Авторы: А.М. Добротворский (ЗАО «НПО «Ленкор», СПбГУ),
В.В. Думрауф, Л.М. Романова, Вальковская С.А. (ЗАО «НПО «Ленкор»),
А.С. Дыкман (ООО «Еврохим–СПб–Трейдинг»).Опубликовано в журнале Химическая техника №1/2016
Предметом обсуждения данной статьи является коррозионная стойкость материалов реакторов синтеза изопрена, эксплуатирующихся в ПАО «Нижнекамскнефтехим» – одной из крупнейших нефтехимических компаний
Европы, занимающей лидирующие позиции по производству синтетических каучуков и пластиков в Российской Федерации. Завод по производству изопрен-мономера является крупнейшим бизнес-подразделением ПАО «Нижнекамскнефтехим».
В основу процесса производства изопрена первоначально была положена технология (двухстадийный синтез), разработанная ООО «Нефтехимстарт» (г. Ярославль).
В 2001 г. установка была реконструирована на основе технологии, предложенной специалистами ООО «Еврохим – СПб – Трейдинг» при участии работников завода [1, 2]. В 2008 г. весь процесс производства изопрена был полностью переведен на жидкофазную технологию синтеза изопрена из изобутилена и формальдегида с использованием ортофосфорной кислоты в качестве катализатора (одностадийный синтез) [2, 3]:
С4Н8 + СН2О T = 165°C С5Н8 + Н2О →
Изобутилен Формальдегид Изопрен
Достоинство данного метода в том, что он менее энергоемок, проще в технологическом исполнении, а также образует меньшее количество сточных вод и обеспечивает высокую чистоту изопрена. Внедрение процесса позволило уменьшить удельный расход сырья и тепловой энергии и, таким образом, на 25–30% снизить себестоимость продукции.
Основными реакционными аппаратами производства изопрена-мономера методом одностадийного синтеза являются реакторы Р-12а, Р-13а, Р-12/1,2, Р-13/1,2.
Один из реакторов был переведен на одностадийную схему в 2002–2003 гг., остальные – в 2008 г.
Каждый реактор является аппаратом теплообменного типа с неподвижными трубными решетками (рис. 1).
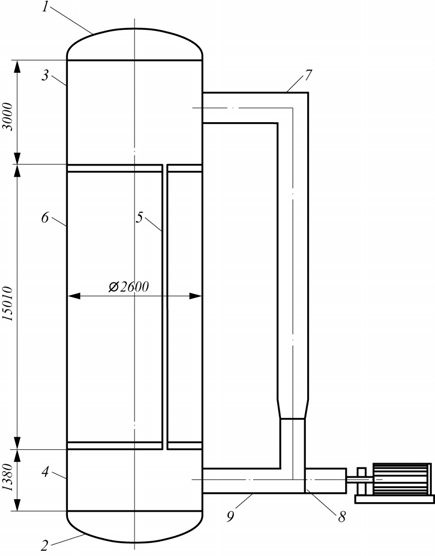
1–5 – трубное пространство; 6 – межтрубное пространство;
7, 9 – циркуляционная труба; 1, 2 – крышки корпуса,
3, 4 – обечайка верхней и нижней частей реактора;
5 – труба теплообменная (199 труб); 6 – обечайка корпуса; 8 – корпус насоса
Химическая реакция происходит в трубном пространстве.
В межтрубное пространство для подогрева реакционной массы подается водяной пар. В качестве катализатора процесса используется ортофосфорная кислота. Из-за высокой коррозионной активности среды трубное пространство реактора материально оформлено высоколегированным сплавом марки SB424 (Япония), близким аналогом которого является железохромоникелевый сплав Инколой 825.
При переходе с двухстадийной схемы получения изопрена на одностадийную остро встала проблема коррозионной стойкости столь высоколегированного сплава.
Изменение технологии привело к необходимости работы реакторов в более агрессивных условиях, чем те, что были заложены при проектировании и выборе конструкционных материалов. Рабочая температура повысилась со 110 до 165°C, концентрация H3PO4 – с 3 до 8%.
Ранее в ходе экспериментов ОАО «ВНИИНефтехим» было установлено, что Инколой 825 в водно-органических растворах фосфорной кислоты корродирует со скоростью до 0,3 мм/год. Опыт эксплуатации реактора с 2003 г. показал, что максимальная скорость коррозии Инколоя 825 составляет 0,4 мм/год.
Специалистами ЗАО «НПО «Ленкор» в рамках проведения экспертизы промышленной безопасности с 1999 г. проводится мониторинг коррозионного состояния реакторов синтеза изопрена. На основании данных толщинометрии основных элементов реакторов за период с 2003 по 2014 г. определены скорости коррозии сплава SB424 и их изменение с течением времени. Результаты представлены на рис. 2.
