех режимах, а также обеспечение энергосберегающих режимов, технологий и алгоритмов работы газоперекачивающих агрегатов (ГПА) с повышенным КПД [8–11].
Выбор энергопривода и повышение его энергоэффективности
Основными критериями научно и технически обоснованного выбора приводных систем для ГПА являются [2, 12]следующие:
- высокая надежность и безаварийность с прогнозированием технического состояния [13–16], поскольку КС являются объектами повышенной опасности с большими ущербами от аварий;
- энергосбережение при минимальных эксплуатационных затратах и расходах на техническое обслуживание и ремонт (ТОиР);
- минимальное воздействие возможных выбросов на окружающую среду.
В качестве приводов ГПА на КС используются газовые турбины (стационарные, авиационные, судовые) или электроприводы с мегаваттными синхронными машинами[5, 12]. В настоящее время компрессорный парк ПАО «Газпром» имеет следующую статистику установленных мощностей типов приводов: газотурбинный (ГТУ) – 87,1% и электроприводной (ЭГПА) – 12,4 %.
Основными причинами массового применения ГТУ являются распространенность топлива при перекачивании природного газа, относительная дешевизна топлива (топливного газа) в сравнении с электроэнергией, большая вариативность типоразмеров ГТУ, включая модульные компоновки, достаточно низкая квалификация обслуживающего персонала. Но при этом ГТУ имеют ряд явных недостатков: низкий КПД (не выше 38%), зависимость от загрязненности и температуры воздуха и топлива, высокий уровень шума и вибраций, большое время запуска и низкая точность регулирования, большие габариты и стоимость строительства и ТОиР.
Однако главным недостатком ГТУ, влияющим на энергоемкость транспорта и себестоимость газа у потребителей, бесспорно, является низкий КПД. Топливная составляющая затрат природного газа на его транспортировку с применением ГТУ для ГПА составляет до 11–15%всего объема его добычи, что в годовом исчислении – более 74,47 млн. м3/год или по усредненным финансовым показателям около 59,7 млрд. $/год [5].
Применение современных ЭГПА в сочетании с комбинированными парогазовыми приводными ГПА, использующими новейшими технологии энергосбережению низкопотенциального тепла выхлопных газов позволит сэкономить на КС более 890 млн. $/год, улучшить экологию и снизить себестоимость транспортировки природного газа.
Резервы повышения эффективности ГТУ с применением ORC-технологий
Как показывает статистика [5,17–21], около 50 % топлива газотурбинных установок, используемых на существующих компрессорных станциях магистрального транспорта газа, расходуется впустую из-за ограниченности процессов преобразования и использования энергии. Утилизация отходящего тепла отработанных газов ГТУ – это наиболее экономичный метод повышения энергоэффективности КС со снижением потребления газа и значительных объемов производства электроэнергии. Установки регенерации отходящего тепла ГТУ (теплоэлектростанции) могут производить электроэнергию по технологии ORC (Organic Rankine Cycle) или органического цикла Ренкина (ОЦР). Для ORC-технологии получения электроэнергии на КС вполне достаточно отходящего тепла выхлопных газов температурой около 300°С.
