Авторы: Г.А. Зуев, И.В. Минкин (ООО «ИК «АСУТП и Диагностика»), Р.З. Хадиев, М.Н. Сапелкин (ЗАО «Сибур-Химпром»).
Опубликовано в журнале Химическая техника №4/2015
Под эффективной диагностикой понимается оптимальное решение задачи определения технического состояния оборудования с максимальным использованием возможностей существующих на предприятии системы диагностики и автоматизированной системы управления технологическими процессами (АСУТП), основываясь на опыте эксплуатации и выявленных отказах за последние несколько лет эксплуатации [1].
В качестве критерия оптимальности выбирается наилучшее соотношение цена/качество создаваемой системы. Система должна обеспечивать диагностирование отказов оборудования, которые происходили за последние несколько лет эксплуатации, достоверность определения отказов должна быть не менее 0,9. При этом необходимо принимать во внимание, что остаточный ресурс диагностируемого оборудования может не превышать 3–5 лет, а ресурс новой системы диагностики составляет 10–15 лет.
Современный подход к решению задачи определения технического состояния оборудования заключается в детальном анализе отказов и ремонтных воздействий с целью выявления причин их появления, связанных или с износом (выработкой ресурса) узлов оборудования, или с нештатными режимами работы оборудования, или с использованием некачественных материалов и комплектующих, или с некачественным выполнением ремонтных воздействий. Данный анализ проводится за последние несколько лет эксплуатации оборудования.
При проведении анализа отказов узлов оборудования, связанного с износом, необходимо к узлам, отказывавшим в последние несколько лет эксплуатации, добавить узлы оборудования, имеющие большую выработку по ресурсу и, соответственно, высокую вероятность проявления отказов.
При проведении анализа отказов, связанных с некачественным выполнением ремонтных воздействий, необходимо обращать внимание на контроль качества выполнения указанных работ, а также на контроль качества материалов и комплектующих, используемых при ремонтных воздействиях.
Подход к диагностике поршневых машин с учетом передовых практик
Следует признать, что эффективность диагностических систем в РФ крайне низка и не зависит от числа установленных датчиков, а связана с низким качеством ремонтных воздействий, неправильной эксплуатацией (несвоевременная смазка, некачественная центровка, деградация фундаментов, трубная обвязка с натягом, перепробег, износ, ремонт «на бумаге», «дешевые» комплектующие и др.) и недостаточной квалификацией диагностов.
В настоящее время основными разработчиками ГОСТов, регламентов, стандартов предприятий на установку и обслуживание диагностических систем являются их поставщики. Естественно, так как цель любой организации – получение прибыли, то поставщик заинтересован в поставке диагностических систем с большим числом датчиков, каналов, без анализа их необходимости и достаточности, что сказывается на цене системы.
У предприятия-потребителя возникает вполне естественный вопрос о цене инсталляции системы, цене владения системы, и, наконец, об эффективности диагностических систем, сроке окупаемости, экономии, изменении объемов технического обслуживания и ремонта (ТОиР).
Как же определить необходимость и достаточность диагностических систем?
Как это часто бывает, отечественные разработки забыты (прогнозирование и надежность), но восприняты передовые практики, пришедшие из развитых стран –RCM (Reliability-сentered Maintenance – Техническое обслуживание, ориентированное на надежность).
Проведем сокращенный анализ видов и критичности последствий отказов (ГОСТ 27.310–95). [2] Сейчас чаще употребляют другой термин в соответствии с модной «best practices – передовым опытом» – FMECA – FailureMode, Effects and Criticality Analysis () [3].
Форма заполнения таблиц, порядок упорядочивания информации приведены в названных документах, рассмотрим общий, упрощенный подход в рамках статьи.
Перечислим дефекты, которые возможны в оппозитном поршневом компрессоре [4]. Например:
- поломка компрессионного кольца;
- срез шпонки коленчатого вала на муфте со стороны силового агрегата;
- срез коленчатого вала по линии сопряжения с шатунной шейкой (рассматриваем случай только нарушения передачи вращения другим участкам вала. Вал в коренных подшипниках не изменил своего положения);
- поломка выпускного клапана и др.
