Авторы: А.И. Швиндин, В.А. Берестовский (Сумский машиностроительный завод);
Б.И. Микерин (Ассоциация нефтепереработчиков и нефтехимиков)
Опубликовано на портале «Химическая техника», ноябрь 2020
За последние 5 лет многие американские и европейские насосные компании пытаются осветить решение проблем в определении стоимости срока службы (ССС) насосного оборудования различных насосных систем. Такие действия вызваны многими причинами. Во-первых, по статистическим данным, электронасосы потребляют почти 20% всей производимой в мире электроэнергии, в отдельных отраслях промышленности эта цифра возрастает до 50% общего потребления. Во-вторых, маркетинговые исследования многих компаний указывают, что спрос на насосы будет увеличиваться на ~5% ежегодно в течение ближайших нескольких лет. Как результат – огромное количество насосов потребуется для установки в новых системах, но еще большее количество потребуется для замены существующих морально и физически устаревших или не соответствующих требуемым параметрам при реконструкции насосных установок. В-третьих, насос как самостоятельный объект в системе отличается низкими инвестиционными затратами, однако он существенно влияет на работоспособность и экономическую эффективность системы. Особенно наглядно это проявляется в технологических установках нефтеперерабатывающих заводов (НПЗ), где стоимость насосного оборудования гораздо меньше стоимости колонного и печного оборудования, а также средств автоматизации технологических процессов нефтепереработки. Но суточный простой одной технологической установки из-за ненадежной работы основных насосов влечет за собой миллионные убытки. Достаточно отметить, что на каждом НПЗ стран СНГ находятся в эксплуатации до 3000 насосов различного конструктивного исполнения мощностью до 1200 кВт.
Известно, что на долю насосно-компрессорного оборудования НПЗ приходится около 80% всей потребляемой на НПЗ электроэнергии [1], поэтому вопрос правильного выбора насосного оборудования для обеспечения снижения энергопотребления как при новом строительстве, так и при модернизации действующих установок весьма актуален. И в дальнейшем, как следствие этого выбора, встает вопрос о снижении затрат на эксплуатацию и ликвидацию последствий аварий.
Оптимизация насосной установки с точки зрения ССС означает не только минимизацию потерь её составных частей, но и выбор оптимальной конструкции насоса с точки зрения обеспечения параметров работы, надежности и долговечности, минимального числа запасных частей и длительности ремонта. Уже сформировалось мнение, что стоимость первоначальных капиталовложений при приобретении оптимальной насосной системы не будет иметь решающего значения. Решающим фактором станет ССС. На основании исследований американского Института гидравлики Hydrаuliс Institute (HI) и Europump основные компоненты, определяющие ССС и их среднестатистический вес в %, можно выразить следующим [2]:
ССС = Сіс + Сіn + Cе + Со + Сm + Cs + Cenv + Cd ,
где Сіс < 15% – стоимость первоначальных капиталовложений в насосную установку, насоса, вспомогательных систем и услуг; Сіn < 10% – стоимость установки, включая стоимость площадей, необходимых для размещения; Cе < 30–35% – затраты на потребляемую энергию при эксплуатации установки; Со < 7% – стоимость оплаты труда обслуживающего персонала; Сm < 15% – стоимость планового и предупредительного обслуживания, включая ремонты; Cs < 15% – стоимость простоя с учетом производственных потерь; Cenv < 5% – затраты на сохранение окружающей среды; Cd < 7% – стоимость полной ликвидации.
Как видно, в ССС превалируют затраты на потребляемую электроэнергию. Проблема энергосбережения является сложнейшей задачей во всех отраслях. Специалисты Управляющей компании «Группа ГМС» (Москва) на примере магистрального нефтепровода «Восточная Сибирь – Тихий Океан» (ВСТО 1 и ВСТО 2) ОАО «АК «ТРАНСНЕФТЬ», где единичная мощность некоторых магистральных насосов достигает 12 500 кВт, выполнили ряд расчетов стоимости жизненного цикла насосной установки нефтепровода [3]. Показано, что для среднего по мощности применяемого магистрального насоса затраты на потребление электроэнергии достигают 45% общей суммы затрат. Приведены также рекомендации по снижению энергопотребления насосами за счет оптимизации компоновки насосов в установке, повышения их КПД, улучшения кавитационных характеристик и применения сменных проточных частей для работы на недогрузочных режимах.
