Автор: В.Н. Глаголев (ОАО «НИИК»)
Опубликовано на портале «Химическая техника», январь 2021
В настоящее время, наверное, не найдётся ни одного химического (особенно крупнотоннажного) производства, где бы ни применялось теплообменное оборудование.
Одной из основных причин преждевременного выхода из строя кожухотрубчатых теплообменников, как правило, являются повреждения теплообменных труб. И основным элементом, определяющим фактический срок службы теплообменных аппаратов, являются именно теплообменные трубы. Обеспечение целостности теплообменных труб с соблюдением необходимых критериев надежности является основной задачей при управлении ресурсными характеристиками теплообменников.
Теплообменные трубы в процессе эксплуатации подвергаются воздействиям различного рода, которые, в общем виде могут носить механический, коррозионный, эрозионный и тому подобный характер. Активно развивающиеся процессы деградации стенок теплообменных труб через определенный период эксплуатации приводят к образованию пропусков и протечек. Максимальная течь образуется при полном разрыве теплообменной трубы. Для исключения аварийных ситуаций дефекты в теплообменных трубах должны своевременно обнаруживаться и классифицироваться по степени опасности, после чего необходимо принимать соответствующие меры (глушение труб или продолжение эксплуатации при периодическом контроле).
Поиск дефектов в теплообменных трубах – достаточно трудоемкая и дорогостоящая процедура. И тем не менее во многих случаях она вполне оправдана, поскольку пропуск в теплообменных трубах как правило ведет к аварийной остановке производства и значительным убыткам предприятия.
Во всем мире основным методом эксплуатационного контроля металла теплообменных труб является вихретоковый метод. Наибольшее распространение получил вариант с использованием проходного преобразователя (зонда). Методика основана на введении вихретокового зонда в теплообменную трубу со стороны трубной решетки и сканировании трубы по всей длине. С помощью вихретокового дефектоскопа вокруг зонда создаётся переменное электромагнитное поле, которое реагирует на изменения в состоянии металла теплообменной трубы. Эти изменения в свою очередь регистрируются дефектоскопом и затем с помощью специального ПО анализируются на предмет наличия или отсутствия дефектов.
Несомненными достоинствами вихретокового метода с использованием проходного зонда являются возможность контроля трубы по всей длине; определение глубины и объема дефекта, точность в определении локации дефекта; высокая производительность; отсутствие контакта с телом трубы. Сравнение полученных результатов в повторяющейся зоне контроля позволяет оценивать скорость роста дефектов, что в свою очередь позволяет превентивно заглушать трубы с дефектами, через которые еще нет течи, но которые могут дорасти до сквозных. Принципиальными недостатками метода с использованием проходного зонда являются невозможность определения азимутальной ориентации дефекта, невозможность надежного обнаружения дефектов в зоне вальцовки и зоне приварки труб к трубной решетке, неразличимость объемных и линейных дефектов.
У заказчиков, особенно тех, кто заказывает такую услугу впервые, довольно часто возникают определённые сомнения в достоверности вихретокового метода контроля. Гидравлические испытания теплообменников, проводимые, как правило, после окончания остановочных ремонтов, не могут считаться таким механизмом подтверждения целостности теплообменных труб, поскольку позволяют обнаружить лишь сквозные или почти сквозные дефекты. В связи с этим на практике единственным методом, подтверждающим или не подтверждающим дефект, является выемка трубы из аппарата. В современных реалиях при достаточно жестких сроках остановочных ремонтов оборудования предприятия очень неохотно идут на удаление труб из аппаратов с целью обнаружения/подтверждения дефектов и дальнейшего исследования причин их возникновения.
В связи с этим большой практический интерес представляет сравнение результатов состояния теплообменных труб, полученных с помощью вихретокового метода и после их извлечения из аппаратов, при инспекциях теплообменников на различных производствах. Далее представлены некоторые результаты такого сравнения.
При контроле теплообменника-предразлагателя производства карбамида на одной из труб был обнаружен дефект, характеризуемый как наружный, с большой потерей металла и оцениваемый в 70–80% толщины стенки трубы (рис. 1).