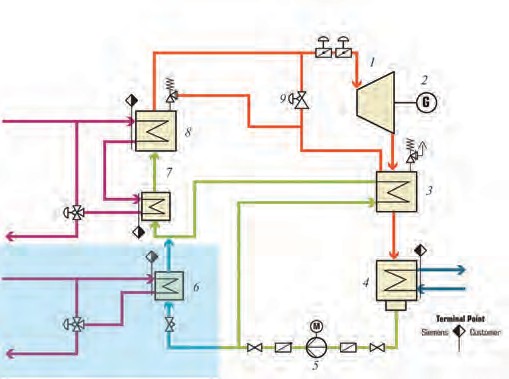
1 –турбина; 2 – генератор; 3 – рекуператор; 4 – конденсатор; 5 – насос подачи; 6 – частичный предварительный нагреватель потока; 7 – главный предварительный нагреватель поток; 8 – испаритель; 9 – клапан обхода
Принцип выработки электроэнергии по ORC-технологии заключается в следующем (рис. 1). Выхлопные газы от ГТУ через переключающий шибер (дивертор) поступают в термомасляный котел. Переключающий шибер позволяет не останавливать работу газовой турбины в случае необходимости прекращения работы системы утилизации. В первичном контуре системы применяется термическое масло, так как большинство низкокипящих рабочих тел (НРТ) являются горючими веществами, а температура выхлопных газов современных ГТУ достигает 500°С. Нагретое масло передает тепло НРТ в подогревателе и испарителе, где происходит процесс парообразования. Органическая жидкость (циклопентан) из жидкого состояния переходит в газообразное и по трубопроводу направляется в турбодетандер. Расширяющийся газ в турбодетандере приводит во вращение синхронный генератор со стабильной синхронной скоростью 1500 об/мин, который вырабатывает электроэнергию со стандартными параметрами напряжения и частоты.
Подобная ORC-система позволяет эффективно увеличить поток компримирования газа через компрессорные станции с газотурбинными ГПА путем полезного использования утилизационного тепла. При этом низкотемпературная энергия тепла выхлопных газов преобразуется в мощность, которая может использоваться для электроприводного центробежного нагнетателя (ЭГПА), работающего параллельно турбокомпрессорам с приводом от ГТУ.
КПД ORC-системы определяется, с одной стороны, температурой и давлением рабочего тела (НРТ) на входе в турбогенератор, а с другой – его параметрами в конденсаторе. Теоретические расчеты применения ORC-технологий на КС показали, что электрический КПД ORC-модуля с учетом затрат на собственные нужды находится на уровне 20%.
Преимуществами низкотемпературных ORC-технологий производства электроэнергии на КС являются повышение КПД ГТУ на 20 %, эффективность при работе в широком диапазоне нагрузок 10–100%, простота и компактность установки ORC-модуля, низкие температуры и давления по сравнению с этими параметрами паровых турбин, возможность эксплуатации в автоматическом режиме и минимум объема ТОиР.
Примеры реализации ORC-технологии на объектах ТЭК
Пилотные проекты ведущих машиностроительных фирм (Siemens, General Electric и др.) показали, что ORC-технологии обеспечивают производство до 17 МВт электроэнергии без дополнительных затрат топлива за счет рекуперации тепла выхлопных газов. Так, с июля 2013 г. в Канаде на КС «Windfall» газопровода «Alliance Pipeline’s» успешно работает ORC-система мощностью 15 МВт [5]. Подобные пять ORC-систем мощностью 17 МВт (рис. 2) внедрены на газопроводах Китая и Индонезии в 2014–2015 гг.
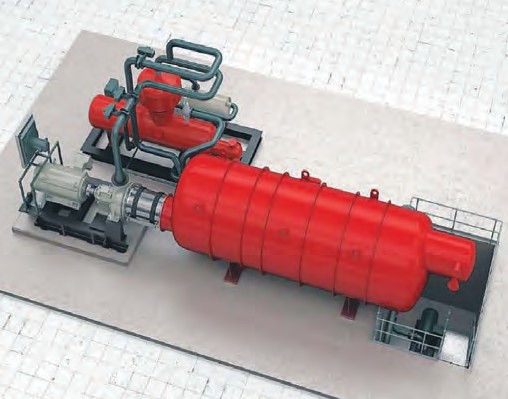
В качестве примера отечественного внедрения ORC-технологий на КС ПАО «Газпром» для ООО «Газпром трансгаз Югорск» [5] представлена типовая компоновка (рис. 3) одного из компрессорных цехов с пятьюГПА-Ц-16с существующим средним КПД 29 % (три – в работе, два – в резерве). При использовании в ГПА-Ц-16 ORC-технологий с потенциалом выработки мощности до 1500 МВт в рамках предприятия возможно дополнительное применение ЭГПА-12,5 вместо одного ГТУ-ГПА, что позволяет согласовать компрессорную мощность с гидравлическими условиями и пропускной способностью магистрального газопровода.
