Авторы: Я.И. Билык, И.Е. Кухарев, В.С. Марцинковский (ООО «ТРИЗ»).
Опубликовано в журнале Химическая техника №12/2016
Изменения на энергетическом рынке, связанные с увеличением стоимости энергоресурсов, ставят перед предприятиями химической промышленности сложные задачи, связанные с повышением объемов выпускаемой продукции и с улучшением ее качества без дополнительных затрат на модернизацию производства.
Повышение эффективности производства аммиака путем увеличения производительности установок с 1 360 до 1 800 т/сут приводит к изменению режимов работы компрессоров, снижению эффективности процесса сжатия. В связи с этим существенно возрастает газодинамическая нагрузка на роторы турбокомпрессоров (ТК) синтеза-газа, что приводит к повышенным вибрациям роторов, уменьшая запас несущих и демпфирующих сил, и, как следствие, снижает надежность работы ТК синтеза-газа. Существующие штатные узлы (опорные подшипники, плавающие уплотнения, лабиринтные уплотнения, соединительные муфты) не обеспечивают двухгодичный пробег (изначально регламент обслуживания предусматривал периодичность обслуживания 1 год). При возросших нагрузках (увеличение производительности технологической линии с 1 360 до 1 800 т/сут) штатные узлы корпуса низкого давления не обеспечивают и годовой пробег. Проблемы, возникающие при эксплуатации ТК синтез-газа, их причины и рекомендации по их устранению приведены в работах [1–6].
Актуальность повышения надежности и эффективности компрессоров синтез-газа вызвана следующими причинами:
- производства аммиака построены в 70-е годы прошлого века; инженерные решения, заложенные в проект, еще раньше;
- продолжительность эксплуатации превысила установленный ресурс;
- сложные сильно нагруженные многосоставные агрегаты работают в технологических линиях без резерва с межремонтным пробегом не менее двух лет;
- штатные узлы не обеспечивают пробег ТК в продолжение 2–6 лет.
- при производстве 1 300 т/сут аммиака требуется КПД агрегата ~78%, при росте производительности до 1 800 т/сут КПД падает до 74% и не соответствует современному уровню – 88%.
Опыт эксплуатации показал, что штатные узлы (подшипники, концевые плавающие уплотнения, лабиринтные уплотнения, зубчатые муфты) не соответствуют современному уровню, не обеспечивают двухгодичный пробег ТК, а в случае увеличения производительности на 20–38% пробег не превышает одного года даже с модернизацией проточной части корпусов среднего и высокого давления (КСД, КВД) без модернизации корпуса низкого давления (КНД).
Модернизации компрессора синтез-газа, проведенные разными фирмами, были выполнены на ряде предприятий химической отрасли с целью увеличения производительности с 1 360 до 1 700 т/сут. В ходе модернизации выполнялась замена ротора и внутренних корпусов среднего и высокого давления; корпус низкого давления модернизации не подвергался. Эксплуатация модернизированных компрессорных агрегатов на различных предприятиях показала, что КНД работает за пределами устойчивой зоны (запас демпфирующих сил недостаточен для подавления возбуждающих сил) и характеризуется высокими уровнями вибрации. Абсолютная вибрация достигает 12 мм/с. Виброобследование корпуса показывает наличие в спектре вибрации низкочастотной спектральной составляющей. Причиной повышенной вибрации является потеря устойчивости вращения ротора. Потеря устойчивости происходит в машинах, рабочая скорость вращения ротора которых равна или превышает удвоенную первую критическую скорость и является следствием действия на ротор аэродинамических сил, возросших в связи с увеличением производительности, и циркуляционных сил в лабиринтных уплотнениях. Она сопровождается автоколебаниями ротора на частоте, близкой к первой критической, т.е. на рабочем технологическом режиме ротор работает в неустойчивой зоне эксплуатации.
Причины динамической неустойчивости
По выполнении анализа неудовлетворительной работы КНД, а также характера разрушения узлов, деталей и спектров вибраций были определены следующие причины.
