Автор: В.В. Иванников, А.Г. Николаев, В.М. Шварц, О.Б. Рябов, В.Н. Степанов (ОАО «НОРЭ»).
Опубликовано в журнале Химическая техника №1/2015
Железобетонные конструкции зданий и сооружений, расположенных на территориях промышленных предприятий, находятся в условиях агрессивных сред и подвержены разрушению. Ремонт этих конструкций требует значительных затрат и в дальнейшем эти затраты будут только возрастать. В связи с этим становится очевидным, что во многих случаях экономически оправдано увеличение первоначальных затрат на изготовление конструкции и ее надежную защиту, если это позволяет сократить число и стоимость ремонтов в процессе эксплуатации объектов строительства.
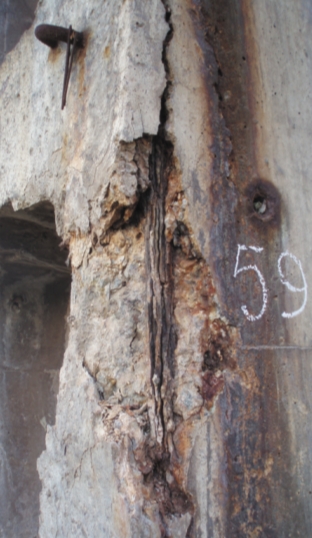
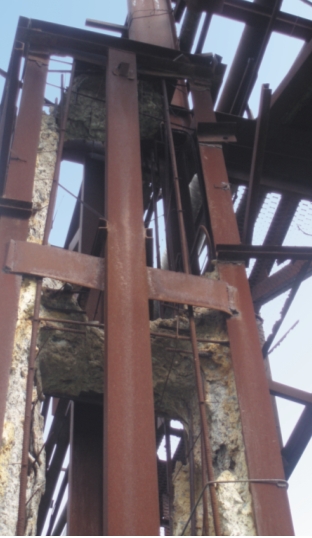
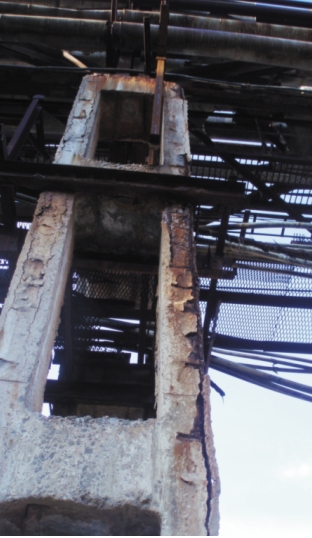
При проведении экспертизы промышленной безопасности (особенно технологических эстакад на предприятиях химической промышленности) часто заметно сильное разрушение железобетонных конструкций (колонны, фермы, балки, траверсы) вследствие воздействия агрессивных сред (см. рисунок).
Железобетон широко известен как долговечный материал, в большинстве случаев не нуждающийся в какой-либо защите от воздействий внешней среды. Бетон, представляющий собой искусственный каменный материал, может быть изготовлен достаточно прочным и стойким против агрессивных воздействий, а стальная арматура обычно находится под надежной защитой слоя этого бетона.
Существенный недостаток железобетона – коррозия арматурной стали, которая является одним из наиболее значимых факторов, определяющих фактическое техническое состояние железобетонных конструкций, их надежность и долговечность, поэтому защита арматуры от коррозии особенно актуальна.
Именно коррозия арматуры может значительно сократить срок службы строительных конструкций. Разрушение металла, конечно, не происходит мгновенно. Для того, чтобы замедлить или предотвратить коррозию металла, нужно подумать о том, чтобы в составе бетона не было примесей, агрессивно воздействующих на металл. К сожалению, это задача практически не решаема, так как не представляется возможным проверить все природное сырье, используемое в бетоне как заполнитель (песок, щебень, гравий).
Особенно опасно проявление коррозии арматуры в конструкциях, подвергающихся значительным нагрузкам. При этом неважно, какой марки использовался бетон: при разрушении арматуры строительная конструкция приходит в негодность.
Разумеется, напрашивается вывод: продлить срок службы железобетонной конструкции можно, предусмотрев меры защиты для входящей в состав изделий арматуры от коррозии. Осуществить это не так просто, как кажется, прежде всего потому, что коррозия появляется еще во время заливки бетона в форму изделия (влажность плюс тепло) процесс коррозии не прекращается.
Коррозия арматуры вызвана, как правило, воздействием на железобетон атмосферно-химических факторов, обусловленных как агрессивными компонентами атмосферы (сульфаты, карбонаты, хлориды), так и частыми циклами мороз–оттепель.
Основой защитного действия цементных бетонов на арматурную сталь является щелочной характер влаги в капиллярно-пористом теле бетона, способствующий сохранению химически пассивного состояния поверхности стали. Таким образом, при высокой плотности бетона, надлежащей толщине защитного слоя и отсутствии его повреждений (трещины, сколы, каверны и пр.) арматура в бетоне сохраняется в химически пассивном состоянии долгие годы и десятилетия. К тому же бетон находится в постоянном взаимодействии со средой, которая может либо способствовать его упрочнению и уплотнению, либо разрушать его структуру и снижать прочность, либо уменьшать его способность защищать арматуру. Повышение прочностных характеристик бетона происходит при воздействии на него кислых газов и жидкостей, например углекислого газа, содержание которого в атмосфере промышленных предприятий превышает 0,03%, или теплого влажного воздуха, упрочняющего цементный бетон. Снижение способности бетона препятствовать коррозии арматуры может быть спровоцировано несколькими процессами, результатом которых является невозможность бетона поддерживать пассивное состояние стали вследствие понижения степени щелочности межфазной жидкости или проникания в нее ионов – стимуляторов коррозии. Как правило, это происходит при воздействии сред, содержащих хлориды.
