Авторы: К.Ю. Зерщиков, Ю.В. Семенов (ООО «Константа-2»).
Опубликовано в журнале Химическая техника №10/2016
Разработка оборудования для добычи нефти из глубоких горизонтов при повышенных давлениях, температурах, агрессивности сред, для сжижения газов, бурения в высоких широтах, сланцевой добычи нефти и газа требует применения новых технологических решений, включающих и уплотнительные узлы. При этом актуальными проблемами в создании новых образцов уплотнительной техники являются повышение их надежности при повышенных рабочих параметрах и уменьшение массогабаритных характеристик узлов.
Манжеты наряду с кольцами и сальниками являются одним из основных типов контактных уплотнений, сочетающих малые габаритные размеры с высокими эксплуатационными характеристиками. Они находят наибольшее применение в уплотнении подвижных соединений в парах с возвратно-поступательным и вращательным движением, а также в ответственных неподвижных соединениях. В зависимости от рабочих давлений, уплотняемых сред, скоростей взаимного перемещения применяют манжеты различных типов, отличающиеся конструкцией и материалами, из которых они изготовлены. Одним из типов манжет, которые, несмотря на отличные характеристики, пока мало применяются в отечественном машиностроении, являются полимерные манжеты с подпружинивающим элементом (МПЭ) [1].
Полимерные манжеты с пружиной (spring energized seales) стали применяться в 70-х годах прошлого века за рубежом. Вначале они использовались только в аэрокосмической и оборонной промышленности для решения задач в рамках космических проектов [2]. Затем их начали применять в оборудовании для нефтяной, газовой и других отраслей промышленности. Еще раньше и в России, и за рубежом начали применять резиновые манжеты с пружинами (рис. 1) для уплотнения вращающихся валов, гидравлических и пневматических приводов, однако потребовалось некоторое время, чтобы уровень технологии позволил получить манжеты с пружиной, где тело манжеты изготовлено из полимеров.
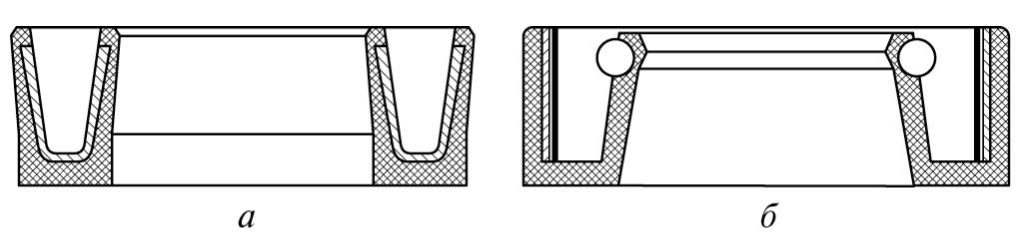
Российские разработчики и эксплуатанты нефтегазового оборудования знакомы с МПЭ по зарубежным источникам [2–4], поскольку в России эти уплотнения не производились. Отчасти поэтому в России не разрабатывалась техника с использованием данных уплотнений, в лучшем случае использовались целые узлы, включающие эти уплотнения. Сведения, приводимые на сайтах зарубежных производителей, позволяют оценить возможность их применения в определенных условиях эксплуатации, но не позволяют целенаправленно выбирать манжеты и конструировать узлы с их применением. С появлением собственных разработок, касающихся конструкции и технологии производства МПЭ, появляется необходимость детального исследования их характеристик и герметизирующей способности. Наши исследования призваны объяснить принцип герметизации данного вида уплотнений и научить российских проектировщиков конструированию узлов с их применением. Данная статья описывает лишь начальный этап исследований и призвана обратить внимание на МПЭ как на прогрессивный вид уплотнений, применение которых позволит решить большой ряд проблем уплотнительной техники и предназначена для разработчиков новой техники с повышенными рабочими характеристиками и показателями надежности.