Предприятия нефтепереработки и нефтехимии являются энергоемкими производствами. Соответственно себестоимость продукции в этой отрасли в значительной степени определяется уровнем затрат. Потребляемая в нефтепереработке энергия – самая высокая статья расходов, сравнимая со стоимостью сырья. По официальным данным, из общего количества затрат на тепловую и электрическую энергию приходится до 45% [1]. Учитывая, что правительство РФ приняло ряд постановлений и мероприятий, в результате которых в ближайшие 5 лет должны быть введены в эксплуатацию более 120 новых установок вторичной переработки нефти, вопрос энергосбережения в нефтепереработке и трубопроводном транспорте нефтепродуктов становится весьма злободневным. По некоторым официальным данным, только оптимизация энергопотребления на НПЗ может снизить расходы на 25–40 % [1]. Перечень технических решений, используемых для снижения энергетических затрат, обобщенно можно представить следующим образом:
- оптимизация процесса в установках, производящих тепловую и электрическую энергию для собственных нужд производства;
- упорядочивание энергетического баланса всех технологических потоков и энергоресурсов с целью их наиболее результативного использования;
- решение задач по увеличению КПД любой установки путем замены устаревшего оборудования современным, более экономичным;
- улучшение технологии производства за счет применения передовых технологических процессов.
Вопросы повышения эффективности нефтепереработки, снижения затрат при производстве и транспортировке нефтепродуктов должны решаться еще на стадии проектирования новых установок. Исходя из общего требования снижения стоимости срока службы насосной станции, в ПАО «Институт транспорта нефти» (г. Киев) разработан проект нового магистрального нефтепродуктопровода (МНПП) «Полоцктранснефть «Дружба», позволяющего транспортировать нефтепродукты (дизельное топливо, автомобильный бензин) непосредственно с НПЗ ОАО «НАФТАН» (республика Беларусь) [4]. Особенностью спроектированного МНПП является то, что насосное оборудование с оптимальными параметрами должно обеспечивать объемы перекачивания на всех стадиях его строительства. Согласно проекту, насосная станция должна быть оснащена тремя насосными агрегатами – двумя рабочими и одним резервным. Максимальное давление на выходе насосных станций (7,4 МПа) обеспечивается режимом последовательной работы двух насосных агрегатов. Насосные агрегаты в насосной станции могут работать и параллельно, и последовательно. Режимы работы насосов приведены в таблице.
Параметры / режимы | 1-й пусковой | 2-й пусковой | 7-й пусковой | ||||
Производительность Q, м3/ч | 160 | 160 | 155 | 176 | 222 | 222 | 260 |
Напор H, м | 515 | 500 | 900 | 1000 | 900 | 770 | 1000 |
Перекачиваемая среда | ДТ | АБ | ДТ | АБ | ДТ | АБ | ДТ/АБ |
Исходя из указанных условий, проектантом были поставлены жесткие требования к конструкции насосных агрегатов, их установленной мощности и вспомогательным системам. Особенностями эксплуатационных требований к этим насосным агрегатам были следующими:
- Последовательная работа двух рабочих насосных агрегатов, при этом каждый из трех агрегатов может быть, как рабочим, так и резервным – по технологическому регламенту насосной станции. В связи с этим уплотнения вала каждого насоса должны быть выбраны на максимально возможное давление в магистрали;
- В отличие от существующих насосных станций МНПП в проектируемой насосной не предусмотрено наличие охлаждающей жидкости;
- В отличие от существующих насосных станций МНПП с серийными насосными агрегатами АНМ 250-475 с одной маслоустановкой на три насосных агрегата в проектируемой насосной маслоустановка не предусмотрена;
- Приводные электродвигатели должны иметь исполнение под систему частотного регулирования, применение которой планируется на последующих этапах эксплуатации. Обеспечение требуемых режимов работы МНПП будет более экономичным при частотном регулировании подачи магистральных насосов. Но это требование предъявляет жесткие условия к характеристикам магистрального насоса и его КПД, так как при применении ПЧ приводной электродвигатель должен выбираться с 10–15%-ным запасом от максимальной потребляемой мощности. А проектом ограничена мощность приводных электродвигателей – не более 400 кВт, тогда как серийные магистральные насосы типа НМ 250-475 комплектуются электродвигателями мощностью 500 кВт.
