Автор: С.В. Панченко, В.А. Платонов, Ю.Н. Тюрин, М.С. Трещева, С.В. Дьяконов (ОАО «НОРЭ»).
Опубликовано в журнале Химическая техника №11/2014
На промышленных предприятиях используется большое количество стальных вертикальных резервуаров, предназначенных для хранения агрессивных химических веществ, используемых на различных стадиях производственного цикла. Такими веществами могут быть кислоты, щелочи, растворы азотных удобрений и карбамида, расплав серы и др. Изготовление таких резервуаров осуществляется по типовым или индивидуальным проектам.
Типовыми проектами предусмотрены резервуары двух типов вместимостью более 100 м3. Первый тип – корпус резервуара изготовлен из коррозионно-стойкой стали, выбранной в зависимости от свойств хранимой среды. Второй тип – корпус резервуара изготовлен из углеродистой или низколегированной стали и оснащен внутренней защитной футеровкой или антикоррозийным покрытием. Для хранения концентрированной серной кислоты и растворов щелочей применяют резервуары из углеродистой стали.
В зависимости от объема и назначения могут отличаться способы установки резервуара на фундаменте.
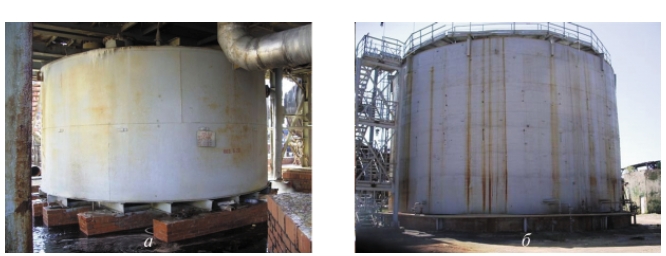
установлен на бетонном фундаменте, облицованном кислотостойким кирпичом (б)
Резервуары с плоским днищем зачастую устанавливаются на ленточном фундаменте и стальных прокатных балках. Резервуары с днищами, имеющими уклон, устанавливают на сплошном основании. (рис. 1 а, б).
Корпус резервуара также может иметь тепловую изоляцию. Требования к монтажу и приемке устанавливают в соответствии со СНиП 3.03.01–87 [1].
Перечень типовых проектов (ТП) резервуаров для агрессивных сред, диагностирование которых требует учета специальных требований:
ТП 705-5-41.89 – Резервуар стальной для агрессивных сред объемом 2000 м3 с плоским днищем;
ТП 705-5-40.89 – Резервуар стальной для агрессивных сред объемом 1000 м3 с плоским днищем;
ТП 705-5-39.89 – Резервуар стальной для агрессивных сред объемом 700 м3 с плоским днищем;
ТП 705-5-38.89 – Резервуар стальной для агрессивных сред объемом 400 м3 с плоским днищем;
ТП 705-5-44.89 – Резервуар стальной для агрессивных сред объемом 400 м3 с конусным днищем;
ТП 705-5-062 с.89* — Резервуар стальной вертикальный для агрессивных химических продуктов объемом 250 м3. Сейсмичность 7, 8, 9 баллов;
ТП 705-5-054 с.89* – Резервуар вертикальный для агрессивных химических продуктов объемом 3200 м3. Сейсмичность 7 баллов;
ТП 705-5-053 с.89* – Резервуар вертикальный для агрессивных химических продуктов объемом 2000 м3. Сейсмичность 7 баллов;
ТП 705-5-034 с.89* – Резервуар стальной вертикальный для агрессивных химических продуктов объемом 2000 м3. Сейсмичность 7, 8, 9 баллов;
ТП 705-5-033 с.89* – Резервуар стальной вертикальный для агрессивных химических продуктов объемом 1500 м3. Сейсмичность 7, 8, 9 баллов;
ТП 705-5-052 с.89* — Резервуар вертикальный для агрессивных химических продуктов объемом 1250 м3. Сейсмичность 7 баллов;
ТП 705-5-032 с.89* – Резервуар стальной вертикальный для агрессивных химических продуктов объемом 1000 м3. Сейсмичность 7, 8, 9 баллов;
ТП 705-5-051 с.89* – Резервуар вертикальный для агрессивных химических продуктов объемом 800 м3. Сейсмичность 7 баллов;
ТП 705-5-31.87 – Резервуар из нержавеющей стали для агрессивных химических продуктов объемом 1000 м3. Возможно применение в районах сейсмичностью 8 баллов;
ТП 705-5-30.87 – Резервуар из нержавеющей стали для агрессивных химических продуктов объемом 700 м3. Возможно применение в районах сейсмичностью 7 баллов;
ТП 705-5-061 с. 89* – Резервуар стальной вертикальный для агрессивных химических продуктов объемом 500 м3. Сейсмичность 7 баллов;
ТП 705-5-050 с.89* – Резервуар вертикальный для агрессивных химических продуктов объемом 500 м3. Сейсмичность 7 баллов;
ТП 705-5-29.87 – Резервуар из нержавеющей стали для агрессивных химических продуктов объемом 400 м3. Возможно применение в районах сейсмичностью 7 баллов.
