Автор: А.Е. Сушко (НТЦ «Завод Балансировочных машин»).
Опубликовано в журнале Химическая техника №3/2016
В настоящее время на промышленных предприятиях в силу целого ряда объективных причин самое пристальное внимание уделяется вопросам повышения надежности и эффективности эксплуатации и ремонта роторного оборудования. Особенно остро эти вопросы стоят на опасных промышленных производствах нефтехимии.
Подобный интерес объясняется рядом объективных причин. Изменяются подходы к эксплуатации оборудования, изменяется само оборудование, усложняются технологические процессы, ужесточаются требования промышленной и экологической безопасности. Большое количество агрегатов, скрытый характер зарождения и развития неисправностей, накопленная за долгие годы усталость оборудования нередко являются причинами аварийных ситуаций, которые могут сопровождаться значительным экономическим ущербом и загрязнением окружающей среды. Ряд аварий и техногенных катастроф различного масштаба последних лет заставляют по-новому переосмысливать требования к достоверности оценки текущего состояния оборудования и определению его остаточного ресурса с учетом последних достижений науки в области технической диагностики [1].
С другой стороны, большинство технических руководителей в условиях экономии средств и сокращения бюджета сталкивается с суровой необходимостью уменьшения затрат, в том числе на модернизацию, техническое обслуживание и ремонт основного и вспомогательного оборудования. Зачастую существенно усложняет ситуацию и общая изношенность агрегатов, часть которых в значительной степени уже исчерпала остаточный ресурс.
В данных условиях особенно важно, чтобы решения о минимизации затрат принимались без ущерба надежности эксплуатации оборудования. Это становится возможным только при наличии достоверной информации о текущем техническом состоянии, полученной с использованием различных методов технической диагностики [2].
Однако для решения всего спектра задач, связанных с повышением надежности работы оборудования и сокращением затрат на его обслуживание и ремонт, одной диагностической информации недостаточно [3, 4].
Необходима реализация целого комплекса мероприятий, объединенных в рамках общей стратегии эффективной эксплуатации, обслуживания и ремонта оборудования SAFE PLANT. К таким мероприятиям относятся: достоверная оценка технического состояния всего парка технологического оборудования, своевременное выявление неисправностей и прогноз остаточного ресурса с использованием всего арсенала методов и средств технического диагностирования в рамках распределенного мониторинга, контроль агрегатов на всех этапах жизненного цикла (входной контроль в процессе монтажа, приемо-сдаточные испытания, эксплуатация, предремонтный контроль, ремонт, послеремонтный контроль), а также внедрение подходов «оптимального» технического обслуживания. Рассмотрим более подробно основные аспекты практического внедрения стратегии SAFE PLANT на производстве.
Контроль и диагностика всего парка технологического оборудования
Любое опасное производство – это огромное количество единиц самого разнообразного оборудования, обеспечивающего непрерывность технологического процесса. Основные и вспомогательные агрегаты существенно различаются по сложности конструктивного исполнения, режимам работы, реализуемым функциям, наличию или отсутствию дублирования и т.д. Очевидно, что не может существовать единого аппаратного решения, позволяющего с максимальной эффективностью выполнять достоверный анализ и предотвращать аварийные выходы из строя всего парка оборудования. В связи с этим для комплексного оснащения предприятия средствами технической диагностики необходим достаточно широкий спектр технических решений. Какое именно из этих решений будет использоваться в каждом конкретном случае, зависит, как правило, от специфики решаемых задач [5].
Эксперты НТЦ «Завод балансировочных машин» на основе обобщенного опыта практических работ предложили классификацию роторного оборудования, в максимальной степени ориентированную на выбор оптимального технического решения. При проведении этой классификации учитывались такие параметры, как критичность оборудования (его стоимость, затраты на обслуживание, затраты на ремонт, стоимость простоя и аварийного ремонта и т.д.) и время развития дефекта (периодичность обновления данных, достаточная для принятия решения по дальнейшему обслуживанию и своевременному безаварийному выводу в ремонт). В результате анализа все вращающееся оборудование было разделено по приоритетности контроля на три основные группы: оборудование, дефекты которого развиваются достаточно медленно (годы – недели), а его критичность минимальна, промежуточная группа – более критичное оборудование с более быстро развивающимися (недели – часы) дефектами и группа особо ответственного оборудования, дефекты которого могут развиться за часы и даже минуты.