Для обеспечения этих требований в ООО «СМЗ» созданы и поставлены на насосную станцию три насосных агрегата АНДМс 250-480 с приводными электродвигателями мощностью 400 кВт. Это оборудование относится к новому поколению нефтяных насосов [5, 6], разработанных в ООО «СМЗ» по предложению Ассоциации нефтепереработчиков и нефтехимиков (Москва) в соответствии с требованиями действующих отечественных нормативных документов и международных стандартов ISO 13709/API 610 и ISO 21049/API 682.
В декабре 2017 г. на МНПП проведены гидроиспытания и пробные пуски насосных агрегатов, а в мае 2017 г. МНПП ОАО «Полоцктранснефть «Дружба» введен в промышленную эксплуатацию. Все эксплуатационные характеристики насосных агрегатов соответствуют паспортным [7]. На рис. 1 приведена насосная станция МНПП, на рис. 2 –комплектующее её насосное оборудование в работе.
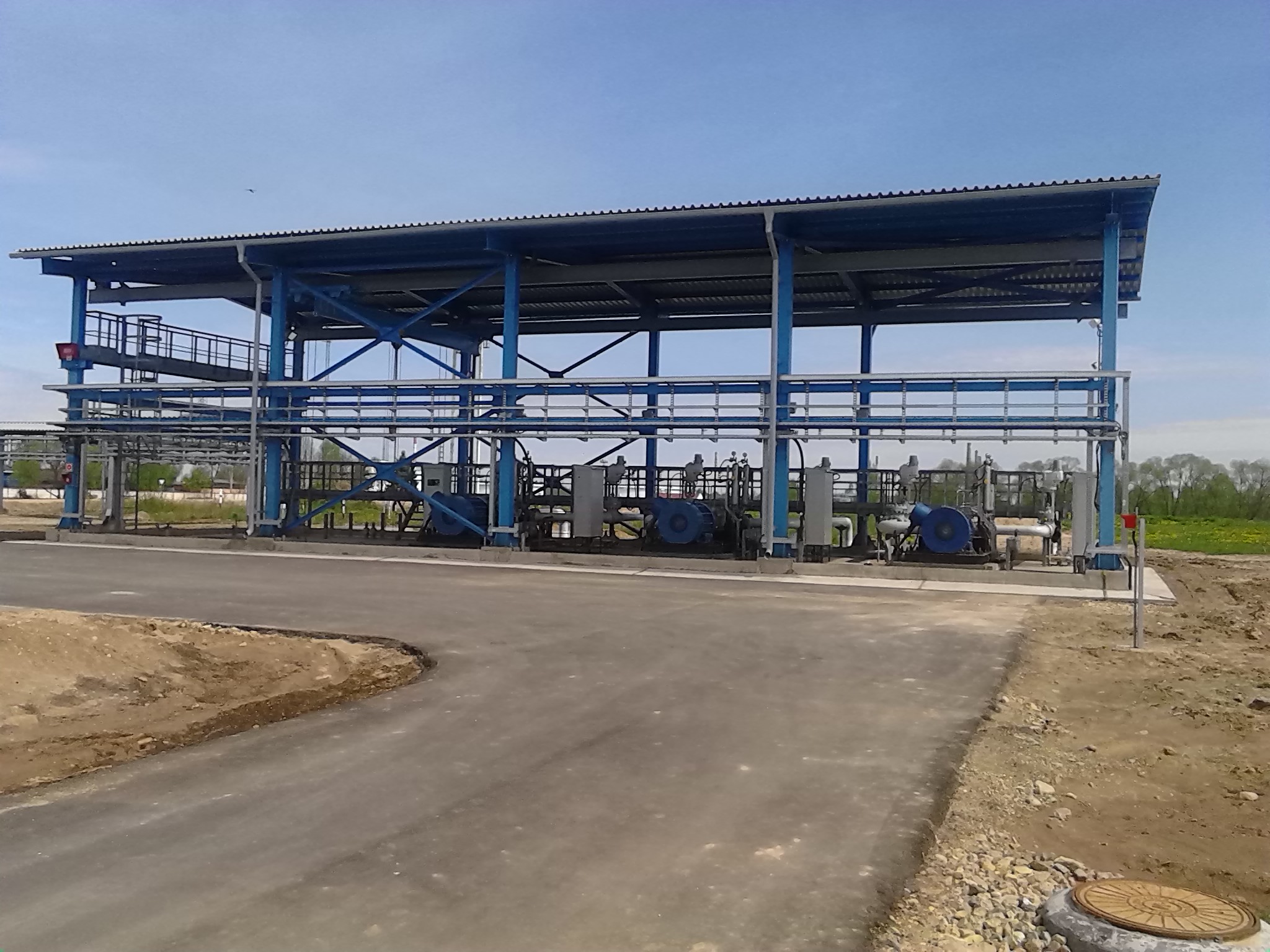
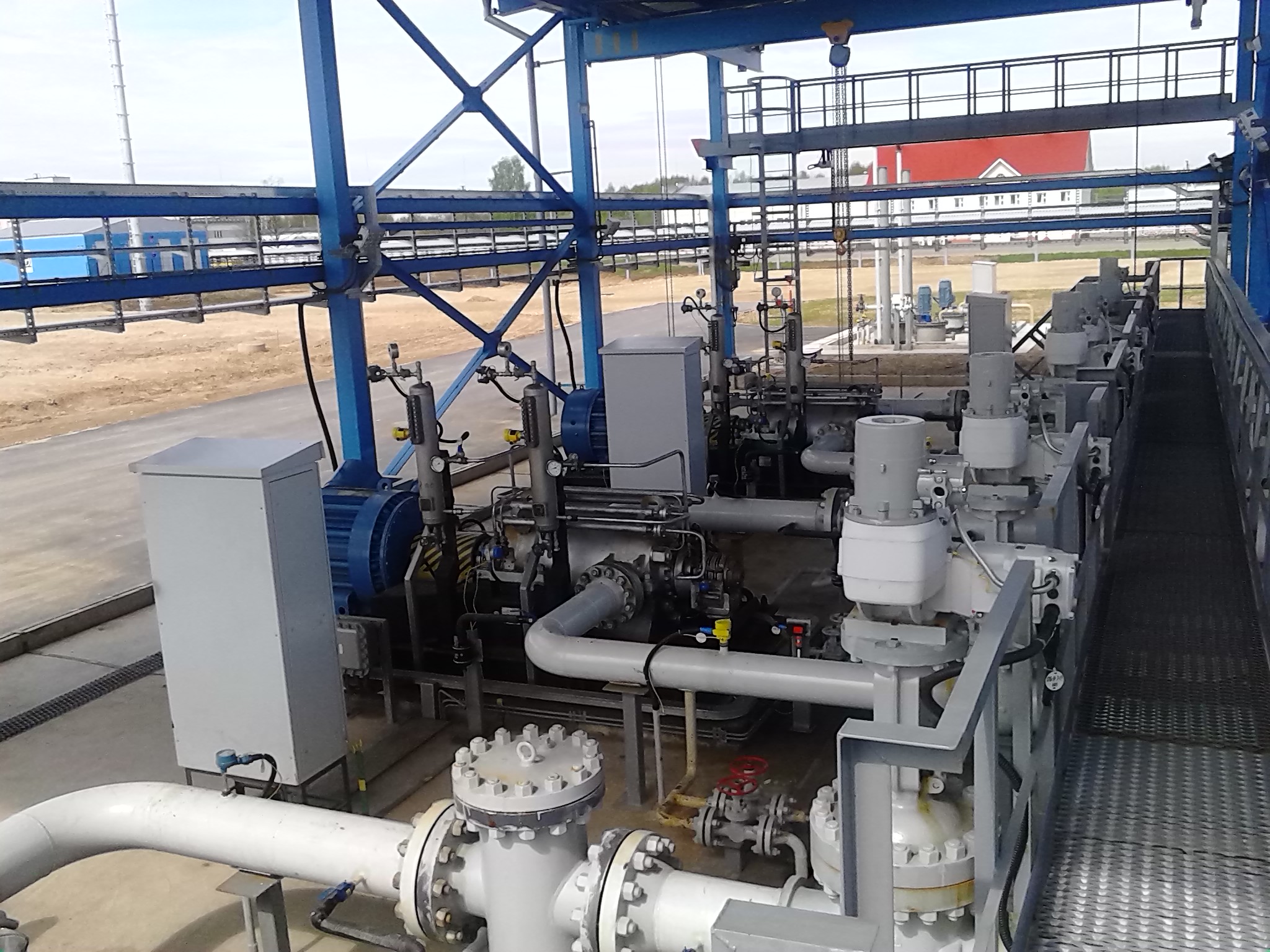
Благодаря постоянному мониторингу и диагностике фактического состояния насосного оборудования существенно снизилось количество внезапных отказов и соответствующих ремонтов. Таким образом, снижение энергопотребления