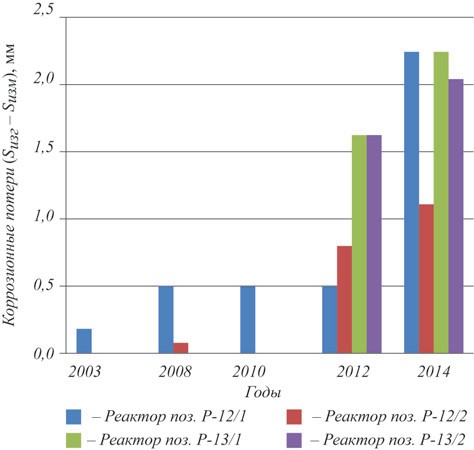
Наиболее сильному коррозионному изнашиванию подвержены элементы трубного пространства (обечайки распределительных камер, теплообменные трубки), где технологической средой является реакционная масса и катализатор процесса – ортофосфорная кислота. Максимальная скорость коррозии зафиксирована для обечайки нижней камеры реактора поз. Р-13/1. Она составляет 0,37 мм/год, что согласуется с данными, полученными в лабораторных условиях ОАО «ВНИИНефтехим».
Сравнение данных за период 2003–2008 гг. и 2008– 2014 гг. показывает наличие двух пиков интенсивности коррозии реакторов: в 2008 и 2012 гг. Первый скачок (2008 г.) логично связать со сменой технологических параметров более агрессивными, тогда как резкое утонение стенок реакторов в 2012 г. сложно соотнести с какими-то внешними факторами. Данное наблюдение не согласуется с предположениями о линейном характере протекания коррозионных процессов в средах производства изопрена, встречающимися в литературе.
В источниках, касающихся теории коррозионных процессов, встречаются упоминания о существовании неустановленных факторов, влияющих на скорость коррозии металлов в агрессивных средах [4–6]. Я.М. Колотыркин, указывая на общность многих черт в анодном поведении различных металлов, отмечает также и то, что природа металла должна налагать на механизм его ионизации свой индивидуальный отпечаток.
Выяснение общности и особенностей кинетики растворения железа, хрома, никеля и их сплавов представляет особый интерес и составляет предмет ряда работ [7].
Анализ установленных зависимостей скоростей активного растворения железа, хрома, никеля и их сплавов от потенциала позволил выявить общую необычную закономерность. Она заключается в том, что для этих металлов свойственные электрохимическим реакциям тафелевские зависимости между скоростью растворения и электродным потенциалом наблюдаются лишь при потенциалах выше некоторого значения, зависящего от природы металла, состава раствора и других переменных. При более низких потенциалах фиксируется отклонение поведения металлов от законов электрохимической кинетики.
Отклонения имеют место в самых различных условиях и носят систематический характер. Для этих эффектов исследователями был предложен термин «аномальное явление при растворении металлов» (или «аномальное растворение»).
Зависимость скорости аномального растворения от природы металла и состава сплава варьируется для различных условий. Например, в достаточно кислых средах при прочих равных условиях эта скорость растет в ряду: никель, железо, хром. Для сплавов железо–хром в тех же условиях с ростом содержания хрома в сплаве скорость аномального растворения сначала возрастает, а затем достигает предела. Скорость аномального растворения железоникелевых сплавов с ростом содержания никеля (при не очень низких его концентрациях) снижается. При добавке к хромистой стали никеля в количестве 25% наблюдается сильное торможение аномального растворения. При этом скорость процесса приближается к скорости растворения чистого никеля.
Помимо механизма растворения металлов в агрессивной среде на скорость коррозии влияет и природа агрессивного компонента: его способность образовывать на поверхности металла пассивирующие пленки, или же наоборот, активировать ее.
Проблема стойкости сплава Инколой 825 в условиях одностадийного синтеза изопрена затронута также в работах ООО «НИУИФ-Инжиниринг». Приведены данные коррозионных испытаний образцов из различных хромоникельмолибденовых сплавов, осуществленных в промышленных условиях работы реакторов. Перечень испытуемых материалов и их химический состав приведен в таблице.
Результаты промышленных испытаний в условиях работы реакторов синтеза изопрена (экспозиция образцов в течение 6…12 месяцев в верхней камере трубного пространства с парогазовой смесью и частично с жидкой фазой):
Сталь или сплав | Средняя скорость
общей коррозии, мм/год |
Incolloy 825 | 0,27 |
904L | 0,47 |
12Х18Н10Т | 0,43 |
Hastelloy C2000A | 0,001 |
Nicrofer 3127 | 0,03 |
Отчетливо видно, что на стойкость материала в исследуемой среде оказывает влияние содержание никеля. Определяющая роль данного легирующего элемента на устойчивость материала в средах производства изопрена подтверждает анализ ряда инцидентов, произошедших в период начала эксплуатации реактора Р-12а по одностадийной схеме. Теплообменные трубы реактора выполнены из коррозионно-стойкого никележелезохромового сплава Инколой-825. Изначально в реакторе были смонтированы трубы, изготовленные в Японии (точные данные об изготовителе отсутствуют). После реконструкции они были заменены холодно-деформированными трубами, изготовленными по стандарту ASTM B163-04 фирмой TTI-TUBACEX TUBOS INOXIDABLES, S.A. (Испания) [8]. В отличие от труб японского производства, отработавших 9 лет, трубы испанской поставки подверглись коррозионному изнашиванию за значительно более короткий срок эксплуатации. После полутора лет работы толщина некоторых трубок уменьшилась до 2,0 мм (при исходной – 5,0 мм), что привело к их разрушению (раздавливанию) в ходе гидравлических испытаний в октябре 2012 г.
