Автор: В.Н. Мухин, И.А. Тришкина, И.Б. Степанищев (ОАО «ВНИКТИнефтехимоборудование»).
Опубликовано в журнале Химическая техника №6/2015
Длительная эксплуатация приводит к изменению свойств металла сварных соединений труб печных змеевиков нефтеперерабатывающих установок. В связи с этим в период ревизии [1] или диагностирования технического состояния печей [2] предусмотрен контроль сварных соединений внешним осмотром и различными физическими неразрушающими методами. Кроме того, действующие нормативные документы предусматривают выполнение стилоскопирования материалов новых элементов змеевиков, изготовленных из легированных сталей, независимо от наличия сертификата, а также измерение твердости непосредственно на оборудовании. Неразрушающий контроль сварных швов, сваренных в процессе монтажа или ремонта, должен охватывать 100% сварных соединений.
Считается, что неразрушающий контроль может обеспечить надежную эксплуатацию сварных соединений и печных змеевиков в целом. Металлографические исследования и механические испытания образцов, вырезанных из сварных соединений, не являются обязательными методами контроля и проводятся только в необходимых случаях [1, 2].
Вырезка контрольного участка для исследования физико-механических свойств металла труб и сварного соединения необходима для определения возможности дальнейшей эксплуатации печных змеевиков, отработавших проектный ресурс. При этом исследование разрушающими методами должно проводиться как минимум на одном однородном (монтажном или ремонтном) и одном разнородном (ремонтном) сварном соединении, работающих с наибольшей температурой стенки в камерах радиации [3].
Ремонтная сварка элементов печного змеевика из теплоустойчивых хромомолибденовых сталей аустенитными электродами без термической обработки разрешена как временный вариант на срок до ближайшего капитального ремонта или более длительный [4], определяемый с привлечением отраслевой научно-исследовательской организации.
Исследование металла контрольных участков сварных соединений печных змеевиков в соответствии с документами [2, 3] выполняется в следующем объеме:
- оценка химического и фазового состава основного и наплавленного металла;
- определение наличия микродефектов в поперечном сечении сварного соединения, а также микроструктуры в зонах шва и термического влияния, межкристаллитной коррозии (для аустенитных сталей);
- измерение твердости по поперечному сечению в зонах шва и термического влияния;
- определение механических свойств при комнатной и рабочей температурах.
Исследование механических свойств сварных соединений, работающих в условиях ползучести, должно включать испытания на длительную прочность [3].
По результатам кратковременных и длительных испытаний (в зависимости от температуры эксплуатации и материального исполнения) элементов змеевиков оценивается остаточная работоспособность печного змеевика.
В 2014 г. «Испытательная лаборатория материалов и элементов конструкций» ОАО «ВНИКТИнефтехимоборудование» выполнила исследования 13 контрольных участков труб печных змеевиков из сталей 20, 15Х5М, 12Х1МФ и 12Х18Н10Т со сварными соединениями, как однородными, так и разнородными (табл. 1). Расчетные температуры стенки печных змеевиков составляли 265…580°С, срок эксплуатации – 87 000…410 000 ч.
Исследования макрошлифов показали, что в семи из 13 сварных соединений имелись различные дефекты изготовления: неполномерность шва, провисание корня, наплывы, недопустимое смещение кромок, подрезы, несплавления в сварном шве, трещины.
Результаты химического анализа, осуществленного методами аналитической химии, свидетельствовали о том (см. табл. 1), что пять из 13 сварных соединений (маркировка «1», «2», «6», «9», «13») были выполнены с применением основных или сварочных материалов, не предусмотренных нормативными документами для рассматриваемых условий эксплуатации, что ускорило структурную деградацию, привело к макрои микроповреждениям и отрицательно сказалось на характеристиках механических свойств. Так, вследствие применения для сварки труб из коррозионно-стойкой стали 12Х18Н10Т электрода Э-10Х25Н13Г2 (ОЗЛ-6) вместо Э-08Х19Н10Г2Б (ЦЛ-15) после длительной эксплуатации при температуре 450°С произошло охрупчивание металла сварного шва и снижение пластичности сварного соединения с маркировкой «13» (см. табл. 1).