Подходы к контролю состояния и диагностике оборудования различных групп должны существенно различаться. Для первой группы наиболее оправдан периодический контроль вибрации с использованием переносных сборщиков данных. Для безаварийной эксплуатации оборудования второй группы необходим постоянный контроль вибрации при помощи стационарных систем, однако допускается последовательный сбор данных с определенной периодичностью. Особо ответственное оборудование третьей группы необходимо контролировать непрерывно, причем помимо мониторинга (отслеживания параметров во времени) необходимо осуществлять и защиту (оперативная сигнализация или отключение в случае превышения заданных уставок). На рис. 1 приведена обобщенная диаграмма, наглядно иллюстрирующая процедуру выбора оптимального технического решения для контроля состояния оборудования различных групп.
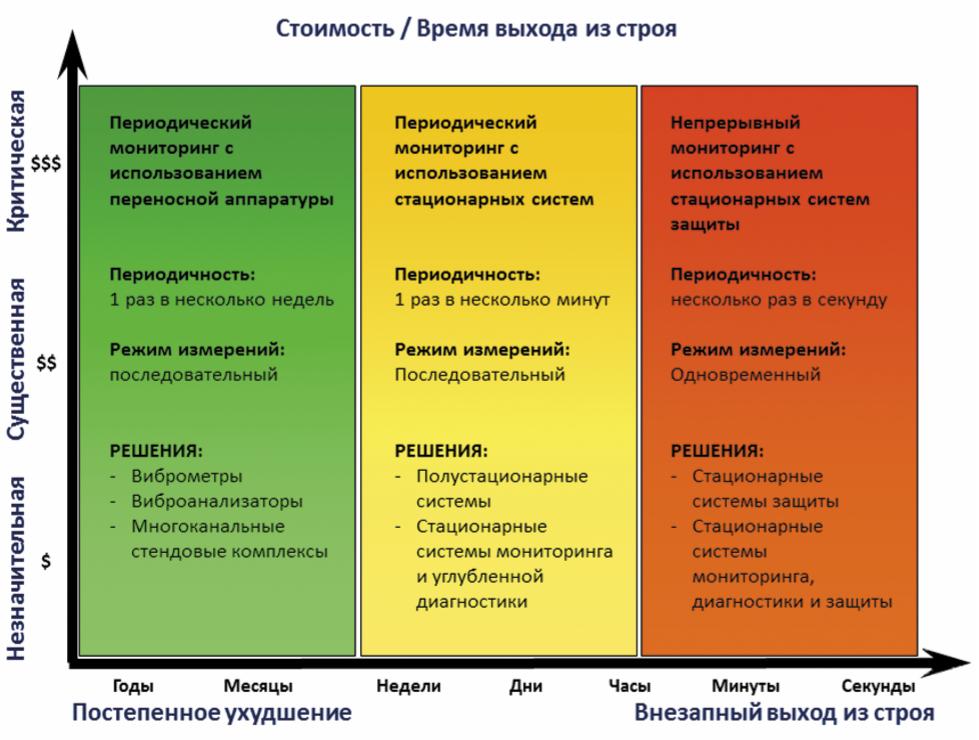
Используемые технические решения могут также отличаться в зависимости от степени критичности оборудования согласно принятой классификации. Например, для контроля состояния ответственного оборудования, дефекты которого развиваются достаточно медленно, оправдано использование многоканальных переносных либо стендовых исследовательских комплексов, более простое оборудование может контролироваться при помощи виброанализаторов, а вспомогательное оборудование – при помощи простейших виброметров [6]. На рис. 2 представлены примеры измерительных средств для контроля оборудования различных групп.