Химический состав сталей и сплавов, установленных на промышленные испытания в условиях работы реакторов синтеза изопрена
Элемент |
Содержание элемента,% | |||
Nikrofer 3127 hMo | Nikrofer 4221 (Incolloy 825) | Hastelloy C2000 (alloy) | Cronifer 1925LC (сплав 904L) | |
Ni | 31,50 | 43,53 | Основа | 25,5 |
Cr | 27,00 | 22,21 | 23,0 | 21,0 |
Mn | 1,48 | 0,34 | – | 0,01 |
Si | 0,09 | 0,01 | 0,08 | 0,01 |
Mo | 6,36 | 2,79 | 16,0 | 5,0 |
Cu | 1,24 | 2,02 | – | 1,8 |
Ti | – | 0,93 | 0,01 | – |
C | 0,007 | 0,01 | – | 0,02 |
Co | – | – | – | – |
Fe | Основа | 28,16 | – | Основа |
S | 0,004 | 0,004 | – | 0,002 |
P | 0,013 | – | – | 0,02 |
Al | – | 0,03 | – | – |
N | 0,203 | – | – | 0,05 |
Сравнительный анализ химического состава труб японской и испанской поставки [9] показал, что основным различием между японским и испанским материалом является количественное соотношение основных компонентов сплава: железа, хрома и никеля (рис. 3).
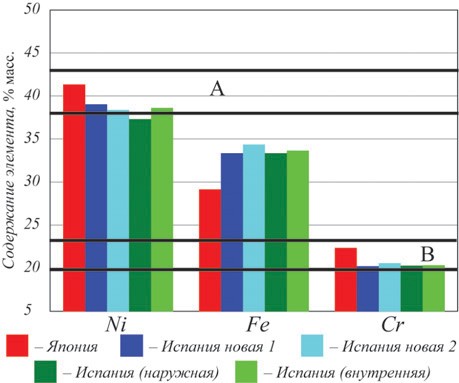
Жирными горизонтальными полосами выделены пределы содержания никеля (область А) и хрома (область В)
в сплаве по стандарту ASTM B163-04
В японской трубе содержание и никеля и хрома выше на несколько процентов, чем в испанской, в то время как железа примерно на 5% масc. меньше. При этом в испанских трубах (во всех образцах) содержание никеля находится на низшем пределе, допускаемом стандартом ASTM B 163-04.
Наблюдаемые тенденции в коррозионном поведении хромоникелемолибденовых сплавов в условиях работы узла синтеза изопрена, как и приведенные литературные данные, иллюстрируют необходимость дополнительных исследований механизма коррозии, а также учета полученных данных при выборе материального оформления.
Основной целью логично считать более точное определение нижней границы содержания никеля, хрома и молибдена в сплавах, которая обеспечит стойкость материалов в интересующих условиях. Полученный критерий можно использовать для экспресс-оценки химической стойкости вновь поставляемого оборудования (новые трубные пучки, детали реакторов и др.).
Список литературы
- http://eurochimgroup.com/en/pages/417/7/ Хабибулина В. Стадия одна – изопрена много. Нефтехимик 04.09.2009
- http://1st-name.ru/katalog/ru/kongress/s4/gilmanov Гильманов Х.Х. Новая промышленная технология получения изопрена из формальдегида и изобутилена
- http://eurochimgroup.com/pages/435 Одностадийный процесс (Курарей)
- Флорианович Г.М. Кинетика растворения железа, хрома, никеля и их сплавов в активном состоянии. Дис. д-ра хим. наук. М.: Науч.-иссл. Физ.-хим. Ин-т, 1984.
- Колотыркин Я. М., Флорианович Г.М. Аномальное растворение металлов. Экспериментальные факты и их творческое толкование//Защита металлов. 1984. Т. 20. №1. С. 14-24.
- Колотыркин Я.М., Флорианович Г.М. Аномальные явления при растворении металлов//Итоги науки. Электрохимия. М.: ВИ- НИТИ, 1971, т.7.
- Флорианович Г.М. Кинетика растворения железа, хрома, никеля и их сплавов в активном состоянии. Автореф. дис. д-ра хим. наук. М.: 1984.
- ASTM B 163-08. Standard Specification for Seamless Nickel and Nickel alloys Condenser and Heat-Exchanger Tubes – 12 p.
- Добротворский А.М., Романова Л.М., Латфуллин Р.Ф. ЗАО «НПО «Ленкор» – ОАО «Нижнекамскнефтехим»: техническая диагностика в модернизации производств//Technopolis XXI. 28, 2013.