Авторы: Л.П. Барабанова, Я.Ю. Шленский, А.А. Соснин, Г.Ю. Рожемберская (АО «ИркутскНИИхиммаш»).
Опубликовано в журнале Химическая техника №9/2015
Для определения технического состояния аппаратов и продления срока безопасной эксплуатации экспертными организациями проводятся работы по экспертизе промышленной безопасности. Одним из этапов такой экспертизы является расчет на прочность.
Масляные насосы «Шварцкопф», установленные на заводе АО «АНХК» (г. Ангарск) – сложные устройства, работающие под высоким давлением, состоят из большого числа деталей и узлов, поэтому к ним предъявляются повышенные требования безопасности. Изготовленные более полувека назад, эти насосы являются типичным примером нестандартного оборудования, при расчете которого нет возможности пользоваться существующими нормативными документами, стандартами и методиками. Выполнять поверочный расчет всех входящих в конструкцию деталей, как правило, не имеет смысла ввиду большой трудоемкости. В этом случае проводится расчет на прочность деталей и узлов, подверженных наиболее интенсивным нагрузкам либо подвергающихся частому ремонту или замене.
Масляный насос «Шварцкопф» относится к плунжерным насосам. Схема насоса представлена на рис. 1.
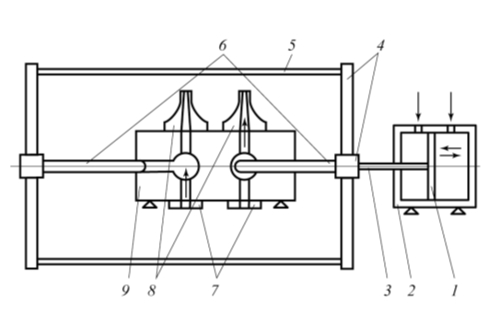
1 – поршень гидроцилиндра; 2 – корпус гидроцилиндра;
3 – шток гидроцилиндра; 4 – крейцкопфы, плечи крейцкопфа;
5 – приводные штанги; 6 – плунжеры;
7 – камеры всасывания; 8 – камеры нагнетания;
9 – двойной прессующий цилиндр
По результатам проведенного анализа конструкции и условий эксплуатации насоса были определены пять наиболее нагруженных деталей насоса, для которых необходимо проводить расчет: шток гидроцилиндра 3, приводные штанги 5, плунжеры 6, камеры нагнетания 8, двойной прессующий цилиндр 9. Все эти детали (кроме камер нагнетания) работают в условиях циклической нагрузки.
Расчеты штока гидроцилиндра, приводных штанг и плунжера проводятся методами технической механики (подробное описание методик расчета этих деталей не входит в рамки данной статьи).
Остановимся на оценке прочности двух наиболее сложных и объемных деталей: камер нагнетания и двойного прессующего цилиндра. Обе детали изготовлены из стали 35ХМ и являются цельнометаллическими элементами сложной конфигурации. Для оценки прочности таких деталей используется программный комплекс NASTRAN, реализующий метод конечных элементов [1].
Камера нагнетания масляного насоса представляет собой осесимметричную деталь диаметром 300 мм и высотой 380 мм. По конфигурации является плоской крышкой с центральным отверстием переменного диаметра.
По центру расположен штуцер криволинейной формы.
По периметру камеры расположены восемь отверстий под шпильки, которыми камера крепится к прессующему цилиндру. Конечно-элементная модель камеры нагнетания приведена на рис. 2.
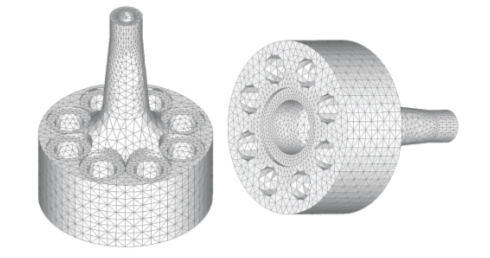
Камера нагружена внутренним избыточным давлением p = 32 МПа, распределенным по поверхности центрального отверстия (рис. 3, а), осевым усилием от давления
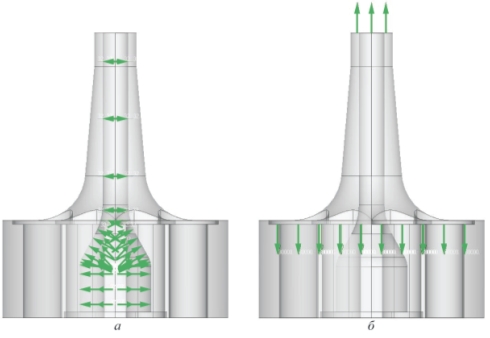
Fp = 3⋅104 Н, распределенным по торцовой поверхности штуцера (рис. 3, б, сверху) и усилием от затяжки гаек
Q = 6⋅105 Н, распределенным по площади контакта гаек с поверхностью камеры (рис. 3, б).
На модель камеры нагнетания наложены следующие граничные условия:
- ограничение радиального перемещения по наружной поверхности в верхней части штуцера моделирует влияние фланца, ограничивающего радиальное расширение штуцера (рис. 4, а);
- ограничение перемещения по направлению нормали к нижней опорной поверхности моделирует контакт с уплотнением (рис. 4, б).
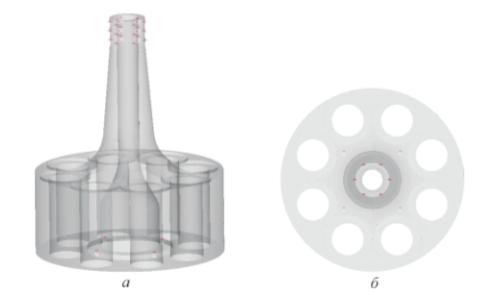
Результаты расчетов напряженно-деформированного состояния камеры представлены в виде набора векторов в цилиндрической системе координат, совпадающей с осью детали.