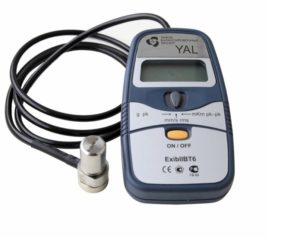
а – виброметр YAL; б – виброанализатор CORVET; в – многоканальный блок UMS-16
Распределенный мониторинг
Для надежной эксплуатации оборудования и сокращения затрат на его обслуживание и ремонт по результатам технического диагностирования необходимо обеспечивать периодичность мониторинга достаточную для своевременного выявления возникающих неисправностей и предотвращения возможных аварийных ситуаций.
На практике, для большинства видов роторного оборудования, нуждающегося в постоянном или периодическом контроле (от 80 до 90 % общего количества оборудования), в зависимости от его конструктивных особенностей и условий эксплуатации интервалы между измерениями устанавливаются в диапазоне от 1/10 до 1/50 межремонтного интервала. В пересчете на абсолютные значения периодичность контроля составляет от 1 до 4 виброобследований в течение одного месяца. Организация мониторинга технического состояния всего парка технологического оборудования с указанной периодичностью требует существенных трудозатрат. По различным оценкам, численность диагностов на предприятии в этом случае должна составлять не менее 20–30 человек.
Содержание и материальное оснащение службы подобной численности требует существенных затрат, которые в ряде случаев могут полностью нивелировать суммарный экономический эффект от мероприятий технического диагностирования. Необходимо понимать, что основными целями внедрения технической диагностики на предприятии является повышение эффективности управления производством и существенный рост прибыли за счет повышения надежности эксплуатации оборудования, снижения затрат на его техническое обслуживание и ремонт, исключения аварийных и сокращения плановых простоев и т.д. Очевидно, что все эти результаты не могут быть достигнуты без оптимизации затрат на развитие и содержание самой службы технической диагностики [6].
Наиболее эффективным путем такой оптимизации без снижения достоверности диагностирования является организация комплекса мероприятий в рамках подходов распределенного мониторинга. Одним из важнейших мероприятий данного комплекса является внедрение стационарных систем мониторинга и углубленной диагностики для оценки состояния оборудования, нуждающегося в постоянном контроле. Подобные системы существенно расширяют возможности традиционного периодического мониторинга с использованием переносной аппаратуры и позволяют производить в автоматическом режиме многоканальный сбор, обработку и анализ различных замеров вибрации и других режимных параметров с периодичностью от нескольких секунд до нескольких минут.
Другим мероприятием, направленным на оптимизацию деятельности службы диагностики, является частичная передача функций по оценке технического состояния службам цехов. Обходчики или эксплуатационный персонал цехов, оснащенные простейшими тестерами, с заданной периодичностью измеряют уровни вибрации и температуры и информируют диагностов в случае изменения данных параметров. В этом случае диагносты производят только выборочный анализ состояния проблемного оборудования и выдают рекомендации по срокам и объемам ремонтных работ. Реализация подобного подхода позволяет максимально эффективно использовать имеющиеся на предприятии людские ресурсы и обеспечивает безотказную работу всего парка оборудования [4].
Одним из ключевых инструментов технической диагностики является периодический мониторинг. Кропотливый анализ и сравнение больших массивов разнородных данных не могут быть выполнены вручную, поэтому для хранения, отображения, оценки результатов измерений, построения отчетов и пр. необходимо использовать специализированное программное обеспечение. Для упрощения процедуры диагностирования в составе такого обеспечения должны использоваться экспертные системы диагностики, которые в автоматическом режиме обрабатывают огромное количество информации и существенно ускоряют работу диагностов. Описанный выше комплекс мероприятий в рамках внедрения распределенного мониторинга позволяет оптимизировать деятельность службы технической диагностики и существенно сократить затраты на ее содержание и материальное оснащение [3, 6].
