Автор: E.В. Захарченко, Ф.С. Советин, Т.Н. Гартман, В.Д. Сафонова, О.П. Шумакова (РХТУ им. Д. И. Менделеева).
Опубликовано в журнале Химическая техника №5/2015
Нитрование является одним из важнейших процессов в химической промышленности России. Динитрохлорбензолы применяются главным образом в производстве азокрасителей, а также фунгицидов (например, 2,4-динитророданбензол) и взрывчатых веществ (тетрил, гексил, гексанитродифенил, пикриновая кислота и др.) [1–4].
Непрерывные технологические схемы получения динитрохлорбензола являются крупнотоннажными, а также энергои ресурсоемкими, поэтому даже незначительное снижение потребления энергии и ресурсов может обеспечить существенный экономический эффект [1–3, 5].
Большинство действующих крупнотоннажных производств динитрохлорбензолов в России используют традиционные технологии нитрования, в которых в качестве нитрующих смесей применяются смеси азотной и серной кислот с водой [1–3, 6–8].
Модернизация с позиции энергои ресурсосбережения указанных производств невозможна без применения современных комплексов программ, позволяющих разрабатывать компьютерные модели химико-технологических систем, создавать так называемые «виртуальные» производства. Кроме того, использование данных комплексов программ делает возможным без значительных материальных и временных затрат производить исследования указанных процессов на их компьютерных моделях [9–10].
Работа [11] посвящена применению комплекса программ CHEMCAD для разработки компьютерной модели технологического узла нитрования крупнотоннажного производства нитробензола. Задачи разработки компьютерной модели технологического узла каталитического восстановления нитробензола водородом рассмотрена в работе [12]. Моделированию технологической схемы хлорирования бензола по Беркману с использованием пакета программ CHEMCAD посвящена работа [13].
Однако необходимо дополнительно рассмотреть вопрос разработки компьютерной модели технологического узла нитрования крупнотоннажного производства динитрохлорбензолов с применением комплекса программ CHEMCAD.
В данной работе решена задача применения комплекса программ CHEMCAD для разработки компьютерной модели технологической схемы получения динитрохлорбензолов нитрованием хлорбензола.
Описание технологической схемы процесса получения динитрохлорбензолов нитрованием хлорбензола
Для получения динитрохлорбензолов хлорбензол двустадийно нитруют нитрующей смесью, представляющей собой смесь азотной кислоты, серной кислоты и воды. Описание технологической схемы нитрования хлорбензола заимствовано из работ [1–2]. Технологическая схема непрерывного узла нитрования хлорбензола, реализованная в среде комплекса программ CHEMCAD (блок-схема блочной компьютерной модели технологической схемы), приведена на рисунке.
В нитратор (модуль 3) непрерывно подают хлорбензол, отработанную кислоту со второй стадии нитрования и нитрующую смесь, представляющую собой смесь азотной кислоты, серной кислоты и воды. При температуре 55°С нитрование хлорбензола проводится до мононитрохлорбензолов в соответствии с уравнением 2C6H5Cl +2HNO3 → → о-C6H4ClNO2 + n-C6H4ClNO2 + 2H2O (1)
Так как реакция нитрования является экзотермической, нитратор охлаждают водой, подаваемой в рубашку и змеевик.
Затем нитромасса передается в сепаратор (модуль 6), где мононитрохлорбензолы отделяются от отработанной кислоты и направляются на вторую стадию нитрования.
Отработанная кислота из сепаратора направляется в экстрактор (модуль 15), где происходит экстракция из нее нитрохлорбензолов (экстрагент – хлорбензол, направляемый на нитрование).
В нитратор второй стадии (модуль 9) подают концентрированную серную кислоту и азотную кислоту, а затем нитромасса передается в нитратор (модуль 10). Нитрование второй стадии начинается при температуре 65°С и заканчивается при температуре 105°С в соответствии с уравнениями о-C6H4ClNO2 +2HNO3 → несимм (NO2)2C6H3Cl + + симм (NO2)2C6H3Cl +2H2O (2) п-C6H4ClNO2 + HNO3 → несимм (NO2)2C6H3Cl + H2O (3)
Данные нитраторы также охлаждаются водой.
Далее нитромасса со смесью динитрохлорбензолов направляется в сепаратор (модуль 11), где динитрохлорбензолы отделяются от отработанной кислоты. Отработанная серная кислота из сепаратора (модуль 11) перетекает в сборник (модуль 14), оттуда насосом (модуль 13) подается на первую стадию нитрования. Динитрохлорбензолы последовательно промываются раствором соды и водой, отделяются в сепараторах (модули 17 и 19) от водных слоев. «Сырые» динитрохлорбензолы (динитрохлорбензолы с небольшим количеством воды) направляются на сушку.