Коррозия носит преимущественно электрохимический характер и протекает на границе металл – раствор электролита. Сталь не будет подвержена коррозии, если электролит при контакте с ее поверхностью имеет достаточно высокий рН, чтобы пассивировать поверхность стали. Когда щелочные свойства на поверхности стали опускаются ниже рН = 8, сталь станет депассивированной, может начаться коррозия. Раствор портландцемента обычно имеет рН = 12,2…12,5, и при изолировании их от воздействия внешней среды это состояние может сохраняться длительное время, поддерживая стальную поверхность в пассивном состоянии.
Одним из основных факторов, способствующих коррозии арматуры, является нейтрализация высокощелочной среды бетона за счет обменной реакции гидроксида кальция в бетоне с кислыми газами в воздухе (в основном СО2). Этот процесс называется карбонизацией бетона:
Сa(OH)2 + CO2 → CaCO3 + H2O.
Процесс карбонизации начинается с поверхности бетонной конструкции с момента ее изготовления и движется вглубь по мере проникновения углекислого газа внутрь бетона. Скорость карбонизации зависит от многих факторов: плотности бетона, температуры и влажности окружающей среды и самой конструкции и др. Достигая арматуры, карбонизация переводит сталь в активное состояние, а поступающие в бетон кислород (окислитель) и влага (электролит) обеспечивают процесс коррозии, проходящий по электрохимическому принципу.
Вторым механизмом коррозионного разрушения арматуры является локальная депассивация арматурной стали при воздействии ионов хлора (Cl–). Ионы хлора – сильнейшие стимуляторы коррозии стали, являющиеся основной причиной возникновения точечной коррозии стержней арматуры. Ионы хлора могут также изначально находиться в бетоне при использовании загрязненных материалов при приготовлении бетонной смеси.
Хлориды оказывают коррозионное воздействие на арматуру вследствие удаления пассивного слоя оксида железа, что вызывает дальнейшее окисление.
Разрушающее действие на бетон и арматуру вызывает и хлорид кальция, вступающий в реакцию с гидратом кальция, присутствующим в бетоне. Результатом реакции является образование оксихлорида гидрата кальция. Разрушающим воздействием на бетон заключается в увеличении объема продукта реакции:
СaСl2 + Сa(OH)2 + H2O → CaO×СaСl2× ×2H2O.
Третьей главной угрозой является растрескивание бетона, происходящее в процессе эксплуатации.
Оно не обязательно является критическим для дальнейшей эксплуатации и долговечности бетона. Величина трещины – вот важный фактор для возникновения коррозии. Микротрещины или незначительные мелкие трещины не рассматриваются как повреждающие бетон, поскольку они зачастую исчезают через какоето время (засоряются). Трещины, которые были идентифицированы как представляющие максимальную опасность коррозии для арматуры, – это параллельные боковые трещины, особенно идущие вдоль рабочей арматуры. В условиях, где растрескивание бетона более допустимых пределов происходит вследствие его чрезмерной усадки, существует угроза долговечности бетона. В этом случае должен быть осуществлен ремонт трещин после полной обработки бетона материалами проникающей гидроизоляции типа «Панетрон».
Еще одним фактором, оказывающим разрушающее действие на бетон и арматуру, являются циклы мороз–оттепель. Вода является катализатором для всех агрессивных компонентов и в описанных выше химических реакций. Влага может стать причиной серьезных повреждений, проникая сквозь поры бетона.
Увеличение объема воды при переходе в лед (на ~9%), различие в коэффициентах линейного расширения продуктов гидратации цемента, клинкерных зерен и зерен мелкого и крупного заполнителя создают предпосылки для появления внутренних напряжений в бетоне при замораживании и оттаивании. Возникающее давление приводит к образованию трещин и разрушению бетона.
В своих рекомендациях по ремонту и восстановлению железобетонных конструкций мы особенно отмечаем коррозионное разрушение арматуры в железобетонных конструкциях вследствие того, что оно может привести к полному разрушению конструкции.
В настоящее время существует ряд способов защитить арматуру в бетоне при ремонте железобетонных конструкций:
- введение в ремонтный состав бетонной смеси полимерных добавок, которые благодаря своим свойствам позволяют без потери прочности создать для арматуры дополнительную защиту;
- замена участков (удаление) с карбонизированным бетоном (рН < 10) нормальным бетоном (рН = 11…13). Недостатком этого метода является неоднородность электрохимических свойств ремонтного участка и ненарушенного бетона;
- обработка поверхности конструкций сеалантами и полимерцементными композитами, которые образуют в порах и трещинах плотную кристаллическую структуру, не пропускающую воду, но позволяющую бетону «дышать»;
- обработка поверхности железобетонной конструкции ингибитором коррозии, который наносят на поверхность бетона; через 10…20 дней на поверхности арматуры образуется защитная пленка;
- обработка поверхности арматуры преобразователями ржавчины;
- обработка арматуры защитным покрытием (гальванизация, покрытие эпоксидным порошком, промышленные окрасочные покрытия, обеспечивающие адгезивную прочность).
Для предупреждения коррозии арматуры и увеличения долговечности железобетонных конструкций необходимо тщательно следить за развитием существующих трещин и выявлять вновь образовавшиеся с определением причин их образования и развития, раковинами и крупными порами в железобетонных конструкциях, а также своевременно и в достаточном объеме реализовывать мероприятия по восстановлению (устройству) защиты железобетонных конструкций от воздействия агрессивных сред.