Автор: Д.В. Еранцев (ОАО «КуйбышевАзот»).
Опубликовано в журнале Химическая техника №6/2015
Усиление конкуренции на внешнем и внутренних рынках продукции компании делает особенно актуальным для производств ОАО «КуйбышевАзот» решение трех основных задач:
- повышение коэффициента использования мощностей (т.е. наращивание выработки);
- обеспечение стабильности работы;
- снижение потребления энергоресурсов.
Для достижения поставленных целей на производстве аммиака за последнее десятилетие выполнен ряд важных технических мероприятий. Так, в 2004 г. был заключен контракт с фирмой Uhde (Германия) на проведение реконструкции агрегата аммиака с увеличением мощности с 1 600 до 1 800 т/сутки.
В 2010 г. после завершения строительства трубопровода газа высокого давления обеспечение производства аммиака технологическим газом было переведено на работу от нового трубопровода. Компрессор природного газа с приводом от паровой турбины был остановлен в резерв, что позволило снизить потребление пара на 15 т/ч.
На период проведения капитального ремонта 2010 г. были запланированы и выполнены следующие работы, направленные как на увеличение выработки аммиака, так и на снижение энергоресурсов:
- монтаж змеевиков подогревателя природного газа в холодной зоне БТА дымохода печи первичного риформинга поз.107 с исключением из технологической схемы огневого подогревателя, что позволило снизить потребление топливного газа на 600 м3/ч;
- монтаж и включение в работу параллельного реактора синтеза аммиака, что повлияло на снижение давления в контуре синтеза с 24 до 21,5 МПа (с учетом модернизации турбины компрессора синтезгаза, проведенной фирмой UTE, снижение потребления пара с давлением 10 МПа составило более чем 12 т/ч.;
- монтаж узла очистки синтез-газа от кислородсодержащих примесей и масла (установка холодильника на входе четвертой ступени компрессора синтез-газа с реконструкцией сепаратора поз.124-F и установкой коалесцентного фильтра).
В 2006–2007 гг. при увеличении нагрузки агрегата по природному газу для поддержания необходимого соотношения азот/водород в синтезгазе были смонтированы и включены в работу вентиляторы поддува на линии всасывания первой секции компрессора технологического воздуха.
Потребляемая мощность вентилятора составляла 630 кВт, что значительно влияло на общий показатель потребления электроэнергии. С учетом наращивания нагрузки в 2011 г. было принято решение о проведении модернизации компрессора технологического воздуха с реконструкцией корпуса низкого давления и заменой воздухоохладителей после второй и третьей ступени более эффективными. Реконструкция компрессора была выполнена по проекту ООО «Невзапмаш» с переобвязкой воздухоохладителей по проекту ПКБ предприятия.
В 2011 г. была проведена полная замена теплоизоляционного покрытия на участке трубопровода 10 МПа, пролегающем по наружной установке общей протяженностью около 160 м.
Результатом данной работы стало снижение потерь теплоты на 0,9 Гкал (~1 000 кВт⋅ч). Экономия природного газа после замены теплоизоляции составила около 160 м3/ч.
В 2012 г. с целью повышения надежности работы компрессора синтез-газа, а также для исключения имеющихся потерь пара была произведена замена приводов насосов уплотняющего масла низкого и высокого давления с паровых турбин на электродвигатели. Таким образом, потребление пара 4 МПа сократилось на 10 т/ч, а расход пара 0,35 МПа противодавления паровых турбин, не имеющий применения на агрегате и на предприятии, до этого сбрасываемый в атмосферу, вошел в необходимый баланс на производстве аммиака.
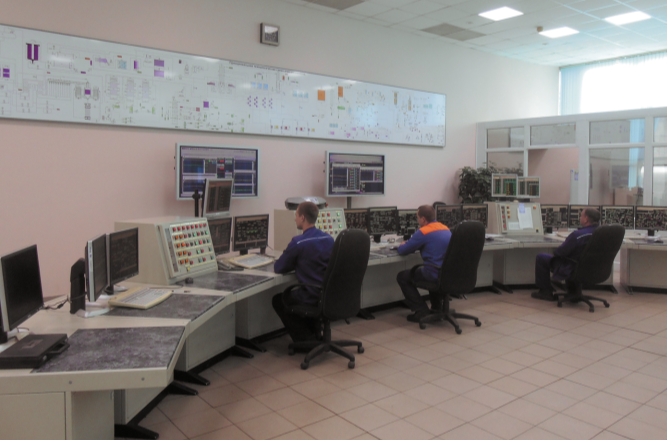
Снижение потребления пара на агрегате с увеличением выработки по аммиаку не могло не вызвать изменений в балансе системы парообразования и парораспределения.