Контроль оборудования на всех этапах жизненного цикла
Еще одной важнейшей составляющей внедрения стратегии SAFE PLANT является контроль оборудования на всех этапах его жизненного цикла (рис. 3). Новое оборудование нуждается в высококвалифицированном монтаже, а роль диагностики на этом этапе заключается в организации тщательного входного контроля вводимого в эксплуатацию оборудования и проверке его параметров на соответствие существующим нормам. На стадии эксплуатации оборудования аппаратные и программные средства технической диагностики призваны осуществлять контроль его текущих характеристик и своевременно информировать о возникающих неисправностях.
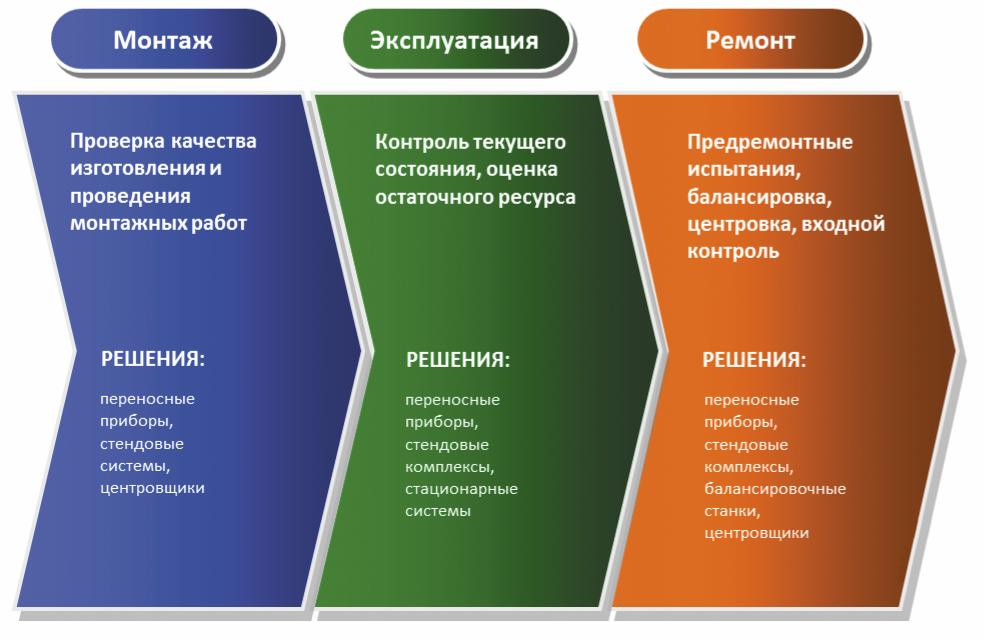
Залогом надежной и продолжительной эксплуатации оборудования является качественный ремонт, который невозможен без контроля всех основных параметров перед выводом в ремонт и после ремонта. Любой ремонт, включающий демонтаж отдельных узлов агрегата, не может быть завершен без балансировки и центровки. Другой немаловажный фактор успешного ремонта – организация стендовых испытаний. В настоящее время наибольшее распространение получили стенды входного контроля подшипников качения, которые способны произвести отбраковку некачественного изделия до его монтажа, а, следовательно, дать существенную экономию средств за счет исключения незапланированных простоев по вине некачественных подшипников. В условиях широкого распространения контрафактных изделий подобная экономия может внести существенный вклад в общее увеличение прибыльности производства. Помимо контроля подшипников, должны организовываться стендовые испытания в рамках послеремонтного контроля отдельных механизмов в сборе – электродвигателей, насосов, редукторов [8]. Только неукоснительное соблюдение изложенных выше положений способно действительно повысить эффективность производства и надежность оборудования и привести к появлению положительного экономического эффекта от оправданного сокращения затрат на техническое обслуживание и ремонт. На рис. 4 представлены современные решения для оценки состояния и наладки оборудования.
