Автор: М.В. Давыдкин (ОАО «ИркутскНИИхиммаш»), О.В. Немыкина (Иркутский государственный технический университет, Россия).
Опубликовано в журнале Химическая техника №3/2015
Для изготовления деталей запорной арматуры, подвергающихся сильному изнашиванию (штоки, седла и др.), стандарты ЦКБА рекомендуют использовать наплавки различного рода [1]. Для достижения требуемой износостойкости необходимо упрочение поверхности до твердости более 40 HRC. В работе [2] проводились испытания по оценке возможности использования стали 20Х13 твердостью 48 HRC для изготовления патрубков клапанов, производимых ОАО «ИркутскНИИхиммаш» (рис. 1). Для достижения соответствующей твердости проводили объемную термообработку патрубка с последующим отпуском резьбового конца.
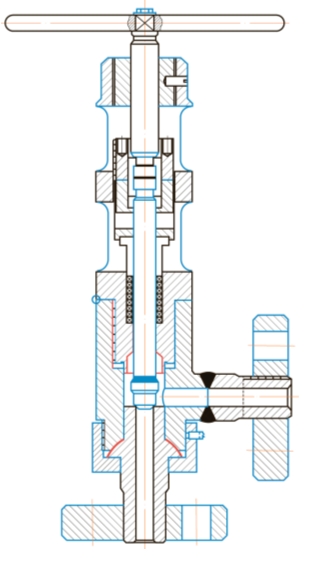
а – общий вид; б – патрубок клапана
Альтернативой объемной термообработке детали из стали 20Х13 до твердости 48 HRC может стать поверхностное упрочнение с помощью наплавки. С учетом типоразмеров патрубка для данной цели подходит проволока диаметром 1…1,2 мм.
В качестве проволоки, соответствующей данному требованию, использовали порошковую проволоку EnDotec DO*04. Данная проволока не включена в стандарты ЦКБА, регламентирующие применение наплавок в арматуростроении, но ее использование не запрещено [1]. При этом необходимо учитывать негативное влияние высокой температуры при сварке и возможную склонность к межкристаллитной коррозии (МКК) зоны термического влияния и зоны контакта основной металл–наплавка. В связи с этим для снятия напряжений, возникающих при наплавке, необходимо делать высокий отпуск. По рекомендации изготовителей проволоки EnDotec можно сделать отжиг, однако механические свойства стали 20Х13 станут неприемлемыми.
Таким образом, при решении вопроса по упрочению поверхности патрубка и увеличению его износостойкости возникают следующие проблемы: состав наплавки не соответствует СТ ЦКБА 053–2008, состояние зоны термического влияния (ЗТВ) и зоны сплавления неизвестны, неизвестно также влияние отпуска на изменение твердости наплавки EnDotec.
Образцы для испытаний
Образцы изготовляли в виде пластины из цилиндрической заготовки стали 20Х13 в исходном отожженном состоянии с наплавкой из En- Dotec DO*04, состав которой представлен в табл. 1
Таблица 1
Состав наплавки EnDotec DO*04
Элемент | C | Cr | Mn | Co | Mo | S | Si | P |
Содержание, % | 0,126 | 12,55 | 0,17 | 13,33 | 2,74 | 0,01 | 0,31 | 0,02 |
В заготовке фрезеровали паз шириной 15 и глубиной 20 мм и наплавляли проволоку EnDotec DO*04 электродом (рис. 2).
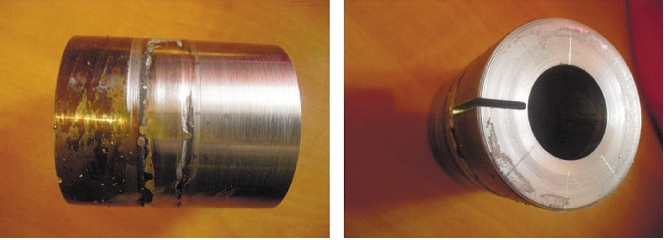
После наплавки вырезали заготовки под образцы размером 10×10×100 мм. Образцы изготовляли следующих типов: №1 – наплавка на сталь 20Х13 в состоянии поставки без термообработки (ТО); №2 – наплавка на сталь 20Х13 после низкого отпуска при температуре 300°С; №3 – наплавка на сталь 20Х13 после отпуска при температуре 650°С. После ТО на образцах оценивали твердость наплавки. Образцы перед испытанием шлифовали до шероховатости Rа = 0,8 мкм.
Методика проведения испытаний
Для хромистых сталей типа 20Х13 условия испытаний на МКК в ГОСТ 6032 не установлены. В ASTM А 262 есть примечание о возможности испытания стали AISI 410 (аналога стали 12Х13), по method C (кипячение в течение 240 ч в 65%-ном растворе HNO3 c оценкой скорости коррозии через каждые 48 ч). Однако структуры сталей 12Х13 и 20Х13 отличаются, и использовать данную методику невозможно.
Согласно работе [4], для хромистых сталей с содержанием хрома 13–17% испытания на МКК проводят следующим образом: выдержка 24 ч при температуре 80°С в растворе CuSO4, H2SO4 и HNO3. Раствор готовится в следующих пропорциях: 38 мл концентрированной H2SO4 + + 22 мл концентрированной HNO3 + + 220 г СuSO4*5H2O + 1000 мл H2O.
Однако при этом не указывается структура хромистых сталей (ферритные или мартенситные). В связи с этим было решено провести испытания по методу, приведенному в работе [2], но по 48 ч, 2 цикла.
Перед испытаниями образцы шлифовали, взвешивали и измеряли.
