Авторы: А.В. Волков, А.Г. Парыгин, А.А. Вихлянцев (НИУ «МЭИ»).
Опубликовано в журнале Химическая техника №10/2018
Уровень развития промышленности в настоящее время требует постоянной модернизации производимого насосного оборудования: совершенствования его конструкции и технологии изготовления, а также повышения энергоэффективности и конкурентоспособности на мировом рынке. В рамках импортозамещающей политики эти тенденции имеют особую актуальность для нефтегазовой и химической отрасли, поскольку доля эксплуатируемого зарубежного оборудования в ней довольно высока и в зависимости от сегмента рынка варьируется от 30 до 63%. Так, согласно статистике Tebiz Group, в различных технологических циклах нефтехимии и нефтепереработки преимущественно используются насосы производства Германии и Швейцарии (KSB, Friatec–Rheinhutte, Sulzer) – 19%, Китая – 16%, США (Worthington, Lewis pumps) – 14%, Дании (DESMI, Grundfos) – 14%, Украины (ООО «ТТ» Харьковский механический завод) – 12% и других стран – 25%.
Класс энергоэффективности – характеристика продукции, во многом отражающая ее конкурентоспособность на мировом рынке. В промышленно развитых странах Европы необходимость производства энергоэффективного насосного оборудования закреплена на законодательном уровне. Свое отражение эта потребность нашла в виде европейского стандарта EN16480:2016, согласно которому эффективность насосов с подачей до 1000 м3/ч определена для пяти конструктивных схем. В качестве основного показателя при этом принят MEI (Minimum Efficiency Index).
MEI представляет собой десятичное число < 1,0 и отражает количественное отношение представленной на рынке продукции разного технического уровня. По мере развития насосного оборудования данный показатель планомерно повышается, задавая новый уровень требований к продукции, выпускаемой производителем. Фактически индекс MEI определяется по трем точкам характеристики КПД насоса. Таким образом, можно сказать, что одной из основных тенденций развития насосных агрегатов на сегодняшний день является повышение их КПД и расширение рабочей зоны.
Также немаловажными показателями являются для большинства потребителей по-прежнему являются массогабаритные показатели оборудования и его кавитационные характеристики, надежность и долговечность.
На сегодняшний день существуют различные подходы к совершенствованию центробежных насосов [1]. Некоторые из них направлены преимущественно на повышение надежности и увеличение ресурса при обеспечении работоспособности насоса в экстремальных или специфичных условиях. Такие решения сопряжены с конструктивными и технологическими изменениями: применением химически стойких металлов и сплавов, разнообразных покрытий, герметизацией конструкции насоса и использованием вспомогательных элементов конструкции (теплообменников, фильтров, систем масляного охлаждения, частотного регулирования, включая системы плавного пуска, автоматизированные системы управления и контроля и т.п.).
Другие подходы направлены на повышение энергетических показателей насосов и реализуются путем модификации или оптимизации отдельных элементов проточной части. По своему влиянию такие решения могут быть направлены на преимущественное повышение гидравлического либо объемного КПД:
Подходы, направленные на повышение гидравлического КПД (или снижение гидравлических потерь):
- смещение оптимальной точки Qopt относительно номинальной Qnom при проектировании (особенно актуально для насосов с низким коэффициентом быстроходности ns) [2–4];
- согласование работы отвода и колеса с целью минимизации совокупных потерь в насосе [2];
- совершенствование методов профилирования проточных частей насосов:
- использование гетерогенной лопастной системы [5, 6];
- изменение диффузорности межлопастных каналов [1];
- использование подходов теории оптимального управления (ТОУ) [7].
Повышение объемного КПД: снижение перетоков в дисковых пазухах за счет модификации щелевых уплотнений [8, 9].
В рамках выполнения ПНИЭР НИУ «МЭИ», совместно с индустриальным партнером (АО «Гидрогаз») был выполнен ряд расчетно-экспериментальных работ по данным направлениям. В качестве основного объекта для апробации представленных подходов был выбран насос АХ12.5/50 (ns = 34).