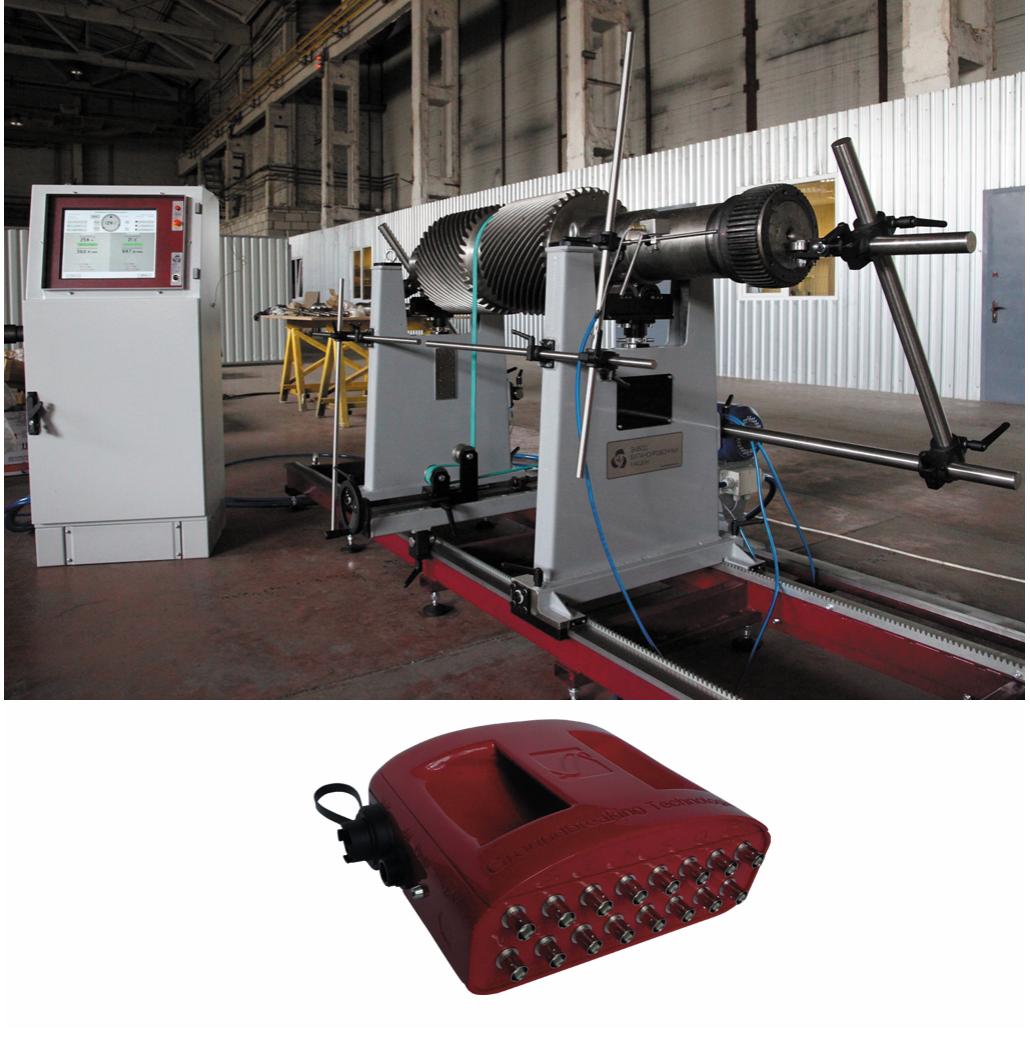
и наладки оборудования на всех этапах жизненного цикла: а – балансировочный станок серии БМ;
б – стендовый комплекс UMS
Описанный комплекс мероприятий, включающий контроль оборудования на всех этапах жизненного цикла, оценку состояния всего парка технологических агрегатов, рекомендации по выбору оптимальных измерительных средств и организацию распределенного мониторинга, на практике обеспечивают высокую надежность эксплуатации и существенное сокращение затрат на техническое обслуживание и ремонт. Реализация данного комплекса мероприятий является необходимым условием для перехода на систему «оптимального» технического обслуживания и достижения экономического эффекта в рамках внедрения стратегии SAFE PLANT [7, 9].