Проанализируем, к каким последствиям, например, они приведут:
- поломка компрессионного кольца – падение компрессии – падение давления на данном цилиндре;
- срез шпонки коленчатого вала на муфте со стороны силового агрегата – отсутствие давления в цилиндрах, падение производительности, отсутствие вибрации.
Как можно диагностировать данный дефект:
- поломка кольца – по показаниям манометра (будут отличаться от показаний в других цилиндрах), по изменению шума работающего компрессора;
- срез коленчатого вала по линии сопряжения с шатунной шейкой – по вибрации, отсутствию давления в некоторых цилиндрах, снижению производительности.
Как можно предупредить данные отказы:
- поломка компрессионного кольца – при входном контроле;
- срез коленчатого вала – при контроле во время каждого ремонта на отсутствие микротрещин в местах сопряжений участков вала методом цветной дефектоскопии.
Теперь оценим, какова частота возникновения каждого из этих событий по опыту эксплуатации:
- поломка вала – 1 раз в 15–20 лет;
- поломка кольца – 1 раз в год;
- поломка выпускного клапана – 1 раз в полгода.
Конечно, необходимо рассмотреть еще и последствия всех дефектов, и если риски велики, то вопрос об избыточности неразрушающего контроля или входного контроля не стоит, лишь бы обнаружить.
Таким образом, можно составить перечень всех возможных и наиболее вероятных дефектов, а также набор рекомендаций по предупреждению данных дефектов.
Например, по данным для реального поршневого компрессора с реальной историей поломок, подшипники компрессора за последние 4 года не выходили из строя, а теплообменник, наоборот, часто выходит из строя.
Последствия поломки компрессора по причине дефицита смазки весьма критичны. В этом случае требуется установить блокировку по отсутствию или падению давления масла в машине. Возможно, будет достаточно визуальных осмотров с записью в журнале значений давлений, уровня масла, отсутствия посторонних шумов с параллельным контролем данных параметров на пульте.
Проведение периодических сравнений данных из журнала повысит производственную культуру и обязательность осмотров.
И все это вместо дорогостоящих диагностических систем, выявляющих любые дефекты на компрессоре, даже маловероятные. Вместо p-V диаграмм, получение которых крайне дорого (для построения p-V диаграммы необходимо отслеживать положение коленвала с точностью не хуже 1° и с опросом датчика давления с частотой, превышающей в 3 раза частоту вращения коленвала).
А можно контролировать температуру и давление и сравнивать с давлением во всех цилиндрах – для мониторинга и оценки технического состояния этого достаточно.
Нарушения в кинематической схеме (задевания, касания, провис) контролируются датчиками удара. Температура подшипниковых узлов информативна для определения дефекта подшипника.
Детальный анализ отказов поршневого компрессора
Проведем анализ работы поршневого компрессора, эксплуатирующегося на нефтехимическом предприятии более 20 лет (реальные данные).
Упрощенная схема поршневого компрессора приведена на рис. 1. Поршневой компрессор представляет 12-рядную поршневую горизонтальную машину с оппозитным расположением цилиндров.

p – давление, вакуум; T – температура; V – вибрация; pм, Tм – соответственно давление, температура масла;
Ta, Tb, Tc – температура обмоток электродвигателя; U – напряжение питания электродвигателя; I – ток электродвигателя;
Lм – уровень масла в электродвигателе; Gв – провис вала; Gо – осевой сдвиг
Компрессор предназначен:
- для сжатия пирогаза в секции TV-1;
- для сжатия синтез-газа в секции TV-2;
- для сжатия водорода (99%) в секции TV-3.
Компрессор В-102 имеет два картера. Главный электродвигатель компрессора жестко соединен с двумя коленчатыми валами. Коленчатые валы вращаются в коренных подшипниках. Коренные подшипники – подшипники скольжения, состоящие из двух частей, имеющих баббитовую заливку. Подшипники жестко прижимаются крышкой и предохраняются от проворачивания штифтом. Для контроля температуры коренных подшипников используются термометры сопротивления.