Манжета с подпружинивающим элементом представляет собой сочетание полимерного компонента, назовем его оболочкой, как правило, U-образной формы, выполняющего в основном функцию контактного уплотнения и пружинящего компонента, создающего начальное контактное давление на кромках манжеты. Геометрически манжеты характеризуются наружным D или внутренним d диаметром (рис. 2), которые соотносятся с диаметром поршня или цилиндра и размерами сечения, которые, в свою очередь, соотносятся с размерами посадочного места L и H (см. рис. 5). Как видно, конфигурация манжеты и вид подпружинивающего элемента могут быть различными. Подпружинивающий элемент круглого сечения (см. рис. 2, а, в, г) может быть выполнен в виде резинового кольца, резинового кольца во фторопластовой оболочке, спирально-витой пружины из проволоки или ленты. U-образная пружина, изготавливаемая специальным образом из листовой стали, также позволяет создавать усилие на кромках манжеты, которая при этом имеет несколько иную конфигурацию (см. рис. 2, б). Наличие подпружинивающих элементов с различными упругодеформационными характеристиками позволяет, как будет показано далее, получать разные характеристики манжет. При этом внутренняя полость манжеты изготавливается таким образом, чтобы подпружинивающий элемент фиксировался в ней от выпадания.
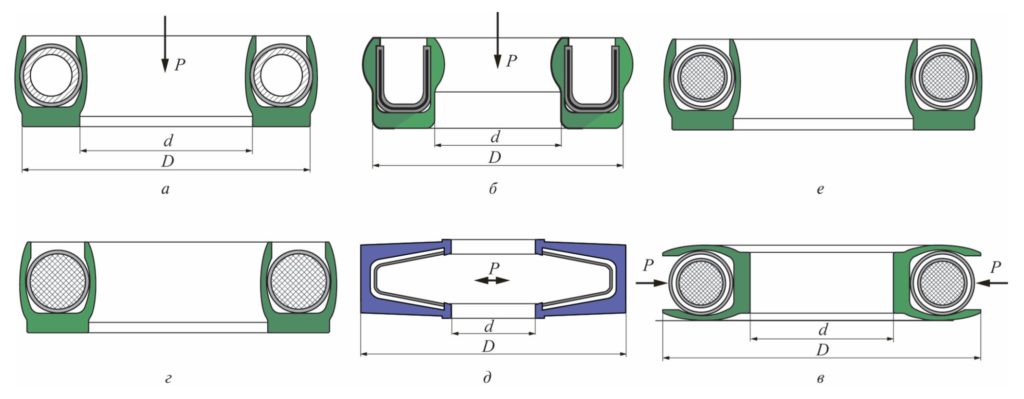
а – со спирально-витой пружиной в сплошной фторопластовой оболочке; б, д – с U-образной пружиной с защитным покрытием;
в, е – с резиновым кольцом в сплошной фторопластовой оболочке; г – с резиновым кольцом круглого сечения;
а – г – радиальные; д – е – торцовые
В зависимости от взаимного направления давления среды и плоскости различают торцовые манжеты, у которых вектор давления параллелен плоскости манжеты (см. рис. 2, а–г) и радиальные, у которых они взаимно перпендикулярны (см. рис. 2, д, е). Для уплотнения неподвижных соединений применяют в основном торцовые манжеты, развернутые в сторону давления среды для реализации эффекта самоуплотнения, в подвижных соединениях чаще используются радиальные манжеты.
Основной характеристикой, определяющей герметичность контактных уплотнений, является развиваемое ими контактное давление на сопрягаемых поверхностях [5]. Оно возникает в результате деформирования уплотнения при установке его между уплотняемыми поверхностями, как правило, в канавку определенной формы и размеров. Контактное давление определяется как частное от деления усилия на кромках и площади контактной поверхности, образуемой при сжатии. Поскольку геометрически уплотнения представляют собой замкнутые кривые (в основном это окружности), на практике определяют усилие, действующее на единицу длины периметра уплотнения – погонное усилие и ширину контакта.