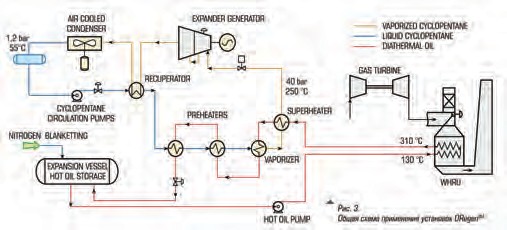
Предложены три варианта реализации схем, изображенные на рис. 4. Изготовители ORC-модулей – компания «ORMAT» и ПАО «Сумское НПО».
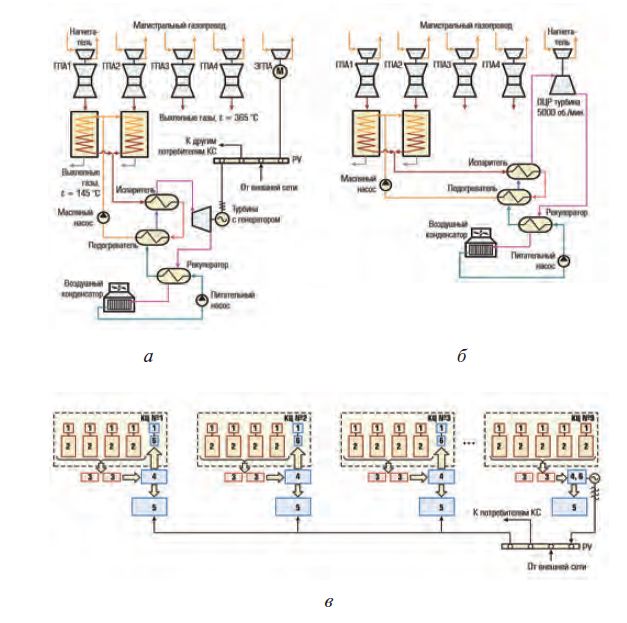
а – УТЭК для одного цеха с заменой ГПА на ЭГПА после замены сменных проточных частей турбокомпрессора НЦ-16/76-1,44 на НЦ-16/76-1,35;б – работа УТЭК на нагнетатель; в – комбинированная выработка механической и электрической энергии; 1 – нагнетатель; 2 – ГТД; 3 – термомасляный котел-утилизатор; 4 – теплообменное оборудование ОЦР-установки; 5 – воздушный котел-охладитель; 6 – турбина ОЦР
Расчеты мощности от утилизации тепла с двух ГПА-16-Ц проведены при 100%-ной нагрузке, температуре наружного воздуха 15°С и давлении 760 мм. рт. ст. – температура выхлопных газов 357°С, расход газа 102 кг/с. В результате энтальпии выхлопных газов на входе (выходе) составляют 632 кДж/кг (409 кДж/кг при 145°С), а суммарная мощность выхлопа двух ГТУ с учетом КПД котла 0,95 равна 43,2 МВт. КПД брутто ORC-модуля на клеммах генератора 0,25 и выработанная электрическая мощность с учетом собственных нужд составляет 10,8 МВт.
Экспериментальные исследования, проведенные на объектах ТЭК, показали корректность теоретических расчетов эффективности ORC-технологий, и целесообразность их внедрения. Модернизация технологического оборудования обеспечивает:
- при замене одного ГТУ-ГПА ORC-модулем мощностью 8,2…12,5 МВт – экономию более 30 000 тыс. м3природного газа в год;
- оптимизацию энергопотребления КСс существенным снижением (на 22–23%) основного показателя энергоемкости транспорта газа – удельного расхода газа на выработку 1 кВт;
- снизить стоимость энергокомплекса на 20–25 % при приводе ГПА от ORC-турбины.