Моделирование основных аппаратов и технологической схемы процесса непрерывного нитрования хлорбензола до динитрохлорбензолов
Основной поток нитратора (поток в резервуаре аппарата, в котором протекает реакция нитрования хлорбензола) моделируется модулем стехиометрического реактора (см. рисунок, модуль 3). При моделировании данного процесса нитрования принято допущение, что в нитраторе протекает только основная реакция в соответствии с уравнением (1). Для модуля реактора 3 указаны следующие условия: стехиометрические данные основной реакции (1), конверсия базового реагента – хлорбензола, равная 1, изотермический тепловой режим (температура 55°С). Расчетная тепловая нагрузка – 83 348 МДж/ч.
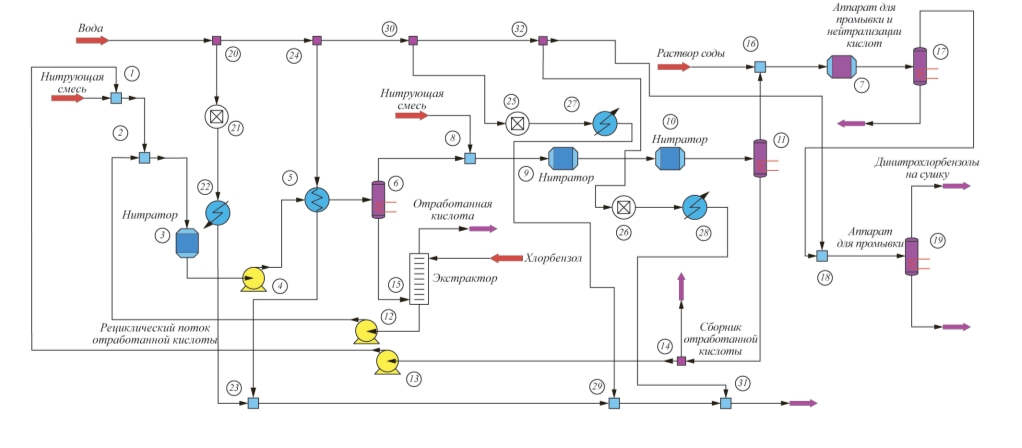
Модули расчета: 3, 9, 10 – модули стехиометрических реакторов; 5, 22, 27, 28 – модули теплообменников; 21, 25, 26 – модули
статических контроллеров; 6, 11, 17, 19 – модули сепараторов; 15 – модуль экстрактора; 4, 12, 13 – модули насосов; 7 – модуль
равновесного реактора; 1, 2, 8, 16, 18, 23, 29, 31 – модули смесителей; 14, 20, 24, 30, 32 – модули делителей потоков
Поток охлаждающей воды моделируется модулем теплообменника (модуль 22) при заданной тепловой нагрузке. Процесс теплопередачи (в данном случае отвода теплоты экзотермической реакции нитрования хлорбензола в рубашку и змеевик реактора) моделируется модулем статического контроллера 21. Данный модуль передает расчетную тепловую нагрузку модуля реактора модулю теплообменника. Применена процедура комбинирования стандартных расчетных модулей комплекса программ CHEMCAD для моделирования сложных химических реакторов, разработанная в работах [14, 15].
Результаты расчета нитратора первой ступени нитрования (процесс нитрования хлорбензола до мононитрохлорбензолов)*
Давление, МПа 0,2/0,1
Температура, °С 20/55
Массовый расход, т/ч 184,2/184,2
Массовая доля компонента, %:
хлорбензол 41,81/0
мононитрохлорбензолы 0,59/59,17
азотная кислота 23,72/0,21
серная кислота 27,15/27,15
вода 6,73/13,47
*В числителе приведены данные на входе, в знаменателе – на выходе.
Сепаратор для отделения нитромассы после первой ступени нитрования от отработанной кислоты (модуль 6) моделируется модулем сепаратора компонентов, при этом заданы температура (20°С) и доли компонентов в потоке смеси мононитропроизводных хлорбензоа, так называемом потоке органической фазы (серная кислота – 0,01, азотная кислота – 0,01, мононитрохлорбензолы – 0,99, вода – 0,01).