К шейкам коленчатого вала при помощи мотылевого подшипника крепится шатун. Шатунный подшипник состоит из двух частей, имеет баббитовую заливку и может регулироваться при помощи прокладок. Втулка шатуна имеет заливку из свинцовой бронзы. При помощи стального пальца шатун соединен с крейцкопфом. Крейцкопф состоит из корпуса, выполненного из стального литья и «башмаков», имеющих баббитовую заливку. Зазор между направляющими крейцкопфа и «башмаками» может регулироваться прокладками. Крейцкопф соединяется с поршневым штоком посредством установочной гайки с контргайкой. Центровка штока выполняется при помощи четырех винтов. Со штоком соединяется поршень при помощи гайки. На поршне устанавливаются направляющие и поршневые кольца. Совершая возвратнопоступательное движение, крейцкопф перемещается по направляющим. Все цилиндры имеют водяные рубашки, в которые подается охлаждающая вода. Смазка компрессора осуществляется двумя отдельными системами: системой смазки механизмов движения и системой смазки поршневой группы.
Главные электродвигатели во время работы обдуваются воздухом, который подается при помощи вентиляционных систем с частичным сбросом давления воздуха из кожуха двигателя через шибер в атмосферу.
Создаваемое избыточное давление в приямке главного двигателя препятствует попаданию взрывоопасной среды к искрящим деталям электродвигателя.
Анализ отказов компрессора в 2008–2012 гг. дал следующие результаты:
Вид отказа Частота
Пропуск нагнетательного клапана 5
Сгорание электродвигателя 1
Ослабление гайки на поршне 3
Негерметичность всасывающего клапана 2
Трещина в гильзе цилиндра 1
Разрушение шатуна на 9-м цилиндре (задир шейки шатуна) 1
Из приведенных данных следует, что основную массу отказов компрессора можно диагностировать по следующим технологическим параметрам работы компрессора:
- по давлению всасывания;
- по температуре газа на всасывании;
- по давлению нагнетания;
- по температуре нагнетания;
- по температуре клапанной крышки;
- по давлению масла;
- по расходу газа.
В соответствии с ГОСТ ИСО 10816-3–2002 на опору (подшипник) рекомендуется установка датчиков вибрации в трех ортогональных направлениях [5]. Полученные в результате анализа выводы вполне коррелируют с ГОСТ 30848–2003.
Возможности существующей системы диагностики и системы АСУТП
В настоящее время на предприятии существуют системы диагностики и АСУТП, обеспечивающие эксплуатацию данного поршневого компрессора. Приведем их возможности в плане обеспечения диагностики отказов.
Перечень параметров и возможности системы диагностики. На поршневом компрессоре на каждом цилиндре установлены следующие датчики:
- абсолютной вибрации корпуса цилиндра;
- абсолютной вибрации корпуса крейцкопфа;
- ударных импульсов корпуса крейцкопфа.
Система вибродиагностики с помощью датчиков абсолютной вибрации позволяет проводить спектральный анализ, а с помощью датчиков ударных импульсов выявлять изменение технического состояния, связанное с наличием ударных воздействий, превышающих заданные допустимые значения [6–10].
Перечень параметров и возможности системы АСУТП.
В настоящее время на поршневом компрессоре установлены следующие датчики, которые можно использовать для диагностики:
- температуры подшипников коленвала; на всасывании; на нагнетании 1-й, 2-й и 3-й ступеней;
- давления на всасывании; на нагнетании 1-й, 2-й и 3-й ступеней; рециркуляции №1 и №2;
- давления масла; масла до и после фильтра;
- расхода.
Из перечисленных датчиков в АСУТП введены практически все за исключением датчика температуры клапанной крышки (для ее контроля используются стеклянные термометры).
Из изложенного следует, что оптимальным решением построения эффективной системы диагностики, позволяющей производить оценку технического состояния на ранней стадии развития дефектов, является построение интегральной системы диагностики, использующей данные системы диагностики и данные АСУТП. В настоящее время задача усложняется тем, что прямой доступ системы диагностики к данным АСУТП запрещен во избежание несанкционированного вмешательства в работу компрессора. Но существует возможность решения данной проблемы через существующую систему управления предприятием (ERP система), которая имеет доступ к данным АСУТП и к данным системы диагностики. Структурная схема интегральной системы диагностики приведена на рис. 2.