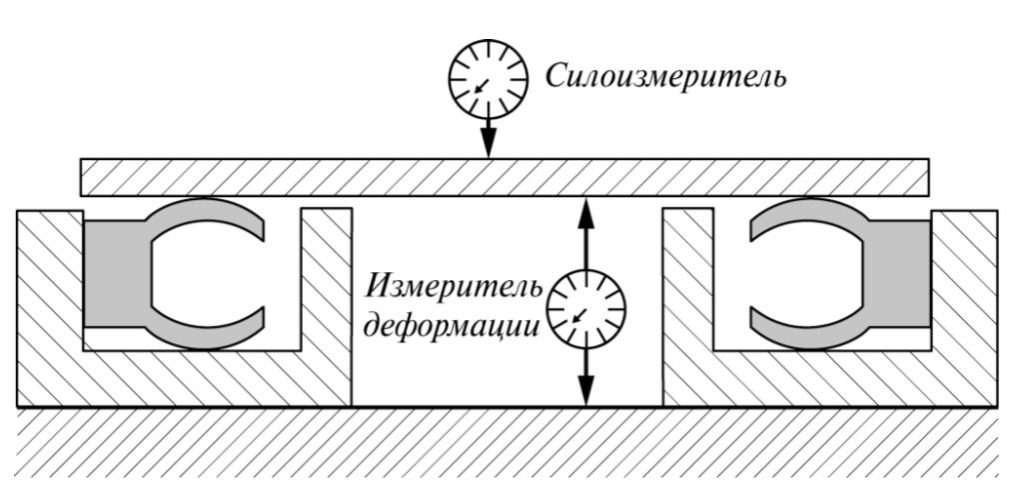
На данном этапе экспериментально определяли усилие при сжатии манжеты между плоскими плитами машины РМ-05, как показано на рис. 3, и рассчитывали погонное усилие манжет с подпружинивающими элементами различной жесткости и оболочками из разных материалов.
Эти данные легли в основу оценки влияния отдельных элементов манжеты при ее сжатии на развиваемое при этом усилие на кромках и в конечном итоге – на герметичность уплотнения. Манжеты, изготовленные из более жестких материалов и снабженные подпружинивающими элементами большей жесткости, имеют крутую зависимость погонного усилия от деформации сжатия (рис. 4).
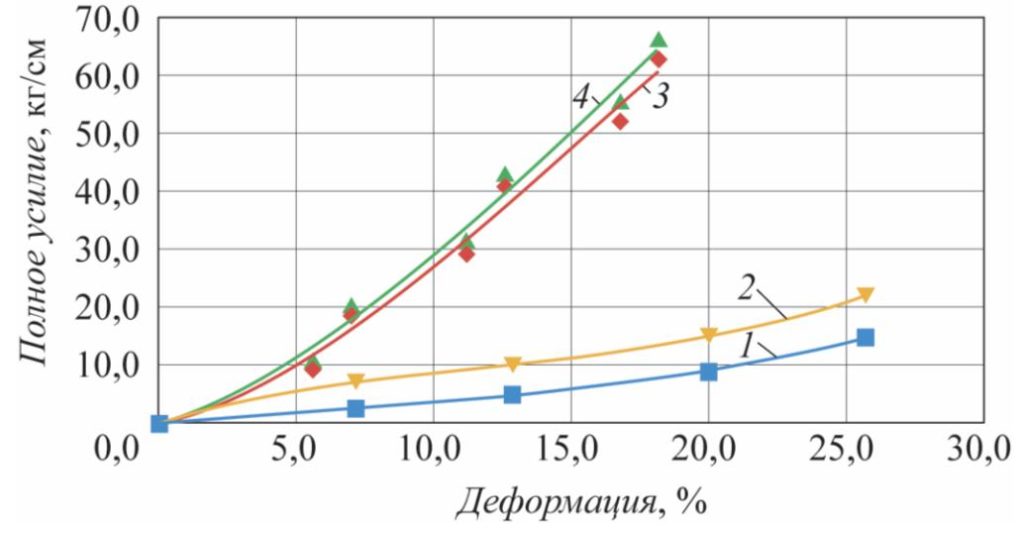
1 – манжета из фторопласта с резиновым кольцом во фторопластовой оболочке (РФК) в качестве подпружинивающего элемента;
2 – манжета из полиэфирэфиркетона с РФК;
3 – манжета из фторопласта со спирально-витой пружиной; 4 – манжета из полиэфирэфиркетона со спиральновитой пружиной
Наименьшей жесткостью обладают манжеты из фторопласта с резиновым подпружинивающим элементом: при 5%-ной деформации погонное усилие на кромках составляет 2,9 кг/см; наибольшей – манжета из РЕЕК со спиральновитой пружиной: при 5%-ной деформации погонное усилие составляет 10 кг/см. Иначе говоря, для создания одного и того же погонного усилия на кромках манжет с разными подпружинивающими элементами необходимо по-разному деформировать манжету, что должно отражаться на размерах мест их установки.