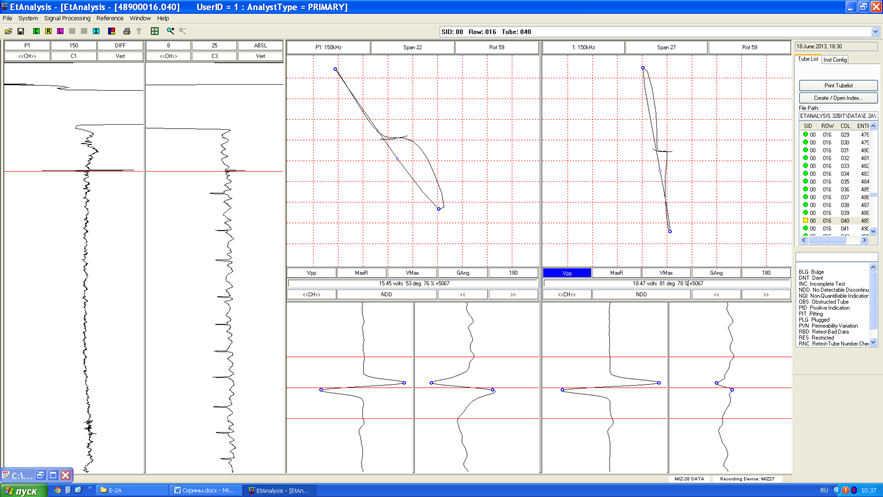
После выемки трубы на наружной поверхности в предполагаемом месте был обнаружен дефект, глубина которого составила 64% толщины стенки (рис. 2). Дефект на трубе имел механический характер и произошел, вероятно, при изготовлении теплообменника.
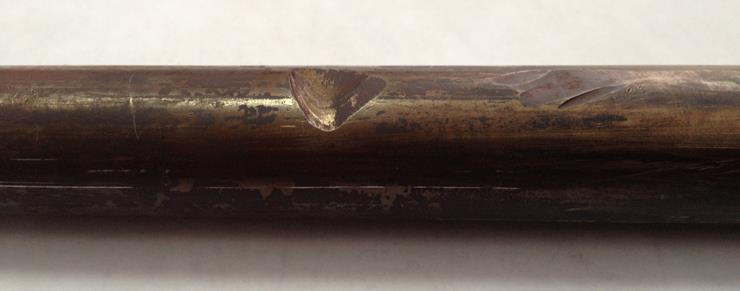
При вихретоковом контроле холодильника I ступени сжатия СО2 агрегата карбамида было обнаружено большое число труб с дефектами. Все дефекты характеризовались как локальные, наружные, очень глубокие (практически сквозные). Дефектная зона характеризовалась наличием сразу нескольких, расположенных рядом дефектов (рис. 3).
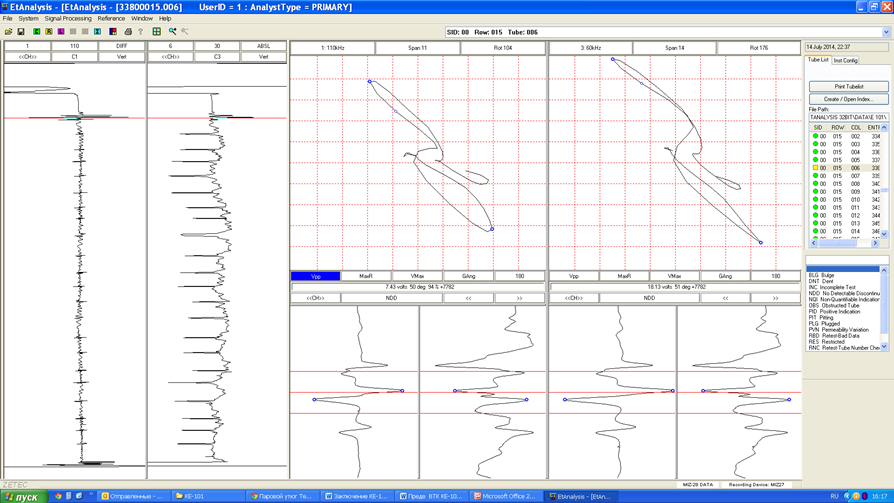
Большинство таких труб было рекомендовано заглушить. Для подтверждения полученных результатов заказчиком была удалена одна из рекомендуемых к удалению труб (труба №1506). После извлечения из аппарата труба повторно прошла вихретоковый контроль, который подтвердил наличие обнаруженных ранее дефектов. Затем труба была разрезана вдоль для визуального осмотра внутренней и наружной поверхности. На срезе трубы в районе предполагаемого дефекта были обнаружены две трещины с глубиной распространения практически на всю толщину стенки трубы (рис. 4, 5).
