Автор: Е.И. Тескер (ООО «Агромаш»).
Опубликовано в журнале Химическая техника №8/2015
Современное машиностроение, обслуживающее нефтехимию и газовую отрасли, находится в сложных условиях, так как технический уровень и стоимостные показатели выпускаемого динамического оборудования, комплектующих и запасных частей не в полной мере отвечают требованиям к эффективности эксплуатации, надежности и безопасности.
Кроме того, замена базового сложного оборудования (например, насосно-компрессорного), выработавшего свой проектный ресурс, связана с большими затратами и не всегда приносит ожидаемый эффект, прежде всего по надежности и затратам на эксплуатацию.
Согласно экспертным оценкам, степень изношенности оборудования топливно-энергетического комплекса уже превышает 70%, а для восстановления его работоспособности требуется замена дорогостоящих базовых деталей и узлов (корпусные детали, роторы, штоки и т.п.).
В условиях дефицита, ограничения и сложности поставок оригинальных деталей и агрегатов рынок начинает заполняться некачественными изделиями низкого технического уровня, в том числе и иностранного производства. Заводы, поставляющие запасные части к оборудованию с большим сроком эксплуатации, работают по технической документации, существенно отличающейся от фирменной заводов-изготовителей, которые сами запасные части чаще всего не выпускают.
Требует совершенствования система входного контроля качества продукции для целей ремонта. Во многих случаях характеристики качества просто декларируются.
Следует отметить, что для реализации программ импортозамещения машиностроительной продукции необходимо освоить выпуск большого количества различных типов динамического оборудования высокого технического уровня.
Однако создание современных импортозамещающих производств не может произойти в достаточно жесткие сроки, так как для постановки на производство новых изделий требуется длительная подготовка производства, проведение определенного объема заводских и ведомственных испытаний, особенно для оборудования во взрывопожаробезопасном исполнении.
Таким образом, замена импортного оборудования отечественным с соответствующим техническим уровнем является сложной проблемой, которая не может быть решена в короткие сроки. В связи с этим большое значение приобретают разработки, направленные на увеличение срока службы оборудования, для чего необходимо совершенствование ремонтных производств и повышения качества отремонтированных изделий. Выполненные нами комплексные исследования и большой практический опыт позволяют утверждать, что это достигается применением новых ремонтных технологий, которые дают возможность значительно продлить жизненный цикл машинного оборудования, увеличить межремонтные пробеги, снизить затраты на эксплуатацию и поставку запасных частей, повысить эффективность и эксплуатационные показатели. Реализация этого направления позволяет получить необходимый запас времени для обновления основных фондов и освоения выпуска отечественного оборудования.
Анализ технического состояния различных типов динамического оборудования, используемого на предприятиях нефтехимии и газовой отрасли, свидетельствуют о том, что в большинстве случаев работоспособность лимитируется выходом из строя наиболее нагруженных быстроизнашивающихся деталей. Требуемая работоспособность этих деталей при изготовлении импортного оборудования чаще всего достигается высокой точностью сопряжений и необходимым качеством изготовления трущихся деталей.
В процессе эксплуатации под действием различных факторов происходит деградация свойств поверхностных слоев, значительное ухудшение физико-механических свойств и разрушение поверхностей (рис. 1). Как правило, эти процессы развиваются в сравнительно тонких поверхностных слоях металла (0,05…0,3 мм), что приводит к нарушению условий смазки, увеличению зазоров и выходу деталей из строя. В то же время нижележащие слои сохраняют необходимые свойства, что предотвращает развитие усталостных трещин по сечению детали и разрушение, которое чаще всего обусловлено предельным износом.
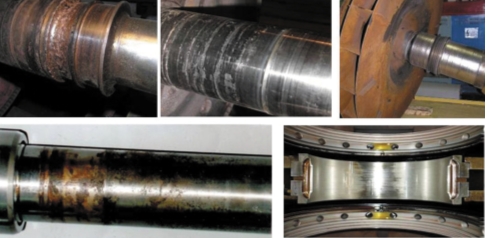
Процессы деградации свойств и изнашивания поверхностных слоев характеризуются динамикой изнашивания, которая отражает темп износа в зависимости от нагрузки и времени эксплуатации. Скорость протекания этих процессов определяет ресурс деталей. В связи с этим внедрение методов упрочнения и модификации поверхностей, обеспечивающих повышение несущей способности и сопротивляемости изнашиванию, является важнейшей задачей производителей оборудования и ремонтных производств.
Достижение высоких показателей оборудования в послеремонтный период осложняется тем, что отремонтированные детали, узлы и агрегаты работают по сравнению с новыми в более жестких условиях. Это объясняется высокой степенью изношенности оборудования, значительными отклонениями от номинальных конструктивных размеров и других характеристик деталей, что обусловлено длительной эксплуатацией, увеличением динамической нагруженности и другими факторами.
Из анализа условий эксплуатации и причин выхода из строя деталей следует, что для восстановления работоспособности изношенного оборудования и продления его срока службы необходимо значительно повысить сопротивляемость изнашиванию поверхностных слоев базовых деталей. Это можно сделать с помощью прогрессивных методов формирования этих слоев с заданными свойствами. Применение прогрессивных методов (упрочнение и модификация поверхности) особенно важно в условиях ремонта, так как простая замена изношенной детали новой не гарантирует требуемого уровня работоспособности. Следует отметить, что иностранные фирмы-производители редко применяют прогрессивные упрочняющие технологии, а требуемый уровень работоспособности в сравнительно небольшой гарантийный период достигается высокой точностью сопряжений и качеством отделочных операций.
