Авторы: П.В. Николаев, С.В. Нефедьев (ООО «ГОЛИАФ»).
Опубликовано в журнале Химическая техника №12/2016
Современные производственные предприятия, как правило, представляют собой сложные административные структуры, в которых множество подразделений выполняют смежные действия. Каждое подразделение, каждый специалист нуждается в применении современных систем учета, мониторинга и обработки информации.
Различным подразделениям производственных предприятий приходится собирать, накапливать и обрабатывать разнообразную информацию, необходимую для нескольких условно-самостоятельных укрупненных направлений деятельности:
- учет перечня оборудования, его характеристик, установок, перемещений и времени наработки с учетом условий эксплуатации;
- планирование и учет ремонтов и технических обслуживаний оборудования;
- планирование и учет поверок, аттестаций и сертификации приборов и автоматики;
- планирование и учет материально-технического оснащения (запасных частей и расходных материалов) в отношении проводимых ремонтов оборудования;
- планирование человеческих ресурсов с учетом необходимой квалификации специалистов, распределение автотранспорта и вспомогательного оборудования при выполнении ремонтов собственными силами;
- управление взаимоотношениями с подрядными организациями, осуществляющими ремонты и обслуживание оборудования;
- корректировка производственного плана с учетом финансовых требований, сформированной годовой программы ремонтов и фактически сложившейся ситуации.
Каждое из этих направлений требует создания программно-аппаратной инфраструктуры и хранения больших массивов той информации, которая может потребоваться при расчетах и управленческом анализе в различных географически распределенных местах на территории деятельности предприятия.
Особенно актуальным является создание соответствующих автоматизированных информационных систем для предприятий химической, нефтехимической, нефтеперерабатывающей, газовой, энергетической и других смежных отраслей промышленности, осуществляющих непрерывный производственный цикл с применением химической техники. Это связано как с повышенной потенциальной опасностью химических производств, так и с особой социальной значимостью такого рода предприятий. Следовательно, перед такими предприятиями особо остро стоят задачи внедрения программных комплексов, осуществляющих управление паспортизацией и ремонтами оборудования, расширения функциональных возможностей уже эксплуатирующихся программных комплексов, сокращения количества пользовательских ошибок при работе с ними, сокращения временных затрат на паспортизацию оборудования, а также повышения эффективности процессов управления ремонтами оборудования в целом.
Существующий на практике подход к внедрению и сопровождению информационных систем, осуществляющих управление процессами паспортизацией и ремонтами оборудования, при всех его несомненных достоинствах обладает существенным недостатком: процесс управления ремонтами оборудования зачастую рассматривается локально, в рамках производственной деятельности и в «отрыве» от общего экономического управления предприятием [1]. Функции формирования графиков планово-предупредительных ремонтов, функции учета оборудования, функции учета выполненных ремонтов и поверок не синхронизированы с управленческим и бухгалтерским учетом, а, значит, не учитываются при производственном планировании.
В то же время обзор существующих решений и примеров внедрения информационных систем, предназначенных для управления паспортизацией и ремонтами энергетического оборудования, выявил ряд интересных направлений. Так, в статье [2] представлена очень удобная система организации графика ППР путем наложения на календарь элементов справочника оборудования и агрегатов. В статье [3] определяются несколько важных этапов (разработка графиков ППР, выполнение ремонтов, взаимодействие с исполнителями, контроллинг) и подробно рассмотрен процесс планирования графиков ремонтов. Наиболее интересной в научном плане является работа [4], где предложен алгоритм принятия решений по ремонту энергооборудования с использованием искусственных нейронных сетей.
Проведенный анализ подтверждает важность применения соответствующих регламентов синхронизации действий различных ремонтных подразделений при планировании своих ремонтных программ. Так, в целях сокращения временных затрат технологически связанное между собой оборудования выгоднее выводить в ремонт совместно (рис. 1) и, наоборот, при наличии ресурсной возможности стремиться не ремонтировать одновременно технологически не связанные между собой группы оборудования, оставляя дублирующие агрегаты в «горячем» и «холодном» резерве.