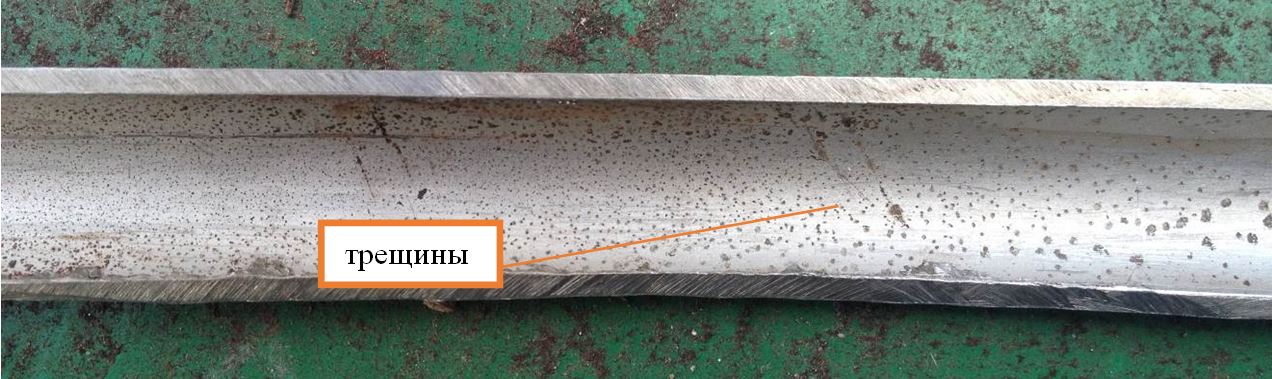
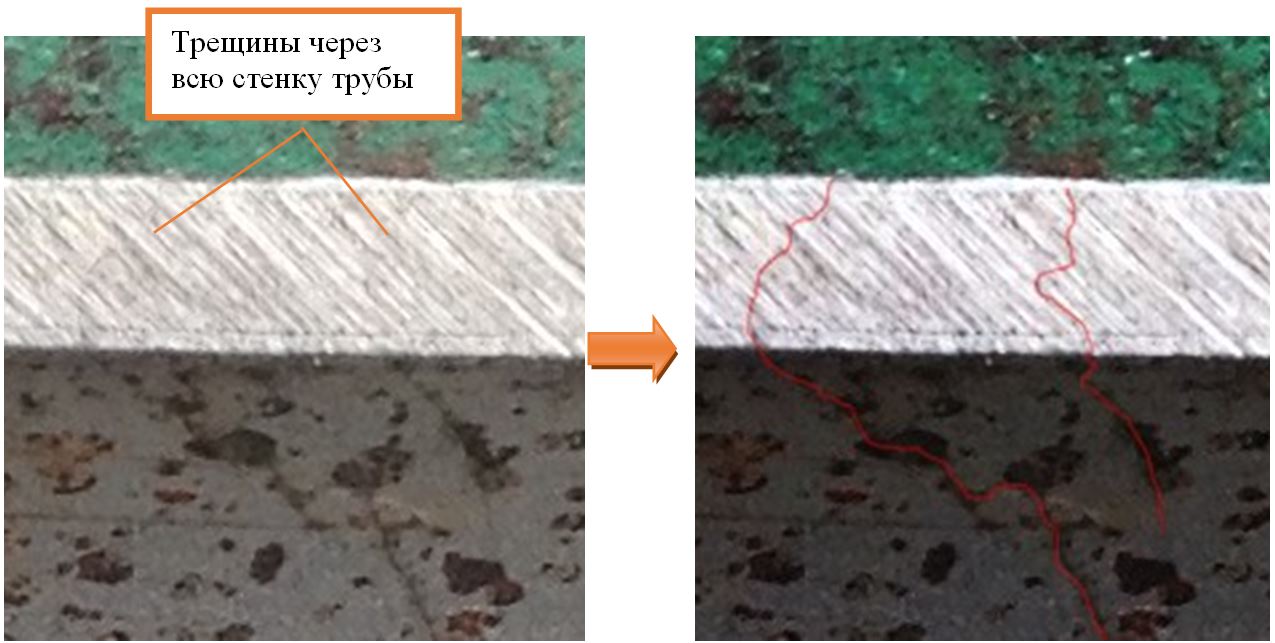
Именно эти дефекты дефектоскоп зарегистрировал и определил как практически сквозные (94–95%).