Результаты расчета сепаратора для отделения смеси мононитрохлорбензолов от отработанной кислоты
На входе | На выходе* | |
Давление, МПа | 0,3 | 0,3/0,3 |
Температура, °С | 55 | 20/20 |
Массовый расход, т/ч | 184,2 | 108,04/76,16 |
Массовая доля компонента, %: | ||
хлорбензол | 0 | 0/0 |
мононитрохлорбензолы | 59,17 | 99,87/1,43 |
азотная кислота | 0,21 | 0,01/0,5 |
серная кислота | 27,15 | 0,01/65,68 |
вода | 13,47 | 0,01/32,39 |
*В числителе – поток мононитрохлорбензолов; в знаменателе – поток «отработанной» кислоты в экстрактор. |
Экстрактор, в котором происходит экстракция нитрохлорбензолов из отработанной кислоты (модуль 15), моделируется модулем расчета экстрактора EXTR с использованием алгоритма Тиле–Геддеса [16]. Число тарелок – 10.
Давление в экстракторе – 0,3 МПа. Поток отработанной кислоты подается на последнюю тарелку. Поток «свежего» хлорбензола, являющегося экстрагентом, – на первую тарелку.
Результаты расчета экстрактора
На входе* | На выходе** | |
Давление, МПа | 0,3/0,2 | 0,15/0,15 |
Температура, °С | 20/20 | 20/20 |
Массовый расход, т/ч | 76,16/80 | 78,57/77,59 |
Массовая доля компонента, %: | ||
хлорбензол | 0/100 | 98,1/3,75 |
мононитрохлорбензолы | 1,43/0 | 1,38/0 |
азотная кислота | 0,5/0 | 0,49/0 |
серная кислота | 65,68/0 | 0,02/64,44 |
вода | 32,39/0 | 0,01/31,81 |
*В числителе – отработанная кислота на очистку; в знаменателе – «свежий» хлорбензол.
**В числителе – поток хлорбензола в нитратор 3; в знаменателе – поток очищенной отработанной кислоты.
Нитраторы второй стадии нитрования (основные потоки аппаратов), в которых мононитрохлорбензолы нитруются до динитрохлорбензолов (модули 9 и 10), моделируются модулями стехиометрических реакторов. При моделировании данного процесса нитрования также принято допущение, что в нитраторах протекают только основные реакции в соответствии с уравнениями (2) и (3). Для модулей реакторов 9 и 10 указаны следующие условия: стехиометрические данные реакций (2) и (3), конверсии базовых реагентов – мононитрохлорбензолов, равные 1; изотермический тепловой режим (температура 55°С и 105°С). Расчетная тепловая нагрузка модуля 9 равна 27 506 МДж/ч, модуля 10 – 51 689 МДж/ч. Потоки охлаждения данных нитраторов моделируются модулями теплообменникой (модули 27 и 28) при заданных тепловых нагрузках. Процесс теплопередачи (в данном случае отвода теплоты экзотермических реакций нитрования монохлорбензолов в рубашки и змеевики реакторов) моделируется модулями статических контроллеров 25 и 26.
Данные модули передают расчетные тепловые нагрузки модулей реакторов модулям теплообменников.
Результаты расчета процесса нитрования мононитрохлорбензолов до динитрохлорбензолов*
Давление, МПа 0,2/0,2
Температура, °С 50/105
Массовый расход, т/ч 192,04/192,04
Массовая доля компонента, %:
хлорбензол 0/0
мононитрохлорбензолы 56,18/0
динитрохлорбензолы 0/72,3
азотная кислота 22/0,44
серная кислота 20,82/20,82
вода 1/6,44
*В числителе приведены данные на входе, в знаменателе – на выходе.
Сепаратор для отделения динитрохлорбензолов от отработанной кислоты (модуль 11) моделируется модулем сепаратора компонентов, при этом заданы температура (20°С) и доли компонентов в потоке смеси органической фазы (серная кислота – 0,01, азотная кислота – 0,01, динитрохлорбензолы – 0,99, вода – 0,01).
Сравнение результатов расчетов данного сепаратора с экспериментальными данными работ [1, 2]
На входе | На выходе | ||
Смесь Динитро-хлорбензолов | Отработанная кислота | ||
Расчет | Расчет | Расчет/ | |
Давление, МПа |
0,2 |
0,2 |
Эксперимент
0,2/– |
Температура, °С | 105 | 20 | 20/20 |
Массовый расход, т/ч | 192,04 | 138,72 | 53,32/– |
Массовая доля компонента, %: | |||
хлорбензол | 0 | 0 | 0/0 |
мононитрохлорбензолы | 0 | 0 | 0/0 |
динитрохлорбензолы | 72,3 | 99 | 0,26/1 |
азотная кислота | 0,44 | 0,26 | 1,59/1,5 |
серная кислота | 20,82 | 0,27 | 75,01/71 |
вода | 6,44 | 0,47 | 23,14/26,5 |
Аппарат для промывки смеси динитрохлорбензолов раствором соды моделируется комбинацией модулей – модуля равновесного реактора и модуля сепаратора компонентов (модули 7 и 17). Для модуля реактора 7 указаны следующие условия: стехиометрические данные реакций «гашения» соды (реакций взаимодействия карбоната натрия с кислотами), конверсии базовых реагентов – кислот, равные 1; изотермический тепловой режим (температура 20°С). Для модуля сепаратора 17 заданы следующие условия: температура (20°С), доли компонентов в потоке смеси органической фазы (динитрохлорбензолы – 0,99, вода – 0,5, карбонат натрия – 0,01, нитрат натрия – 0,01, сульфат натрия – 0,01).