Однако для решения всего спектра задач, связанных с повышением эффективности управления производст-вом, применения перечисленных диагностических средств недостаточно. Итоговый успех внедрения стратегии SAFE PLANT определяется возможностью оперативного доступа различных структурных подразделений предприятия к актуализированным массивам диагностических и ремонтных данных, содержащих всю необходимую информацию для принятия компетентных решений. Для этого требуется организация единого многоуровневого информационного пространства, позволяющего всем участникам технологического, производственного и ремонтного процессов осуществлять быстрый и эффективный обмен данными. Существующие на предприятиях программные решения по управлению основными фондами EAM/ERP, CMMS и пр. позволяют получать доступ к финансовым, производственным и технологическим показателям, складским данным, сведениям о ремонтах, однако, они не содержат важнейшей диагностической информации о текущем состоянии оборудования и его остаточном ресурсе, необходимой для грамотного планирования.
Организация эффективной производственной деятельности невозможна без полноценного обмена данными между диагностическими измерительными приборами и программными системами управления. Для формирования единого диагностического пространства (обработки, накопления, хранения и отображения результатов измерений) и передачи сведений о текущем состоянии оборудования в глобальные информационные системы должно использоваться специализированное программное обеспечение. Требования к функциональным возможностям такого обеспечения крайне высоки.
Программа должна иметь сетевую распределенную архитектуру, поддерживать многопользовательский режим с различными правами доступа, обеспечивать унифицированный обмен данными со всеми диагностическими измерительными средствами, надежное хранение результатов измерений, удобный инструментарий многоуровневого просмотра и анализа данных, а также осуществлять взаимодействие с АСУ и внешними информационными средами.
Примером компании, выпускающей полный спектр программно-аппаратных средств для оценки технического состояния роторного оборудования на всех этапах его жизненного цикла и предлагающей наиболее разнообразный арсенал индивидуальных технических решений для агрегатов различных групп, является НТЦ «Завод Балансировочных машин». Помимо широчайшей линейки современных высокоточных балансировочных станков нового поколения серии БМ, систем лазерной центровки (FREGAT), переносных (BRIG, CORVET), стендовых (UMS-16) и стационарных систем (CMS, MPS и др.) мониторинга, диагностики и защиты, завод предлагает первый отечественный программный продукт, удовлетворяющий всем необходимым требованиям для успешной реализации стратегии SAFE PLANT.
Одноименный программный продукт SAFE PLANT представляет собой единую интеллектуальную платформу для сбора, хранения, отображения и анализа различной диагностической информации с целью повышения надежности эксплуатации и эффективности обслуживания и ремонта всего парка технологического оборудования на основании сведений о его фактическом и прогнозируемом техническом состоянии (рис. 5).