технологической установки сводится в основном к выбору современного энергосберегающего насосного оборудования. Но не только. При выборе насоса расчетным режимом для него считается режим его подачи, соответствующий максимальной проектной мощности установки, который в условиях реального производства случается очень редко. Технологические режимы работы установок НПЗ не исключают работу основных насосов на частичных подачах, а при технологических пусках – их кратковременную работу на подачах, близких к нулевым. В результате большинство основных насосов годами работают на 40 – 70%-ной подаче. Например, первый сумской двухопорный насосный агрегат АНГ 200-510 с приводным электродвигателем мощностью 400 кВт, предназначенный для перекачивания гудрона температурой до 400°С в УЗК цеха №73 Новокуйбышевского НПЗ, длительное время работал с подачей 120 м3/ч (расчетная – 200 м3/ч), а напорной задвижкой давление в трубопроводе дросселировалось до 24 кгс/см2 (проектное 40 кгс/см2) [8]. Таким образом, насос работал на 60%-ной подаче, а при дросселировании напорной задвижкой терялось более 50% потребляемой насосом мощности. При этом из трех насосных агрегатов один был в работе, а два – в горячем резерве. В ООО «Пермьнефтеоргсинтез» в 2005 г. пуск нового комплекса глубокой переработки нефти по различным причинам занял длительное время. В результате насосы НКВ 600/320 мощностью 800 кВт несколько недель работали на подачах 40…80 м3/ч. От повышенной низкочастотной вибрации на этих подачах происходило самоотвинчивание крепежа рабочего колеса, что неоднократно приводило к аварийному останову насоса.
Известно, что работа центробежных насосов на недогрузочных режимах – частичных подачах – сопровождается повышенной виброактивностью, являющейся причиной преждевременного выхода из строя торцовых уплотнений и подшипников. Кроме того, КПД насоса на таких режимах значительно ниже оптимальных значений. Учитывая то, что основным потребителем электроэнергии на НПЗ являются насосы, то это прямые потери. Международным стандартом ISO 13709/API 610 четко оговорена предпочтительная (рекомендуемая) зона работы насоса по подаче (0,7…1,1)Qопт (здесь Qопт – режим максимального КПД), рис. 3. Кратковременно допустимая минимальная подача установлена в пределах 0,5Qопт, максимальная – 1,2Qопт.
