Автор: Д.Г. Давыдова, А.В. Жуков, Д.Б. Журавлев (ООО «Стратегия НК»).
Опубликовано в журнале Химическая техника №7/2015
По данным статистики, полученной в ходе проведения технического диагностирования более 400 сосудов и аппаратов опасных производственных объектов в период 2014–2015 гг., доля объектов, имеющих недопустимые дефекты, достигает 20%. В настоящее время большая часть технологического оборудования опасных производств отработала нормативный срок службы и находится в эксплуатации более 30…40 лет. Дальнейшая эксплуатация оборудования возможна на основании обследования технического состояния, установления работоспособности, оценки остаточного ресурса безопасной эксплуатации, а также на основе анализа экономической эффективности, с учетом необходимости дальнейшей модернизации и перевооружения. Как показывает опыт работы последних лет, необходимость проведения комплексного обследования оборудования не ограничивается плановой экспертизой промышленной безопасности технических устройств. В условиях, когда безопасность эксплуатации является приоритетным направлением деятельности предприятий нефтехимической и нефтеперерабатывающей отраслей, на первый план выходят задачи оценки текущего состояния оборудования при входном контроле, после модернизации отдельных компонентов сложных систем, во время плановых испытаний и т.д.
В общем случае техническое диагностирование сосудов предполагает использование целого комплекса методов неразрушающего контроля, среди которых можно выделить локальные (визуальный контроль, контроль проникающими веществами, ультразвуковой и радиографический методы контроля) и интегральные методы (метод магнитной памяти металла, акустико-эмиссионный контроль). Все перечисленные подходы имеют свои преимущества и недостатки. Повышение точности измерений, расширение границ применения, а также учет объективных ограничений методов контроля определяет вектор дальнейшего развития отрасли неразрушающего контроля.
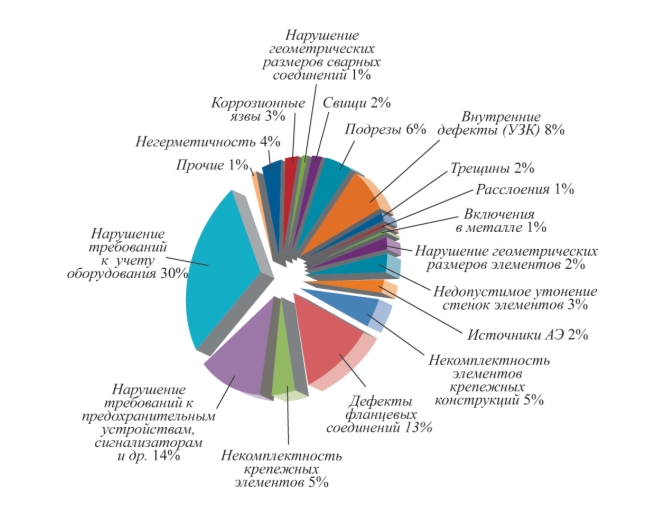
При комплексном обследовании сосудов выявлено, что нарушения требований промышленной безопасности в третьей части случаев связаны с имеющим место ненадлежащим учетом и содержанием оборудования (рис. 1). В частности, речь идет об отсутствии паспортов сосудов, информационных табличек, размещаемых на оборудовании и устанавливающих разрешенные параметры работы и периодичность обследований. Выявленные нарушения в отношении установленных предохранительных устройств, средств учета и контроля параметров работы, сигнализаторов, функционирования заземлений и др. составляют 14% их общего числа.
Часто причинами появления дефектов сосудов и аппаратов являются нарушения режима сварочного процесса, вследствие чего происходит образование непроваров, сквозных свищей, подрезов, раковин, подповерхностных дефектов сварных соединений и т.п. Дефекты такого типа являются источниками нескомпенсированных напряжений в области сварного шва и могут инициировать дальнейшее разрушение металла при значительном снижении прочностных характеристик материала в период эксплуатации. При этом среди дефектов сварных соединений превалируют (8%) подповерхностные дефекты (внутренние трещины, непровары), обнаружение которых возможно только с использованием специализированных методов неразрушающего контроля (ультразвуковой и радиографический контроль). Примечательно, что один из самых «популярных» механизмов разрушения устройств нефтехимического комплекса – критическое утонение толщины стенки элементов (корпус, днища, патрубки) вследствие коррозионно-эрозионного изнашивания – характерно только для 3% диагностируемого оборудования.
