Автор: Ю.Н. Тюрин, Д.Е. Васильев, В.Д. Чугаев, С.Л. Масякин (ОАО «НОРЭ»).
Опубликовано в журнале Химическая техника №3/2015
Основными несущими элементами мостовых кранов являются главные и концевые балки, которые и составляют мост крана. При оценке состояния металлоконструкций необходимо обратить внимание на наличие дефектов, представляющих явную опасность и могущих привести к хрупкому разрушению. К таким дефектам относятся трещины в основном металле, в сварных швах и околошовной зоне. Опасность трещин заключается в непредсказуемости их развития и вытекающих последствий. По этой причине «Правила безопасности опасных производственных объектов, на которых используются подъемные сооружения» запрещают эксплуатацию грузоподъемных машин до проведения ремонта при выявлении трещин любого размера в ответственных металлоконструкциях [1].
Основным способом выявления трещин является осмотр элементов и узлов металлоконструкций. Места возможного наличия трещин должны быть очищены от пыли, грязи, смазочного материала и при необходимости зачищены до металлического блеска [2, 3]. Признаками наличия трещин являются подтеки ржавчины, выходящие на поверхность металла, и шелушение краски. Трещины могут возникнуть по концам сварных швов или по самим швам, имеющим технологические дефекты (непровары, поры, прожоги, подрезы, шлаковые включения и др.), поэтому следует внимательно проверять состояние сварных швов.
При удовлетворительном состоянии лакокрасочного покрытия металлоконструкции и нормальном освещении образовавшиеся трещины хорошо видны невооруженным глазом. В темных местах следует применять фонарь или переносную лампу. Образовавшиеся очаги коррозии необходимо удалить при помощи абразивного круга или механической проволочной щетки, после чего имеющиеся трещины также будут хорошо видны. Аналогичным образом следует обработать вызывающие сомнение сварные швы.
Хороший результат в обнаружении трещин показывают методы цветной и магнитопорошковой дефектоскопии (рис. 1, 2).
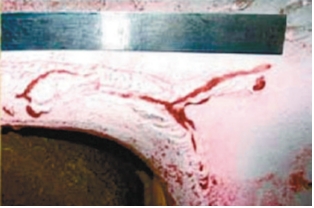
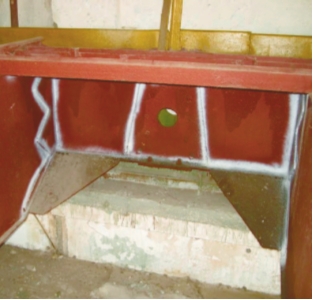
Следует отметить, что трещины возникают не бессистемно, а в конкретных узлах металлоконструкций, где условия нагружения провоцируют их возникновение. При проведении экспертизы промышленной безопасности мостовых кранов выявляются дефекты в виде трещин в следующих узлах [2, 3]:
- в узлах крепления букс ходовых колес моста (рис. 1, 3);
- в узле сопряжения главной балки с концевой (рис. 4);
- в главных балках – в верхнем поясе в районе устройства стыков тележечного рельса (рис. 5);
- в районе, где скачкообразно меняется профиль поперечного сечения – в нижнем поясе при переходе от наклонной части элемента к горизонтальной (в месте соединения стенки конструкции с нижним поясом);
- на вертикальной стенке – в местах, где привариваются крепежные кронштейны, поддерживающие рабочие площадки кранов (особенно в зоне приварки кронштейнов крепления механизмов передвижения моста к основному металлу вертикальной стенки как главной, так и концевых балок). Одна из причин их возникновения – возрастающие динамические нагрузки на сварные швы и зоны термовлияния в результате неудовлетворительного технического состояния механизма привода моста;
- в узле крепления перил к торцовому листу концевой балки;
- в узле крепления кабины крановщика – трещины появляются в полках уголков и косынок элементов крепления кабины машиниста к мосту крана.

Наиболее напряженной частью металлоконструкций крана является узел крепления угловых букс ходовых колес на концевых балках, который воспринимает вертикальные нагрузки и поперечные горизонтальные усилия, возникающие при движении крана (рис. 6). Горизонтальные усилия концентрируются в буксовых частях концевых балок в виде крутящего момента, равного произведению боковой силы на радиус колеса и силы, обусловленной перекосом. Сила перекоса, а, следовательно, и крутящий момент в процессе движения крана меняются, поэтому воздействие поперечных сил приводит к появлению в узле знакопеременных напряжений, частота которых зависит от числа включений механизма передвижения крана [2, 3].