Варьируя необходимые сочетания свойств компонентов, можно получить всю гамму промежуточных зависимостей. Таким образом, подбирая жесткость подпружинивающего элемента, можно получить различное усилие на кромках манжеты и, таким образом, регулировать герметизирующие свойства и целенаправленно, располагая значением необходимого контактного давления, подбирать сочетания элементов МПЭ для достижения требуемого эффекта.
Для улучшения герметизирующих свойств логично стремиться к росту контактного давления. Этого, очевидно, можно достичь за счет роста погонного усилия.
Необходимо, однако, учитывать, что рост погонного усилия, хотя и улучшает герметичность, но в то же время увеличивает трение и изнашивание уплотнения в подвижных соединениях. В неподвижных уплотнениях высокие погонные усилия могут привести к росту ползучести под нагрузкой с потерей герметичности. Таким образом, при выборе уплотнения необходимо тщательно взвешивать возможности, представляемые подпружинивающими элементами с различными характеристиками и материалами для оболочки.
Как известно [5], наилучшими герметизирующими свойствами обладают уплотнения, в которых реализуется эффект самоуплотнения. Он заключается в увеличении контактного давления на сопрягаемых поверхностях с ростом давления среды. МПЭ обладают этим свойством при установке их в посадочное место, что позволяет использовать их при высоких давлениях без увеличения усилия сжатия.
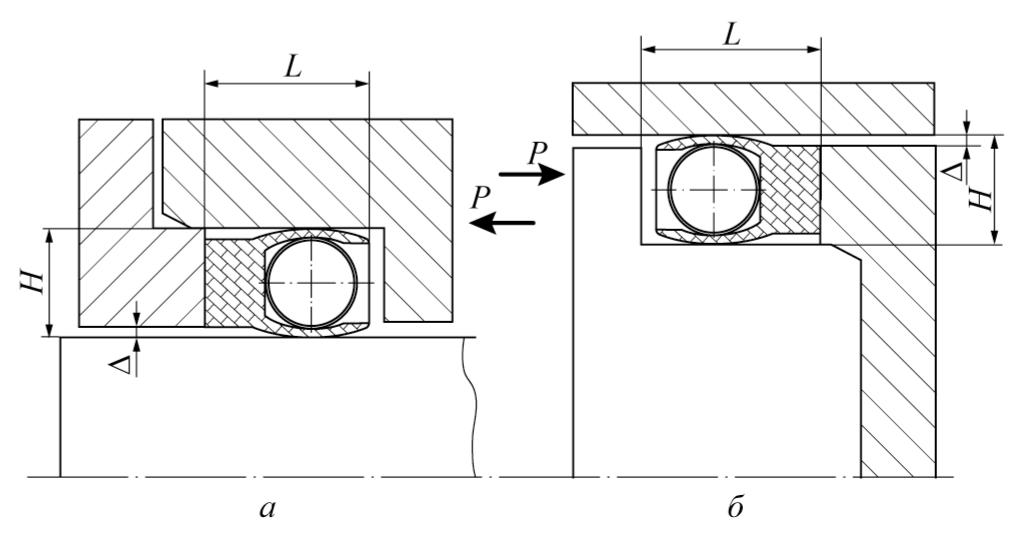
а – уплотнение цилиндра; б – уплотнение поршня
Как и для всех контактных уплотнений, очень важным элементом является соотношение размеров манжет и канавок, в которые их устанавливают. Именно соотношением размеров манжеты и канавки определяется степень деформации кромок манжеты, следовательно, и развиваемое на сопрягаемых поверхностях усилие. На рис. 5 приведена схема установки радиальной манжеты в канавке. Производимые различными предприятиями за рубежом манжеты имеют сечения примерно одинаковых размеров [2–4]. Поскольку существует возможность подбирать упругие характеристики подпружинивающих элементов, размеры канавок для установки манжет, хотя и не стандартизованы, но практически одинаковы у разных производителей. При этом в зависимости от типа применяемой манжеты (см. рис. 2) в канавках одинакового размера мы получим разные контактные давления и соответственно различные характеристики работоспособности и герметичности. Как видно из таблицы, размеры сечений канавок под манжеты зависят только от диаметра манжеты. Размеры сечений манжет и мест их установки практически не связаны с условиями эксплуатации и определяются лишь технологическими возможностями и необходимостью снижать по возможности массогабаритные характеристики уплотнительных узлов. Необходимо отметить, что существует и другая возможность: для получения нужного контактного давления на сопрягаемых поверхностях проектировать и изготавливать канавки исходя из жесткости манжеты.