При вихретоковом контроле теплообменника агрегата серной кислоты на ряде труб были обнаружены дефекты под поддерживающими перегородками (рис. 6). Предположительно это были перетирания труб об эти перегородки. Заказчик не принял решение о выемке трубы, но и через люк в кожухе аппарата хорошо видны перетертости труб в поддерживающих структурах (рис. 7).
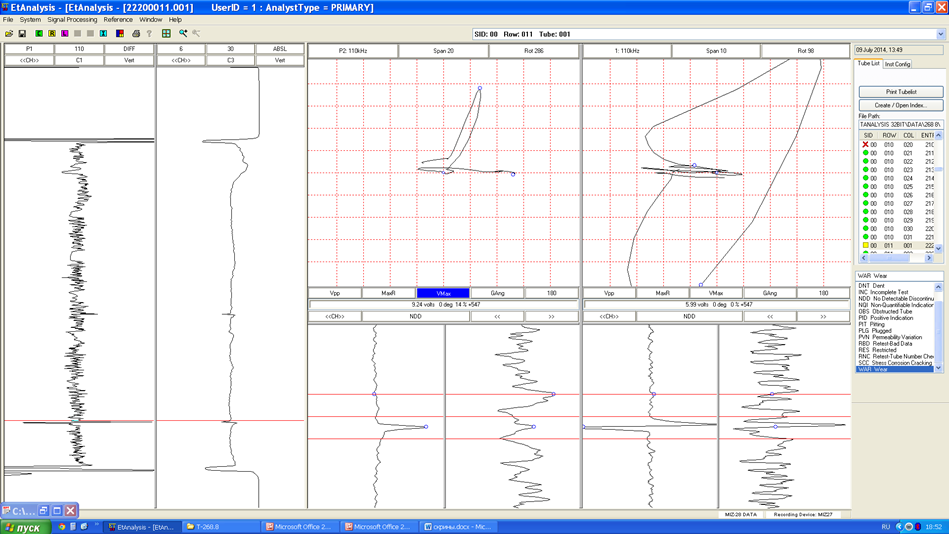
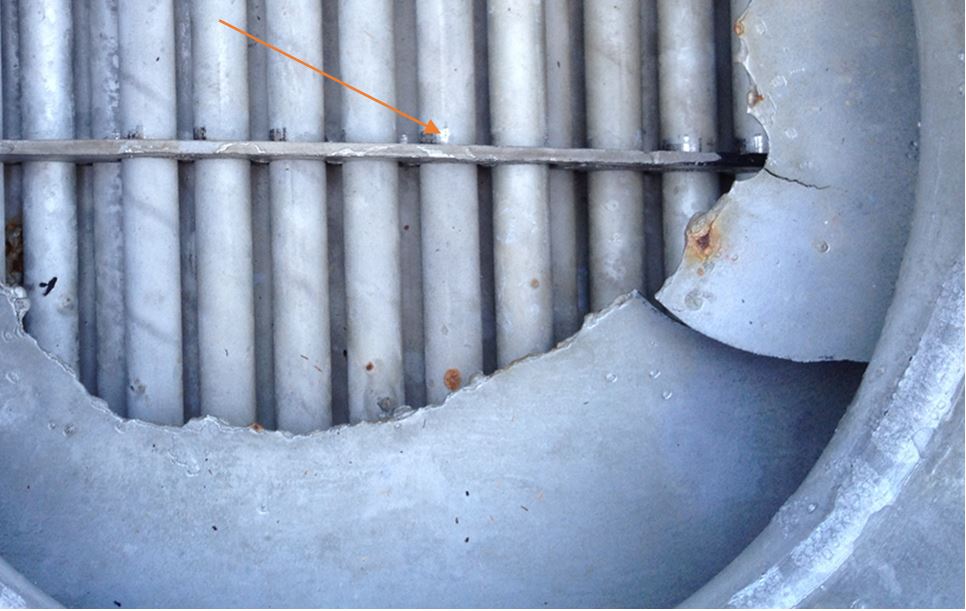
Таким образом, вихретоковый контроль подтвердил наличие дефектов на трубах в виде перетираний о поддерживающие перегородки.