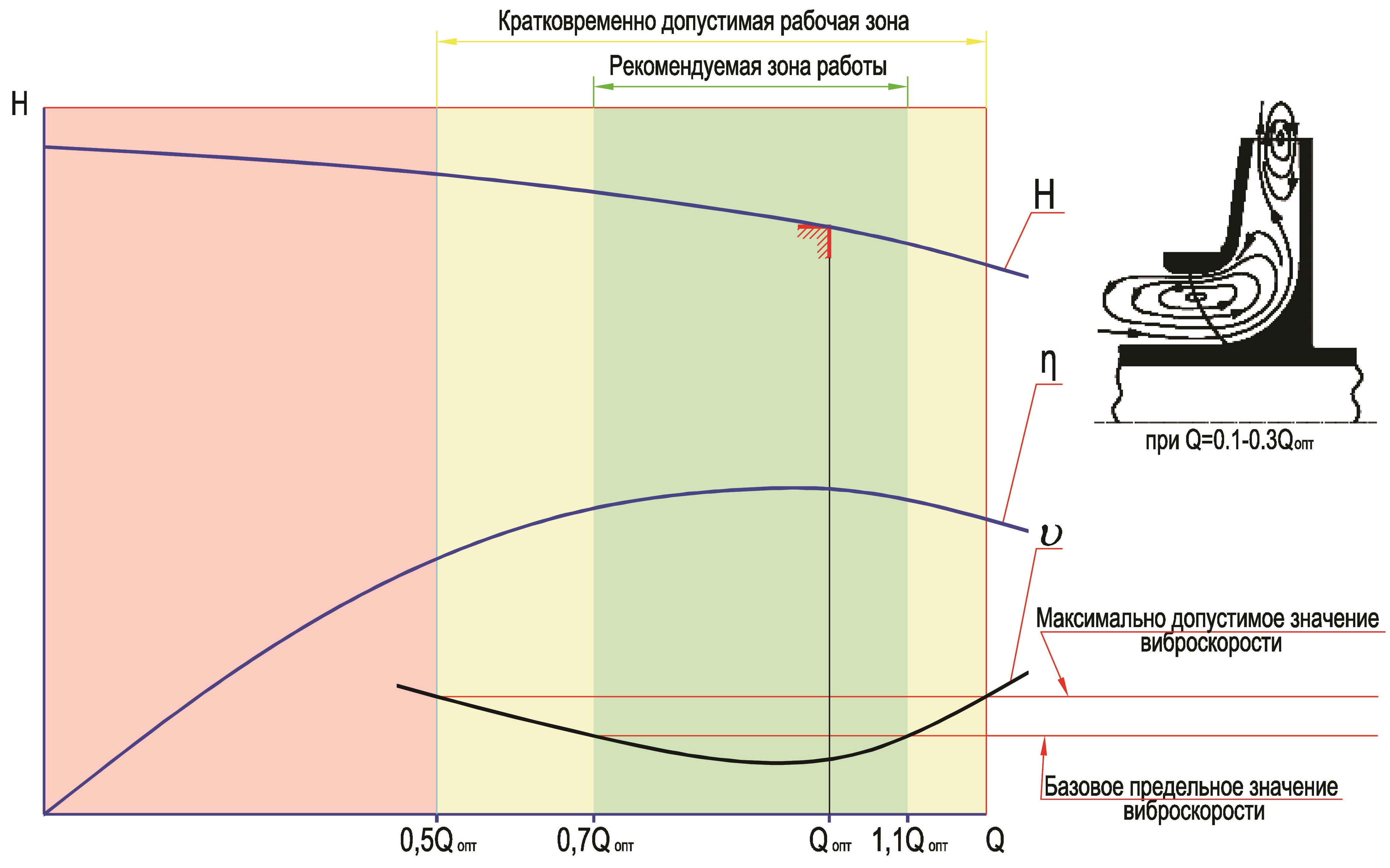
На рис. 3 также показана физическая картина течения на малых подачах, когда образуются «обратные токи» на входе и иногда на выходе рабочего колеса. Эти локализованные вихри вызывают мощные пульсации в проточной части, которые являются причиной повышенной низкочастотной вибрации.
Одним из известных способов экономичного изменения параметров насосов является изменение частоты вращения его привода. Из устройств для такого регулирования наиболее экономичными и надежными зарекомендовали себя преобразователи частоты (ПЧ) различных исполнений с современной электроникой и гидродинамические муфты. Применение таких устройств с асинхронными электродвигателями позволяет добиться:
- экономии потребляемой электроэнергии до 40%;
- обеспечения плавного пуска электродвигателя;
- увеличения срока службы силовых электродвигателей;
- сокращения расходов на обслуживание;
- удобства управления, диагностики и контроля за работой оборудования.