Рекомендуемые размеры канавок
Диаметр вала, мм | Ширина Н
канавки, мм |
Длина L
канавки, мм |
Зазор
в соединении Δ, мм |
6…250 | 3,1 | 5…9 | 0,05 |
13…300 | 4,8 | 7…12 | 0,05 |
50…500 | 6,1 | 9…14 | 0,07 |
50…1400 | 9,4 | 13…18 | 0,1 |
Поскольку манжеты обладают определенной жесткостью, процесс их установки в канавку без повреждений требует осторожности и применения специального инструмента, кроме того, канавка должна быть правильно спроектирована.
Очень важно для создания герметичных соединений соблюдать требования к шероховатости сопрягаемых поверхностей, так как именно сглаживание неровностей поверхностей и перекрытие каналов утечек при приложении контактного давления создает герметичное соединение.
В общем случае для поверхностей, сопрягаемых с МПЭ, можно рекомендовать как среднюю шероховатость Ra = = 0,4 мкм. При этом шероховатость поверхности для герметизации подвижных соединений должна быть меньше, чем для неподвижных. Также необходимо учитывать, что шероховатость поверхности для герметизации более вязких сред может быть выше, чем при герметизации менее вязких сред. Соответственно, с переходом от герметизации жидкостей к газам требуется снижать шероховатость контактирующих поверхностей. Как было установлено ранее [5, 6], со снижением вязкости среды растет требуемое для создания герметичного соединения контактное давление. Это связано с необходимостью перекрытия все более мелких каналов, образуемых за счет неровностей и шероховатости поверхностей. Снижение исходной шероховатости поверхностей контакта снижает утечки и позволяет достигать герметичности при меньшем контактном давлении.
Оболочки манжет могут изготавливаться из различных полимеров или композиционных материалов; это зависит в первую очередь от условий эксплуатации. Для температур 200…250°С применяют высокотермостойкие полимеры – фторопласт 4, полиэфирэфиркетон, полифениленсульфид. Для криогенных температур их изготавливают из фторопласта 4 и политртифторхлорэтилена (Ф-3).
При эксплуатации манжет в абразивных средах применяют сверхвысокомолекулярный полиэтилен (СВМПЭ).
Однако при этом температурный интервал эксплуатации смещается в сторону более низких температур: от –70 до +100°С при относительно высоком давлении (до 70 МПа).