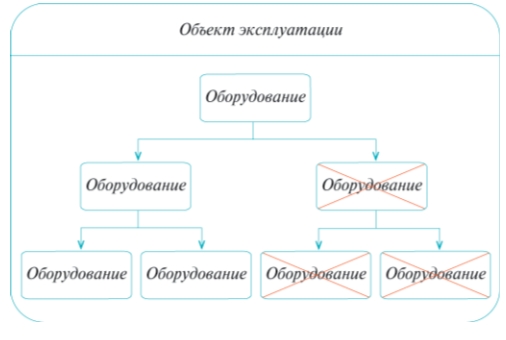
В связи с этим в информационных системах управления ремонтами должны быть инструменты обмена информацией: автоматически рассчитанный график ППР должен автоматически формировать ремонтную документацию, готовить информацию для расчета материальных и трудовых ресурсов и для прогнозирования аварий на основании их тотальной регистрации в специализированных базах данных. В свою очередь, графики ППР должны формироваться на основе электронных паспортов агрегатов и оборудования и согласовываться как с планово-экономическим отделом предприятия, так и со службой главного энергетика. Несоблюдение этих подходов к управлению планово-предупредительными ремонтами может приводить к срыву финансовых планов предприятия, а также делает невозможным переход от планово-предупредительных ремонтов к ремонтам с учетом фактического индекса технического состояния оборудования.
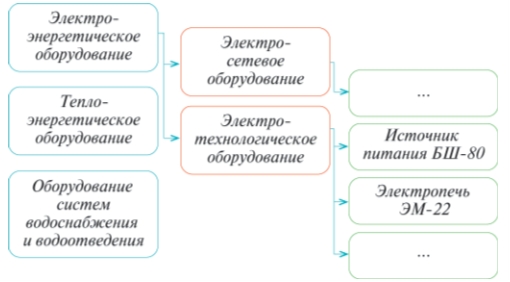
Таким образом, первой важной задачей подготовки к автоматизации управления паспортизацией и ремонтами оборудования является классификация оборудования по группам (рис. 2.). В результате классификации имеющееся на балансе оборудование необходимо информационно разделить на иерархически вложенные «технические» группы. Количество групп, их наименования, детализация, иерархическая вложенность строго индивидуальны для каждого предприятия и формируются на основании сложившейся на данном предприятии практики ведения учета.
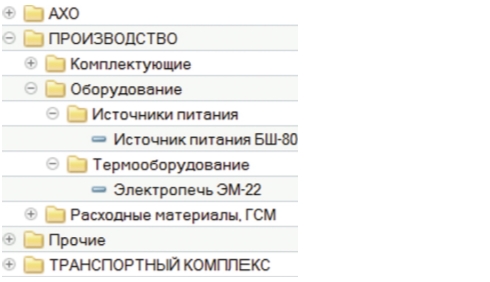
Второй задачей является введение правил классификации номенклатуры оборудования и МТР (материально-технических ресурсов – запасных частей, расходных материалов и т.п) с точки зрения бухгалтерского и управленческого учета. Перечень номенклатуры необходимо также делить по иерархически вложенным группам (рис. 3.). При этом «бухгалтерская» классификация номенклатуры оборудования может отличаться от «технической» классификации фактически используемого оборудования.
Наименования номенклатуры должны формироваться исходя из строгих правил, не допускающих произвольное описание объектов. Например, если с точки зрения человеческой логики «Трансформатор ТР-64» и «Трансформатор ТР64» – это два одинаковых объекта, то с точки зрения информационной системы – это две различные сущности. Такое дублирование наименований номенклатуры приведет к некорректному учету оборудования и искажениям в формируемой отчетности.
Правила ведения номенклатуры и классификации групп предпочтительно вводить в действие с началом какого-то выбранного отчетного периода (квартала или года). Корректировать классификацию групп в течение жизненного цикла эксплуатации информационной системы настоятельно не рекомендуется, так как это приведет не только к некорректному формированию отчетной документации, но и может исказить данные бухгалтерского учета. Таким образом, разработка свода правил, определяющих классификацию номенклатуры, оборудования и МТР является важнейшими аналитическими задачами, которые обязательно должны быть решены до начала внедрения информационной системы управления паспортизацией и ремонтами оборудования.

Важнейшим понятием, применяемым в информационных системах, осуществляющих паспортизацию и управление ремонтами, является электронный паспорт оборудования (ЭП). ЭП – это расчетная функция информационной системы, которая динамическим образом показывает качественные и количественные характеристики оборудования и его элементов, с учетом накопленной информации о различных зарегистрированных событиях, которые произошли с этим объектом паспортизации. Такой информацией может быть дата выпуска оборудования; дата приобретения или передачи в аренду; организационные, технические, и финансовые условия приобретения или аренды; дата ввода в эксплуатацию; параметры амортизации и износа элементов оборудования; межремонтные циклы всего объекта или его узлов и компонентов; требуемые квалификации и трудозатраты ремонтного персонала на производство ремонтов; нормы материальных затрат на каждый вид ремонта и т.п.