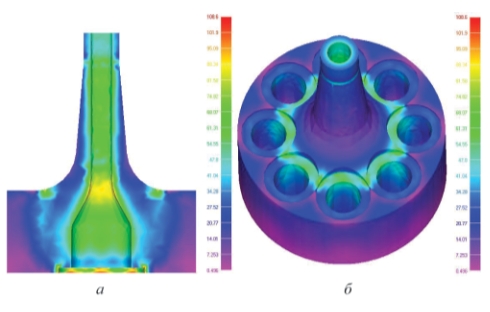
На рис. 5 приведено распределение эквивалентных напряжений σэкв (МПа) по четвертой теории прочности (теория наибольшей удельной потенциальной энергии формоизменения). Как видно, эквивалентные напряжения имеют наибольшую интенсивность на нижней опорной поверхности, по всей внутренней поверхности, в зоне изменения диаметра, в зоне краевого эффекта от фланца и в зоне концентрации на верхней поверхности. Максимальные эквивалентные напряжения составляют 108,6 МПа.
Условие прочности, согласно ноpмам pасчета на пpочность [2], принимает вид σэкв ≤ σRV, где σRV – допускаемый размах напряжений для материала камеры, МПа.
Допускаемый размах напряжений для стали 35Х при температуре 55°С, согласно данным справочника [3], составляет 470 МПа. Поскольку 108,6 МПа < 470 МПа, условие статической прочности для камеры нагнетания выполняется.
Двойной прессующий цилиндр (далее цилиндр) представляет собой массивную кованую деталь длиной ~1,5 м с наибольшим диаметром 710 мм. Внутри детали имеются две сферические полости – рабочие камеры, где происходит нагнетание масла. Каждая рабочая камера имеет три выхода: направляющее отверстие для плунжера, впускной канал, по которому рабочая среда попадает в рабочую камеру, и выпускной канал, по которому через клапан рабочая среда уходит в камеру нагнетания. Конечно-элементная модель цилиндра приведена на рис. 6.
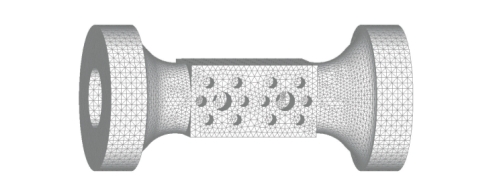
Цилиндр нагружен внутренним избыточным давлением p = 32 МПа, распределенным по внутренней поверхности (рис. 7, а), и силой от уплотнения Q = 6⋅105 Н, приложенной к поверхностям соприкосновения цилиндра с уплотнениями (рис. 7, б). Жесткое закрепление торцовых поверхностей цилиндра (рис. 7, б) моделирует фланцевые соединения.
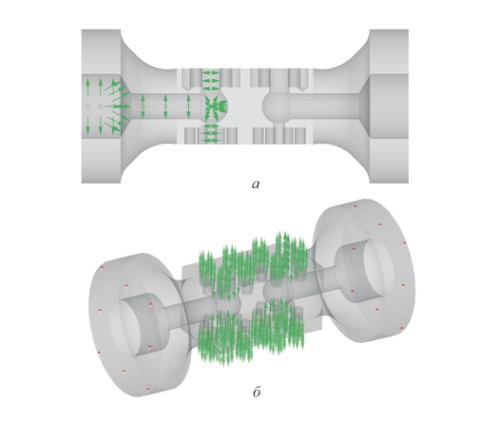
Результаты расчетов напряженно-деформированного состояния цилиндра представлены в виде набора векторов, содержащих полное перемещение узлов, шесть составляющих напряженного состояния и эквивалентные напряжения по четвертой теории прочности. Все результаты представлены в прямоугольной системе координат, где ось X совпадает с осью детали, а ось Z параллельна осям отверстий под шпильки.
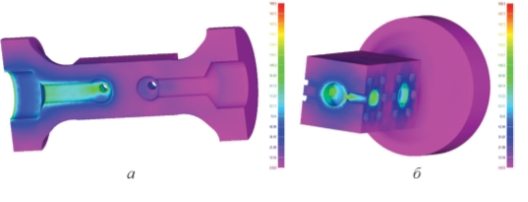
На рис. 8 приведено распределение эквивалентных напряжений в цилиндре. Как видно, максимальные напряжения отмечаются в отверстиях под шпильки, на поверхностях контакта с уплотнением и по кромке отверстий сферической рабочей камеры.
Проверяем условие статической прочности σэкв ≤ σRV.
В численной форме 168,3 МПа < 470 МПа, т.е. условие статической прочности для цилиндра выполняется.
Для зоны концентрации напряжений в отверстиях под шпильки дополнительно проводим оценку циклической прочности цилиндра согласно нормам [2]. При этом цикл изменения эквивалентных напряжений принимаем асимметричным.
Данный метод используется для проведения расчетов на прочность насосов высокого давления.
Список литературы
- NX-& NASTRAN 7.5. Copyright 2010 Siemens Product Lifecycle Management Software Inc. Лицензия №1258787.
- ПНАЭ Г-7-002–86. Ноpмы pасчета на пpочность обоpудования и тpубопpоводов атомных энергетических установок. М.: Энеpгоатомиздат, 1989.
- Биргер И.А. Расчет на прочность деталей машин. Справочник. М.: Машиностроение, 1979.