Установка дополнительных датчиков в определенных местах оборудования и системы позволяет автоматизировать управление работой насосов. Несмотря на то, что цена такого регулятора частоты немалая, но и экономическая выгода от его применения несомненна. Имеются сведения, что средства, вложенные в приобретениt ПЧ, окупаются в течение 1,5–2 лет, а в дальнейшем он приносит чистую прибыль. Но не все так просто, потребуется решать много проблемных технических и экономических вопросов, поэтому принятие решения о приобретении регулятора частоты для каждого конкретного насоса или установки требует обстоятельного экономического обоснования.
Но всё это оправдано при новом строительстве. А в странах СНГ практически все НПЗ (кроме НПЗ в Нижнекамске) построены до 1980-х годов. Износ основных фондов многих этих производств достиг 40%. Самыми эффективными способами снижения энергопотребления для этих производств могут быть как их модернизация с целью внедрения прогрессивных ресурсосберегающих технологий, так и замена морально и физически устаревшего оборудования новой техникой, созданной для задач энергосбережения.
Для обеспечения нормальной работы насосного оборудования при пусковых и нерасчетных режимах по подаче можно предложить другой, менее затратный, способ при модернизации старых установок. Традиционная компоновка – один рабочий насос на 100%-ную расчетную подачу плюс один резервный насос на 100%-ную расчетную подачу (суммарная установленная мощность 200%) требует пересмотра. Учитывая то, что все насосы допускают длительную работу в допустимом интервале подач (от 50 до 120% оптимальной подачи насоса Qопт), а также полагая, что установки длительное время работают на частичной нагрузке (подаче), можно предложить следующую компоновку (рис. 2): три насоса (рабочий, резервный и пуско-резервный) на 50%-ную от расчетной подачу (+ 20 %).
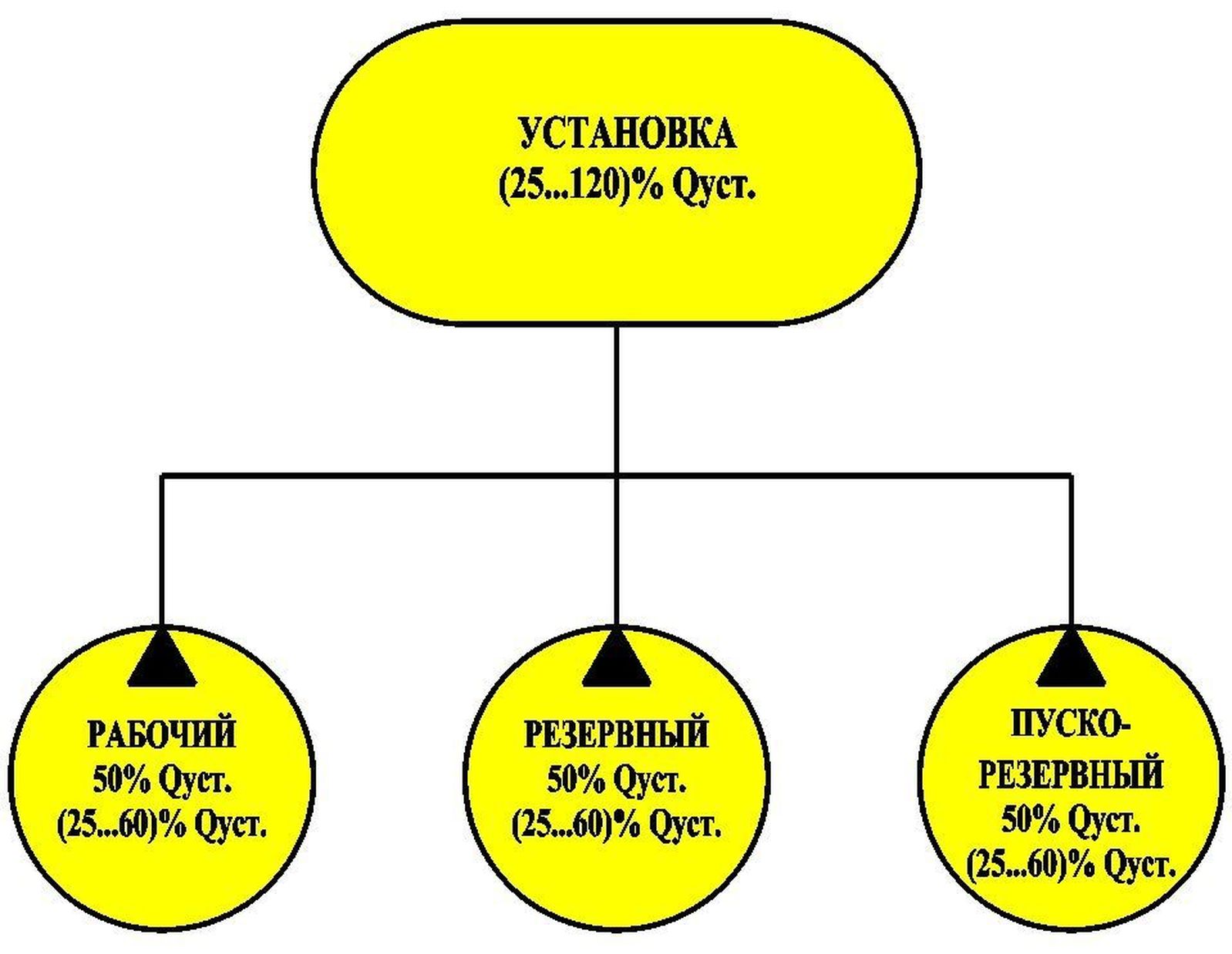