ТП 705-5-049 с.89* – Резервуар вертикальный для агрессивных продуктов объемом 320 м3. Сейсмичность 7 баллов.
ТП 705-5-022.86 * — Резервуар стальной вертикальный для агрессивных химических продуктов объемом 320 м3, собираемый методом рулонирования;
ТП 705-5-28.87 – Резервуар из нержавеющей стали для агрессивных химических продуктов объеом 300м3. Возможно применение в районах сейсмичностью 8 баллов;
ТП 705-5-048 с. 89*– резервуар вертикальный для агрессивных химических продуктов объемом 200 м3. Сейсмичность 7 баллов;
ТП 705-5-021.86 – Резервуар стальной вертикальный для агрессивных химических продуктов объемом 200 м3, собираемый методом рулонирования;
ТП 705-5-27.87 – Резервуар из нержавеющей стали для агрессивных химических продуктов объемом 200 м3. Возможно применение в районах сейсмичностью 8 баллов;
ТП 705-5-047 с. 89* – Резервуар вертикальный для агрессивных химических продуктов объемом 152 м3. Сейсмичность 7 баллов;
ТП 705-5-26.87 – Резервуар из нержавеющей стали для агрессивных химических продуктов объемом 100 м3. Возможно применение в районах сейсмичностью 7 баллов;
ТП 705-5-020.86 – Резервуар стальной вертикальный для агрессивных химических продуктов объемом 100 м3, собираемый методом рулонирования.
Технические требования к отдельным видам резервуаров и емкостей (для кислот и щелочей) содержатся в ФНиП [2] и относятся, главным образом, к оборудованию резервуаров предохранительной и запорной арматурой и измерительными приборами. Кроме того, определены требования к установке резервуаров.
Основные требования ФНиП:
- на емкостном оборудовании для хранения жидких кислот или щелочей (резервуары, сборники объемом 1 м3 и более) трубопроводы нижнего слива должны быть оснащены двумя запорными устройствами, одно из которых подсоединяют непосредственно или в непосредственной близости к штуцеру сосуда;
- фланцевые соединения трубопроводов кислот и щелочей должны иметь защитные кожухи; конструкционные материалы арматуры подбирают из условия устойчивости к транспортируемой среде и обеспечения надежной эксплуатации арматуры в допустимом диапазоне параметров среды;
- емкостное оборудование для использования кислот и (или) щелочей объемом 1000 л и более должно быть оснащено поддонами, вместимость которых достаточна для содержания одного аппарата максимальной емкости в случае его аварийного разрушения. Высота защитного ограждения каждой группы резервуаров должна быть на 0,2 м выше уровня расчетного объема разлившейся жидкости;
- поддоны и площадки с бортами должны быть оснащены стационарными или передвижными устройствами для удаления аварийных проливов и их дальнейшей нейтрализации. Поддоны для открытых складов без сливов в специальную канализацию организации должны быть дополнительно защищены от атмосферных осадков;
- для складов хранения кислот и щелочей в резервуарах должна быть обеспечена возможность аварийного освобождения любого из резервуаров в другие резервуары склада, в специальные аварийные системы или в оборудование технологических установок, материал которого коррозионно стоек к эвакуируемому продукту;
- емкости для хранения кислот и щелочей должны быть оснащены средствами измерения, контроля и регулирования уровня этих жидкостей с сигнализацией предельных значений уровня и средствами автоматического отключения их подачи в емкости при достижении заданного предельного уровня или другими средствами, исключающими возможность перелива.
На сегодняшний день не существует единой нормативной методики, определяющей содержание и объем диагностирования резервуаров, предназначенных для хранения агрессивных химических веществ под наливом. В качестве базовой в большинстве случаев принимается методика, изложенная в Инструкции [3] разработанной ОАО «НИИХИМ-МАШ», ОАО «ГИАП», ОАО ЦНИИПСК им. Мельникова, НПК «ИЗОТЕРМИК».
