Автор: Николаев А.Г., Иванников В.В., Рябов О.Б., Шварц В.М., Степанов В.Н. (ОАО «НОРЭ»).
Опубликовано в журнале Химическая техника №8/2015
ОАО «Норе» было проведено техническое обследование выхлопной трубы с поддерживающей металлической башней на основании обращения владельца.
Причиной послужило заметное раскачивание металлической башни, замеченное персоналом, эксплуатирующим данное сооружение. В тот же день тепловые агрегаты были отключены от трубы и раскачивание башни (при визуальном наблюдении с поверхности земли) прекратилось.
Не было выявлено сверхнормативных отклонений башни и на следующий день при начале обследования объекта специалистами нашей организации, причем скорость ветра и температура наружного воздуха были выше, чем в день наблюдения раскачивания.
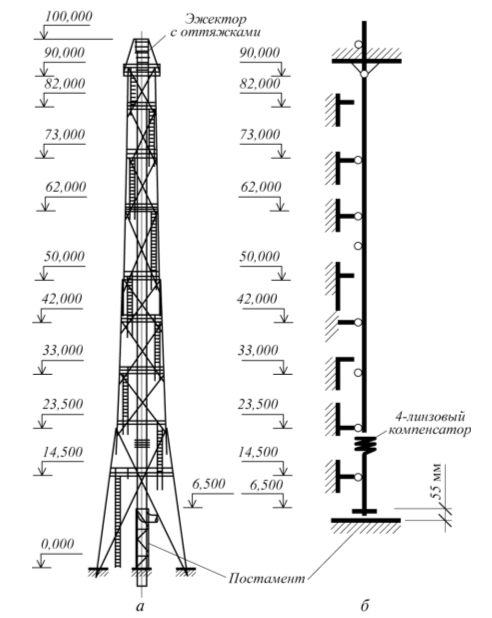
При анализе документации было установлено, что металлическая выхлопная труба с поддерживающей башней предназначена для отвода хвостовых газов, образующихся при производстве слабой азотной кислоты. Объект представляет собой сооружение башенного типа, состоящее из поддерживающей решетчатой башни и расположенного внутри нее газоотводящего ствола в форме цилиндрической оболочки наружным диаметром D = 1 620 мм, опирающегося на специальную металлическую решетчатую опору (постамент).
Основные технические характеристики
Башня – четырехгранная решетчатая усеченная пирамида высотой 90 м с основанием 14,0 м и шириной грани 3,0 м в верхней части. Пояса башни выполнены из прокатных равнополочных уголков крестового сечения, переломы поясов – на отметках +23,00 м и +50,00м. Раскосы – прокатные равнополочные уголки. Башня оснащена 9 горизонтальными диафрагмами жесткости (площадки обслуживания) на отметках: +14,500 м (нижняя); +23,000 м; +33,000 м; +42,000 м; +50,000 м; +62,000 м; +73,000 м; +82,000 м; +90,000 м (верхняя). Материал диафрагм – прокатные швеллеры. С отметки +0,000 м до отметки +90,000м установлены вертикальные лестницы.
Ствол трубы – стальной сварной (по проекту толщина стенки – переменная 3…4 мм, фактически измеренные значения – 3,2…4,5 мм), диаметр ствола – 1 620 мм. Материал ствола по проекту – сталь Х18Н10Т по ГОСТ 5632–61, что соответствует 12Х18Н10Т по ГОСТ 7350–77.
Коническая оболочка (эжектор из нержавеющей стали) в верхней части ствола усилена кольцевыми ребрами жесткости (∟85Ч85Ч5) и жестко закреплена к верхней площадке башни с установкой дополнительных креплений в виде стальных оттяжек. Внизу ствол опирается на отдельную решетчатую опору (постамент), в верхней части жестко закреплен к площадке на отметке +90,000 м.
Горизонтальный металлический надземный газоход выполнен аналогично стволу с креплениями на железобетонных стойках (колоннах).
Температура газов на входе в ствол составляет 130…185°С (max); в состав отводимых газов входят: N2, Н2O, O2, NО, CO, NH3, пары (туман) НNO3.