Ударная вязкость КCU понизилась до 15 Дж/см2 при минимально допустимой 70 Дж/см2, а угол изгиба, равный 40°, был меньше минимального значения (100°) по РД 26-02-80–2004 «Змеевики сварные для трубчатых печей. Требования к проектированию, изготовлению и поставке».
Применение для сварки труб из стали 12Х18Н10Т высокохромистого сварочного материала, формирующего аустенитно-ферритную структуру с высоким содержанием феррита в металле сварного шва, не стабилизированную ниобием, привело к развитию 475-градусной хрупкости, т.е. к внутрифазовому перераспределению хрома в феррите, выделению и растворению карбидов хрома в α-фазе при температуре эксплуатации, недостаточной для выделения σ-фазы (350…550°С). При нагреве до температуры 700°С с выдержкой в течение 1 ч и охлаждением на воздухе предвыделения в феррите, вызывающие фазовый наклеп, растворились, а ударная вязкость сварного соединения повысилась до 70 Дж/см2.
Таблица 1
Эксплуатационные параметры сварных соединений печных змеевиков
Маркировка сварного соединения | Марка стали свариваемых труб | Температура эксплуатации, °С | Срок эксплуатации печного змеевика, тыс. ч | Требования
РД 26-02-80–2004, [4, 5] |
Фактически примененные сварочные материалы |
1 | 15Х5М | 580 | 240 | Св-6Х5Г2СМФТЮЧ | Св-6Х3Г2СМФТЮЧ |
2 | 12Х1МФ | 580 | 140 | – | Э-09Х15Н25М6Г2Ф |
3 | 15Х5М | 570 | 410 | Э-10Х5МФ (ЦЛ-17) | Э-10Х5МФ (ЦЛ-17) |
4 | 20 | 265 | 219 | УОНИ 13/45 | УОНИ 13/45 |
5 | 15Х5М | 455 | 210 | Э-06Х25Н40М7Г2 (АНЖР-2), Э-10Х25Н13Г2 (ОЗЛ-6)* | Э-10Х25Н13Г2 (ОЗЛ-6) |
6 |
15Х5М |
555 |
87 |
Э-08Х25Н60М10Г2 (АНЖР-1), Э-06Х25Н40М7Г2 (АНЖР-2)* | Э-11Х15Н25М6АГ2 (ЭА-395/9) |
7 | 15Х5М | 570 | 96 | Э-10Х5МФ (ЦЛ-17) | Э-10Х5МФ (ЦЛ-17) |
8 | 15Х5М | 400 | 104 | Э-10Х5МФ (ЦЛ-17) | Э-10Х5МФ(ЦЛ-17) |
9 | 15Х5М | 580 | 108 | Э-08Х25Н60М10Г2 (АНЖР-1), Э-06Х25Н40М7Г2 (АНЖР-2)* | Э-09Х15Н25М6Г2Ф |
10 | 12Х18Н10Т | 460 | 192 | Э-08Х19Н10Г2Б (ЦЛ-15) | Э-08Х19Н10Г2Б (ЦЛ-15) |
11 | 12Х18Н10Т | 475 | 192 | Э-08Х19Н10Г2Б (ЦЛ-15) | Э-08Х19Н10Г2Б (ЦЛ-15) |
12 | 12Х18Н10Т | 430 | 201 | Э-08Х19Н10Г2Б (ЦЛ-15) | Э-08Х19Н10Г2Б (ЦЛ-15) |
13 | 12Х18Н10Т | 450 | 201 | Э-08Х19Н10Г2Б (ЦЛ-15) | Э-10Х25Н13Г2 (ОЗЛ-6) |
* Допускается применение при более коротком времени эксплуатации после ремонта по сравнению с основным технологическим вариантом. |
Бездефектные сварные соединения труб с маркировкой «10» – «12» (см. табл. 1) из той же стали 12Х18Н10Т, выполненные в соответствии с требованиями нормативных документов электродами Э-08Х19Н10Г2Б (ЦЛ-15), имели после длительной эксплуатации удовлетворительные механические свойства при комнатной и повышенной температурах.