Для обеспечения поступления необходимого количества воды на подогреватели блоков метанирования и синтеза в период капитального ремонта 2012 г. был смонтирован и включен в работу паропровод с редуцирующим узлом и с системой охлаждения для выдачи пара 4 МПа в общезаводской коллектор 2 МПа.
В настоящее время выдача пара потребителям предприятия составляет не менее 30 т/ч, а необходимый баланс нагрузки по природному газу и системы парообразования восстановлен.
Во время проведения капитального ремонта 2014 г. одна из запланированных и выполненных работ была направлена как на увеличение выработки аммиака, так и на снижение энергоресурсов: доработка узла очистки синтез-газа от кислородсдержащих примесей и масла с реконструкцией сепаратора после третьей ступени компрессора синтез-газа.
Была проведена также замена ранее установленных внутренних устройств сепаратора поз.124-F сепарирующим устройством, изготовленным по проекту ПКБ ОАО «Куйбышев- Азот». Причиной замены внутренних устройств, установленных в 2012 г., явилась повышенная концентрация аммиака при подключении узла отмывки от кислородсодержащих соединений и масла до 5,0% в синтез-газе на выходе из сепаратора с последующим ростом давления в блоке синтезе аммиака. Увеличение площади поверхности барботера сепаратора, расположенного внутри каплеотбойной корзины, позволило уменьшить скорость прохождения газа и снизить унос жидкого аммиака.
Результатом проведенной реконструкции сепаратора в 2014 г. с последующим включением в работу узла отмывки и коалесцентного фильтра явилось снижение содержания аммиака в циркуляционном газе на входе в колонны синтеза с 4,5 до 3,5%; снижение давления в блоке синтезе аммиака составило 1,2 МПа (с 21,6 до 20,4 МПа).
Была достигнута стабильная и эффективная работы конденсационной колонны, а увеличение выработки продукционного аммиака составила 11 т/сут.
Значимым фактором для обеспечения двухгодичного и более пробега агрегата аммиака, а также такого оборудования, как компрессор технологического воздуха, абсорбционно-холодильная установка и др., является эффективность работы теплообменного оборудования. Именно эти факторы ранее и лимитировали обеспечение выработки аммиака и увеличивали энергозатраты производства.
Ранее применяемая программа реагентной обработки водооборотных циклов не позволяла обеспечивать качественный съем теплоты на теплообменном оборудовании на протяжении межремонтного пробега агрегата в течение года. Значительные отложения органического и неорганического характера приводили к неизбежному снижению теплосъема и увеличению затрат для возможности поддержания требуемой нагрузки и внеплановой чистки оборудования.
С 2011 г. на производстве аммиака выполнен переход на комплексную программу реагентной обработки оборотной воды систем охлаждения ВОЦ-9,10 компании General Electric Water & Process Technologies (GE W&PT).
Конечной целью данной реагентной обработки является достижение максимальной эффективности и надежности работы систем охлаждения при снижении общих эксплуатационных расходов. Данная задача решается за счет минимизации и/или полного устранения проблем, связанных с процессами коррозии, отложениями накипи и микробиологическим обрастанием.
С целью обеспечения максимальной эффективности программы реагентной обработки и возможности оперативной корректировки в зависимости от изменения текущих условий эксплуатации, т.е. для достижения оптимальной стоимости обработки реализован гибкий подход, предусматривающий использование компонентов программы в виде отдельных реагентов (многобочковой подход).
Контроль за комплексной программой реагентной обработки осуществлялся по результатам аналитического контроля центральной лабораторией ОАО «КуйбышевАзот» (отбор проб подпиточной воды один раз в неделю, охлаждающей воды два раза в неделю), лабораторией ОТК производства аммиака и на основании еженедельных сервисных визитов представителя (GE W&PT).