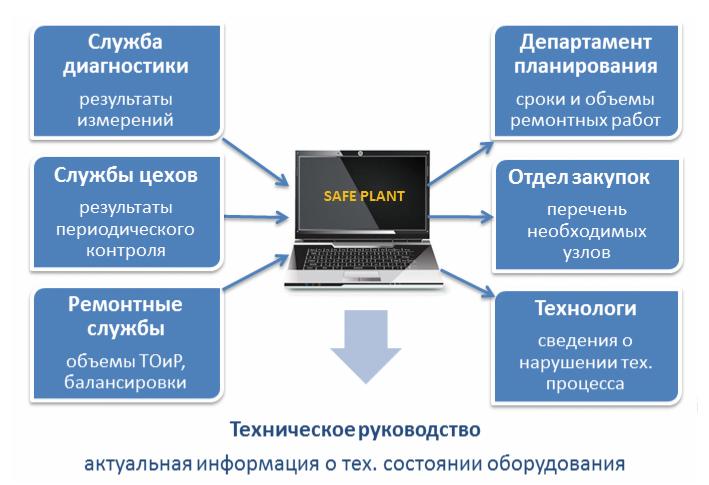
SAFE PLANT – первый масштабируемый программный продукт, позволяющий объединять сведения о состоянии оборудования, режимах его эксплуатации, производимых обслуживаниях и ремонтах в единую диагностическую базу данных, выполнять их анализ и осуществлять передачу необходимой информации для планирования сроков и объемов ремонтных работ (рис. 6). В качестве входных данных могут быть использованы результаты различных видов измерений, получаемых как при помощи собственных аппаратных решений, так и измерительных средств сторонних производителей (рис. 7). Сводные данные о текущем состоянии оборудования и рекомендуемых ремонтах могут быть переданы по запросу во внешние информационные среды. Для автоматизации диагностических процедур в программе реализован экспертный модуль смешанного типа, адаптированный к основным видам роторного оборудования опасных промышленных производств. Практическое внедрение данного программного продукта позволяет предприятиям нефтехимии не только организовать обработку, сбор и централизованное хранение сведений о результатах диагностики и ремонтов, наладить более эффективное взаимодействие различных служб, но и обеспечить эффективный переход к стратегии SAFE PLANT.
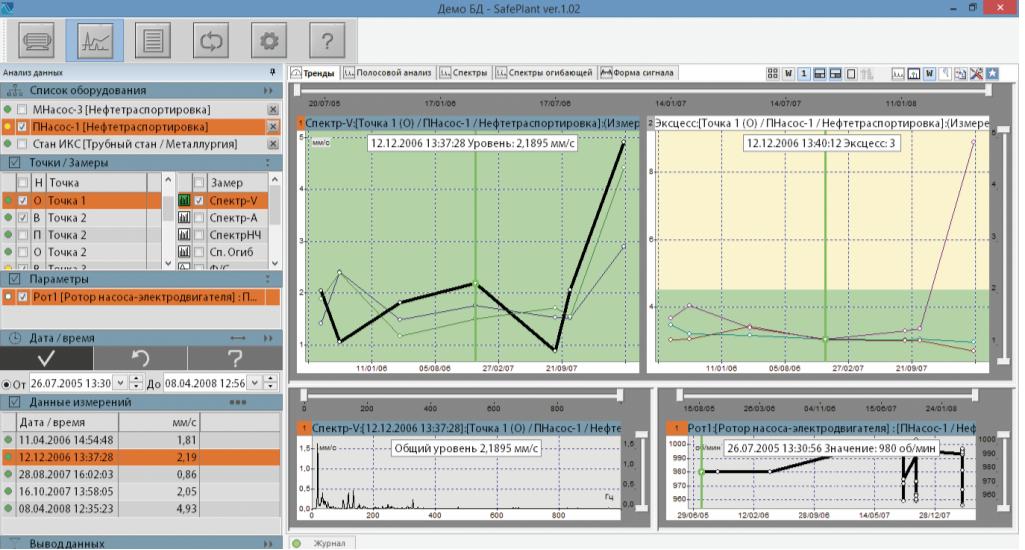
Подводя итоги рассмотрения основных аспектов повышения надежности работы оборудования опасных промышленных производств и сокращения затрат на техническое обслуживание и ремонт путем внедрения всего комплекса мероприятий стратегии SAFE PLANT, необходимо подчеркнуть ряд тезисов, имеющих важное практическое значение. Достоверная оценка состояния всего парка технологического оборудования на основе результатов технического диагностирования с использованием существующего арсенала измерительных средств, внедрение распределенного мониторинга, контроль оборудования на всех этапах жизненного цикла, переход на стратегию «оптимального» обслуживания – являются важнейшими составляющими стратегии SAFE PLANT.
