Автор: В.М. Давыдов, П.В. Деревицкий, С.Д. Рязанов, Л.С. Алексенцева (ООО «Научно-производственное предприятие «Механик»).
Опубликовано в журнале Химическая техника №4/2016
Впервые задача создания технических решений по обеспечению безопасности подводных и мостовых переходов магистральных трубопроводов была поставлена в конце 1970-х годов при проектировании аммиакопровода Тольятти–Одесса (диаметр магистральной трубы 350 мм). На протяжении более 2 000 км трасса трубопровода предусматривает десятки переходов через реки Волга, Дон, Днепр и ряд других водных преград.
Принимая во внимание токсичность и взрывоопасность аммиака, в местах переходов в проект была заложена конструкция типа «труба в трубе», в которой основной трубопровод размещался в защитном наружном трубопроводе, рассчитанном на полное рабочее давление.
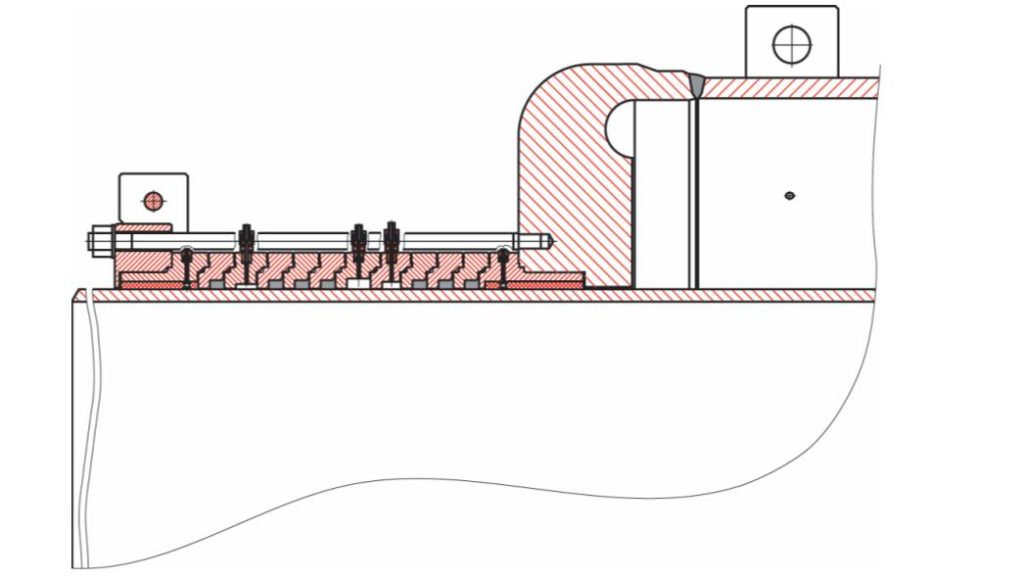
Это значительно повышает экологическую безопасность участка трассы в случае разгерметизации основного трубопровода.
Для предотвращения коррозии предусмотрено заполнение межтрубного пространства азотом. Минимальное рабочее давление азота в межтрубном пространстве назначается из условия превышения над наибольшим гидростатическим давлением на глубине залегания трубопровода. Центральный трубопровод снабжен расположенными пошагово центрирующими опорными кольцами из антифрикционного материала.
В зависимости от протяженности перехода расчетные относительные перемещения, вызванные климатическими перепадами температур магистральной трубы и кожуха, могут доходить до 1 000 мм. С целью исключения дополнительных напряжений в магистральной трубе было принято решение о применении сальникового компенсатора.
При разработке конструкции сальникового компенсатора (СК) должны были обеспечиваться следующие требования:
- СК должен сохранить герметичность при работе с давлением азота 0,2…0,5 МПа, а также при аварийном повышении давления в случае раскрытия основного трубопровода в зоне перехода при давлении до 8 МПа;
- допускается максимальное расчетное относительное перемещение кожуха до 1 000 мм;
- герметичность должна обеспечиваться по необработанной поверхности специально отобранного или изготовленного участка магистральной трубы с шероховатостью до Rz 80;
- конструкция должна исключить постоянное обслуживание при сохранении допустимого уровня утечки;
- технические решения должны предусматривать возможность замены изнашивающихся элементов (уплотнительные кольца, центрирующие опорные кольца) без демонтажа узла, т.е. без нарушения целостности трубопровода.
В качестве рабочего варианта была принята конструкция СК, представляющая собой секционный корпус с несколькими эластичными герметизирующими элементами, встроенными центрирующими опорами и узлом для пополнения и распределения герметизирующей смазки (см. рисунок). Опытный стенд – два натурных образца СК, смонтированных на участке магистральной трубы и связанных между собой центральной камерой, – был установлен на открытой площадке. Условия испытаний полностью имитировали рабочие условия (давление, температура, относительные перемещения). В результате испытаний были получены зависимости утечек и сил трения от уплотняемого давления за полный климатический период в течение одного года.
Как показывают исследования многоэлементных уплотнений, практически весь перепад давления воспринимается одним из элементов, имеющим наибольшую плотность. По мере изнашивания или изменения условий работы (перемещение в зону с другим качеством поверхности) в работу включается другой элемент, имеющий в данный момент наибольшую плотность. Таким образом, достигается надежность собственно уплотнительного узла.