Таблица 2
Характеристики длительной прочности и длительной пластичности металла исследованных вырезок печных змеевиков
Маркировка образцов | Расчетная температура, °С | Предел длительной прочности на срок 35 000 ч s35000, МПа | Минимальное значение относительного удлинения после разрушения dк, % | Минимальное значение относительного сужения после разрушения yк, % | |
Сварное соединение | Основной металл* | Сварное соединение | |||
1 | 580 | 42,5 | 50,5 | 10,07 | 17,18 |
2 | 580 | 58,0 | 73,5 | 1,18 | 1,99 |
3 | 570 | 52,5 | 44,5 | 6,31 | 32,53 |
6 | 555 | 45,5 | 52,5 | 6,27 | 17,18 |
7 | 570 | 46,0 | 54,5 | 13,36 | 55,1 |
9 | 580 | 50,5 | 45,0 | 29,09 | 82,37 |
* Наименьшее из значений, определенных для металла двух свариваемых труб |
Испытания на растяжение показали соответствие пределов прочности всех исследованных сварных соединений (см. табл. 1) требованиям стандартов на основной металл в состоянии поставки.
По результатам проведенных испытаний на длительную прочность шесть контрольных вырезок металла сварных соединений, работавших при температурах ползучести (выше 550°С), в четырех из них (маркировка «1», «2», «6», «7») пределы длительной прочности сварного соединения на срок последующей эксплуатации, равный межремонтному периоду (35 000 ч), оказались ниже пределов длительной прочности основного металла (табл. 2).
Кроме того, при удовлетворительных значениях кратковременных характеристик пластичности (δ20 = 19,0… 22,0%, ψ20 = 78,0%) металл с маркировкой «2» имел ограниченный ресурс длительной пластичности – δк < 2% (табл. 2). Для сварных соединений с пониженными пределами длительной прочности предел прочности или предел текучести при расчетных температурах также имели меньшие значения, чем соответствующие прочностные характеристики основного металла труб (табл. 3), а модули разности пределов текучести сварного соединения и основного металла были максимальными.
Таблица 3
Средние значения кратковременных характеристик прочности металла сварных соединений и основного металла труб, работавших в условиях ползучести
Маркировка образцов | Расчетная температура,
°С |
Предел прочности sв при расчетной температуре, МПа | Предел текучести s0,2 при расчетной температуре, МПа | /Δσ0,2/ | Твердость НВ | |||
Сварное соединение | Основной металл | Сварное соединение | Основной металл | Сварное соединение |
Металл труб |
|||
1 | 580 | 240 | 312 | 160 | 174 | 14 | 120…196 | 137 |
2 | 580 | 283 | 295 | 259 | 247 | 12 | 122…220 | 137 |
3 | 570 | 562 | 562 | 256 | 256 | 0 | 130…143 | 143 |
6 | 555 | 332 | 337 | 278 | 308 | 30 | 165…185 | 163 |
7 | 570 | 297 | 266 | 172 | 202 | 30 | 131…216 | 156 |
9 | 580 | 219 | 211 | 174 | 166 | 8 | 93…191 | 114 |
Если по результатам испытаний на растяжение при расчетной температуре можно качественно оценить соотношение длительной прочности сварного соединения и основного металла, то оценка длительной прочности сварных соединений печных змеевиков по результатам измерений твердости затруднительна. Нормативными документами регламентируются только верхние пределы допустимых значений твердости для хромомолибденовых сталей, способных подкаливаться на воздухе. Так, в соответствии с документом [1] твердость сварных соединений печных змеевиков из стали 15Х5М при сварке однородными электродами типа ЦЛ-17 не должна превышать 270 НВ. Согласно документу [4] для труб из стали 15Х5М с аустенитным швом твердость металла шва, измеренная на поперечных шлифах, должна быть не выше 220 НВ, околошовной зоны при сварке с наплавкой кромок – 325 НВ, без наплавки кромок – 375 НВ, основного металла – 270 НВ. Все исследованные сварные соединения хромомолибденовых сталей (см. табл. 1) имели твердость не выше норм отбраковки (см. табл. 3).