По результатам аналитического контроля осуществлялся оперативный контроль оптимального водного баланса и корректировка основных анализируемых параметров путем изменения в ручном режиме расходов на насосах-дозаторах в пределах нормируемых величин.
Помимо мониторинга основных показателей подпиточной и охлаждающей воды, концентраций основных компонентов применяемых реагентов осуществлялся оперативный контроль стабильного уровня pH оборотной воды ВОЦ-9,10 плавным регулированием расходов на насосах-дозаторах серной кислоты.
Динамическим колебаниям уровня pH в основном способствует периодическое попадание аммиака в охлаждающую воду, что первоначально сопровождается повышением уровня pH за счет высвобождения гидроксильной группы при диссоциации гидрата аммиака и затем приводит к развитию процессов нитрификации.
При аналитическом контроле для оценки стабильности систем охлаждения также прогнозировалась величина индекса Ланжелье, который характеризует склонность охлаждающей воды к вероятному образованию карбонатных отложений на теплопередающих поверхностях технологического оборудования. При превышении допустимой положительной величины индекса Ланжелье возникает риск образования нерастворимых карбонатных отложений накипного характера на стенках трубных пучков теплообменного оборудования, что может способствовать риску существенного снижения эффективности теплосъема.
В ходе планового останова производства аммиака на капитальный ремонт проведены вскрытие и осмотр теплообменных аппаратов, охлаждаемых оборотной водой ВОЦ-9,10, с целью оценки состояния теплопередающих поверхностей трубных пучков в условиях двухлетнего безостановочного пробега технологического оборудования c применением комплексной программы реагентной обработки GE W&PT.
При осмотре теплообменников установлено, что поверхности внутритрубного пространства со стороны входа и выхода оборотной воды воздухоохладителей компрессора технологического воздуха визуально чисты (до металлического блеска), неорганические, микробиологические загрязнения и отложения отсутствуют.
Стабильный режим применения комплексной программы реагентной обработки GE W&PT оборотной воды ВОЦ-9,10 в условиях двухлетнего безостановочного пробега технологического оборудования цеха №11 производства аммиака признан эффективным, что подтверждается стабильной работой компрессора технологического воздуха на максимальных нагрузках даже в летний период без дополнительных энергозатрат на привод турбины компрессора. Температура технологического воздуха после воздухоохладителей компрессора не превышает 35°С. Абсорбционно-холодильная установка на порядок увеличила количество принимаемого газообразного аммиака за счет эффективного съема теплоты абсорбции.
Для дальнейшей оптимизации режима реагентной обработки специалистами GE W&PT совместно с техническими специалистами производства аммиака ОАО «КуйбышевАзот» разработано техническое решение по автоматизации процесса дозирования реагентов и обеспечению автоматического он-лайн мониторинга программы реагентной обработки с применением Интегрированного Центра Управления TrueSense.

В ближайшем будущем система позволит решать следующие задачи:
- оптимизировать и снизить затраты на эксплуатацию систем охлаждения;
- автоматически измерять уровень pH, электропроводность, концентрацию основных дозируемых компонентов;
- автоматически управлять насосами-дозаторами в соответствии с результатами измерений;
- передавать данные о фактическом состоянии системы охлаждения с необходимой периодичностью и в заданное время через интерфейсы связи, что позволяет осуществлять удаленный мониторинг в режиме реального времени с любого устройства, имеющего доступ в интернет (компьютер, планшет, мобильный телефон);
- обеспечить гибкую систему обвязки оборудования, позволяющую соответствовать новым требованиям за счет дополнения измерительного комплекса новыми датчиками и сенсорами.
В летний период существенное количество энергоресурсов расходуется на конденсацию аммиака, в данном случае за счет необходимости включения в работу аммиачного компрессора с потреблением электроэнергии 5 МВт⋅ч. Принятое в 2012 г. решение о замене аппаратов воздушного охлаждения на одной из ниток абсорбционно-холодильной установки конденсатором испарительного типа фирмы Baltimore Aircoil (Бельгия) компании «Инфинит Групп» полностью себя оправдало. При значительно меньшем энергопотреблении конденсатор имеет высокую эффективность работы. В 2014 и 2015 гг. произведена замена аппаратов воздушного охлаждения конденсаторами испарительного типа на двух других нитках. Таким образом, в летний режим работы выработку аммиака не лимитирует вторичная конденсация, а пуск энергозатратного аммиачного компрессора производится значительно позже и на более короткое время.