Повышение гидравлического КПД
Использование гетерогенной лопастной системы (ЛС). Проектирование рабочих колес с гетерогенной ЛС показало хорошие результаты при апробации на консольно-моноблочном насосе КМ 65-50-160 (ns = 80). Данное направление совершенствования является потенциально перспективным для насосов нефтехимической и неф-теперерабатывающей промышленности. Концепция гетерогенной ЛС предполагает проектирование насоса на расчетную область. Лопасти рабочего колеса проектируются на различные расчетные режимы и при компоновке образуют решетку переменной густоты. Такой подход направлен на перераспределение гидравлических потерь во всей рабочей области насоса и расширение рабочей зоны.
Изменение диффузорности межлопастных каналов рабочих колес. Довольно подробно данные подходы описаны в публикации [1]. Как в ней отмечено, изменение диффузорности может быть осуществлено за счет увеличения толщины лопасти с тыльной, рабочей стороны и при одновременном их изменении. Для количественной оценки модификации во всех трех случаях удобно использовать коэффициенты диффузорности, характеризующие относительное изменение ширины межлопастного канала относительно средней линии тока в каждой i-й точке:
где kb.т – коэффициент диффузорности по тыльной стороне лопасти; kb.р – коэффициент диффузорности по рабочей стороне лопасти; (bi – b*i.р) – изменение ширины межлопастного канала по рабочей стороне лопасти на i-м радиусе; (bi – b*i.т) – изменение ширины межлопастного канала по тыльной стороне лопасти на i-м радиусе.
Сам межлопастной канал при этом рассматривается как несимметричный плоский диффузор, характеризуемый, помимо прочего, числом лопастей рабочего колеса.
Подходы к проектированию гетерогенной ЛС и ЛСс измененной диффузорностью межлопастных каналов были апробированы с использованием теории планирования эксперимента. В случае с гетерогенной ЛС область исследования была разбита на две части относительно средней по лопастной системе расчетной подачи Qср = 1.Рассматривалась постановка двухфакторного эксперимента с варьированием параметров на двух уровнях. Основными параметрами, определяющими геометрию лопасти, являлись углы установки лопасти в плане на входе и выходе j1 = [14°; 22°] и j2 = [24°; 34°] соответственно. Меридиональная проекция колеса принималась неизменной.
В случае с ЛС с измененной диффузорностью межлопастных каналов также была выполнена постановка факторного эксперимента на базе линейной модели: двухуровневый план для трех факторов. В рамках этого эксперимента диффузорность изменялась от 20 до 60% по тыльной и рабочей сторонам лопасти. Число лопас-тей принималось равным от 5 до 6. За основу при этом была принята геометрия ЛС серийного образца.
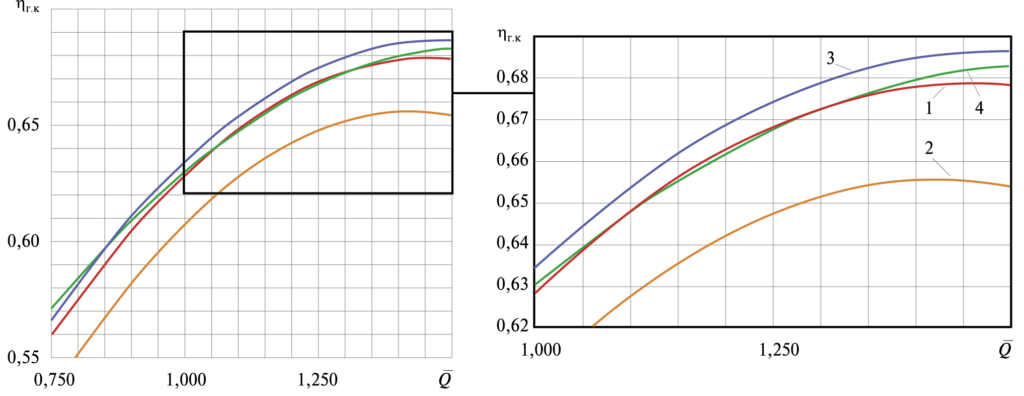
1 – расчетные характеристики КПД серийного насоса; 2 – вариация гетерогенной ЛС с наибольшим значением целевой функции; 3, 4 – вариации гетерогенной ЛС с наименьшим значением целевой функции
Как показали результаты расчетов, функция отклика (обобщенный функционал) при использовании гетерогенных ЛС (рис. 1) оказалась чувствительна к значениям углов лопасти; основные тренды, закладываемые в концепцию гетерогенной ЛС (расширение рабочей зоны), выдерживались. Однако значительных положительных эффектов для насоса данной быстроходности достигнуть не удалось. Максимальное повышение гидравлического КПД рабочего колеса составило 0,5–0,8% во всей рабочей области Q = (0,75…1,50)Qnom.