В соответствии с работой [6] критериями работоспособности сварных соединений паропроводов из теплоустойчивых хромомолибденованадиевых сталей, характеризующими неоднородность свойств, являются относительное упрочнение металла шва γм.ш и относительное разупрочнение зоны термического влияния ζрп: γм.ш = HVм.ш/НVо.м = 1…1,4, (1) где HVм.ш, НVо.м – твердость по Виккерсу соответственно металла шва и основного металла; ζрп = [(НVо.м – НVзтв рп.)/НVо.м)100% ≤ 10%, (2) где НVзтв рп. – твердость по Виккерсу металла разупрочненной прослойки зоны термического влияния.
Вычисления по формулам (1), (2) с учетом их справедливости для значений твердости НВ [7] показали, что для исследованных сварных соединений, работавших длительное время при температурах выше 550°С, показатель γм.ш, составляющий 1…1,7, и показатель ζрп, превышающий 10% для всех вырезок, кроме «6», не влияли на длительную прочность. При этом роль разупрочненной мягкой) прослойки в зоне термического влияния (рис. 1) играли околошовная зона или зона отпуска, котораянагревалась при сварке до температур ниже Ас1, а в случае однородных сварных соединений – повторно до температур выше 700°С при последующей термической обработке.
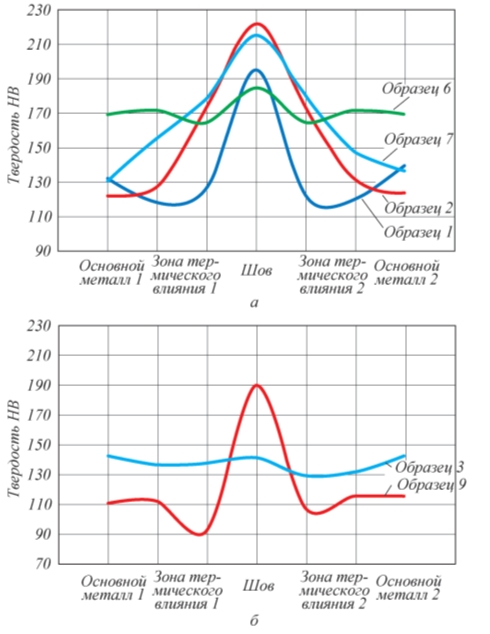
и выше (б) длительной прочности основного металла
Отсутствие однозначной зависимости длительной прочности от твердости объясняется тем, что твердость зон сварных соединений определяется химическим составом и структурными составляющими, а длительная прочность зависит также от агрегатной прочности зон металла с различными свойствами, от величины разупрочненных прослоек с низкими значениями предела текучести и предела ползучести, от наличия контактного упрочнения, локальных зон с микроповреждениями, от состояния границ зерен и степени их поврежденности.
Наименьший предел длительной прочности, прогнозируемый на 35 000 ч эксплуатации, имело сварное соединение «1» (см. табл. 1, 2) из стали 15Х5М, выполненное сварочным материалом с недостаточно высоким содержанием хрома (Св-6Х3Г2СМФТЮЧ вместо Св-6Х5Г2СМФТЮЧ), в результате чего твердость и прочность металла околошовной зоны были понижены (рис. 1, а). Кроме того, после термической обработки и последующей эксплуатации в течение 240 000 ч в зоне отпуска сформировалась структура металла, представляющая собой феррит и карбиды, которая отличалась от структуры основного металла свариваемых труб отсутствием карбидных колоний (рис. 2), значительным (до 7 мкм) размером карбидных частиц в виде пограничных прослоек, малой плотностью распределения карбидов по телу зерен, наличием по границам зерен отдельных микропор и микротрещин ползучести. Такие структуры типичны для стали 15Х5М с содержанием углерода менее 0,1% после длительных экспозиций при температурах выше 700°С с замедленным охлаждением в результате локальных перегревов, соответствуют низким пределам текучести при повышенной температуре испытаний на растяжение и низкой длительной прочности.