В конденсаторе низкого давления производства карбамида, основными дефектами теплообменных труб также являются перетирания в межтрубных перегородках. Вихретоковый контроль позволяет достаточно точно определить место и глубину повреждения таких дефектов (рис. 8).
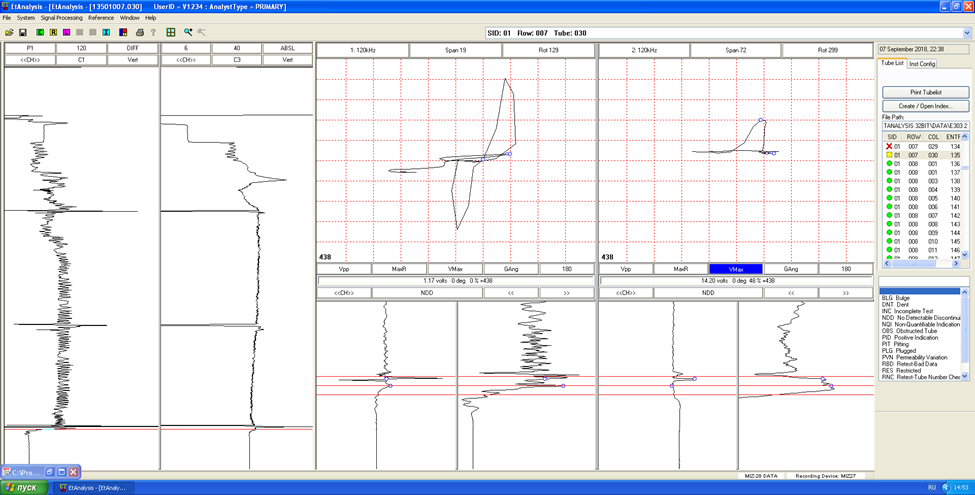
При этом достаточно точно можно определить, образовался ли дефект в настоящее время или он произошел в предыдущие периоды эксплуатации, до перемещения перегородок (рис. 9).