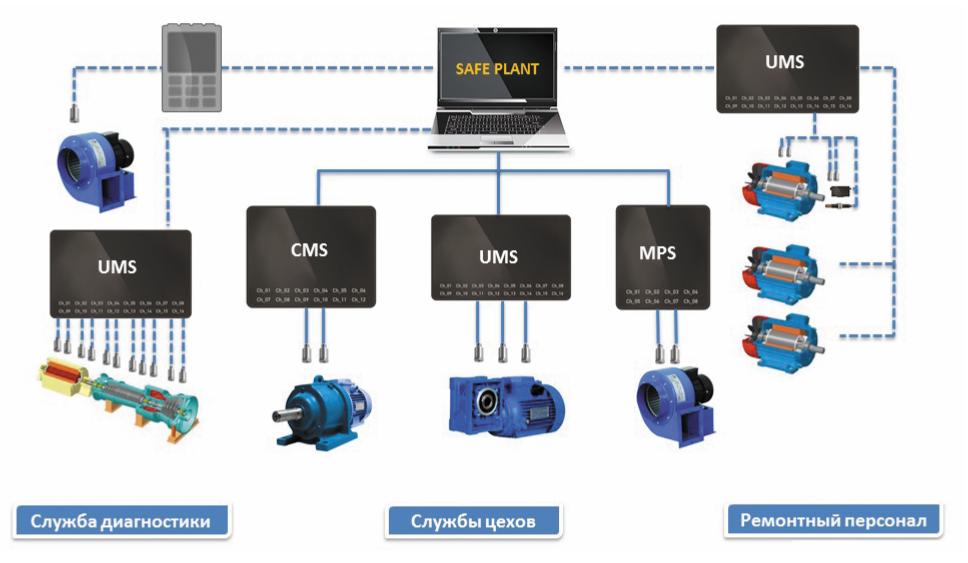
Однако для успешной реализации данного комплекса мероприятий требуется организация единого многоуровневого информационного пространства, позволяющего всем участникам технологического, производственного и ремонтного процессов осуществлять быстрый и эффективный обмен данными. Примером программного продукта, представляющего собой единую интеллектуальную платформу для сбора, хранения, отображения и анализа различной диагностической и ремонтной информации и оснащенного экспертным модулем автоматизированной диагностики, служит одноименный пакет SAFE PLANT.
Список литературы
- Неразрушающий контроль: Справочник: В 7 т./Под общ. ред. В.В. Клюева. Т. 7: Кн. 2: Вибродиагностика/М.: Машиностроение, 2005. 829 с.
- Сушко А.Е., Грибанов В.А. Проблемы оценки технического состояния динамического оборудования опасных производственных объектов//Безопасность труда в промышленности. 2011. №10. С. 58–65.
- Сушко А.Е. Комплексный подход к вопросам повышения надежности работы оборудования//Вибрация машин: измерение снижение защита. 2006. №3. С. 42–47.
- Радчик И.И., Рябков В., Сушко А.Е. Комплексный подход к вопросам надежности работы основного и вспомогательного оборудования современного металлургического производства // Оборудование. Технический альманах. 2006. №1. С. 24–28.
- Сушко А.Е. Практические аспекты внедрения систем вибрационной диагностики в условиях современных промышленных производств//Вибрация машин: измерение снижение защита. 2007. №4 С. 24–30.
- Сушко А.Е. Современные технологии повышения надежности эксплуатации и ремонта роторного оборудования опасных промышленных производств//Ремонт. Восстановление. Модернизация. 2010. №8 С. 5–11.
- Сушко А.Е. Современные подходы к формированию системы оптимального технического обслуживания и ремонта компрессорного оборудования//Компрессорная техника и пневматика. 2007. №1. С. 33–37.
- Сушко А.Е. Практика использования многоканальной виброизмерительной аппаратуры для диагностики агрегатов нефтехимического комплекса // Вибрация машин: измерение снижение защита. 2008. №4 С. 22 25.
- Сушко А.Е. Вибродиагностика как путь экономии. Практика внедрения современных ресурсосберегающих технологий для повышения надежности эксплуатации и ремонта оборудования опасных промышленных производств//Химагрегаты. 2010. №3 С. 34 – 37.