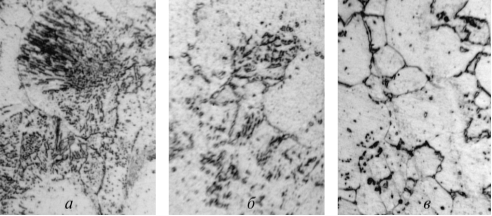
а – основной металл трубы 1 (140 НВ); б – основной металл трубы 2 (132 НВ); в – мягкая прослойка зоны термического влияния с микротрещинами (120 НВ)
Другим примером негативных последствий неправильного подбора материалов для изготовления элементов печных змеевиков явилось образование микротрещин в металле труб и сварного соединения 2 (см. табл. 1).
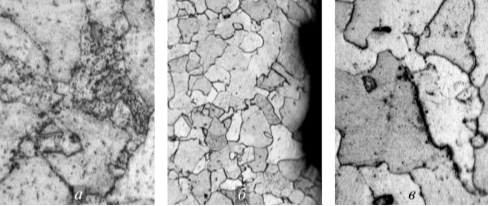
в водородсодержащей среде:
а – средняя часть трубы, x2 000; б – обезуглероженная внутренняя поверхность трубы, x500; в – то же, микротрещины, x2 000
В соответствии с рекомендациями по применению сталей в атмосфере водорода, приведенными в справочном руководстве [8], перлитная сталь 12Х1МФ не должна работать в водородсодержащих средах при температуре 580°С, так как карбид типа Ме3C в этих условиях не является устойчивым к воздействию водорода. И действительно, после 140 000 ч эксплуатации в металле трубы произошло обезуглероживание внутренней поверхности (рис. 3, б) на глубину до 14% фактической толщины стенки, снижение микротвердости в этом слое по сравнению с микротвердостью необезуглероженного металла (рис. 3, а) на 22,5% и образование в видоизмененном поверхностном слое микротрещин водородной коррозии по границам зерен (рис. 3, в). Кроме того, сварное соединение стали 12Х1МФ было выполнено с применением электрода Э-09Х15Н25М6Г2Ф, не обеспечивающего содержание никеля, достаточное для работы при температуре 580°С [9]. Никель как аустенитообразующий элемент повышает жаропрочность твердого раствора, ограничивает диффузионную подвижность углерода, препятствует образованию кристаллизационных и диффузионных прослоек. При малом содержании никеля в сварочном материале в околошовной зоне сварного соединения 2 у подрезов в корне шва сформировалась мелкозернистая диффузионная (обезуглероженная) прослойка, по границам зерен которой были обнаружены микроскопические поры и микротрещины ползучести (рис. 4, а, б).
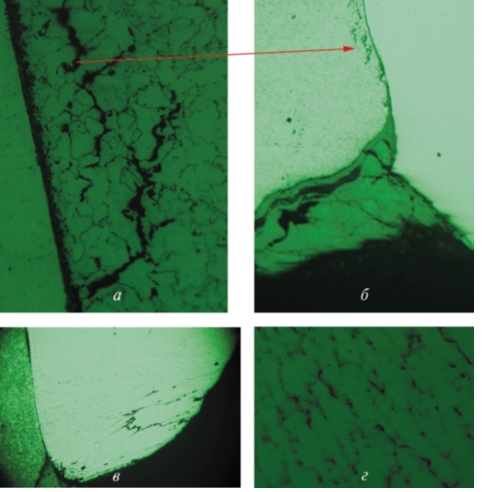
Э-09Х15Н25М6Г2Ф, после 140 000 ч
эксплуатации при температуре 580°С:
а – x1 000; б – x100 – микропоры и микротрещины ползучести в околошовной зоне; в –x100;
г – x2 000 – микротрещины в шве
В корне и вершине самого шва вблизи концентраторов напряжений (подрезов) образовались трещи-ны, распространявшиеся по границам дендритов (рис. 4, в), а также транси интеркристаллитные микротрещины у выделений избыточных фаз (рис. 4, г). Для определения причин образования трещин были использованы результаты химического анализа и соотношения [6]:
НCS = C[(S + P + Si/25 + Ni/100)1000)/(3M
n + + Cr + Mo + V)]; (3)
РSR = Cr + Cu + 2Mo + 10V + 7Nb + 5Ti – 2; (4)
ΔG1 = Cr + 3,3Mo + 8,1V + 10C – 2. (5)
Сравнение показателя сопротивления образованию горячих (кристаллизационных) трещин HCS и показателей сопротивления образованию термических трещин повторного нагрева РSR и ΔG1 исследованного металла с критериями, представленными в работе [6], показано в табл. 4.