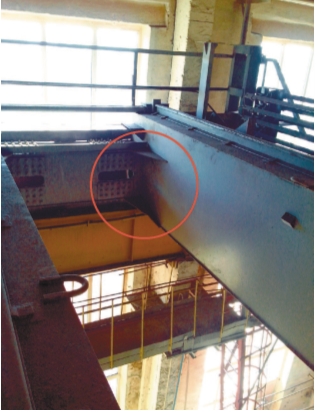
При проведении экспертизы промышленной безопасности мостовых кранов в узлах крепления угловых букс на концевых балках периодически выявляются дефекты в виде трещин. Образование трещин, в зависимости от модификации конструкции, строго локализовано определенными участками. На рис. 6 обозначены основные участки появления трещин концевых балок различных модификаций:
- первый участок – сварной шов соединения вертикальной стенки с нижним поясом в зоне изменения высоты поперечного сечения балки. Трещины 1 (см. рис. 6) возникают в криволинейной части перехода от меньшего сечения к большему. Очень часто трещины от сварного шва распространяются на основной металл;
- второй участок – углы вырезов.
В вертикальных стенках это вырезы под болтовые соединения букс.
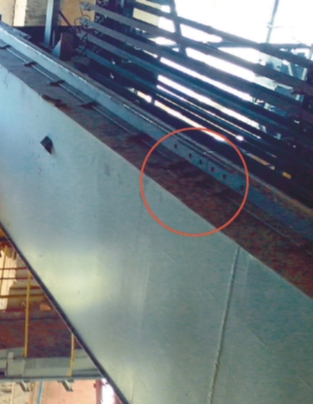
Трещины 2 формируются в углах вырезов, поражая затем основной металл стенки. В углах вырезов нижнего пояса и торцового листа балки также возникают трещины;
- третий участок – ребра жесткости, подкрепляющие стенку. Трещины 3 образуются в местах приварки кромки ребра к поясу;
- четвертый участок – трещины 4 в основном металле вертикальной стенки. Трещины возникают в стенке на расстоянии 100…150 мм от нижнего пояса в местах установки диафрагм.
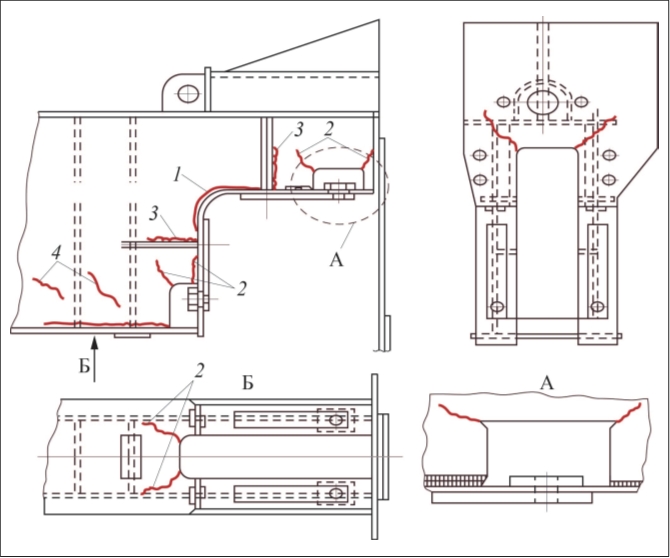
Таким образом, безопасность эксплуатации грузоподъемных кранов, отработавших нормативный срок службы, определяется уровнем экспертизы промышленной безопасности или технического диагностирования, а также качеством последующего проведенного ремонта, так как только они позволяют своевременно выявить и устранить дефекты металлоконструкций в текущий момент времени.
Список литературы
- Федеральные нормы и правила в области промышленной безопасности «Правила безопасности опасных производственных объектов, на которых используются подъемные сооружения», утвержденные приказом Федеральной службы по экологическому, технологическому и атомному надзору №533 от 12.11.2013 г.
- РД 10-112-5–97. Методические указания по обследованию грузоподъемных машин с истекшим сроком службы. Ч. 5. Краны мостовые и козловые.
- РД 10-112-6-03. Методические указания по обследованию специальных металлургических кранов.