Список литературы
- Титов В.В. Разработка АСУ автономными энергетическими установками//Автоматизация в промышленности. 2009. №4. С. 35–37.
- Крюков О.В. Энергоэффективные электроприводы ГПА на базе интеллектуальных систем управления и мониторинга// Дис. … д-ра техн. наук. М.: АО «Корпорация ВНИИЭМ». 2015.
- Серебряков А.В.О новых возможностях технологий Smart Grid//Электрооборудование: эксплуатация и ремонт. 2013. №2. С. 47–48.
- Milov V.R., Suslov B.A. Intellectual management decision support in gas industry//Automation and Remote Control. 2011. Т. 72. №5. С. 1095–1101.
- Пужайло А.Ф. и др. Энергосбережение и автоматизация электрооборудования компрессорных станций//Н. Новгород: Вектор ТиС. 2010. 570 с.
- Крюков О.В. Интеллектуальные электроприводы с IT-алгоритмами//Автоматизация в промышленности. 2008. №6. С. 36–39.
- Краснов Д.В. Перспективы применения преобразователей частоты для регулирования производительности электроприводных ГПА//Газовая промышленность. 2014. №6 (707). С. 86–89.
- Крюков О.В. Регулирование производительности электроприводных газоперекачивающих агрегатов преобразователями частоты//Компрессорная техника и пневматика. 2013. №3. С. 21.
- Аникин Д.А., Рубцова И.Е., Киянов Н.В. Проектирование систем управления электроприводными ГПА//Газовая промышленность. 2009. №2. С. 44–47.
- Крюков О.В. Частотное регулирование производительности электроприводных ГПА//Электрооборудование: эксплуатация и ремонт. 2014. №6. С. 39–43.
- Крюков О.В. Анализ моноблочных конструкций электрических машин для ГПА//Машиностроение: сетевой электронный научный журнал. 2015. Т. 3. №4. С. 53–58.
- Kryukov O.V. Intelligent electric drives with IT algorithms//Automation and Remote Control. 2013. Т. 74. №6. С. 1043–1048.
- Милов В.Р., Шалашов И.В. Процедуры прогнозирования и принятия решений системе технического обслуживания и ремонта//Автоматизация в промышленности. 2010. №8. С.47–49.
- Серебряков А.В., Васенин А.Б. Диагностика электромеханической части энергетических установок//Електромеханiчнi I енергозберiгаючi системи. 2012. №3 (19). С. 549–552.
- Серебряков А.В. Метод и система принятия решений по прогнозированию технического состояния электроприводных газоперекачивающих агрегатов//Электротехнические системы и комплексы. 2015. №4 (29). С. 35–38.
- Serebryakov A.V. A system of online diagnostics of the technical condition of wind power plants//Russian Electrical Engineering. 2015. T. 86. №4. C. 208–212.
- Бабичев С.А., Захаров П.А. Мониторинг технического состояния приводных электродвигателей ГПА//Контроль. Диагностика. 2009. №7. С. 33–39.
- Степанов С.Е., Плехов А.С. Принципы автоматического управления возбуждением синхронных машин газокомпрессорных станций//Автоматизация в промышленности. 2010. №6. С. 29–31.
- Серебряков А.В., Васенин А.Б. Нечеткие модели и алгоритмы управления энергетическими установками//В сб.: Материалы конференции «Управление в технических, эргодических, организационных и сетевых системах». 2012. С. 467–469.
- Степанов С.Е., Титов В.Г. Встроенные системы мониторинга технического состояния электроприводов для энергетической безопасности транспорта газа//Энергобезопасность и энергосбережение. 2012. №2. С. 5–10.
- Серебряков А.В. Интеллектуальные энергетические установки для автономных систем электроснабжения//Н. Новгород: НГТУ, 2014. 135с.