Результаты расчетных исследований по влиянию диффузорности межлопастных каналов показали следующее:
- функция отклика оказалась чувствительной к параметрам kb.т и kb.р. Как видно из графиков, приведенных на рис. 2, варьирование k2.т и k2.р при постоянном числе лопастей (линии 2 и 3) вызывало изменение гидравлического КПД рабочего колеса от –0,1% до +1,0% при Q = 0,75 и от +1,5% до +1,8% при Q = 1,25.
- меньшая чувствительность отмечена к числу лопас-тей. При постоянных k2.т и k2.р и варьируемом числе лопастей (см. рис. 2, линии 3 и 4) изменение КПД составляло от –0,1% до +0,4% при Q = 0,75 и от +1,75% до +1,8% при Q = 1,25.
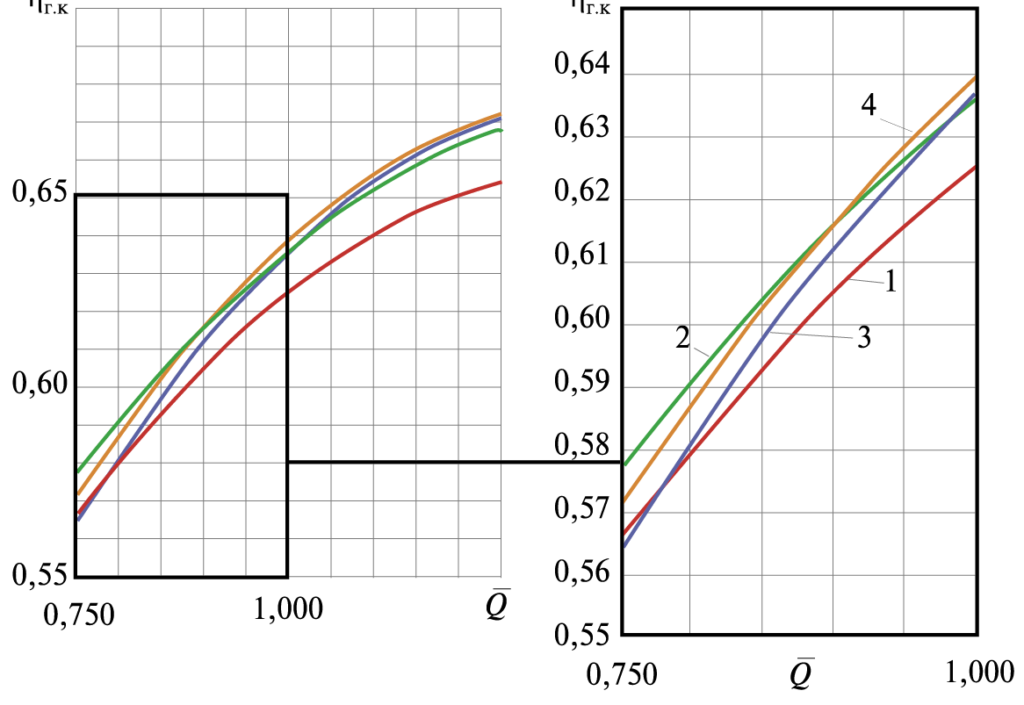
1 – расчетные характеристики КПД серийного насоса; 2 – модификация ЛС k2.т = 0,6; k2.р = 0,6; z = 5; 3 – модификация ЛС k2.т = 0,2; k2.р = 0,6; z = 5; 4 – модификация ЛС k2.т = 0,2; k2.р = 0,6; z = 6
Использование подходов ТОУ. Как показывает практика, подходы теории оптимального управления являются довольно эффективным инструментом для решения задач синтеза геометрии элементов проточной части насосов [7]. Согласно концепции подходов ТОУ, стратегия разработки оптимально действующей системы состоит в определении ее структуры и управления, обеспечивающих достижение целевых показателей при заданных возмущающих воздействиях и ограничениях и достижении экстремума показателя качества.