Методика определяет перечень методов неразрушающего контроля, применяемых при диагностировании резервуаров, и объем контроля.
Состав работ по проведению обследования и диагностирования технического состояния:
- анализ проектно-технической документации, механической и температурной нагруженности;
- визуальный осмотр резервуара;
- геодезическую съемку стенки и днища;
- ультразвуковую толщинометрию стенки, днища и кровли резервуара;
- дефектоскопию сварных швов неразрушающими методами контроля;
- проведение металлографических исследований;
- определение механических свойств металла;
- проведение расчетов прочности, устойчивости и долговечности стальных конструкций;
- расчет остаточного ресурса работоспособности.
Дополнительные виды контроля и испытаний могут быть назначены, исходя из особенностей хранимой среды и ее коррозионного воздействия на материал, истории эксплуатации резервуара, объемов и способов ранее проведенных ремонтов и т.п.
Далее приведены особенности обследования, характерные для ряда ранее проведенных работ по диагностированию технического состояния резервуаров.
Диагностированию подвергают резервуары, выработавшие нормативный срок. Значительная часть резервуаров находится в эксплуатации 20–40 лет и более. Частой проблемой диагностирования оказывается то, что комплект проектной, монтажной и эксплуатационной документации бывает неполным. В некоторых случаях отсутствуют даже ссылки на проект резервуара.
В этом случае на первом этапе оценивают соответствие резервуара типовому проекту и наличие возможных отступлений в части конструктивного оформления. В частности, оценивают соответствие материала несущих конструкций климатическим условиям места расположения резервуара (в соответствии с ГОСТP 52630–2012 [4] и СНиП 23-01–99 [5]), а также коррозионным свойствам хранимой среды (при ремонте владельцы резервуаров могут использовать материалы, не соответствующие проекту). Для определения и/или подтверждения марки материала элементов резервуара может быть проведен анализ химического состава материала.
Как положительный пример замены материала можно привести распространенную практику замены кровли футерованного кислотного резервуара. По проекту, кровля резервуара изготавливается из углеродистой (низколегированной) стали и не подлежит оборудованию защитным покрытием. При эксплуатации под действием паров и случайных проливов кислот происходит интенсивное коррозионное изнашивание настила кровли. В ряде случаев владельцы резервуаров серной и фосфорной кислот заменяют материал настила кровли коррозионно-стойкой сталью. Такая замена позволяет заметно увеличить срок службы настила кровли и сократить затраты на ремонт.
С другой стороны, проектное материальное исполнение резервуара не всегда обеспечивает достаточную его долговечность. Как частный пример: при эксплуатации сернокислотных резервуаров наблюдается колебание концентрации хранимого продукта. Снижение концентрации серной кислоты может существенно увеличивать скорость коррозии стенки резервуара, изготовленного из углеродистой стали и приводить к выходу из строя оболочки резервуара задолго до окончания планируемого срока эксплуатации.
Следующим шагом диагностирования бывает оценка соответствия оборудования резервуара нормативным требованиям и свойствам хранимой среды. В настоящее время основным документом, определяющим требования к оборудованию резервуара, являются ФНиП [2].
Оснащение резервуаров, пущенных в эксплуатацию десятилетия назад, может не соответствовать действующим нормам.
Еще одной значимой проблемой, с которой можно столкнуться при диагностировании резервуара, является состояние основания. Напряженное состояние металлоконструкций корпуса напрямую зависит от положения и состояния фундамента.
Крен фундамента или деформация окрайков днища, вызванная неравномерной осадкой, могут привести к аварийному разрушению резервуара или систематическому появлению дефектов на перегруженных участках.
В большинстве случаев резервуары находятся на территории действующих промышленных предприятий.
Из-за большой агрессивности обращающихся сред при наличии проливов и затопления основания фундаменты резервуаров могут подвергаться интенсивному повреждению.
При выявлении отклонения положения резервуара в пространстве от проектного для оценки объема ремонта и прогнозирования возможности дальнейшей эксплуатации необходимо иметь точную информацию о состоянии грунтов и скрытой части фундамента. Сбор информации о состоянии грунтов и скрытых конструкций требует проведения дополнительных исследований и может существенно увеличивать стоимость диагностики.