Предлагаемая компоновка в различных комбинациях параллельной работы может устойчиво обеспечивать любые режимы по технологическому регламенту работы установки (от 25 до 120%), в том числе сохраняя 100%-ный резерв. При этом насосы будут работать в режимах, близких к оптимальным, что обеспечивает снижение энергопотребления по сравнению с традиционной компоновкой. Установленная мощность при такой компоновке не превысит 150%. Естественно, что это должны быть насосы нового поколения, разработанные в соответствии с требованиями международных стандартов ISO 13709/ API 610 и ISO 21049/ API 682 и с максимально высоким КПД.
Выбор любого технического решения требует тщательных экономических расчетов всех возможных вариантов, что позволит гарантированно обеспечить и бесперебойную работу установки, и снижение её энергопотребления, и, в конечном итоге – снижение стоимости срока службы. А это, в свою очередь, приведет к снижению себестоимости вырабатываемой продукции.
Список литературы
- Микерин Б., Швидин А. Об энергосбережении в нефтепереработке// Насосы и оборудование. – 2015. №4-5.
- Guide of Europump and Hydraulic Institute (USA). Pump Life Cycle Costs: A Guide to LCC Analysis for Humhing Systems.
- Твердохлеб И., Бирюков А., Визенков Г. К вопросу о выборе насосного оборудования для трубопроводного транспорта нефти// Насосы и оборудование. – 2014. №6.
- Швиндин А., Шевченко С., Заворотний В., Кухто Ю. Нефтяные магистральные насосы нового поколения// Насосы и оборудование. – 2015. №6.
- Насосное оборудование для нефтеперерабатывающей и нефтехимической промышленностей. Каталог выпускаемой продукции ООО «СМЗ». Ч. II. г. Сумы. – 2008. – 44 с.
- Швиндин А.И. Центробежные насосы для нефтеперерабатывающих и нефтехимических производств. – М.: ООО «НТЦ при Совете главных механиков», 2012. – 152 с.
- Швиндин А., Кацов С., Кухто Ю. Новая насосная техника в работе// Насосы и оборудование. – 2017. №6.
- Востриков И.Ю., Надршин К.А., Артеменко А.В., Швиндин А.И.) и др. Новые высоконапорные насосы для нефтеперерабатывающих производств// Химическая техника. – 2007. №7.