Фактически задача синтеза ЛС на базе ТОУ сводится к решению классической задачи вариационного исчисления: определение пути перемещения частицы жидкости из точки А в точку В с минимальными затратами энергии.
Постановка задачи синтеза проточной части рабочего колеса насоса может быть выполнена двумя способами. В первом случае оптимизируется только профиль лопасти в плане, при этом меридиональная проекция остается жестко зафиксированной (вариант 1). Во втором – оптимизируется вся проточная часть, в том числе и в меридиональной проекции (вариант 2).
Из-за конструктивных ограничений корпуса насоса экспериментальная апробация была возможна только для первого способа оптимизации, не затрагивающего меридиональную проекцию рабочего колеса. В связи с этим оптимизация c использованием подходов ТОУ выполнялась в виде двух блоков.
Первый блок включал оптимизацию с учетом всех конструктивных ограничений и расчетно-численное моделирование с последующей экспериментальной верификацией данных. Как видно из графиков (рис. 3), расчетные и экспериментальные тренды выборки колес совпадают. Это позволяет сделать вывод о корректности расчетной модели и возможности дальнейшего прогнозирования характеристик насоса по вариациям геометрии на ее базе.
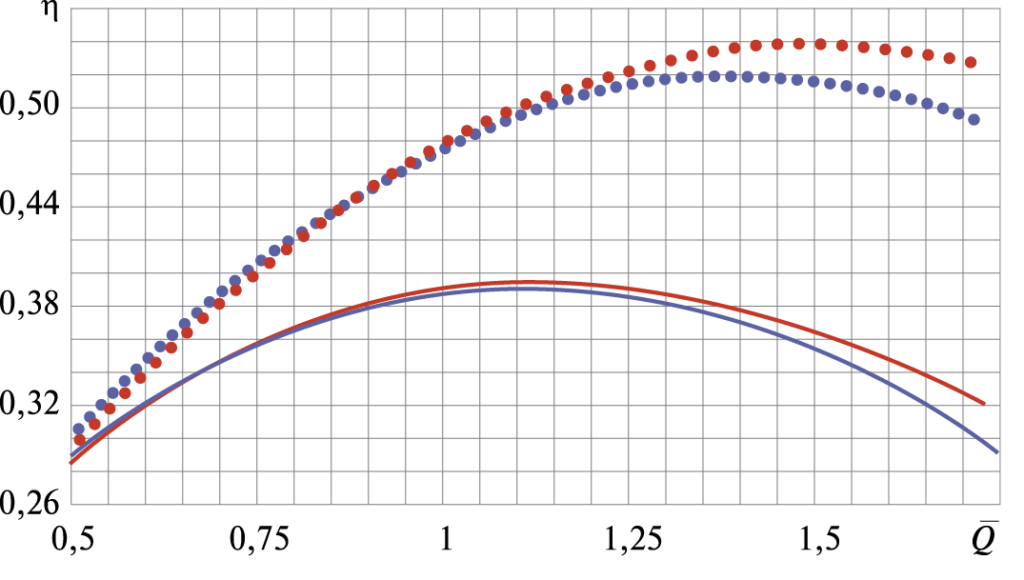
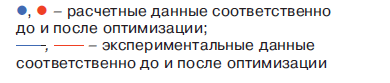
Также можно отметить что оптимизация только профиля лопасти без коррекции меридиональной проекции обеспечивает относительно небольшое повышение КПД (около 0,5–2,5% для насосов данной быстроходности ns = 34), при этом преимущественно правее номинального режима.