Еще одна распространенная проблема, выявляемая при диагностировании, связана с взаимодействием оболочки резервуара и подводящих трубопроводов. При неправильном исполнении трубопроводных линий из-за тепловой деформации примыкающих трубопроводов узел вварки патрубков оказывается нагружен дополнительным моментом или осевой силой. Похожий эффект могут оказывать деформации фундаментов резервуара или опор трубопроводов, вызванные промерзанием грунта или подтоплением. При этом напряжения в сварном узле могут превышать расчетные. При достаточной пластичности материала оболочки происходит деформация стенки резервуара. При исчерпании пластичности материала могут возникать трещины в сварных швах вварки патрубков и в основном металле.
Специфика коррозионного изнашивания материалов оболочки и вспомогательных конструкций резервуара определяется материальным исполнением элементов резервуара и свойствами хранимой среды. Хранение кислот (азотной, щавелевой, уксусной, разбавленной серной, ортофосфорной и др.), растворов минеральных удобрений, карбамида, органических веществ часто осуществляется в резервуарах, оболочка которых изготовлена из коррозионно-стойкой стали. При этом на первый план выходят повреждения от локальной коррозии – межкристаллитной, питтинговой, коррозионного растрескивания под напряжением.
Эти виды коррозии представляют большую опасность тем, что при внешне малозаметном повреждении металла приводят к опасным дефектам микроструктуры материала.
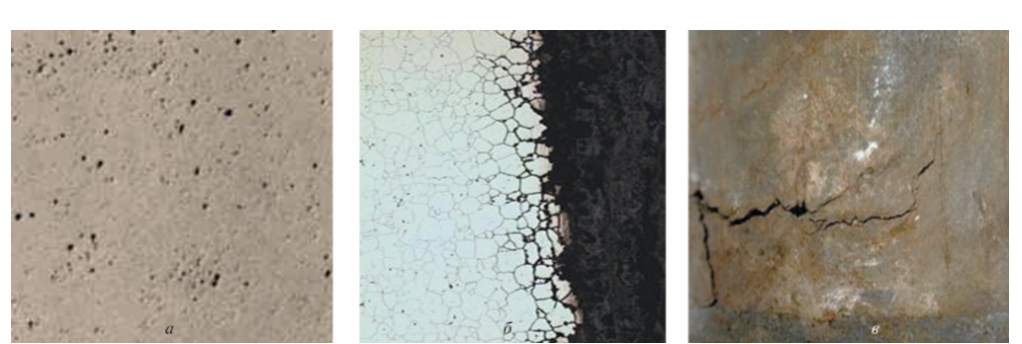
а – питтинговая коррозия; б – межкристаллитная коррозия; в – коррозионное растрескивание металла
Питтинги представляют собой точечные повреждения, проникающие на большую глубину, с образованием сквозных дефектов (рис 2, а).
Этот вид коррозии развивается в среде, содержащей ионы – активаторы питтинговой коррозии (хлориды, сульфаты) и более всего характерен для кислотных резервуаров из коррозионно-стойких сталей.
Межкристаллитная коррозия реализуется, главным образом, в зоне термического влияния сварных швов и приводит к разупрочнению материала за счет локальной коррозии по границам зерен. На рис. 2, б представлена микроструктура металла, поврежденного межкристаллитной коррозией. Межкристаллитная коррозия также характерна для кислотных резервуаров. Наличие межкристаллитной коррозии в металле при визуальном осмотре и цветной дефектоскопии можно заподозрить по наличию сетки разнонаправленных поверхностных трещин со стороны контакта с продуктом, либо по губчатой поверхности околошовной зоны.
Коррозионное растрескивание характерно как для аустенитных, так и для перлитных сталей. Под действием агрессивной среды происходит снижение вязкости стали, что в конечном итоге приводит к растрескиванию металла. Коррозионные трещины, обычно разветвленные, проходят по границам зерен.Характер излома всегда хрупкий.
В отличие от межкристаллитной коррозии в случае растрескивания под напряжением коррозионные трещины преимущественно распространяются в направлении, нормальном к вектору растягивающего напряжения. Такой вид коррозии характерен для щелочных резервуаров.
Атмосферная коррозия оболочек резервуаров из углеродистых сталей происходит под воздействием водяных паров и растворенных в воздухе промышленной зоны коррозионно-активных веществ, а также атмосферных осадков. Если температура хранимого продукта оказывается ниже температуры точки росы для окружающего воздуха, возможно также выпадение конденсата на наружной поверхности металла.