В условиях ремонта и при изготовлении запасных частей невозможно выполнить требования конструкторской документации, которая на ремонтных предприятиях практически отсутствует или морально устарела, так как оборудование находится в эксплуатации длительное время.
Попытки повысить требования к поставке быстроизнашивающихся деталей насосно-компрессорного оборудования уже предпринимаются эксплуатирующими компаниями. Так, новые технические условия на поставку запасных частей и комплектующих разработаны ОАО «Лукойл». В этих технических условиях установлен гарантийный срок (не менее 3 лет) эксплуатации ответственных деталей и комплектующих до замены.
Многолетний опыт разработки и внедрения новых упрочняющих технологий свидетельствует о том, что перспективным направлением, обеспечивающим продление жизненного цикла и высокое качество ремонта, является разработка и применение новых прогрессивных импортозамещающих лазерных технологий и многофункциональных износостойких покрытий на рабочих поверхностях быстроизнашивающихся деталей. Это направление, развиваемое нами, успешно реализуется на крупных предприятиях ПАО «Газпром» и в нефтехимии.
Для реализации указанного направления нами разработан комплексный подход, сущность которого заключается в выполнении следующих этапов:
- анализ нагруженности, условий эксплуатации, разработка критериев оценки предельных состояний и причин выхода из строя базовых деталей, лимитирующих ресурс оборудования в целом;
- анализ качества аналогичных деталей фирменного изготовления;
- разработка научно-обоснованных требований к качеству рабочих поверхностей трущихся деталей, выбор упрочняющих обработок и характеристик качества упрочненных слоев, определяющих работоспособность и сопротивляемость изнашиванию;
- внедрение новых технологий с предварительным изготовлением опытных образцов и проведением комплексных исследований и испытаний.
Разработанный комплекс лазерных импортозамещающих технологий успешно применяется на различных предприятиях нефтехимии и газовой отрасти для полного восстановления работоспособности предельно изношенного насосно-компрессорного, теплоэнергетического и газотурбинного оборудования, чаще всего импортного производства.
Разработанные технологии ремонта вышедших из строя и подлежащих замене и деталей и узлов динамического оборудования позволяют:
- повысить в 1,5–2 раза срок службы машинного оборудования в послеремонтный период с обеспечением всех технических характеристик на уровне характеристик новых изделий фирменного изготовления;
- восстанавливать работоспособность сложных, не восстанавливаемых другими методами предельно изношенных деталей и узлов импортного оборудования с сохранением взаимозаменяемости комплектующих;
- сократить расходы на эксплуатацию и обслуживание, повысить эффективность эксплуатации;
- восстанавливать геометрические размеры и формировать высокие свойства корпусных деталей (насосов, турбин), в том числе и из чугуна.
Технологии аттестованы ПАО «Газпром» в соответствии с СТО ГАЗПРОМ 2-3,5-046–2006 и рекомендованы для применения при ремонте вышедших из строя деталей и узлов оборудования ЕСГ ПАО «Газпром».
Длительный опыт эксплуатации (более 20 лет) отремонтированных изделий с применением новых импортозамещающих технологий подтверждает высокую эффективность основанных на них технических решений. Согласно отзывам с мест эксплуатации, срок службы некоторых деталей и узлов увеличился в 5–10 раз по сравнению с продолжительностью работы новымх изделий.
В качестве примера приведем фотографии роторов газоперекачивающих агрегатов, отремонтированных совместно с ОАО «Газэнергосервис» с применением новых лазерных технологий (рис. 2). В настоящее время на дочерних предприятиях ПАО «Газпром» в эксплуатации находятся более 70 роторов газоперекачивающих агрегатов импортного производства, отремонтированных с применением новых технологий, что позволило получить большой экономический эффект за счет сокращения поставок по импорту.
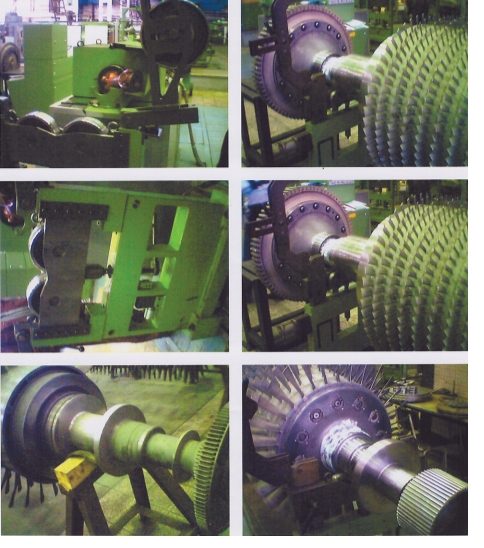
Кроме того, в эксплуатации находятся различные типы насосно-компрессорного и теплоэнергетического оборудования крупных предприятий нефтехимии (рис. 2), также отремонтированных с применением новых технологий.
Отзывы эксплуатирующих организаций и опыт эксплуатации отремонтированных деталей, узлов и агрегатов в послеремонтный период свидетельствуют о высокой технико-экономической эффективности применения новых технологий. При этом достигается полное импортозамещение за счет восстановления работоспособности оригинальных базовых деталей, узлов и агрегатов.
Внедрение технологий позволяет значительно увеличить жизненный цикл импортного оборудования с минимальными затратами и тем самым получить необходимый резерв времени для масштабной модернизации производств.
Следует также отметить, что опыт эксплуатации отремонтированного оборудования может быть использован разработчиками нового оборудования и его изготовителями для совершенствования конструкций и повышения качества продукции.