Имеющегося штатного запаса демпфирующих сил (ΣFд/ΣFв = 34 400/26 000 = 1,32) недостаточно для работы на режиме остановки по блокировке и на режимах как повышенной (потери мощности NКНД = 3,41 МВт), так и пониженной производительности.
Разрушения вызваны резонансными автоколебаниями, возникшими из-за совпадения собственной частоты колебательной системы, равной первой критической частоте ротора, с частотой возмущающих аэродинамических сил. Возмущающими силами являются низкочастотные аэродинамические силы, возникшие в связи с работой компрессора на повышенной производительности из-за рассогласования проточной части корпуса КНД, которые усиливаются аэродинамическими циркуляционными силами в межсекционном и покрывных лабиринтных уплотнениях рабочих колес, а также аэродинамические силы, возникающие из-за несовпадения каналов рабочих колес и каналов кольцевых диффузоров.
Потеря устойчивости и автоколебания ротора на частоте, близкой к первой критической, под действием аэродинамических циркуляционных сил, так как выполняется условие nр > 2n1кр (здесь nр – рабочая частота вращения ротора).
Устранение динамической неустойчивости КНД
Для устранения причин неустойчивой работы КНД необходимо:
- снизить возбуждающие аэродинамические силы из-за рассогласования характеристик КНД и требуемого технологического режима;
- уменьшить возбуждающие аэродинамические силы изза смещения каналов рабочих колес и каналов кольцевых диффузоров;
- устранить циркуляционные силы;
- увеличить демпфирующие силы;
- увеличить жесткость опорных и уплотнительных узлов;
- увеличить жесткость ротора.
Модернизация КНД турбокомпрессора синтез-газа
Поскольку изначально при проектировании ТК синтез–газа КНД был наиболее неустойчив, при эксплуатации на режиме повышенного расхода аэродинамические силы, действующие на его ротор, возрастают, что, в свою очередь, приводит к росту низкочастотной вибрации, совпадающей по частоте с собственными частотами ротора. Работа КНД в таком режиме приводит к разрушению штатных подшипников, плавающих уплотнений, износу лабиринтных уплотнений проточной части, что обусловливает увеличение протечек газа по ступеням и снижение эффективности сжатия корпуса и, как следствие, еще больший рост амплитуды вибрации, превышающей допустимые нормы.
Первый этап. Были реализованы решения ТРИЗ® для обеспечения устойчивой работы КНД компрессора синтез–газа на производительности 1 580…1 700 т/сут с сохранением межосевого расстояния.
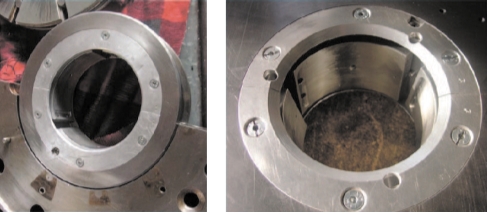
Комплектация штатного корпуса НД узлами надежности ТРИЗ®:
- демпферные опорные подшипники ТРИЗ® (рис. 1);
- антициркуляционные лабиринтно-лунковые уплотнения ТРИЗ® рабочих колес (рис. 2);
- межсекционное лабиринтно-лунковое уплотнение с полимерными вставками (рис. 3);
- плавающие уплотнения ТРИЗ® с шестью демпферными колодками, дополнительным демпфером и упругим кольцом жесткости (рис. 4).
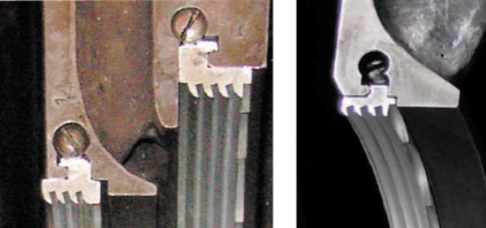
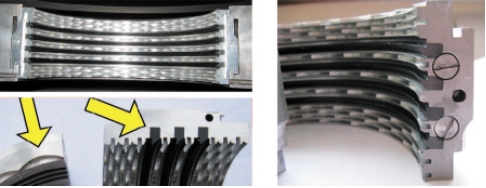
В результате работ первого этапа получены следующие результаты:
- возможность эксплуатации компрессорного агрегата на режимах с производительностью в диапазоне 1 580…1 720 т/сут продукционного аммиака;
- улучшение вибрационного состояния агрегата в целом;
- отсутствие разрушений подшипниковых и уплотнительных узлов при многократных технологических остановках, что позволяет осуществлять быстрый запуск без выполнения ремонтных работ.