Атмосферная коррозия приводит к уменьшению толщины стенки, в некоторых случаях – до критического значения. Наблюдались случаи интенсивной наружной коррозии стенки резервуара в зоне, примыкающей к уторному узлу. На высоте до 100…150 мм от днища глубина коррозионных повреждений превышала среднюю по резервуару в 5 раз.
Для резервуаров с концентрированной серной кислотой характерен износ в зоне изменения уровня продукта. Через неплотности в кровле или через воздушную линию внутрь резервуара проникает атмосферный воздух, содержащий пары воды.
Концентрированная серная кислота способна поглощать влагу из воздуха, что приводит к снижению ее концентрации в верхних слоях и усилению коррозионной способности среды. В случае наличия сквозных дефектов в кровле, через которые внутрь резервуара могут проникать осадки, в местах стекания атмосферных осадков скорость коррозии стенки резервуара может возрастать на порядок.
Для резервуаров из углеродистых и низколегированных сталей характерно сочетание сплошной и язвенной коррозии как атмосферной, так и развивающейся под действием продукта и его паров. В ряде случаев коррозионные язвы имеют большую глубину и малую площадь, создавая локальные концентраторы напряжений. При малой площади язвенных повреждений обычно рекомендуется механическое шлифование на глубину язвенной коррозии, которое позволяет сгладить пик напряжений в зоне язвы. Расчетом на прочность должно быть подтверждено, что остаточная толщина стенки в месте шлифовки достаточна для выполнения условия прочности. Обычным требованием является то, что остаточная толщина стенки в месте шлифовки не должна быть менее расчетной, определенной в соответствии с нормативным методом. Более точные результаты можно получить при расчете методом конечно-элементного анализа.
Вообще, нормативные методы расчета позволяют рассчитывать только те конструкции, отклонения формы которых находятся в пределах, установленных нормами проектирования и изготовления. Аналитическими методами рассчитать влияние на прочность отклонений формы, в том числе коррозионных дефектов, превышающих допустимые значения, зачастую не представляется возможным. Более точным является расчет методом конечных элементов с моделированием выявленных дефектов, отклонений формы и не учтенных при проектировании нагрузок. При этом следует также учитывать возможное снижение механических свойств материала, происходящее в процессе эксплуатации.
Снижение свойств возможно как под действием коррозионного воздействия среды, так и за счет эксплуатационного старения углеродистой стали.
В большинстве случаев снижение механических свойств сопровождается изменениями микроструктуры материала, поэтому обязательным этапом исследований металла бывает полевая металлография, позволяющая оценить состояние микроструктуры без вырезки образцов.
Если при проведении металлографических исследований будут выявлены признаки ухудшения микроструктуры, то проводят испытания образцов материала на прочность.
При испытаниях определяют пределы прочности и текучести, относительное удлинение или сужение, ударную вязкость. Для оценки склонности стали к хрупкому разрушению испытания на ударный изгиб проводятся при различной температуре.
Проведение испытаний позволяет сопоставить фактическую прочность материала с требованиями стандартов и при необходимости внести поправки в стандартные значения расчетного сопротивления материала.
На ресурс эксплуатации резервуара большое влияние оказывают нагрузки от изменения уровня хранимого продукта. Изменение напряжений в некоторых узлах конструкции могут достигать значений, при которых следует учитывать влияние на прочность малоцикловой усталости материала. Наиболее подвержены малоцикловой усталости, как правило, узлы вварки патрубков в нижней части стенки. Поскольку сведения об изменениях уровня продукта за весь период эксплуатации обычно бывают неполными, адекватный расчет остаточного ресурса малоцикловой прочности едва ли возможен. Неразрушающий контроль сварных швов узлов вварки патрубков следует выполнять максимально подробно. Если существует вероятность исчерпания ресурса малоцикловой прочности какоголибо узла резервуара, то следует рекомендовать заказчику проведение регулярного контроля этого узла неразрушающими методами.
Если по результатам геодезических измерений было выявлено отклонение формы или положения резервуара от проектного, то следует оценить, в каких узлах резервуара напряжения могут превысить номинальные. Сварные швы перегруженных зон должны быть проконтролированы неразрушающими методами по всей длине. Расчет на прочность следует проводить с учетом фактических напряжений.
При обнаружении дефектов в виде трещин в сварных швах резервуара необходимо провести расчет на трещиностойкость с учетом фактически действующих напряжений для оценки опасности хрупкого разрушения конструкции резервуара.