Во втором блоке исследований с использованием подходов ТОУ выполнялась оптимизация всей проточной части рабочего колеса, в том числе и в меридиональной проекции. При этом снимались все конструктивные ограничения. Проектирование выполнялось как на строго заданные номинальные параметры, так и с отклонением от них в пределах, допустимых ГОСТ 32601–2013 (ISO 13709:2009). Как известно из классической литературы [2–4], смещение по подаче dQ расчетной точки (Qopt, Hopt) относительно номинальной (Qnom, Hnom) приводит к повышению быстроходности насоса и, как следствие улучшению его энергетических характеристик. Величина смещения определяется уравнением
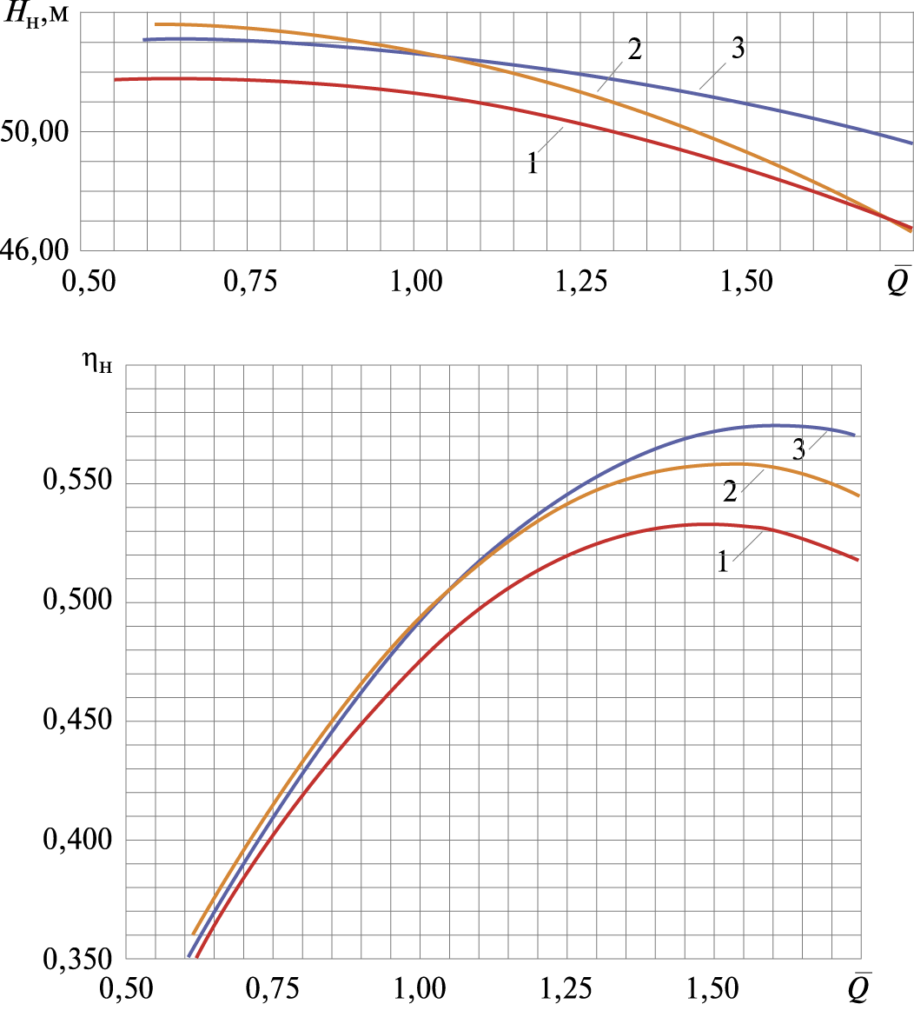
Как можно отметить из результатов, приведенных на рис. 4, оптимизация всей проточной части рабочего колеса может позволить повысить КПД насоса на 2,0–2,8% в зависимости от режима работы при проектировании на номинальные параметры (значения ГОСТ либо ТЗ заказчика).