Примеры выполнения первого этапа модернизации:
- компрессор поз. 103J, цех Ам-3, ОАО «Гродно Азот» (Беларусь) – до выполнения работ по модернизации с уменьшением межопорного расстояния;
- компрессоры поз. 103J, цехов Ам-1 и Ам-2, АО «Одесский Припортовый Завод» (Украина) – до выполнения работ по модернизации с уменьшением межопорного расстояния;
- компрессор поз. 103J, цех А5, ПАО «Черкассы Азот» (Украина);
- компрессор поз. 103J и компрессор поз. К-401, ОАО «Череповецкий Азот», Россия.
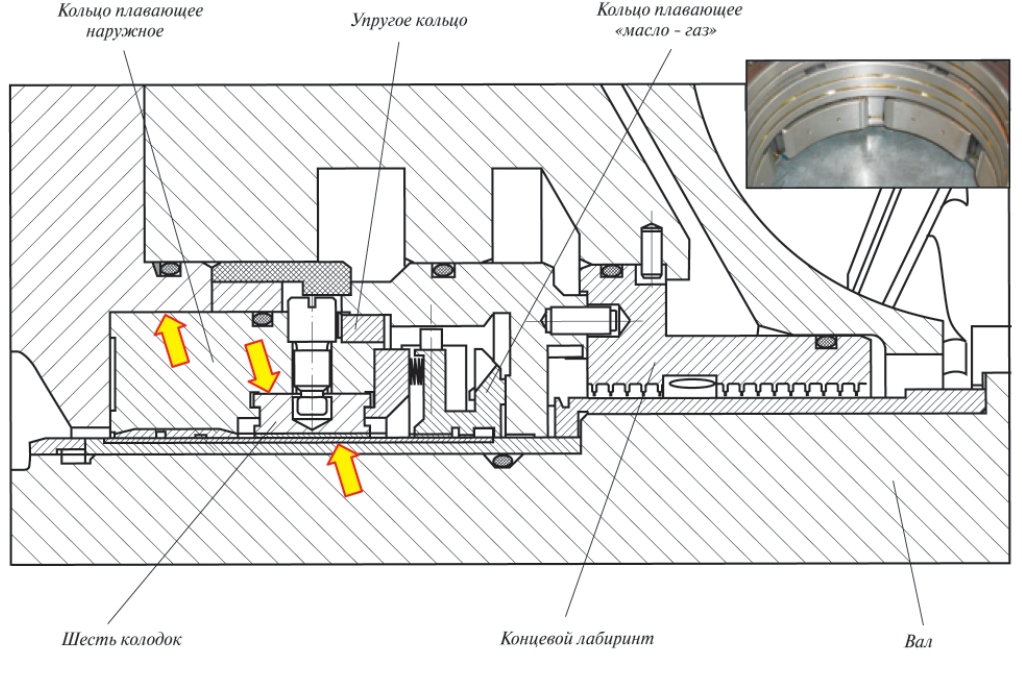
Второй этап. Реализация решений ТРИЗ® для обеспечения устойчивой работы КНД компрессора синтезгаза на производительности 1 700 т/сут и выше с уменьшением межосевого расстояния осуществлялась после анализа причин неустойчивой работы КНД со схемой расположения рабочих колес 5 + 5 в результате рассмотрения технических решений [7, 8], предложенных руководством ОАО «ОПЗ» и ОАО «Гродно Азот». Был установлен следующий объем работ:
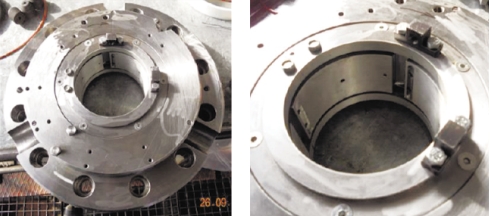
- установка опорного демпферного подшипника ПД-114 (сторона паровой турбины поз.103-JT). Для увеличения жесткости подшипник выполнен неразъемным (рис. 5);
- установка опорно-упорного подшипника ПДУ-114 новой конструкции с демпфером
Рис. 6. Опорно-упорный подшипник ПДУ-114 КНД (463 В5/5) (рис. 6). Опорная часть подшипника смещена в сторону масляного уплотнения для уменьшения межопорного расстояния на 125 мм, что позволило увеличить жесткость ротора и повысить первую критическую частоту. Посадка упорного диска на ротор осуществляется по конусной гидропрессовой посадке, что позволяет избежать задиров и фреттингкоррозии на посадочной поверхности ротора. Демпфер выполнен как крышка опорно-упорного узла и представляет собой трехколодочный демпферный подшипник с валом диаметром 89 мм;
- монтаж ступенчатого межсекционного лабиринтнолункового уплотнения с отверстиями, выполненными из области высокого давления под углом к оси против
Рис. 7. Межсекционное лабиринтно-лунковое уплотнение КНД направления вращения ротора (рис. 7). Наличие лунок позволяет снизить влияние на ротор циркуляционных сил, вызывающих аэродинамическое возбуждение.
Цель отверстий – подвод газа с закруткой обратной направлению основного потока для устранения автоколебаний газодинамической природы. Впервые было реализовано антициркуляционное ступенчатое уплотнение высокого давления с протечками газа в 1,7 раза меньше, чем у существующих уплотнений;