Основные факторы, определяющие опасность хрупкого разрушения, – низкая температура металла при эксплуатации, наличие дефектов сварных швов корпуса (непроваров, несплавлений, подрезов, трещин и т.д.), циклический характер нагрузки, качество использованной для изготовления оболочки резервуара стали (хладноломкость), габаритные размеры резервуара, характер коррозионного воздействия среды.
Наличие коррозионных повреждений в зоне концентрации напряжений также повышает опасность возникновения хрупкой трещины и является основанием для проведения оценки склонности стали к хрупкому разрушению.
Из-за большого разнообразия конструктивного и материального исполнений резервуаров и условий их эксплуатации достаточно сложно предложить единый алгоритм проведения диагностирования. При проведении работ следует учитывать положения различных документов, предусматривающих необходимый объем работ.
В части проведения измерений отклонений геометрической формы и положения в пространстве рекомендуется использование положенийСНиП 3.03.01–87 [1] и СА 03-008–08 [6], объем работ по оценке коррозионного состояния можно принимать по «Инструкции по проведению обследования и диагностирования технического состояния сернокислотных резервуаров» с оценкой результатов измерений толщины стенки в соответствии с «Методикой прогнозирования остаточного ресурса безопасной эксплуатации сосудов и аппаратов по изменению параметров технического состояния», объем и содержание исследований металла – по РД 03-421–01 [7]. Объем неразрушающего контроля сварных швов в каждом случае назначается индивидуально, в зависимости от общего технического состояния и выявленных в процессе контроля повреждений и дефектов, но в любом случае не должен быть менее установленного СНиП 3.03.01–87 [1].
Поверочный расчет резервуара должен учитывать все выявленные дефекты и повреждения. В том случае, если величина дефектов и отклонений формы не превышает установленные СНиП 3.03.01–87 [1], коррозионный износ находится в пределах проектной прибавки на компенсацию коррозии, а механические свойства материала соответствуют требованиям стандартов, то возможно проведение расчета в соответствии с методикой СА 03-008–08 [6].
При этом класс опасности резервуаров, содержащих токсичные, горючие и агрессивные вещества прини мается не ниже 1, расчетное сопротивление по пределу текучести принимается по ГОСТ Р 52857.1 [8] илиСНиП II-23–81 [9].
При проведении расчетов следует учитывать снижение прочностных свойств материала. При этом максимальное эквивалентное напряжение не должно превышать предела текучести с учетом коэффициентов надежности и условий работы.
Оценку склонности стали к охрупчиванию следует выполнять на основе серии испытаний на ударный изгиб при различной температуре.
Если наименьшая возможная температура эксплуатации металла несущих конструкций резервуара оказывается ниже первой критической температуры хрупкости, то следует выполнить проверку условия
где σm – теоретические напряжения от фактической нагрузки, установленной в процессе обследования;Ru – расчетное сопротивление стали растяжению по временному сопротивлению; γu – коэффициент надежности для элементов конструкций, рассчитываемых на прочность по временному сопротивлению, равный 1,3; β – коэффициент уменьшения расчетного сопротивления при снижении эксплуатационной температуры ниже первой критической температуры, определяемый в соответствии с табл. 84 СНиП II-23–81 [9].
В случае наличия отклонений формы (вмятин, смещения и увода кромок, некруглости стенки, деформации окрайков днища и т.п.) и положения (крен фундамента), коррозионных дефектов типа язвенной коррозии свыше максимально допустимых размеров, дефектов формы сварных швов рекомендуется проведение расчета методом конечных элементов с использованием специального программного обеспечения.
Список литературы
- СНиП 3.03.01–87. Несущие и ограждающие конструкции.
- ФНиП. Правила безопасности химически опасных производственных объектов.
- Инструкции по проведению обследования и диагностирования технического состояния сернокислотных резервуаров.
- ГОСТ Р 52630–2012. Сосуды стальные сварные. Общие технические условия.
- СНиП 23-01–99. Строительная климатология.
- СА 03-008–08. Резервуары вертикальные стальные сварные для нефти и нефтепродуктов. Техническое диагностирование и анализ безопасности.
- РД 03-421–01. Методические указания по проведению диагностирования технического состояния и определению остаточного ресурса срока службы сосудов и аппаратов.
- ГОСТ Р 52857.1. Сосуды и аппараты.Нормы и методы расчета на прочность.Общие требования.
- СНиП II-23–81. Стальные конструкции.