Смещение расчетной точки на +20% относительно номинала позволяет дополнительно повысить КПД до 5,0% в области больших подач.
Согласование работы отвода и колеса с целью минимизации совокупных потерь в насосе. Согласование расчетных параметров колеса и отвода является очень важным при проектировании. Как известно, расчетная подача элемента проточной части определяет режим работы с минимальными гидравлическими потерями. Как известно из классической литературы, проектирование колеса и отвода насоса на одну и ту же точку не всегда является самым эффективным решением.
Расширение спиральной камеры (увеличение ее расчетной подачи Qopt.СО по сравнению с рабочим колесом Qopt.РК) оказывает двоякий эффект. С одной стороны, оно приводит к снижению интегральных потерь в отводе, что положительно сказывается на энергетических характеристиках насоса (может быть достигнуто повышение КПД и расширение рабочей зоны). С другой стороны, смещение минимума гидравлических потерь в отводе в область больших подач может вызвать недопустимое снижение КПД насоса на номинальном режиме.
Таким образом, имеет место постановка оптимизационной задачи, сводящейся к определению структуры ? объекта оптимизации (насоса), характеризуемой параметрами ?, при заданных ограничениях ? и достижении экстремума показателя качества F, математическая формулировка которой может быть представлена в виде
? ˫ ?, F_ext; (3)
F = DhS = Dhг.CO + Dhг.РК;
? : ? ∈ [?].
С целью апробации данного подхода был выполнен ряд расчетов с использованием геометрии корпусов насосов типа АХ, серийно выпускаемых АО «Гидрогаз». Непременным условием при отборе корпусов являлось обеспечение требуемых габаритных и посадочных размеров, позволяющее провести стендовые испытания на площадке индустриального партнера. Так, для экспериментальной апробации были выбраны два варианта корпусов, характеризующихся различным законом изменения площади проходного сечения (рис. 5, а). Результаты экспериментальной апробации для двух вариаций рабочих колес в данных корпусах (рис. 5, б) согласуются с существующими эмпирическими трендами и подтверждают перспективность представленного направления совершенствования центробежных насосов для нефтегазовой и химической промышленности. Как можно отметить из графиков на рис. 5, б, в результате согласования рабочего режима колеса и корпуса снижаются совокупные потери в насосе, на что указывает повышение максимума КПД Dhopt = 3,5–4,5% и КПД на номинальном режиме Dhnom = 1,0–1,8%.