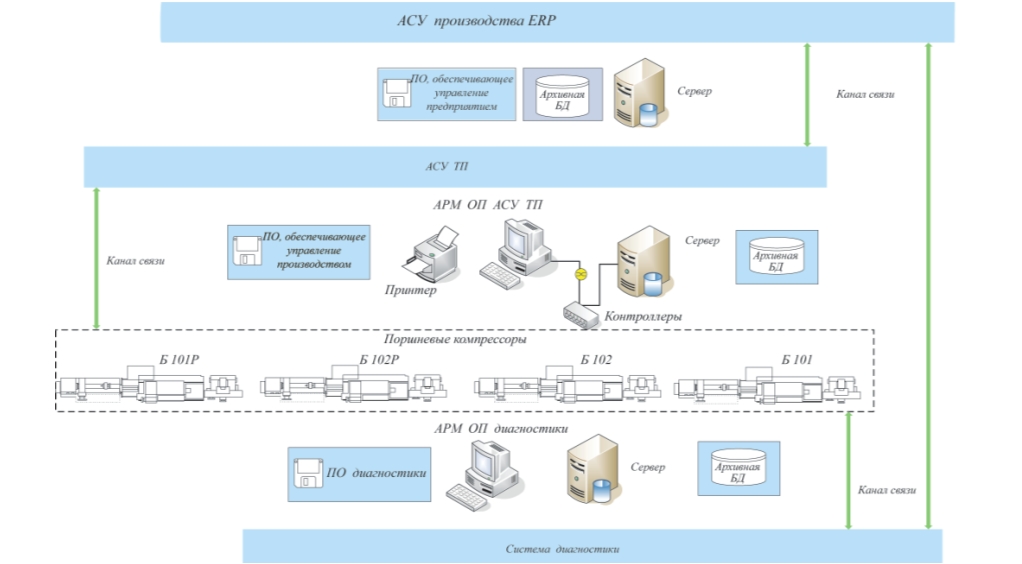
В общем случае варианты передачи информации между системами могут быть различными, что определяется принятыми на предприятиях правилами ограничения доступа и защиты информации.
Общее описание алгоритмов диагностирования
За основу алгоритма диагностирования (выявление дефектов на ранней стадии развития) взят алгоритм контроля выхода параметра, по которому контролируется появление дефекта, за допустимые пределы. Для алгоритмов диагностирования число допустимых пределов может быть два и более[11].
Так как изменение параметра, по которому контролируется появление дефекта, в большинстве случаев носит вероятностный характер, использование данного алгоритма дает достоверность на уровне 0,6…0,7.
С целью повышения достоверности до уровня 0,9 в алгоритм диагностирования дополнительно вводятся следующие виды контроля:
- контроль отклонений параметров от «базовых» значений (контроль относительных изменений параметров), где за «базовое» значение может браться либо значение параметра при заводских испытаниях, либо значение параметра после проведения очередного ремонта или иного технического воздействия (проведение балансировки и т.п.);
- контроль скорости изменения параметра за определенный интервал времени;
- в связи с тем, что на появление дефекта откликаются и другие технологические параметры, в алгоритм вводятся еще от одного до трех дополнительных параметров, значения которых коррелируют с основным параметром по данному дефекту.
В качестве примера рассмотрим дефект подшипника качения, который можно диагностировать по следующим параметрам:
- по уровню вибрации в стандартной полосе частот 10… 1 000 Гц в соответствии с ГОСТ ИСО 10816-3–2002;
- по уровню вибрации на подшипниковых частотах;
- по температуре корпуса подшипника.
В качестве основного параметра желательно выбирать параметр, изменение которого при появлении дефекта превышает 30% (в данном случае – вибрация на подшипниковых частотах). Дополнительные параметры откликаются на появление дефекта небольшим изменением, как правило, не более чем на 5–10%. При выборе параметров контроля надо иметь в виду, что не все параметры отслеживаются из-за отсутствия возможности установки датчика в желаемой точке или из-за существенного влияния на показания датчика в возможном месте установки других параметров.
