Авторы: М.С. Трещёва, В.А. Платонов, С.В. Панченко, Ю.Н. Тюрин, В.Н. Середа (ОАО «НОРЭ»).
Опубликовано в журнале Химическая техника №9/2015
На заводе по производству строительных материалов произошло аварийное разрушение дымососа, обслуживающего вращающуюся обжиговую печь. Производительность дымососа 1 000 000 м3/ч, рабочая температура 380°С, мощность двигателя 2 800 кВт. Рабочее колесо дымососа – двухстороннего входа, лопатки приварены по обеим сторонам коренного диска и к покрывным дискам.
При аварии произошел отрыв лопатки рабочего колеса, который спровоцировал разрушение покрывного диска, отрыв прочих лопаток с этой стороны колеса, повреждение корпуса дымососа и разлет обломков по прилегающей территории. Было повреждено здание электроподстанции, пробиты в нескольких местах газоходы, поврежден маслопровод, что привело к возгоранию масла и пожару.
Отрыв лопаток произошел вдоль сварных швов, при этом линии разлома проходили как по зоне сплавления сварных швов и наплавленному металлу, так и по основному металлу (рис. 1, 2).
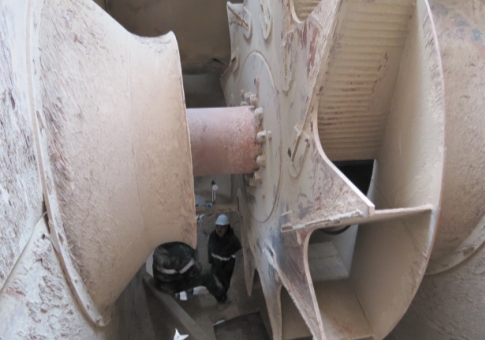
Были проведены исследования химического состава, микроструктуры и прочности материала лопаток и разрушенного покрывного диска. Сталь, из которой были изготовлены элементы рабочего колеса, – Q 295A (09Mn2) по стандарту GB/T 1591–94 (Китай) [1]; область применения этой стали соответствует условиям эксплуатации рабочего колеса. Дефектов микроструктуры стали обнаружено не было. Прочностные свойства основного металла элементов рабочего колеса соответствуют требованиям стандарта. Очевидно, что причина выхода колеса из строя связана с особенностями изготовления и/или эксплуатации.

а, б – по линии сплавления, наплавленному металлу и основному металлу лопатки; в – по основному металлу лопатки
При рассмотрении технической документации установлено, что инструкция по обслуживанию дымососа и технические требования к эксплуатации не переведены на русский язык (имеется частично английский, частично китайский текст); в представленной документации отсутствуют технические условия на изготовление рабочего колеса дымососа, в том числе на исполнение сварных швов рабочего колеса. Нет сведений о сварочных материалах, способе сварки и типе сварных швов.
Запросить документы у изготовителя дымососа не удалось, поскольку рабочее колесо было изготовлено сторонней фирмой, и контрактом не была предусмотрена поставка рабочей документации вместе с изготовленным колесом. По этой причине говорить сколько-нибудь определенно о соответствии исполнения колеса требованиям проекта и каким-либо нормам проектирования и изготовления невозможно.
При осмотре оторванных лопаток установлено, что сварные швы таврового сварного соединения приварки лопаток к коренному и покрывному дискам на большей части длины были выполнены с непроваром (рис. 3).
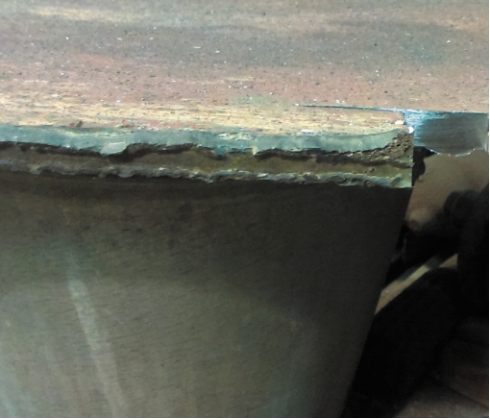
Разрыв произошел по наплавленному металлу
Сварные швы неоднородные, площади сечения сварных швов на разных участках одного и того же шва существенно различаются.
По нашему мнению, несущие сварные соединения конструкций, работающих в условиях динамических нагрузок, целесообразно выполнять с полным проплавлением. Такое исполнение необходимо для максимального исключения концентраторов напряжения в нагруженных узлах. Наличие непровара в несколько раз снижает циклическую прочность сварного изделия.
Кроме того, для уменьшения концентрации напряжений следует выполнять плавный переход сварного шва на основной металл, исключить подрезы, обеспечивать достаточное усиление сварных соединений. Оптимальные размеры сечения валика наплавленного металла и катета сварного шва рекомендованы действующими стандартами (ГОСТ 5264, ГОСТ 8713, ГОСТ14771 и др.)
