Автор: Т.Д. Алеференко, М.А. Квантов (ООО «НПО ЛЕНКОР-НЕФТЕХИМ»).
Опубликовано в журнале Химическая техника №5/2015
ООО «НПО ЛЕНКОР-НЕФТЕХИМ» проводит научно-исследовательские работы в области металловедения и водородной коррозии оборудования гидрогенизационных процессов.
В свое время под руководством Ю.И. Арчакова во ВНИИНефтехиме была создана исследовательская установка высокого давления водорода, на которой прошли испытания почти все материалы, применяемые в настоящее время в оборудовании нефтеперерабатывающих заводов (НПЗ).
Полученные результаты вошли в соответствующие нормативные документы и послужили основой для выбора материального оформления гидрогенизационных процессов в нефтепереработке и нефтехимии. Следует отметить, что российские нормативы более жесткие, чем принятые в Европе и США.
В настоящее время на многих заводах такое оборудование проработало 300 000 ч и более. Для теплонапряженного оборудования на таких сроках эксплуатации при проведении экспертизы промышленной безопасности особого внимания заслуживают вопросы водородной коррозии и длительной прочности металла. Оба механизма ослабления металла не могут быть исследованы методами неразрушающего контроля и требуют проведения исследований на образцах металла, вырезанных из действующего оборудования.
Кинетика водородной коррозии характеризуется двумя параметрами: индукционным периодом, в течение которого она никак себя не проявляет, и скоростью водородной коррозии после окончания индукционного периода [1]. И если данные по водородостойкости сталей, т.е. индукционному периоду, для целого ряда марок сталей известны и требуют лишь уточнения на пробеге 300 000 ч, то данные по скорости водородной коррозии (после окончания индукционного периода) для большинства марок сталей или отсутствуют, или недостаточны. Само по себе обнаружение наличия результатов водородной коррозии на внутренней поверхности аппарата (обезуглероженного слоя) – неприятный сигнал, но для оценки остаточного ресурса и прогнозирования ситуации нужно знать еще и скорость развития этого процесса.
Известно, что при эксплуатации оборудования в области ползучести металл подвержен термическому старению. При поверочном расчете на прочность в таком случае необходимо использовать имеющиеся в нормативной литературе значения длительной прочности, отвечающие реальному времени наработки оборудования для конкретной марки стали.
В последнее время наблюдаются случаи (в первую очередь с оборудованием импортного производства), когда прочностные расчеты с использованием приводимых в нормативной документации значений длительной прочности на базе 300 000 ч дают неудовлетворительные результаты, и оборудование формально нужно выводить из эксплуатации.
Приведем примеры:
- реакторы риформинга DR – 311… 314, изготовленные фирмой Construction Metalliques de Provence (Франция) в 1979 г., входящие в состав комплекса по производству ароматических углеводородов. Температура эксплуатации – 525°С, сталь A387 Gr11 Cl1 (отечественный аналог – сталь 12 ХМ). При использовании нормативных значений длительной прочности стали 12ХМ на базе 300 000 ч расчетная толщина стенки обечайки этих реакторов уже заметно превышает фактическую. В то же время известно, что нормативные значения длительной прочности представляют собой достаточно консервативную оценку, реальные прочностные свойства металла конкретного аппарата могут оказаться заметно выше;
- оборудование того же комплекса: один из трубопроводов (коллектор) изготовлен из аустенитной стали А376 Тр316Н (отечественный аналог – сталь 08Х17Н13М2Т) и имеет расчетную температуру по паспорту 721°С, в то время как по нашим нормативным документам эта сталь рекомендована к применению при температуре не выше 600°С. Сейчас время наработки этого оборудования составляет почти 300 000 ч, и для оценки его остаточного ресурса необходимо экспериментальное определение параметров длительной прочности этого металла.
Для решения вопросов подобного рода актуальным становится проведение лабораторных исследований длительной прочности и водородной коррозии на вырезанных из действующего оборудования образцах металла. Технология вырезки темплетов и последующей заделки образовавшегося отверстия известна и приведена в нормативной документации [2]. В настоящее время есть определенный опыт применения этой технологии, усовершенствованы некоторые ее аспекты.
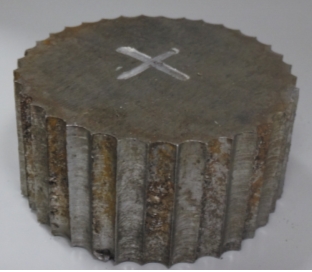
Пример темплета диаметром 100 мм, вырезанного из стенки аппарата, приведен на рис. 1. Темплет вырезается высверливанием электродрелью через кондуктор. На рис. 2 показано место вырезки образца из стенки аппарата, подготовленное под заварку заглушки (отверстию придали цилиндрическую форму шлифовкой), которая изготавливается из того же металла, что и материал аппарата (рис. 3). На рис. 4 показан вид отремонтированного места изнутри и снаружи аппарата.