Практика проведения неразрушающего контроля показывает, что наряду с общим износом оборудования имеют место локальные повреждения. Выявление таких дефектов с использованием стандартных подходов к техническому диагностированию существенно затруднено в связи с тем, что места контроля носят «стандартизованный», унифицированный характер. В этой ситуации перспективным является использование интегральных методов контроля, которые дают информацию о состоянии 100% металла оборудования.
Большую популярность приобретает техническое диагностирование оборудования в режиме мониторинга [1]. Развитие приборной базы неразрушающего контроля, модернизация технологий хранения и обработки информации открывают новые возможности для оценки технического состояния оборудования.
Активно развиваются устройства мониторинга состояния технических устройств, устанавливая новые задачи в области интерпретации результатов, полученных с применением современных систем контроля.
На многих предприятиях вводится автоматизированный учет и хранение информации, связанной с эксплуатацией опасных производственных объектов (паспорта оборудования, графики обслуживания и ремонтов).
По оценкам работ, проведенных в период 2014–2015 гг. (100 единиц оборудования), техническое диагностирование в режиме мониторинга было реализовано в 20% случаев благодаря использованию акустикоэмиссионного (АЭ) метода контроля [2]. Основным преимуществом данного метода является возможность 100%-ного контроля металла оборудования в условиях текущей эксплуатации.
На диаграмме (см. рис. 1) доля источников АЭ, указывающих на возможные дефекты, составляет всего 2%. Это связано не только с характером их появления, но и с ограничениями применения АЭ-контроля в рамках комплексного диагностирования опасных производственных объектов.
В практике проведения технического диагностирования оборудования имеют место случаи, когда проведение АЭ-контроля существенно затруднено из-за наличия высокого уровня помех. Одним из динамично развивающих направлений в области АЭ-контроля является расширение его возможностей путем разработки помехоустойчивого метода контроля [3]. Обеспечение возможности проведения АЭ-контроля в высокозашумленных условиях особенно актуально в рамках реализации мониторинга состояния оборудования опасных производственных объектов. Концепция построения системы мониторинга технологического оборудования предполагает использование системы беспороговой регистрации данных акустической эмиссии, построение количественных критериев оценки технического состояния объекта контроля с использованием статистических методов. Предложенный подход обладает адаптивным характером работы, позволяющим учитывать характерные особенности сигналов, обусловленные характером источника, а также условиями контроля. Данный метод контроля прошел необходимые лабораторные исследования, показав высокий уровень достоверности, успешно зарекомендовал себя при проведении технического диагностирования реальных технических устройств как при наличии стационарного шума, так и в условиях наличия высокоамплитудных нестационарных помех.
В приведенной на рис. 1 статистике не отражены дефекты металла, возникающие при изготовлении оборудования. Сложность состоит в том, что дефекты такого рода по разным причинам не всегда выявляемы на этапе входного контроля владельцем оборудования. При этом дефекты структуры могут существенно повлиять на безопасность эксплуатации оборудования в дальнейшем.
Иллюстрацией сказанного является ситуация, сложившаяся на одном из нефтехимических предприятий и связанная с аварийным выходом из строя оборудования вследствие разрыва металла. Стандартные подходы к техническому диагностированию не позволили установить механизм разрушения устройств и его возможные причины.
Темпы развития науки и технологий открывают новые возможности оценки состояния оборудования.