- установка лабиринтно-лунковых уплотнений проточной части. Цель установки таких лабиринтов та же – снижение влияния на ротор циркуляционных сил, вызывающих аэродинамическое возбуждение;
- установка концевых масляных уплотнений с плавающими кольцами;
- уплотнение имеет шесть демпферных колодок, дополнительный демпфер (масляная пленка) и упругое кольцо жесткости. Демпферные колодки, установленные в наружном плавающем кольце, обеспечивают не только его надежное центрирование, но и эффективно демпфируют колебания ротора. В процессе гашения вибрации ротора участвуют три масляные пленки с обратной связью: первая – между валом и колодкой, вторая – между колодкой и наружным плавающим кольцом и третья – масляная пленка полости демпфирования наружного плавающего кольца (в эту полость масло подается от трех колодок). Принцип действия упругого кольца жесткости основан на том, что оно поочередно контактирует своей внутренней и наружной поверхностью с выступами, расположенными соответственно на плавающем кольце и на корпусе уплотнения. Сечение упругого кольца (а также размеры и число выступов) подобраны таким образом, что при действии нагрузки на плавающее кольцо уплотнения, превышающей силу его прижатия к корпусу, упругое кольцо прогибается в пределах зазора между плавающим кольцом и корпусом уплотнения. При этом со стороны упругого кольца возникает сила реакции, действующая на плавающее кольцо и направленная в сторону, противоположную его смещению. Тем самым создается дополнительная жесткость узла уплотнения;
- доработка вала штатного ротора (рис. 8) в месте установки опорно-упорного узла, установка конусной втулки, упорного диска, гайки (ОАО «ОПЗ»);
- изготовление нового вала с насадкой на него штатных рабочих колес (ОАО «Гродно Азот»).
Рис. 8. Модернизированный КНД с установленными узлами
В октябре 2012 г. ООО «ТРИЗ» была проведена модернизация двух КНД ТК синтез-газа поз.103J в ОАО «ОПЗ» и ОАО «Гродно Азот».
Результаты модернизации КНД поз. 103J, (цех АМ-3, ОАО «ГРОДНО АЗОТ»). До модернизации агрегата первая критическая частота вращения ротора низкого давления составляла 4 250 об/мин (т.е. корпус работал за удвоенной первой критической частотой), после модернизации на пуске – 5 280…5 480 об/мин.