Аппарат для промывки смеси динитрохлорбензолов водой моделируется модулем сепаратора компонентов (модуль 19). Для модуля сепаратора 19 заданы следующие условия: температура (20°С), доли компонентов в потоке смеси органической фазы (динитрохлорбензолы – 0,99, вода – 0,01).
При расчете технологической схемы непрерывного нитрования хлорбензола до динитрохлорбензолов для обеспечения сходимости рецикла использовался метод простых итераций.
Таким образом, разработана компьютерная модель крупнотоннажной технологической схемы нитрования хлорбензола, пригодная для решения задач энергои ресурсосбережения промышленных производств динитрохлорбензолов. Посредством разработанной модели возможно выявление неоптимальных режимов работы как отдельных аппаратов, так и технологической линии в целом.
Список литературы
- Орехов В.С., Дьячкова Т.П., Субочева М.Ю., Колмакова М.А. Технология органических полупродуктов. Ч. 1. Тамбов: ТГТУ, 2007.
- Лисицын В.Н. Химия и технология промежуточных продуктов. М: Химия. 1987.
- Орлова Е Ю. Химия и технология бризантных взрывчатых веществ. Л.: Химия, 1973.
- Васин А.Я., Маринина Л.К., Гаджиев Г.Г., Голубева В.А. Изучение влияния галогенов на взрывоопасность органических соединений//Вектор науки Тольяттинского государственного университета. 2013. №3 (25).
- Щеглова А.А. Реконструкция технологического узла нитрования крупнотоннажного производства нитробензола//Успехи в химии и химической технологии. 2012. Т. 26. №11 (140).
- Данов С.М., Колесников В.А., Есипович А.Л. Кинетика нитрования бензола азотной кислотой//Журнал прикладной химии. 2010. Т. 83. №1.
- Юдин Н.В., Вьет Д.Т., Якубов Д.Б., Збарский В.Л. Изучение связи нитрующей активности и кислотности серно-азотных кислотных смесей в широком интервале составов//Успехи в химии и химической технологии. 2008. Т. 22. №4 (84).
- Юдин Н.В., Вьет Д.Т., Якубов Д.Б., Збарский В.Л. О некоторых особенностях нитрования в серно-азотных кислотных смесях с низким содержанием серной кислоты//Успехи в химии и химической технологии. 2007. Т. 21. №4 (73).
- Гартман Т.Н., Клушин Д.В. Основы компьютерного моделирования химико-технологических процессов. М: Академкнига, 2008.
- Гартман Т.Н., Советин Ф.С. Аналитический обзор современных пакетов моделирующих программ для компьютерного моделирования химико-технологических систем//Успехи в химии и химической технологии. 2012. Т. 26. №11 (140).
- Советин Ф.С. Гартман Т.Н. Применение комплекса программ CHEMCAD для разработки компьютерной модели технологического узла нитрования крупнотоннажного производства нитробензола//Химическая техника. 2012. №4.
- Мешкова А.А., Советин Ф.С., Гартман Т.Н., Проскуров Е.А., Сафонова В.Д. Разработка компьютерной модели технологического узла получения анилина из нитробензола с применением комплекса программ CHEMCAD//Химическая техника. 2014. №7.
- Советин Ф.С., Гартман Т.Н., Сафонова В.Д., Шумакова О.П., Тамбовцев И.И. Применение комплекса программ CHEMCAD для разработки компьютерной модели технологической схемы хлорирования бензола по Беркману//Химическая техника. 2014. №10.
- Советин Ф.С., Гартман Т.Н. Логико-вычислительные процедуры разработки блочных компьютерных моделей реакторных и ректификационных процессов//Известия ТулГУ. Технические науки. 2011. Вып. 5. Ч. 3.
- Советин Ф.С. Разработка и применение методического обеспечения блочного компьютерного моделирования энергоресурсоемких химико-технологических систем c применением инструментальных комплексов программ. Дис. … канд. техн. наук. М.: РХТУ им. Д.И. Менделеева. 2011.
- Гартман Т.Н. Анализ и синтез непрерывной ректификации на основе автоматизированного накопления и классификации информации. Дис…. д-ра техн. наук. М.: 2000.