Таблица 4
Показатели склонности сварных соединений к образованию трещин
Маркировка сварных соединений | Вариант сварки | НCS | РSR | ΔG1 |
1 | I | 0,68 | 4 | 6 |
2 | II | 0,13 | 27 | 32 |
3 | I | 0,55 | 6 | 7 |
5 | II | 0,64 | 15 | 16 |
6 | II | 1,26 | 14 | 18 |
7 | I | 0,00 | 5 | 6 |
8 | I | 0,89 | 6 | 8 |
9 | II | 0,78 | 18 | 20 |
Отсутствие склонности
к образованию трещин [6] |
– | ≤4 | ≤0 | ≤2 |
Варианты сварки: I – однородными со сталью электродами;
II – электродами аустенитного класса без термической обработки |
Данные табл. 4 свидетельствуют о том, что исследуемый металл сварного шва не склонен к образованию горячих трещин при сварке, но проявляет высокую склонность к образованию трещин повторного нагрева, которые возникают при последующей за сваркой эксплуатации сварных соединений в интервале температур 500…700°С в условиях ползучести [6]. При этом сварные соединения, выполненные аустенитными электродами без термической обработки, более склонны к образованию термических трещин повторного нагрева в условиях ползучести, чем однородные сварные соединения из стали 15Х5М.
Образованию такого рода трещин способствовало выделение в сварном шве 2 карбидов у границ зерен, повышающих прочность и снижающих пластичность, наличие крупных зерен аустенита и высокие напряжения, соответствующие пределу текучести в зонах концентрации напряжений.
Микроповрежденность внесла вклад в снижение длительной прочности металла сварного соединения 2 до уровня ниже пределов длительной прочности основного металла труб, а длительной пластичности – до недопустимых значений (см. табл. 2): минимальное относительное удлинение δк после разрушения образцов составило при напряжении испытаний 140 МПа –5,14%; 100 МПа – 2,03%; 75 МПа – 1,18%; а относительное сужение ψк – соответственно 3,92%; 1,99%; 1,99%.
Аналогичные повреждения сварного шва – трещины в зонах концентрации напряжений у дефектов изготовления (подрезы, смещение кромок, непровары) и микротрещины – были обнаружены в швах сварных соединений стали 15Х5М с маркировкой 6 и 9 (рис. 5), выполненных аустенитными электродами Э-11Х15Н25М6АГ2 (ЭА-395/9) и Э-09Х15Н25М6Г2Ф вместо предусмотренных нормативными документами Э-08Х25Н60М10Г2 (АНЖР-1) или Э-06Х25Н40М7Г2 (АНЖР-2). Длительная прочность металла сварного соединения 6 оказалась ниже длительной прочности основного металла (см. табл. 2) и ниже минимального значения по РТМ 26-02-67–84 «Методика расчета на прочность элементов печей, работающих под давлением» для прогнозируемого срока эксплуатации (рис. 6).