Рабочая частота (9 500…10 400 об/мин < 10 560… 10 960 об/мин) меньше удвоенной первой критической частоты, и после выполненной модернизации ротор находится в зоне устойчивой работы.
Результаты модернизации КНД поз. 103J, АМ1 (ОАО «Одесский припортовый завод»). После первой модернизации агрегата первая критическая частота ротора низкого давления составляла 4 600…5 400 об/мин, после второй модернизации на пуске – 5 600…6 000 об/мин.
Рабочая частота (10 800 об/мин < 11 200…12 000 об/мин) меньше удвоенной первой критической частоты. После выполненной модернизации ротор находится в зоне устойчивой работы.
В июне 2014 г. в ОАО «ОПЗ» был проведен регламентный ремонт производства аммиака, во время которого выполнена ревизия КНД ТК синтез-газа. Состояние модернизированных узлов представлено на рис. 9.
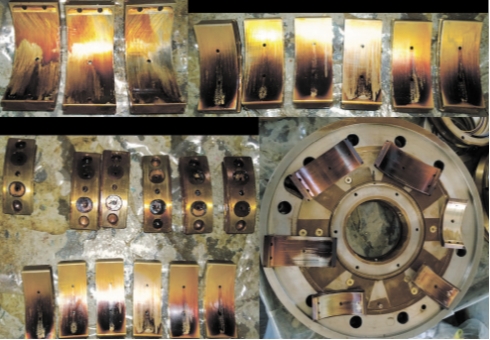
После осмотра и замеров, подтвердивших их соответствие формулярным размерам, сделан вывод об их дальнейшем использовании.
О стабильности характеристик узлов свидетельствует также и вибрационные характеристики которые в процессе эксплуатации сохранились, несмотря на то, что в январе 2014 г. произошла остановка агрегата по причине отключения электроснабжения. Несмотря на внезапную остановку по блокировке на полной нагрузке агрегата ТК успешно выдержал этот «стресс». После пуска ТК все его параметры сохранились.
Величина всплытия роторов на масляной пленке (обычно повышенная) характерна для демпферных подшипников «ТРИЗ». Уровень общей вибрации – в пределах категории «хорошо», т.е. до 40 мкм. На КНД в точках №№ 1 и 2 практически отсутствует субгармоника 80…90 Гц. При этом при измерении вибрации на корпусе имеются следы субгармонических колебаний до 0,5 мм/с, что свидетельствует об аэродинамической составляющей воздействия на ротор. Среднее положение оси ротора стабильно как по горизонтали, так и по вертикали, что свидетельствует об отсутствии просадки и износа несущей поверхности баббитового слоя.
Значение nкр. при пуске не изменилось, что свидетельствует об отсутствии какихлибо конструктивных изменений в системе ротор–корпус–опоры. Таким образом, правильность решения о проведении модернизации КНД с переходом на «пятиопорный» ротор потвердилась.
Третий этап. Рассматриваются решения ТРИЗ®, направленные на повышение надежности и эффективности работы агрегата. На этом этапе модернизации ТК синтез-газа в цикле производства аммиака рассматривается замена штатных проточных частей (внутреннего корпуса и ротора) модернизированными, рассчитанными на повышенную производительность и эффективность.
Эффект достигается за счет оптимизации геометрии сменной проточной части и согласования ее параметров с требуемыми технологическими параметрами.
Замена существующих проточных частей компрессора новыми, согласованнымми с оптимумом технологического режима, обеспечит повышение эффективности сжатия компрессора до 5–8% и снизит аэродинамическую нагрузку на ротор. Комплексное применение узлов ТРИЗ® повышает эффективность работы ТК от 2,5 до 5%.
При замене проточных частей необходимо сохранить модернизированные опорную и уплотнительную системы для увеличения демпфирующих сил и изменения критических частот для обеспечения устойчивой работы ТК.