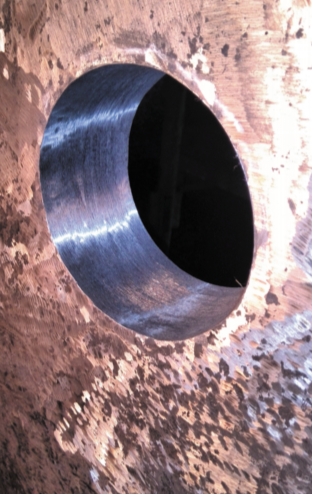
Конструкция заглушки и узла заделки в целом обеспечивает достаточный запас прочности.
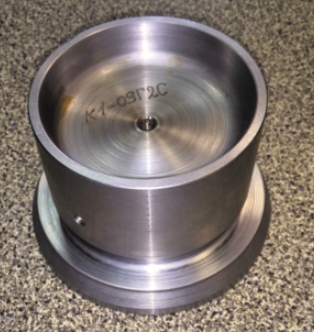
Положительный опыт длительной эксплуатации оборудования с такими заглушками есть в ОАО Уфанефтехим (с 2007 г.) и на Омском НПЗ (с 2008 г.).
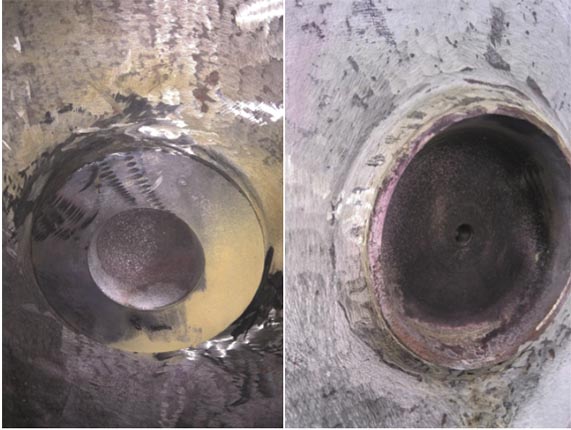
а – вид изнутри аппарата; б – вид снаружи аппарата
Из темплета диаметром 100 мм изготавливаются образцы для механических испытаний на длительную прочность и для металлографических исследований (водородная коррозия). Методики проведения ускоренных испытаний на длительную прочность при нескольких температурах позволяют ограничиться небольшим количеством образцов (12) и сократить время испытаний до 3…4 мес.
В зависимости от толщины стенки аппарата может потребоваться 1…2 темплета. Исследование структуры металла такого темплета позволяет оценить глубину ослабленного водородной коррозией слоя металла.
Анализ результатов исследования обоих механизмов ослабления металла (тепловая деградация и водородная коррозия) позволяет оценить вклад каждого и корректно рассчитать остаточный ресурс металла оборудования для обоснованного планирования его замены.
Еще одним практическим примером полезности использования разрушающих методов исследования является определение длительной прочности хромомолибденовых сталей печных змеевиков. С ростом времени эксплуатации на уровне 250 000…300 000 ч фактическая толщина стенки змеевиков заметно уменьшается, а отбраковочная толщина, наоборот, увеличивается из-за уменьшения параметров длительной прочности. «Лишние» 0,1…0,2 мм отбраковочной толщины в этом случае часто означают отбраковку «лишних» десятков труб.
Экспериментальное определение параметров длительной прочности металла с учетом водородной коррозии позволяет оптимизировать эту ситуацию.
Таким образом, на основании изложенного можно сделать следующие выводы:
- при оценке остаточного ресурса теплонапряженного оборудования при больших сроках эксплуатации необходимо учитывать тепловую деградацию металла и воздействие водорода. Получить информацию о реальных параметрах длительной прочности и кинетике водородной коррозии можно только в лабораторных условиях на образцах, вырезанных из действующего оборудования;
- технологии вырезки темплета и ремонтной заделки образовавшегося отверстия известны и многократно опробованы практически.
Список литературы
- Арчаков Ю.И. Водородоустойчивость стали. М.:Металлургия, 1978.
- Технические указания – регламент по эксплуатации и обследованию оборудования установок каталитического риформинга и гидроочистки, работающих в водородсодержащих средах при повышенных температуре и давлении. СПб, 1998.