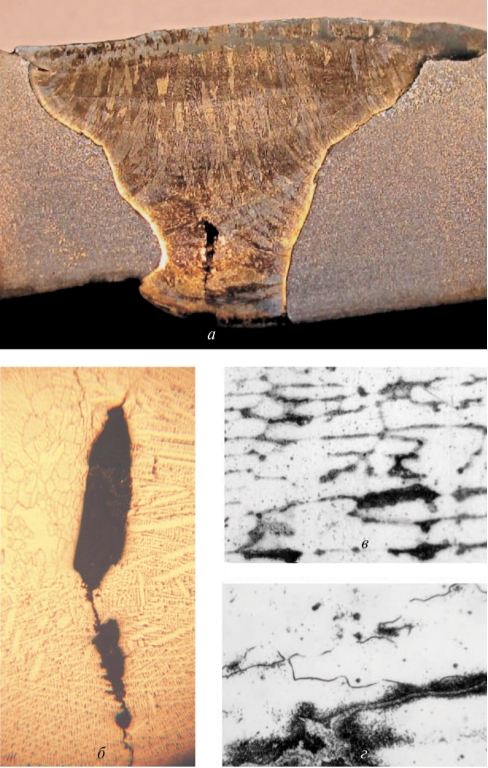
В то же время при высоких значениях показателей РSR и ΔG1 трещины в сварном соединении 5 из стали 15Х5М с применением электрода Э-10Х25Н13Г2 (ОЗЛ-6) после 210 000 ч эксплуатации отсутствовали, так как оно не имело дефектов формы, размеров, сплошности, а, значит, концентраторов напряжений, и работало при температуре 455°С, которая находится ниже порога ползучести.
В однородных сварных соединениях трещины отсутствовали. Качественными, достаточно прочными и пластичными были сварные соединения с маркировкой 3, 4 и 8 (см. табл. 1), выполненные без дефектов электродами, рекомендуемыми нормативными документами Э-10Х5МФ (ЦЛ-17) для труб из стали 15Х5М и УОНИ 13/45 для труб из стали 20. В однородном сварном соединении 7 (см. табл. 1) труб из стали 15Х5М дефекты изготовления, а также микрои макроповрежденность отсутствовали, твердость монотонно снижалась от сварного шва к основному металлу (см. рис. 1, а), по которому и произошло разрушение во время кратковременных и длительных испытаний. Разность пределов текучести основного металла и сварного соединения 7 была максимальной (см. табл. 3), а длительная прочность – ниже длительной прочности основного металла, хотя и соответствовала минимальному уровню значений по РТМ 2602-67–84 (см. рис. 6).
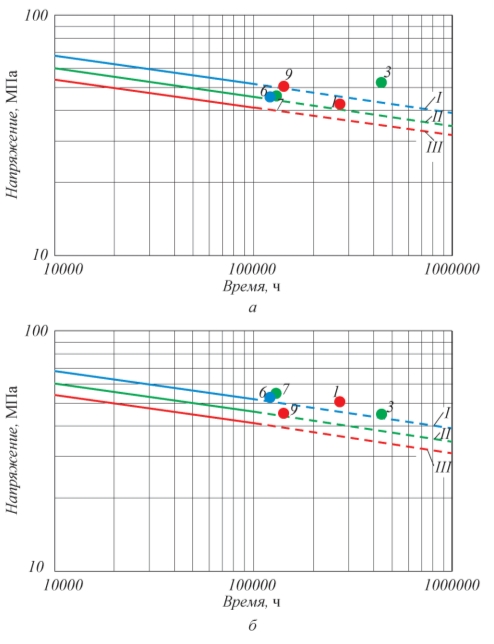
l, I – 555°С; l, II – 570°С; l, III – 580°С;
цифрами обозначена маркировка образцов
Прочностные характеристики, полученные в результате испытаний металла контрольных вырезок из элементов печных змеевиков (труб и сварных соединений), позволили определить допускаемые напряжения для прочностных расчетов. Применение коэффициента запаса прочности, равного 1,5, при определении допускаемых напряжений по экспериментально полученным пределам длительной прочности для трех из шести сварных соединений (2, 6, 7) привело к снижению допускаемых напряжений до уровня ниже минимальных нормативных значений по ГОСТ Р 52857.1–2007 «Сосуды и аппараты. Нормы и методы расчета на прочность. Общие требования» и РД 10-249–88 «Нормы расчета на прочность стационарных котлов и трубопроводов пара и горячей воды» (рис. 7). Это свидетельствует о необходимости учета длительной прочности сварных соединений как разнородных, так и однородных, при оценке остаточного ресурса печных змеевиков, отработавших проектный ресурс.