Необходимо учитывать, что некоторые из возможных параметров уже введены в АСУТП (как правило, при проведении детального анализа выясняется, что практически 90% дополнительных параметров уже присутствуют в АСУТП), и задача заключается только в том, чтобы обеспечить доступ к этим данным.
Таким образом, оптимальным вариантом реализации алгоритма диагностирования является ввод основного параметра непосредственно с датчика в систему диагностики, а ввод дополнительных параметров – из состава существующих в АСУТП.
В связи с тем, что в эксплуатационной документации на контролируемое оборудование отсутствует математическое описание протекающих технологических процессов, а также значения допусков основных и дополнительных параметров на конкретные виды дефектов, то они определяются опытным путем в процессе проведения пусконаладочных работ с возможностью корректировки в процессе эксплуатации.
Таким образом, эффективная система диагностики должна строиться на следующих принципах:
- на детальном анализе отказов и отклонений в работе компрессора за последние несколько лет эксплуатации;
- на выявлении деталей и узлов компрессора, выходивших из строя в последние несколько лет эксплуатации;
- на определении перечня параметров, необходимых для выявления отказов компрессора на ранних стадиях развития дефектов;
- на анализе возможностей существующих на предприятии систем диагностики и АСУТП и на основании проведенного анализа создание интегральной системы диагностики с достоверностью не ниже 0,9 определяющей дефекты, выявленные за последние несколько лет эксплуатации контролируемого оборудования.
В основу построения эффективной системы диагностики положены те же принципы, что и при создании классической системы диагностики, но имеющие следующие отличия:
- основному контролю подлежат узлы и детали компрессора, которые имеют самую высокую вероятность появления отказов;
- максимально используются возможности существующей АСУТП и системы диагностики;
- алгоритмы диагностирования строятся на использовании нескольких параметров, технологически связанных друг с другом, что обеспечивает высокую достоверность выявления дефектов.
Реализация такого подхода позволяет создать эффективную и недорогую систему диагностики вместо предлагаемых в настоящее время на рынке дорогостоящих систем, основанных на построении p-V диаграмм.
Список литературы
- Гриб В.В. Диагностика технического состояния нефтегазохимических производств. М.: ЦНИИТЭнефтехим, 2002. 268 с.
- ГОСТ 27.310–95. Надежность в технике. Анализ видов, последствий и критичности отказов. Основные положения.
- ГОСТ Р 51901.12–2007. Менеджмент риска. Метод анализа видов и последствий отказов.
- Ястребова Н.А. и др. Техническая диагностика и ремонт компрессоров. М.: ЦНИИТЭхимнефтемаш, 1991, Ч. 2. 60 с.
- ГОСТ ИСО 10816-3–2002. Вибрация. Контроль состояния машин по результатам измерений вибрации на невращающихся частях. Ч. 3. Промышленные машины номинальной мощностью более 15 кВт и номинальной скоростью от 120 до 15000 мин–1.
- ИСО 10816-6:1995. Вибрация. Оценка состояния машин по результатам измерений вибрации на невращающихся частях. Ч.6: Машины возвратно-поступательного действия номинальной мощностью свыше 100 кВт.
- Балицкий Ф.Я., Иванова М.А., Соколова А.Г., Хомяков Е.И. Виброакустическая диагностика зарождающихся дефектов. М.: Наука, 1984. 129 с.
- Генкин М.Д., Соколова А.Г. Виброакустическая диагностика машин и механизмов. М.: Машиностроение, 1987. 283 с.
- Гриб В.В., Жуков Р.В. Особенности спектральной вибродиагностики поршневых компрессорных машин//Компрессорная техника и пневматика 2001 №8. С. 30–32.
- Рандалл Р.Б. Частотный анализ/Пер. с англ. Глоструп, Дания: К. Ларсен и сын А/О, 1989. 389 с.
- Неразрушающий контроль и диагностика. Справочник под ред. В.В. Клюева. Т. 7. Кн. 2. М.: Машиностроение, 2005.