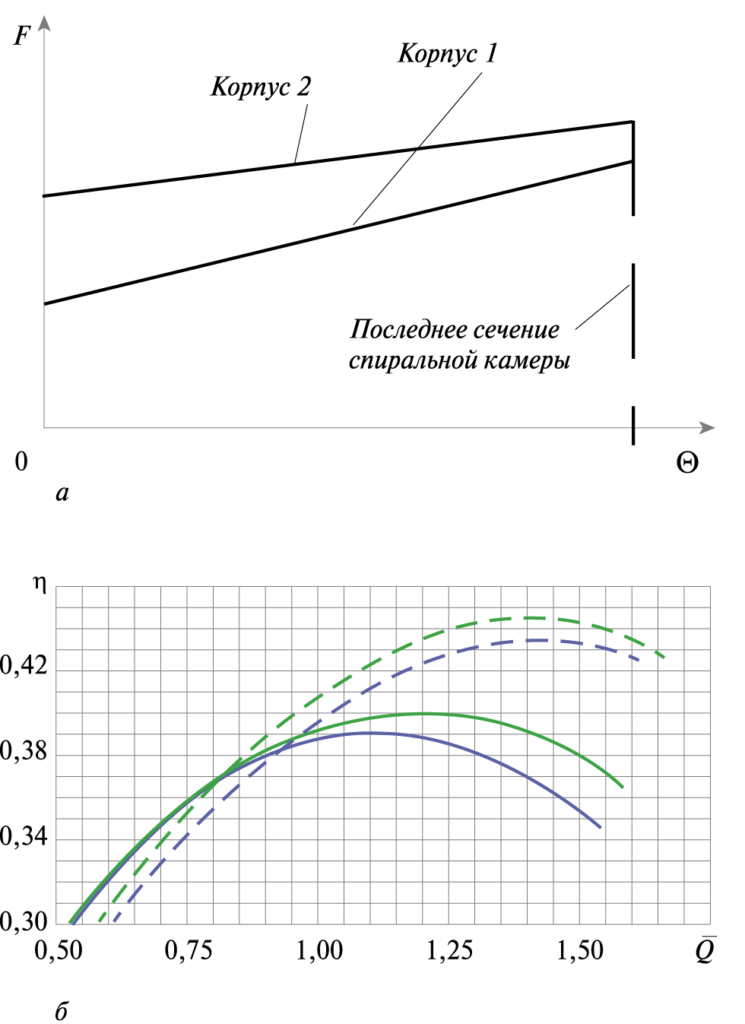
а – изменение площади проходного сечения выборки корпусов; б – результаты экспериментальной апробации; , – корпус 1, колесо соответственно 1, 2;– – –, – – – – корпус 2, колесо соответственно 1, 2
Повышение объемного КПД
Направление, связанное с повышением объемного КПД насоса, является перспективным для насосов малой быстроходности. Так, доля объемных потерь для насоса АХ12.5/50 (ns = 34) по расчетным оценкам составляет от 20 до 30%, что особенно существенно для малорасходных насосов [8].
Существуют различные способы повышения объемного КПД. Это может быть увеличение длины щелевых уплотнений и уменьшение зазора, это могут быть лабиринтные двух- и трехщелевые уплотнения и т.д. Каждое из обозначенных решений имеет свои недостатки и ограничения. Так, довольно перспективной является модификация щелевого уплотнения за счет нарезки кольцевых и винтовых канавок. При этом положительный эффект от увеличения гидравлического сопротивления щели нивелируется снижением длины щелевого уплотнения, т.е. имеется некоторый оптимум. Существующие опытные рекомендации [9] носят частный характер и не всегда дают положительные результаты. Оптимизационные методы являются более гибким и универсальным инструментом, позволяющим прогнозировать реальный эффект от модернизации уплотнительного узла.
НИУ «МЭИ» была выполнена постановка многофакторной оптимизационной задачи в рамках проведения экспериментальных исследований по повышению объемного КПД центробежного насоса с малым ns. Были выделены основные факторы (параметры оптимизации), определяющие конечную структуру объекта (модифицируемого рабочего колеса), а также ограничения конструктивного и технологического характера.
Как показали результаты стендовых испытаний, выполненных для выборки из трех рабочих колес с различной геометрией проточной части, прогнозные расчеты имеют хорошую сходимость с экспериментом. При этом во всех случаях оптимизационные подходы, в отличие от опытных рекомендаций, обеспечивают положительных эффект: повышение КПД от 0,8 до 3,2 %.