Специальные исследования были посвящены выяснению «механизма» герметизации поверхностей, имеющих шероховатость до Rz 60, и значительную погрешность формы (конусность до 0,5 мм на погонный метр, эллипсность до 1,0 мм). Результаты этих исследований были также использованы в ряде конструктивных решений [1].
Герметизирующая способность СК, работающего по поверхности, имеющей очень большие геометрические размеры и соответственно протяженные герметизируемые линии контакта, в значительной степени зависит от наличия равномерно распределенной пленки герметизирующей консистентной смазки. Важность этого момента иллюстрируется тем, что в зимнее время при экстремально низких температурах величина утечки на порядок больше, чем при положительных температурах. В связи с этим все «эволюционные» преобразования в конструкции за 30 лет коснулись именно проблем равномерного распределения смазки. Наиболее простое и надежное решение нашло отражение в последних проектах.
Особенностью консистентных смазок является то, что при сдвиге в объеме происходит относительное смещение слоев, как в твердом теле. По мере уноса смазки с поверхностным слоем происходит «зависание» ее в полости над уплотняемой поверхностью. Для обеспечения восполнения уносимого слоя сальник снабжен узлом подкачки и распределения консистентной смазки.
Цель достигается тем, что в сальниковом компенсаторе камера для подкачки герметизирующей смазки состоит из двух полостей, разделенных перегородкой, сопрягаемой с минимальным зазором по цилиндрической уплотняемой поверхности, при этом каналы для подачи уплотняющей смазки и для продувки выполнены в разных полостях [2].
По мере подачи уплотняющей смазки происходит удаление воздуха через зазор между перегородкой и уплотняемой цилиндрической поверхностью. Поскольку сопротивление зазора значительно больше, чем сечения полости, то воздух вытесняется до тех пор, пока вся кольцевая полость не будет заполнена смазкой полностью.
Таким образом, обеспечивается равномерное распределение герметизирующей смазки по всей окружности уплотняемой поверхности.
Рабочий вариант СК предусматривает монтаж собственно герметизирующего узла на участке протяженностью 3…4 м магистральной трубы с приваренным участком кожуха длиной 1,5…2,0 м. Это позволяет обеспечить качество сборки и испытаний в условиях завода-изготовителя с последующей поставкой на место монтажа в готовом к эксплуатации состоянии. Размеры выбранных участков труб определяются значениями расчетных относительных перемещений, а также технологией монтажа.
Программой испытаний кроме проверки пробным давлением на прочность и герметичность, предусмотрены относительные перемещения сальника и центральной трубы, имитирующие температурные перемещения, а также контроль их влияния на герметичность узла.
Конструкция предусматривает стыковку и замену уплотнительного элемента на месте эксплуатации без демонтажа узла в целом. По результатам ревизии СК после 25 лет эксплуатации были обнаружены повреждения только первого (со стороны атмосферы) уплотнительного элемента, связанные со старением материала.
В последующем разрабатывался СК для трубопроводов диаметром 750 и 1 020 мм, в котором были реализованы аналогичные технические решения для Оренбурггазпрома в 1989 г. и Балтнефтепровода в 2003 г. (разработчик ООО НПП «Механик»).
Для перехода нефтепровода Палкино-Приморск (диаметр 1020 мм) в 2005 г. был проведен анализ утечек азота через СК за первые два года эксплуатации перехода. Среднегодовая утечка в пересчете на один сальник составила 9⋅10–3 м3/ч (при предусмотренных в ТУ 50⋅10–3 м3/ч).
При нормальной эксплуатации давление азота в межтрубном пространстве непрерывно контролируется приборами.
Для «подпитки» межтрубного пространства азотом (при поступлении сигнала о снижении давления) должен доставляться контейнер-газификатор на грузовой автомашине. Контейнер-газификатор работает в автономном режиме и имеет систему автоматического поддержания давления азота.
В случае расположения СК в шахте для контроля содержания кислорода в воздухе рабочих зон в шахтах устанавливаются автоматические газоанализаторы. При снижении содержания кислорода (19% об.) автоматически включается вентиляция.
Для обеспечения безаварийной работы «узла заполнения» должны быть предусмотрены:
- автоматическое регулирование давления газообразного азота («после себя»);
- автоматическое отключение подачи азота в случае роста давления;
- сигнализация предельно допустимых значений параметров срабатывания блокировок содержания кислорода в шахтах и давления азота в защитном кожухе;
- сигнализация предельно допустимых значений давления.
Конструкция перехода магистрального трубопровода типа «труба в трубе» с заполнением азотом межтрубного пространства обладает рядом несомненных достоинств.
В случае разгерметизации основной магистральной трубы в зоне перехода кожух и сальниковые компенсаторы способны обеспечить работу продуктопровода с полным рабочим давлением в течение времени, необходимого для отсечения аварийного участка и остановки его работы в штатном режиме.
Система позволяет осуществлять контроль герметичности центральной трубы и кожуха. По характеру изменения давления в межтрубном пространстве можно судить о герметичности как основного магистрального участка, так и кожуха.
Обеспечивается защита от коррозии подводного участка магистральной трубы.
Исключается образование взрывоопасной смеси в межтрубном пространстве.
Список литературы
- Давыдов В.М., Деревицкий П.В. и др. Исследование уплотняющей способности сальниковых компенсаторов подводных переходов магистральных трубопроводов. Труды ГИАП, М.: 1987.
- Патент РФ №2238462 Сальниковый компенсатор, 2004.