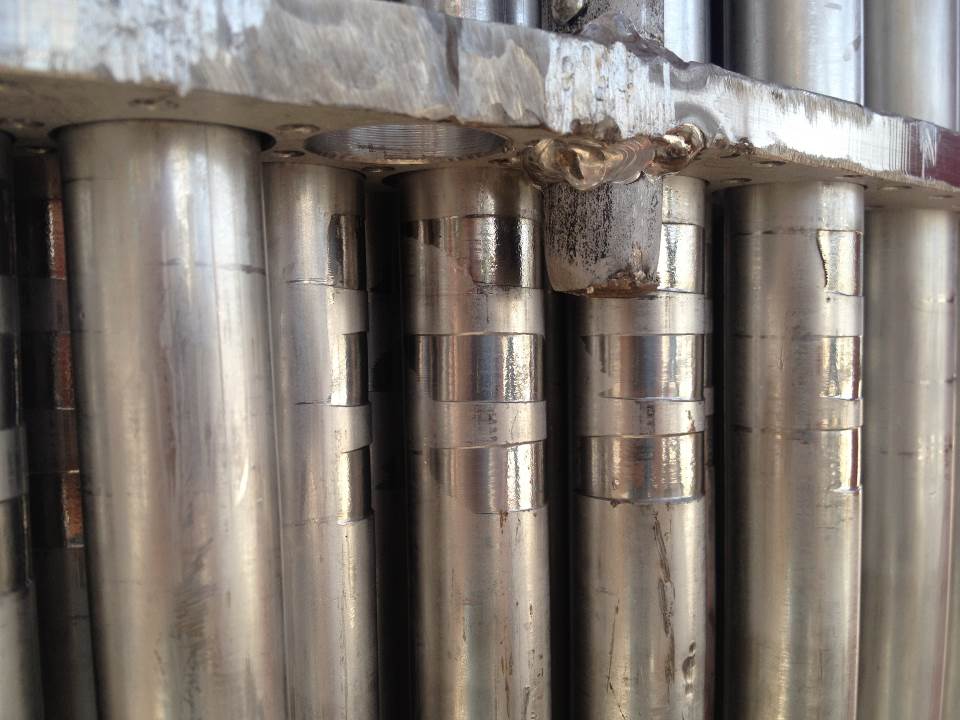
При проведении предэксплуатационного контроля теплообменников нагрева нефти на одном из нефтяных месторождений у значительного числа теплообменных труб на внутренней поверхности были обнаружены многочисленный дефекты, характеризуемые глубиной проникновения 30–90% и малым объемом потери металла, предположительно образование язв и питтингов (рис. 10).
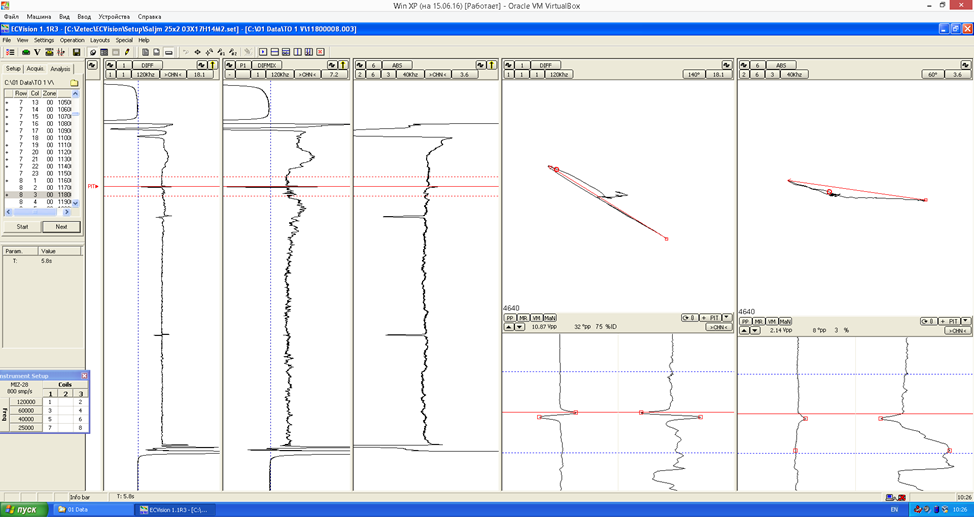
После извлечения ряда дефектных труб из аппарата и разрезания их вдоль на внутренней поверхности труб действительно были обнаружены многочисленные язвы и питтинги различной глубины (рис. 11).