Металлическая башня для выхлопной трубы выполнена по типовому проекту 4-05-324/8, разработанному в 1964 г. проектным институтом ГОСХИМПРОЕКТ (Москва) и привязанному к объекту в 1967 г. ГИАП. Год постройки и начала эксплуатации – 1968.
Было выявлено несоответствие в части передачи нагрузок от ствола трубы на башню: расчет башни предусматривает подвес ствола в уровне верхней площадки на отметке + 90,00 м для проведения ремонтных работ, а в строительных чертежах и чертежах технологической части, помимо этого, предусмотрено опирание ствола трубы на постамент из металлических прокатных уголковых профилей на отметке + 6,50 м и устройство в стволе трубы 4-линзового компенсатора температурных расширений, что фактически и было выполнено. В результате ствол трубы оказался зажатым между двумя опорами, а температурные линейные расширения не поглощаются установленным линзовым компенсатором, что привело к сверхнормативным отклонениям ствола от вертикального положения – максимальный изгиб ствола на отметке +73,000 составил 441 мм. Очевидно, что данное решение крепления ствола относится к ошибкам при проектировании объекта.
В 2010 г. был произведен ремонт площадок, узлов скольжения, и опоры ствола трубы в зоне постамента были подрезаны. В холодном состоянии трубы расстояние от опоры вертикального ствола трубы до верха постамента составляет 55 мм.
Расчет удлинений металлического ствола
Исходные данные:
- высота трубы – 100 м;
- диаметр ствола трубы – 1 620 мм;
- температура выхлопных газов t = 150…200°С (данные паспорта);
- температура наружного воздуха tв = 26,1°С;
- коэффициент линейного расширения стали α = 0,000012 град–1.
Расчетное удлинение трубы при вводе трубы в работу
Δl = αТL, где T = t + tв = 200 + 26,1 = 226,1°С;
L = 90 – 6,5 = 83,5 м (90 м – отметка верха ствола до эжектора, 6,5 м – отметка верха постамента).
Удлинение ствола трубы при нагреве, таким образом, составит:
Δl = 0,000012×226,1×83,5 = 0,228 м = 227 мм
Компенсирующая способность одной линзы компенсатора при Dствола = 1 620 мм составляет 10 мм (см. табл. 6 ОСТ 26-01-1512–76).
Компенсирующей способности четырех линз (40 мм) и существующего зазора между опорами в нижней части вертикального ствола и верхом постамента (55 мм) в данном случае недостаточно (95 мм < 227 мм), т.е. линейные температурные расширения ствола не компенсируются установленным компенсатором и выполненным зазором, что приводит к изгибу ствола трубы и растяжению конструкций несущей башни стволом трубы. При этом изгибающийся ствол, заклиниваясь в узлах скольжения, повреждает бандажные кольца и настилы площадок.
Причинами образования значительных колебаний выхлопной трубы послужило увеличение тепловой нагрузки в газоотводящем тракте (при включении двух тепловых агрегатов, ранее не задействованных в технологическом процессе) и растяжение конструкций башни с увеличением гибкости и возникновением резонанса колебаний.
В данной ситуации владельцу выхлопной трубы было рекомендовано (помимо устранения других выявленных при обследовании дефектов и повреждений) при подключении более двух технологических агрегатов (проектом предусмотрено четыре агрегата) при температуре наружного воздуха больше 5°С выполнить опирание ствола трубы на постамент с исключением жесткого крепления ствола на отметке +90,000 и демонтажом линзового компенсатора, а также растяжек эжектора на отметке +90,000 м.
В качестве временного решения проблемы, было предложено увеличить существующий зазор с 55 мм до 125 мм, исходя из результатов фактических замеров удлинения ствола при различных вариантах подключения агрегатов и температуры наружного воздуха.
После выполнения наших рекомендаций по увеличению зазора и последующих измерений удлинения ствола при всех работающих тепловых агрегатах и наблюдения за башней возникновения нештатных ситуаций с трубой не выявлено.