Авторы: В.В. Антонова, Д.Е. Васильев, Ю.П. Афромеев, С.Л. Масякин, А.В. Жулин (ПАО «НОРЭ).
Опубликовано в журнале Химическая техника №1/2016
Один из методов неразрушающего контроля – визуальный – основан на получении первичной информации о контролируемом объекте при визуальном наблюдении или с помощью оптических приборов и средств измерений. Измерительный контроль – важная составляющая визуально-измерительного контроля (ВИК), который проводится в соответствии со строгими правилами контроля и требованиями нормативных документов, регулирующих его качество. Он заключается в присваивании дефекту категории или типа по одной из характеристик в виде конкретной физической величины, полученной путем практического измерения. Измерительные средства и их метрологические показатели указываются в нормативных документах. ВИК является первым этапом при проведении технического диагностирования трубопроводов, позволяющим получить до 50% общего объема необходимой информации об объекте. Положительное заключение по результатам ВИК дает основание продолжать диагностирование с использованием других неразрушающих и разрушающих методов контроля (в зависимости от особенностей подлежащего диагностике трубопровода), отрицательные результаты оформляются в виде дефектного акта, на основании которого выявленные дефекты должны быть устранены. Это дает возможность после проведения повторного ВИК продолжить обследование трубопровода.
Как правило, при диагностировании трубопроводов химической промышленности, специалисты ПАО «НОРЭ» визуальному и измерительному контролю подвергают:
1. Опорно-подвесную систему;
2. Изоляцию трубопроводов (при ее наличии);
3. Размещение трубопровода и его элементов;
4. Устройства для дренажа и продувки;
5. Сварные швы;
6. Конструкционные особенности элементов трубопровода;
7. Наружную поверхность элементов трубопровода на наличие трещин, выпучин, вмятин и других механических повреждений, коррозионных повреждений, расслоений металла;
8. Внутреннюю поверхность обследованных участков трубопровода на наличие поверхностных трещин, коррозионных повреждений и расслоений металла, механических повреждений;
9. Фланцевые соединения и их крепеж;
10. Трубопроводную арматуру;
11. Другие узлы трубопровода.
Перечисленное – это основные направления, где на практике специалистами ПАО «НОРЭ» были выявлены различного рода дефекты при визуально-измерительном контроле трубопроводов.
Анализ выявленных дефектов дает возможность установить частоту встречаемости (рис. 1) каждого из них согласно указанной классификации, пп.1…11 (диаграмма составлена по данным выборки дефектных актов, выданных заказчикам).
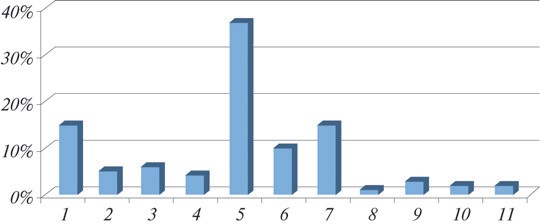
Как видно, частота встречаемости дефектов сварных швов (п. 5) при визуальном и измерительном контроле трубопроводов заметно больше, чем других дефектов, и составляет ~37% общего числа.
Это свидетельствует о необходимости уделять повышенное внимание именно контролю сварных соединений трубопроводов, что дает возможность не только получить информацию о внешнем состоянии шва, но и теоретически оценить внутреннее его состояние и рекомендовать проведение более точной проверки посредством других методов НК (РК, УЗК, ЦД, МПД и др.) в зависимости от особенностей конструкции и условий эксплуатации трубопровода.
Визуальному осмотру и измерениям подлежат все сварные соединения в целях выявления следующих дефектов:
- трещин всех видов и направлений;
- свищей и пористости наружной поверхности шва;
- подрезов;
- наплывов, прожогов, незаваренных кратеров;
- отклонений геометрических размеров и взаимного расположения свариваемых элементов;
- смещений и совместного увода кромок свариваемых элементов свыше предусмотренных нормами;
- несоответствий формы и размеров шва требованиям технологической документации;
- дефектов на поверхности основного металла и сварных соединений (вмятины, расслоения, раковины, непровары, поры, включения) [1].
Как видно из сказанного, дефекты сварных швов довольно разнообразны, поэтому главной задачей специалиста, проводящего обследование, является правильная идентификация найденного дефекта и оценка степени его опасности для дальнейшей эксплуатации трубопровода.
По результатам обследований трубопроводов, проводимых специалистами ОАО «НОРЭ», наиболее частыми дефектами сварных соединений при ВИК являются неполномерность шва, неравномерная его ширина и высота. Нарушение формы и размеров шва зачастую свидетельствует о наличии таких дефектов, как наплывы (натеки), подрезы, прожоги и незаваренные кратеры [2].
К внешним дефектам также можно отнести углубление (западание) между валиками шва, неправильный профиль и превышение усилия сварного шва, брызги металла на поверхности сваренных элементов трубопровода.
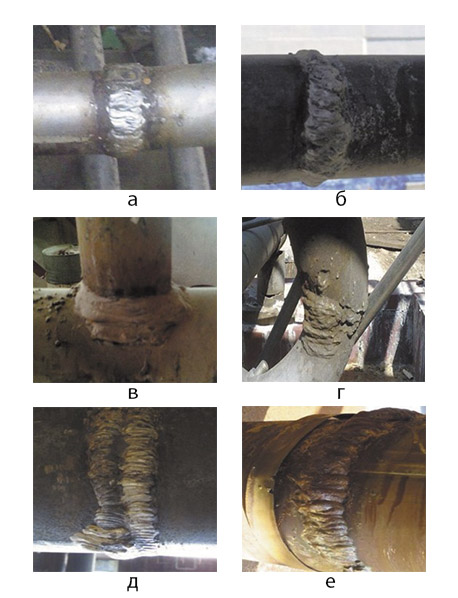
а; б – неравномерная ширина и неправильный профиль, наплывы; в, г – наплывы (натеки), превышение усиления и асимметрия углового сварного шва, брызги металла; д, е – неполномерность и чешуйчатость сварного шва, углубление (западание) между валиками шва, наплывы
На рис. 2 показаны наиболее частые дефекты сварных швов, выявленных при проведении диагностирования специалистами ОАО «НОРЭ».