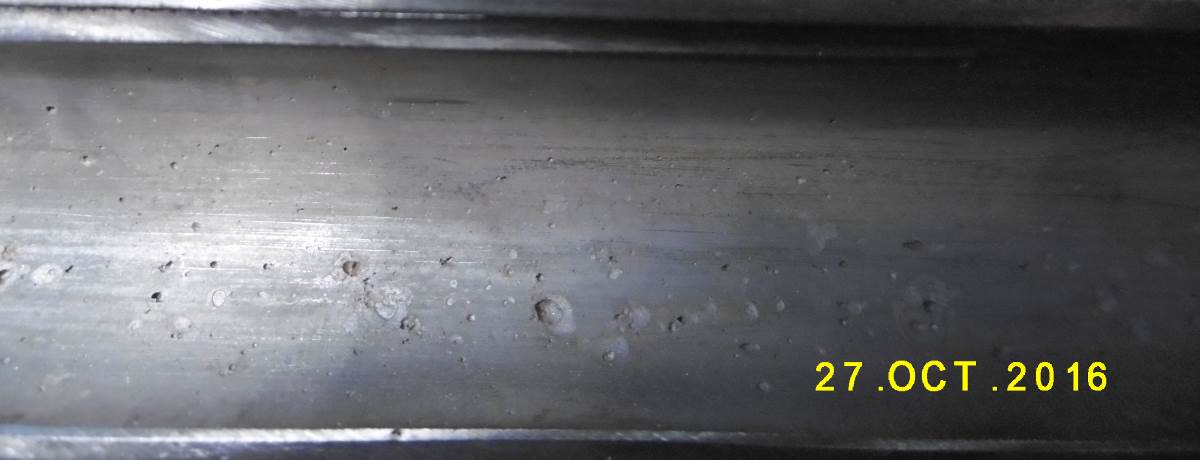
Анализ шлифов наиболее глубоких дефектов (рис. 12) позволил утверждать, что все обнаруженные дефекты имеют коррозионную природу, что для новых аппаратов, не бывших в эксплуатации, несколько странно.
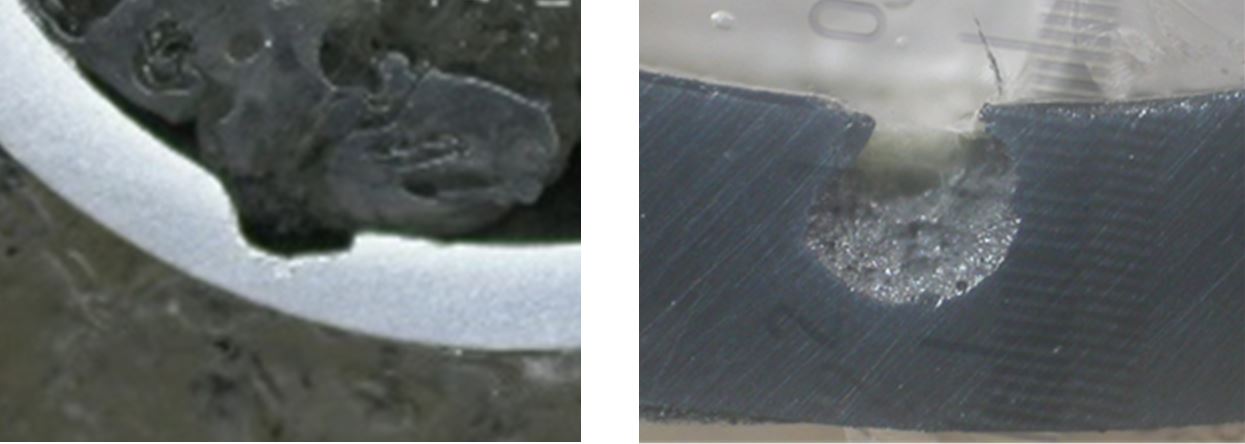
Таким образом, на основании представленных результатов можно сделать следующие выводы.
Применение вихретокового метода контроля при диагностике как эксплуатируемых, так и вновь вводимых теплообменников позволяет с высокой достоверностью обнаруживать практически все типы дефектов на теплообменных трубах. Это позволяет оперативно оценивать действительное состояние металла теплообменных труб и исключать как аварийный выход аппаратов из строя, так и преждевременный их ремонт. Предэксплуатационный контроль позволяет обеспечить качество изготовления аппарата и подтвердить его соответствие нормативной документации.
В заключение выражаю особую благодарность всем сотрудникам ОАО «НИИК», принимавшим участие в инспекциях теплообменников в полевых условиях.