После испытаний проводили оценку под микроскопом ЗТВ и переходной зоны основной металл–наплавка на наличие микротрещин и рассчитывали скорость коррозии.
Результаты испытаний
Образцы с наплавкой выдерживали в течение двух циклов по 48 ч в растворе H2SO4, НNO3 и СuSO4.
Общий вид образцов представлен на рис. 3, 4.
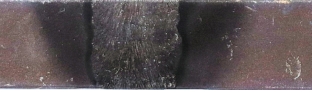
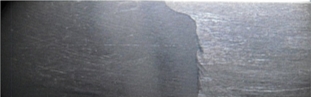
Твердость наплавки:
Образцы без ТО 44…48 HRC
Образцы после отпуска при температуре: 300°С 44…48 HRC 650°С 35 HRC
Скорость коррозии на образцах рассчитывали по формуле
где р – плотность стали; S – площадь образца; m – масса образца; t – время испытаний.
Результаты расчета скорости коррозии представлены в табл. 2.
Таблица 2
Показатели скорости МКК стали 20Х13
Номер образца |
Исходные данные | 1-й цикл | 2-й цикл | ||||||||
m | S | vк | m | S | Δm | vк | m | S | Δm | vк | |
1 | 49,6023 | 6,5 | – | 49,2838 | – | 0,3185 | 11,28 | 48,7328 | – | 0,551 | 19,55215 |
2 | 51,0159 | 6,64 | – | 50,7015 | – | 0,3144 | 11,26 | 50,1625 | – | 0,539 | 19,31471 |
3 | 50,2734 | 6,63 | – | 49,9504 | – | 0,323 | 11,59 | 49,4194 | – | 0,531 | 19,05674 |
4 | 47,2424 | 6,14 | – | 46,9205 | – | 0,3219 | 11,44 | 46,3997 | – | 0,5008 | 19,40723 |
5 | 50,0805 | 6,62 | – | 49,7447 | – | 0,3358 | 12,07 | 49,1811 | – | 0,5636 | 20,25725 |
6 | 50,514 | 6,62 | – | 50,1625 | – | 0,3515 | 12,63 | 49,6095 | – | 0,553 | 19,87626 |
7 | 50,6225 | 6,63 | – | 50,2719 | – | 0,3506 | 12,58 | 49,7265 | – | 0,5454 | 19,57353 |
8 | 50,4733 | 6,45 | – | 50,1263 | – | 0,347 | 12,80 | 49,5655 | – | 0,5608 | 20,68787 |
9 | 50,1815 | 6,61 | – | 50,0913 | 0,0902 | 3,25 | 49,9125 | 0,1788 | 6,436 | ||
10 | 50,5219 | 6,62 | – | 50,4099 | 0,112 | 4,03 | 50,1953 | 0,2146 | 7,713 | ||
11 | 49,3523 | 6,55 | – | 49,2465 | 0,1058 | 3,84 | 49,4655 | 0,219 | 7,956 | ||
Примечание. Образцы №1–4 – без термообработки; №5…8 – после отпуска при температуре 300°С; №9…11 – после отпуска при температуре 650°С |
При детальном рассмотрении образцов без термообработки и с термообработкой (отпуск при температуре 300°С) трещины в основном металле не наблюдались в отличие от ЗТВ, зоны сплавления и наплавки (рис. 5). В образцах после отпуска при температуре 650°С трещины не зафиксированы.
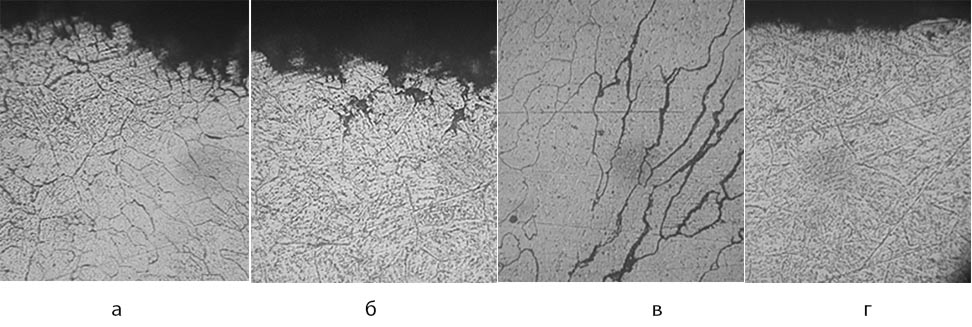
Выводы
Использование наплавки EnDotec DO*04 на сталь 20Х13 без термообработки и после термообработки (отпуск при температуре 300 и 650°С) не рекомендуется. Согласно результатам испытаний, скорость коррозии очень высокая. При отпуске при температуре 650°С трещины не зафиксированы, скорость коррозии в несколько раз меньше. С учетом отсутствия регламентированной методики этот результат можно считать удовлетворительным. Однако твердость наплавки после отпуска 650°С снизилась до 35 HRC, применение наплавки такой твердости снижает износостойкость материала.
Список литературы
- СТ ЦКБА 053–2008. Арматура трубопроводная. Наплавка и контроль качества наплавленных поверхностей. Технические требования.
- Давыдкин М.В., Немыкина О.В. Оценка стойкости патрубков из стали 20Х13 к стресс коррозии в условиях нефтепереработки//Химическое и нефтегазовое машиностроение. 2014. №11.
- ASTM А 262. Standard Practices for Detecting Susceptibility to Intergranular Attack in Austenitic Stainless Steels.
- Чигал В. Межкристаллитная коррозия нержавеющих сталей. Пер. с чешского под ред. Б.В. Строкана. М.: Химия, 1969.