К дефектам макроструктуры шва трубопровода, выявляемым при увеличении не более чем в 10 раз, относятся газовые поры, шлаковые включения, непровары, трещины [2].
Специалистам, обладающим достаточной квалификацией и имеющим в своем арсенале современное оборудование, отвечающее необходимым требованиям для проведения визуального и измерительного контроля трубопроводов, не составит труда выявить дефекты данной группы.
Как правило, трещины в сварных швах подразделяют на продольные, поперечные, кратерные, радиальные, разветвленные. Выявленные на практике разрывы металла в сварном шве и (или) прилегающих к нему зонах сварного соединения и основного металла трубопроводов показаны на рис. 3.

прилегающих к нему зонах сварного соединения
и основного металла трубопроводов:
а – продольная; б – поперечная;
в – разветвленная + кратерная
Такой дефект сварного шва, как включение (обобщенное наименование пор, шлаковых и вольфрамовых включений), представляет собой полость в металле, заполненную газом, шлаком или инородным металлом (рис. 4).
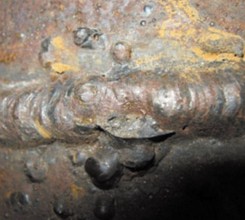
Непровар как один из дефектов макроструктуры представляет собой несплавления в сварном соединении вследствие неполного расплавления кромок основного металла или поверхностей ранее выполненных валиков сварного шва (рис. 5).
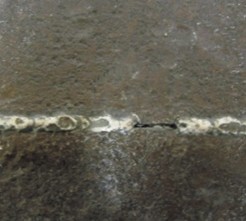
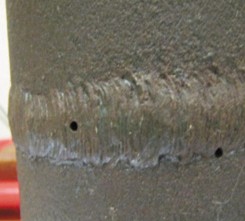
Как показывает практика диагностирования трубопроводов, такие дефекты, как свищи в сварных соединениях, широко распространены на трубопроводах, транспортирующих агрессивные среды, с выходом последних на наружную поверхность элементов объекта обследования (рис. 6, 7).
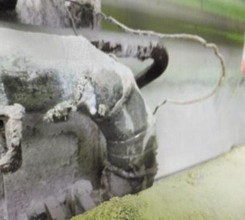
Определенные требования выдвигаются и при сваривании различных элементов трубопроводов, при этом не допускаются:
- отклонения геометрических размеров и взаимного расположения свариваемых элементов;
- смещение и совместный увод кромок свариваемых элементов свыше предусмотренных нормами [1].
Примером могут служить выявленные в цехах производства азотной кислоты дефекты такого вида (рис. 8).
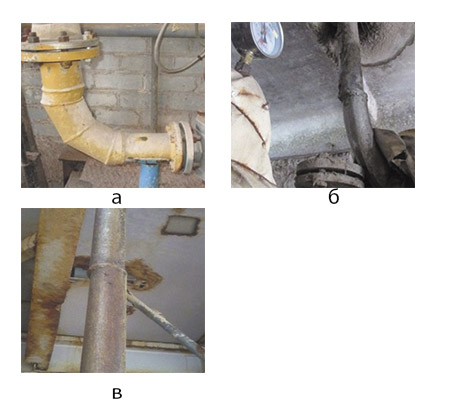
Подробно рассмотрев возможные дефекты сварных швов, выявляемые при визуально-измерительном контроле, можно заключить, что работоспособность сварных конструкций (в частности, трубопроводов) во многом определяется качеством сварных швов, которое напрямую зависит от соблюдения технологии сварки, а также от квалификации сварщика и качества применяемых сварочных материалов.
Так как вопросы надежности работы трубопроводов в настоящее время приобретают все большее значение из-за их эксплуатации при высоких и низких температурах, в агрессивных средах, при больших рабочих напряжениях и пр., качество проведения визуально-измерительного контроля при диагностике последних выходит на первый план, что дает возможность специалистам, проводящим обследование, на начальном этапе выявить дефекты, препятствующие эксплуатации, и дать рекомендации по их устранению. В свою очередь, владелец подлежащего диагностике трубопровода также должен выполнять ряд условий: для полного и своевременного проведения контроля трубопровод должен быть выведен из эксплуатации (при необходимости), а для получения наиболее достоверной информации об объекте заказчик обязан обеспечить специалистам прямой доступ к нему (снятие изоляции в необходимом объеме, использование вышек для контроля на эстакадах и т.д.). Таким образом, можно сделать вывод, что качество и достоверность полученных результатов при визуально-измерительном контроле трубопроводов обеспечивается не только высокой квалификацией специалиста ВИК, но и совокупностью выполнения всех указанных условий и мероприятий по подготовке трубопровода к техническому диагностированию.
Список литературы
- Федеральные нормы и правила в области промышленной безопасности «Правила промышленной безопасности опасных производственных объектов, на которых используется оборудование, работающее под избыточным давлением» (ФНиП ОРПД).
- Щебеко Л.П., Яковлев А.П. Контроль качества сварных соединений. М.: 1972.