Событиями в этой концепции являются факты ввода в эксплуатацию; факты вывода из эксплуатации и остановы; факты проведения плановых и внеплановых ремонтов; факты модернизации, замены комплектующих, аварий и изменений режимов эксплуатации и т.п. Взаимосвязь экземпляра оборудования с местом его установки и технологической картой ремонтов и технических обслуживаний отображена на рис.4.
Основополагающим для создания электронного паспорта оборудования является договор, на основании которого предприятие имеет право эксплуатировать это оборудование (покупка, аренда, субаренда, лизинг, эксплуатация и пр.). С точки зрения информационной системы, договор – это электронный документ, содержащий основные характеристики бумажного, юридически оформленного документа. Например, на основании договора покупки отслеживаются поставщик, партия поставки, гарантийный срок; рассчитываются остаточная балансовая стоимость и другие показатели, существенно влияющие на организацию эксплуатации оборудования. На основании договора аренды отслеживаются арендодатель и дата окончания аренды, планируются сроки платежей. Как видим, учет договорных характеристик представляется очень важным с точки зрения организации корректных управленческих решений по отношению к оборудованию. Отсутствие «привязки» оборудования к договору может приводить к юридическим коллизиям и серьезным финансовым убыткам. Взаимосвязь номенклатуры, экземпляров оборудования и договора отображена на рис. 5.

Таким образом, задачей информационной системы управления паспортизацией и ремонтами оборудования является создание такой структуры хранения данных, которая позволяла бы с помощью различных характеристик отразить существенные составляющие возникших договорных отношений, приведших к появлению оборудования в эксплуатации.
Кроме того, должна быть возможность постоянно регистрировать хранить и обрабатывать данные об изменяющихся характеристиках оборудования хозяйства и о событиях, которые изменяют эти характеристики и определяют так называемый индекс технологического состояния оборудования.
Зарегистрированные в электронном паспорте данные о требуемой квалификации, необходимых трудозатратах ремонтного персонала на производство ремонтов, нормы материальных затрат на каждый вид ремонта позволяют планировать численность и уровень необходимой квалификации ремонтного персонала и при развитие информационной системы могут формировать сметы и спецификации на каждый вид ремонта, а главное, эта функция позволит организовать систему планирования необходимых трудовых и материальных ресурсов для обеспечения бесперебойной работы оборудования.
Накопленные данные о фактах проведения плановых и внеплановых ремонтов, о фактах модернизации, о фактах остановок и аварий дают возможность встраивания в информационную систему инструментов прогнозирования аварий и ремонтов оборудования.
Таким образом, поэтапная подготовка к внедрению, а затем и само внедрение функций электронной паспортизации и автоматического формирования графиков ППР при развитии информационной системы позволит не только управлять ремонтами, но и планировать затраты, формировать финансовые и производственные планы, развивать управленческий учет, повышать производственную надежность, управлять эксплуатационными затратами.
Предлагаемый в настоящей статье подход позволит сократить сроки внедрения программных комплексов управления паспортизацией и ремонтами оборудования на предприятиях, уменьшить количество ошибок в производственном и управленческом учете при эксплуатации этих программных комплексов и, следовательно, сократить финансовые затраты на их исправление.
Список литературы
- Ерохин Е.А., Осинцев А.Н. Эволюция систем технического обслуживания и ремонта оборудования//Организатор производства. 2009. Т. 43. №4. С. 37–41.
- Слаутин Ю.А., Полевщиков И.С. Автоматизированная система построения графиков планово-предупредительных ремонтов (часть 2)//Science Time. 2015. №8 (20). С. 182–186.
- Бородулина С.А., Шимохин А.В. Методы процессуального управления сервисной службой промышленного предприятия//Научный журнал НИУ ИТМО. Серия: Экономика и экологический менеджмент. 2015. №4. С. 216–226;
- Васильев Д.А., Шабельникова А.Ю., Иващенко В.А. Алгоритм принятия решений по ремонту энергооборудования промышленныхпредприятий//ВестникСГТУ. 2014. Т. 3.№1(76).С. 84–89.