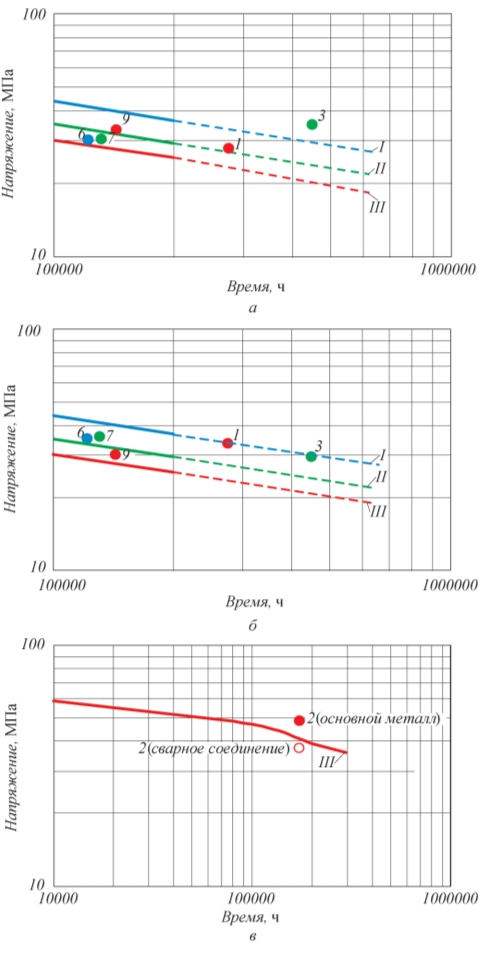
I, l – 555°С; II, l – 570°С; III, l, – 580°С; а, б – сталь 15Х5М,
в – сталь 12Х1МФ; цифрами обозначена маркировка образцов
Результаты проведенных исследований показали, что для безопасной эксплуатации печного змеевика необходимо проведение испытаний сварного соединения на длительную прочность, если предел текучести сварного соединения при повышенной температуре ниже предела текучести основного металла трубы.
Так как в большинстве случаев снижение механических свойств сварных соединений печных змеевиков после длительной эксплуатации до недопустимого уровня обусловлено неправильным подбором основных и сварочных материалов, в период ремонта печи следует особое внимание уделить определению химического состава труб и сварных швов переносными приборами.
Список литературы
- СТО-СА-03-004–2009. Трубчатые печи, резервуары, сосуды и аппараты нефтеперерабатывающих и нефтехимических производств. Требования к техническому надзору, ревизии и отбраковке. 2010.
- Методика оценки остаточного ресурса трубчатых печей нефтеперерабатывающих, нефтехимических и химических производств. 1998.
- РД РТМ 38.14.006–86. Методика определения сроков эксплуатации змеевиков печей установок каталитического риформинга, отработавших проектный ресурс. 1986.
- СТО 38.17.003–2009. Стандарт организации. Сварка технологических трубопроводов и печных змеевиков при ремонте и реконструкции нефтеперерабатывающих и нефтехимических установок. 2012.
- Технологическая инструкция по сварке трубопроводов и печных змеевиков из теплоустойчивых хромомолибденовых сталей без термической обработки сварных соединений при изготовлении, монтаже и ремонте нефтеперерабатывающих и нефтехимических установок. 1981.
- Хромченко Ф.А. Ресурс сварных соединений паропроводов. М.: Машиностроение. 2002.
- СТО 1723082.27.100.005–2008. Основные элементы котлов, турбин и трубопроводов ТЭС. Контроль состояния металла. Нормы и требования. 2008.
- Коррозия и защита химической аппаратуры. Т. 9. Нефтеперерабатывающая и нефтехимическая промышленность/Под ред. А.М. Сухотина, А.В. Шрейдера, Ю.И. Арчакова. М.: Химия, 1974.
- Закс И.А. Сварка разнородных сталей. Л.: Машиностроение, 1973.