Для определения типа сварного шва и оценки качества выполнения сварных швов, а также возможного наличия ремонтных подварок, были вырезаны темплеты с участка сварного шва приварки торца лопатки к коренному (рис. 4, а) и к покрывному дискам (рис. 4, б).
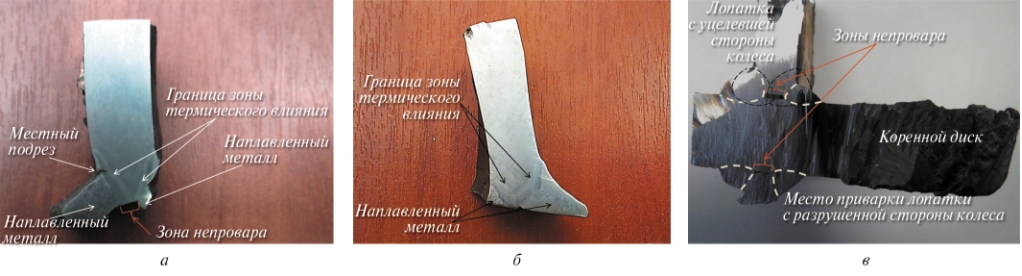
а – к коренному диску колеса; б – к покрывному диску (на участке вырезки темплета шов выполнен с полным проплавлением); в – разрез сварного узла приварки торца лопаток к коренному диску (на участке вырезки темплета швы выполнены с непроваром; сечение однотипных сварных швов существенно отличается по форме и площади). Белой штриховой линией показаны контуры сечений швов; черной штриховой линией показаны контуры сечения рекомендуемого сварного соединения тип Т8 по ГОСТ 5632
Темплет, изображенный на рис. 4, б, вырезан с участка, где шов выполнен с полным проплавлением. Протяженность участка шва с полным проплавлением составила не более 5% общей длины шва рассматриваемой лопатки. Темплет, изображенный на рис. 4, а, содержит непровар, характерный для большей части длины сварных швов приварки лопаток. В обоих случаях сварка однопроходная, признаков переплавки металла шва, характерных для ремонтной сварки, не обнаружено.
Кроме того, проводилась вырезка темплета, включавшего сварные швы приварки к коренному диску оторванной и уцелевшей лопаток (рис. 4, в). Как видно, сварные швы обеих лопаток в месте вырезки выполнены с непроваром. По краям непроваров имеются трещины, не выходящие на поверхность наплавленного металла (рис. 5).
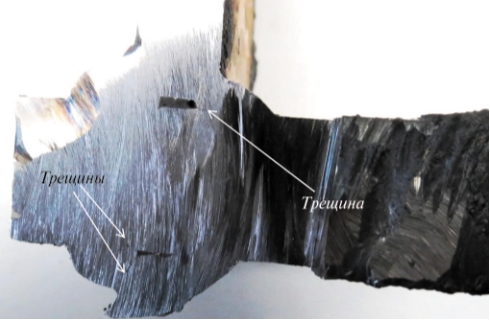
При опросе персонала было установлено, что блокировка, предусматривающая остановку дымососа при повышении вибрации до критического уровня, была отключена. В системе АСУТП и контроля производства не предусмотрена запись тренда виброскорости, фиксируется только переход от нормального режима работы к режиму повышенной вибрации (виброскорость 6 мм/с) и к режиму критического уровня вибрации (виброскорость 8 мм/с).
Было обнаружено расхождение требований эксплуатационного регламента установки и технических требований изготовителя. По регламенту критическим при работе дымососа считается уровень виброскорости 8 мм/с, а в технических требованиях указано, что при номинальной нагрузке виброскорость не должна превышать 4,6 мм/с. Превышение виброскорости выше установленного значения (до 11 мм/с) допускается в режиме охлаждения при закрытых заслонках.
По результату расследования причин аварии был сделан вывод, что с технической точки зрения причиной образования трещин явилось неблагоприятное сочетание низкого качества сварки и наличия непровара в несущих сварных швах с работой при повышенной вибрации.
С организационной точки зрения условия для аварии были созданы рядом отступлений от необходимых требований к изготовлению, приемке поставки и эксплуатации оборудования. В силу этого владельцам оборудования были даны следующие рекомендации:
- при приобретении импортного оборудования запрашивать у изготовителя технические условия на изготовление ответственных узлов и деталей на русском языке [2];
- проводить входной контроль ответственного оборудования;
- соблюдать соответствие требований регламента эксплуатации оборудования с техническим требованиями изготовителя к режимам эксплуатации;
- использовать систему блокировки, предусматривающую отключение дымососа при превышению вибрации.
Список литературы
- GB/T 1591-94. Low content alloy high strength structural steel.
- Постановление Правительства РФ от 15 августа 1997 г. N1037. О мерах по обеспечению наличия на ввозимых на территорию Российской Федерации непродовольственных товарах информации на русском языке.