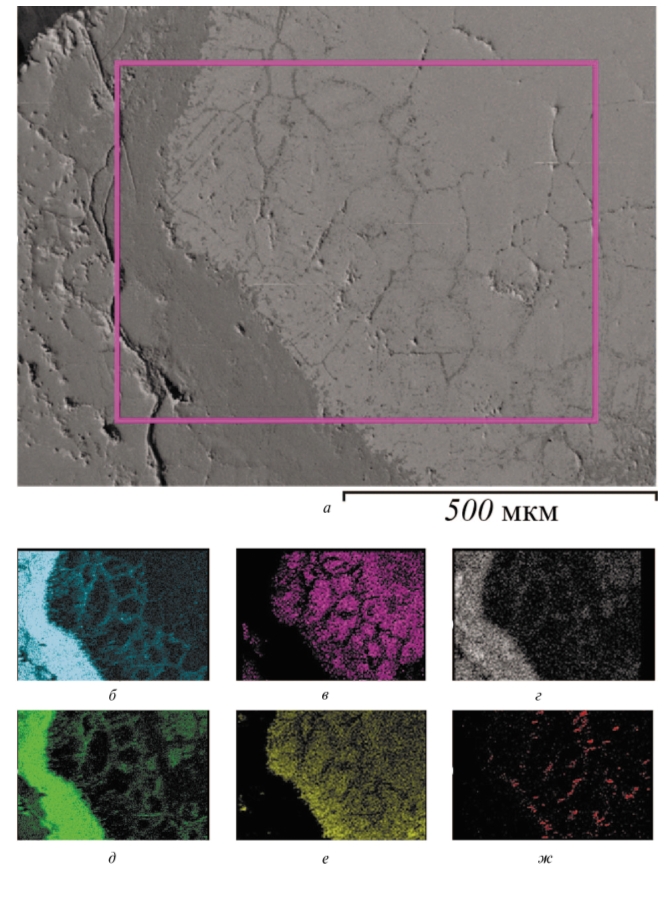
в – содержание железа; г – содержание марганца; д – содержание хрома;
е – содержание никеля; ж – содержание титана
Положительно зарекомендовал себя опыт применения электронно-зондового микроанализа макрои микроструктуры металла. Результаты, полученные при металлографическом исследовании материала, представлены на рис. 2, а, где видна характерная структура окисления вдоль границ зерен, при этом нарушается механическая связь между соседними зернами. Такая картина характерна в случае межкристаллитной коррозии коррозионно-стойких сталей [4]. При такой разновидности коррозии вдоль границ зерен выделяются фазы, обогащенные хромом (главным образом, карбиды на основе хрома – Cr23C6). Эти карбиды концентрируются на границах зерен, иногда образуя сплошную цепочку.
При этом участки, непосредственно окружающие карбиды Cr23C6, оказываются существенно обедненными по хрому (менее 12%) и становятся электрохимически активными. Микроанализ выполнен с использованием сканирующего электронного микроскопа FE-SEM Zeiss Σigma VP.
В ходе исследования получена информация о локальном химическом составе межзеренных пространств в исследуемом материале.
Результаты электронно-зондового микроанализа приведены на рис. 2, б–ж. Распределение хрома (см. рис. 2, д) позволяет сделать предположение о выделении карбидов хрома по границам зерен и обеднению по хрому приграничных областей. Эти процессы характерны для межкристаллитной коррозии. Высокое содержание кислорода в межзеренном пространстве (см. рис. 2, б) свидетельствует о наличии прокорродировавшей зоны вдоль границ зерен металла (оксиды металлов).
Таким образом, электронно-зондовый микроанализ подтвердил ранее высказанное предположение о том, что основным механизмом разрушения материала компенсатора является межкристаллитная коррозия.
На практике показатели предельного состояния оборудования лежат в основе принципа назначения срока дальнейшей безопасной эксплуатации. В последнее время участились случаи, когда стандартные задачи определения остаточного ресурса при экспертизе промышленной безопасности предполагают использование нетривиальных подходов.
Таким образом, комплексное диагностирование сосудов, работающих под давлением, заключается в следующем:
- в адаптации механизмов неразрушающего контроля к условиям диагностирования без вывода объекта из эксплуатации, что в некоторых случаях позволит существенно упростить процедуру проведения технического диагностирования действующего оборудования без потери эффективности контроля;
- в использовании инновационных разработок в области оценки состояния металла и конструкций;
- в реализации многофакторного анализа механизмов повреждения, внедрении передовых методов неразрушающего контроля;
- в комплексном подходе к диагностике, использовании интегральных методик контроля.
Список литературы
- Шитов Д.В., Давыдова Д.Г., Журавлев Д.Б. Повышение энергоэффективности теплоносителей с применением систем мониторинга технологических параметров//ТехНадзор. 2014 г. №2(87).
- ПБ 03-593–03. Правила организации и проведения акустико-эмиссионного контроля сосудов, аппаратов, котлов и технологических трубопроводов. Утв. постановлением Госгортехнадзора России от 09.06.03 №77.
- Шайбаков Р.А., Давыдова Д.Г., Кузьмин А.Н., Абдрахманов Н.Х., Марков А.Г. Помехоустойчивый метод акустико-эмиссионного мониторинга резервуаров// Нефтегазовое дело: электрон. науч. журн. 2013. №4. URL:http://www.ogbus.ru/authors/ ShaybakovRA/ShaybakovRA_2.pdf
- Колотыркин Я.М., Княжева В.М. Итоги науки и техники. Сборник. Серия: Коррозия и защита от коррозии. 1974. Т. 3. М.: ВИНИТИ.