В данный момент проведены газодинамические расчеты корпусов сжатия компрессора поз.401 с оптимумом производительности ~1 750 т/сут.
На основании расчетов была спроектирована и изготовлена ступень сжатия, с которой будут сняты основные газодинамические характеристики на стенде аэродинамических испытаний разработанном и изготовленном ТРИЗ®. После подтверждения расчетов будут изготовлены полномасштабные проточные части компрессора поз.401.В
Повышение эффективности производств аммиака увеличением нагрузки ТК синтез-газа требует модернизации всех корпусов компрессора и в первую очередь КНД. Штатные опорные, опорно-упорные, уплотнительные узлы не могут обеспечить двухгодичный и более длительный межремонтный пробег ТК. Наибольшая эффективность достигается при комплексной модернизации совместно со сменной проточной частью. В случае увеличения производительности с 2 000 т/сут и более необходимо рассматривать также и новые компоновки ТК с использованием современных схем. При этом резко увеличатся экономичность, надежность и массогабаритные показатели компрессорного агрегата. Не следует при этом забывать о современных системах защиты, контроля, диагностики и системах автоматического управления.
Разработанные и апробированные современные узлы обеспечивают несущую и демпфирующую способность, которая сегодня не имеет аналогов. Замена штатных узлов предлагаемыми обеспечит расширение диапазона эксплуатации ТК, надежную работу на переходных режимах, стабильную высокоэффективную работу в межремонтный период, сократит сроки проведения ремонтных работ.
Список литературы
- Витусевич А.Б., Копнин В.А., Проноза В.А., Опаренко В.И., Гриценко В.Г. Повышение надежности компрессоров синтезгаза// В сб. «Безопасность эксплуатации компрессорного и насосного оборудования», 2–5 октября, Одесса: 2001.
- Марцинковский В.С., Краевский В.Н., Рыбальченко О.П. Модернизация турбокомпрессора синтез газа//Труды 11-й междунар. науч.-техн. конф. «Герметичность, вибронадежность и экологическая безопасность насосного и компрессорного оборудования». Сумы: изд-во СумГУ, 2005.Т.
- С. 83–103. 3. Соломатин С.Я., Кадушкин А.С., Краевский В.Н., Демидов В.Н. Исследование влияния прогрева опор центробежного компрессора на взаимное положение валов при работе//Компрессорная техника и пневматика. 2005. №3. С. 12
- Манаба Сага, Казуаки Ивата, Эйджи Хираиши, Норихиса Вада. Модернизация компрессоров и паровых турбин на заводах по производству аммиака с целью повышения производительности и надежности//Компрессорная техника и пневматика. 2009. №4.
- Ив Бидаут, Урс Бауманн, Салим Мохаммед Хамед Аль-Харти. Динамическая устойчивость ротора центробежного компрессора обратной закачки, оборудованного уплотнением HOLEPATTERN – измерения сопоставляются с прогнозами, сделанными учетом эксплуатационных граничных условий//Отчет о работе 38 турбомашиностроительного симпозиума. 2009. С. 251–260.
- Марцинковский В.С. Обеспечение динамической устойчивости корпуса низкого давления турбокомпрессора синтезгаза//Компрессорная техника и пневматика. 2010. №5. С. 20–27.
- Марцинковский В.С., Плякин А.В. Проблемы, возникающие при эксплуатации компрессоров синтез-газа производства аммиака, их причины и рекомендации по их устранению//Сб. докл. семинара «ЭККОН-11» «Ремонт и модернизаци компрессорного и насосного оборудования химических производств». Сумы: Изд-во СумГУ, 2011. Т. 3. С. 36–44.
- Краевский В.Н., Рыбальченко О.П., Марцинковский В.С., Юрко В.И. Обеспечение динамической устойчивости корпуса низкого давления (463В5/5) компрессора синтез-газа поз. 103J//Сб. докл. семинара «ЭККОН-11» «Ремонт и модернизаци компрессорного и насосного оборудования химических производств». Сумы: Изд-во СумГУ, 2011. Т.3. С. 36–44.