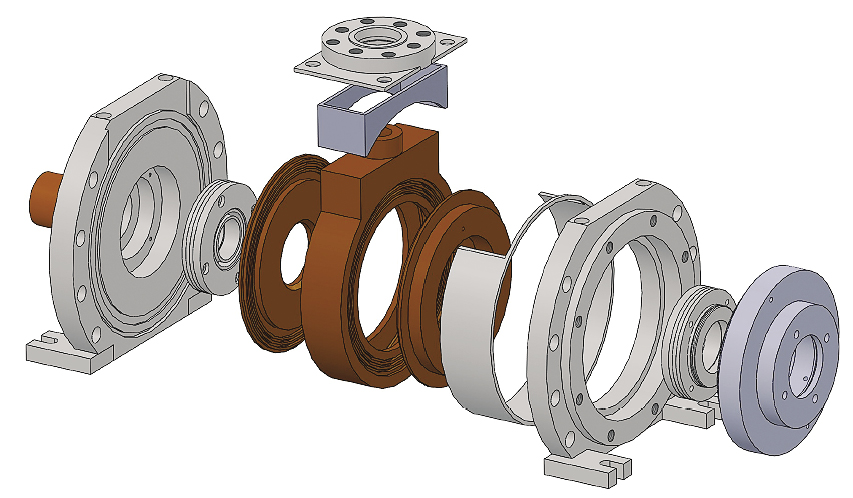
Как можно отметить из всего сказанного, лучшие результаты могут быть достигнуты за счет комплексной оптимизации элементов проточной части насоса. Для проведения перспективных экспериментальных исследований серии насосных агрегатов низкой быстроходности с усовершенствованными элементами проточной части НИУ «МЭИ» совместно с АО «Гидрогаз» был разработан универсальный корпус. Его конструкция позволяет проводить моделирование проточных частей нескольких типоразмеров насосов АХ с использованием возможностей 3D-аддитивных технологий (рис. 6).
Список литературы
- Вихлянцев А.А., Волков А.В., Парыгин А.Г. и др. Анализ возможностей совершенствования отечественных центробежных насосов для нефтегазовой и химической промышленности// Эл. журнал «Гидравлика». 2016. ¹2. ФГБОУ ВПО «МГТУ им. Н.Э. Баумана».
- Ломакин А.А. Центробежные и осевые насосы. 2-е изд. М.: Машиностроение, 1966. 364 с.
- Малюшенко В.В., Михайлов А.К. Энергетические насосы: Справ. пособие. М.: Энергоиздат, 1981. 200 с.
- Машин А.Н. Профилирование проточной части рабочих колес центробежных насосов. М.: МЭИ, 1976. 55 с.
- Волков А.В., Парыгин А.Г., Вихлянцев А.А. Возможности применения гетерогенных лопастных систем для расширения рабочей зоны центробежных насосов//Сб. докл. МНТК «ECOPUMP-RUS 2016. Энергоэффективность и инновации в насосостроении. Импортозамещение и локализация производства в России». 2016. С. 9–12.
- Stefan D., Moravec P., Rudolf P., Pochyly F., Stejskal J. Design and shape optimization of Pump-turbine runner and CFD simulation of 4-quadrant characteristic//Сб. докл. XXI МНТК студентов и аспирантов. НИУ «МЭИ», 6 декабря 2017 г. М.: Изд-во МЭИ, 2017. 198 с
- A.V. Volkov, A.G. Parygin, A.V. Naumov, A.A. Vikhlyantsev, A.A. Druzhinin. Application of Methods of the Optimum Control Theory for Development of High Efficiency Centrifugal Pumps// International Journal of Applied Engineering Research. 2017. Vol. 12. ¹19. Рp. 8768–8778. URL:http://www.ripublication.com/ijaer17/ijaerv12n19_105.pdf.
- Волков А.В., Парыгин А.Г., Вихлянцев А.В. Повышение энергоэффективности тихоходных малорасходных насосов за счет уменьшения утечек через щелевые уплотнения// Сб. научных трудов Х МНТК «Гидравлические машины, гидропневмоприводы, гидропневмоавтоматика. Современное состояние и перспективы развития». СПб: Изд-во Политехнического университета, 2018.
- Степанов Л.И. Центробежные и осевые насосы. Теория, конструирование и применение / Под ред. В.И. Поликовского. М.: ГНТИ Машиностроительной литературы, 1960. 463 с.