Замена аппаратов воздушного охлаждения конденсаторами испарительного типа дала следующие результаты:
- применение оборудования холодопроизводительностью до 5,2 МВт взамен аппаратов воздушного охлаждения мощностью 3,8 МВт на каждой нитке;
- снижение давления газообразного аммиака на абсорбционно-холодильных установках на 0,5 МПа (с 1,7 до 1,2 МПа);
- увеличение нагрузки на аммиачный испаритель поз. 606А до 100%;
- полное исключение возможности попадания воды системы увлажнения на оборудование, исключение, таким образом, коррозии.
Нельзя оставить без внимания и работу каталитических стадий производства аммиака.
Одним из важных показателей работы катализатора первичного реформинга является содержание остаточного метана в конвертированном газе на выходе из трубчатой печи.
Положительный итог выполнения решения в отношении выбора трехъярусной загрузки катализатора, произведенного в 2014 г., заключается в снижении размера катализатора в самой нижней части труб, т.е., там, где близко к трубам расположены газосборные туннели, что обусловливает более высокую активность и способствует снижению температуры стенки трубы. Это наиболее важно в условиях повышенной нагрузки и значительного срока пробега реакционных труб печи первичного реформинга агрегата аммиака.
Специалистами компании Johnson Matthey было выполнено детальное моделирование работы катализатора первичного риформинга при условиях обеспечения выработки аммиака не менее 1 800 т в сутки, при этом температура конвертированного газа на выходе из печи не должна превышать 785°С при остаточном содержании метана не более 10,9 %.
Таким образом, результатом трехъярусной загрузки катализатора Johnson Matthey является работа печи при следующем профиле загрузки:
- KATALCO™ 25-4Q – верхние 50% высоты трубы;
- KATALCO™ 57-4GQ – средние 34% высоты трубы;
- KATALCO™ 57-4Q – нижние 16% высоты трубы.
При выборе катализатора первичного реформинга (производство Johnson Matthey) учитывали, что он способен выдерживать жесткие эксплуатационные условия, работу при повышенных температурах, а также продолжительное пропаривание, быстрые пуски и остановки, конденсацию пара.
Как показал опыт эксплуатации предыдущих загрузок, при умеренном отравлении катализаторы Johnson Matthey легко поддаются регенерации и практически полностью восстанавливают первоначальную активность.
Результаты загрузки трубчатой печи первичного реформинга катализатором Johnson Matthey:
- температура конвертированного газа на выходе из печи составила 783°С;
- содержание остаточного метана – 10,7–10,9%;
- перепад давления на катализаторе поддерживается на уровне 0,3 МПа.
При пуске были отмечены стабильная активация всего объема катализатора, его быстрый запуск. При работе не выявлено наличия локальных перегревов реакционных труб.
По данным за апрель 2015 г. агрегат аммиака достиг следующих показателей:
- выработка аммиака – 1 820 т/сут;
- расходный коэффициент природного газа – 1 070 м3/т; (в пересчете на стандартную калорийность – 7 900 ккал/м3, при калорийности природного газа 8 200 ккал/м3);
- расходный коэффициент электроэнергии – 75 кВт/т.
В настоящее время дальнейшее наращивание выработки аммиака на агрегате уже не является первоочередной задачей. Это связано с тем, что вложения, которые требуются для выхода на производительность, существенно превышающую уже достигнутую, неоправданно велики. Главное сегодня – безостановочная работа и снижение потребления, в первую очередь, природного газа, электроэнергии и воды. Эти цели и преследовала успешно проведенная ранее модернизация агрегата аммиака. В совокупности все выполненные за последние годы работы были комплексом мероприятий, направленных на снижение удельного потребления сырья и энергоресурсов, а также на повышение уровня стабильности работы агрегата.
Итогом этой деятельности стало достижение в производстве аммиака ОАО «КуйбышевАзот» одних из лучших показателей среди аналогичных агрегатов, действующих в странах СНГ.