Для высоких давлений (100 и более МПа) применяют манжеты с оболочкой из высокопрочных полимеров – полиамида, полиэфирэфиркетона, полифениленсульфида и др.
Кроме того, для предотвращения экструзии полимера в зазор при больших давлениях дополнительно устанавливают защитные кольца. Лучшим материалом для получения минимального коэффициента трения, безусловно, является фторопласт 4 с коэффициентом трения f = 0,05…0,1. Таким образом, существует некоторый перечень полимерных материалов и композитов на их основе, позволяющий находить компромиссные вариации свойств.
Как уже было отмечено, существует несколько типов МПЭ, отличающихся подпружинивающими элементами: манжеты с резиновым кольцом круглого сечения; манжеты с резинофторопластовым кольцом; со спирально-витой пружиной из коррозионно-стойкой стали; с пружиной, заключенной во фторопластовую оболочку; с U-образной пружиной из коррозионно-стойкой стали; с пружиной из углеродистой стали с антикоррозионным покрытием. Каждый из вариантов имеет положительные и отрицательные стороны, но наличие различных вариантов позволяет выбрать решение, наиболее приемлемое в конкретных условиях эксплуатации. Для применения в высокоагрессивных средах при температуре от –70 до +200°С и давлении до 50 МПа рекомендуется применять манжеты с резинофторопластовым кольцом в качестве упругого элемента. Манжеты с упругим элементом из хромоникелевых аустенитных сталей хорошо зарекомендовали себя при работе в условиях криогенных температур – ниже –170°С, поскольку в отличие от эластомеров они сохраняют упругие свойства при этих температурах.
Так как в силу конструктивных особенностей манжет подпружинивающий элемент непосредственно контактирует со средой, его изготавливают из коррозионностойких материалов. За рубежом в качестве подпружинивающего элемента применяются резиновые кольца или спиральновитые или U-образные пружины из коррозионно-стойких сталей, а для особо агрессивных сред – из высоколегированных сталей. Однако оба эти решения характеризуются ограниченной стойкостью в агрессивных средах, резиновые кольца ограничены в применении из-за недостаточной хладои теплостойкости, а для повышения коррозионной стойкости стальных пружин приходится применять дорогие марки сталей.
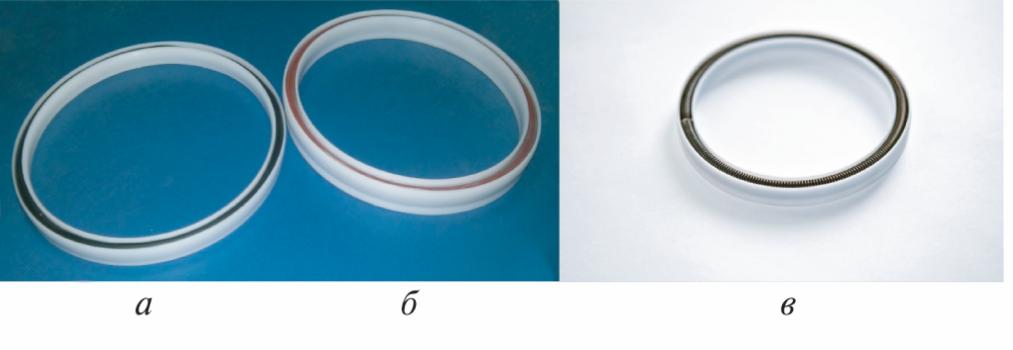
Отличие манжет, производимых ООО «Константа-2» (рис. 6), заключается в высокой коррозионной защищенности подпружинивающего элемента за счет применения сплошной герметичной фторопластовой или иной полимерной защиты. Поскольку для оболочек манжет и подпружинивающих элементов применяются фторопласт и другие высококоррозионно-стойкие материалы, есть все основания полагать, что манжеты будут стойкими в наиболее коррозионно-активных средах, таких как растворы кислот, щелочей, органические соединения, нефтепродукты, могут эксплуатироваться при высоких температурах. Необходимо отметить, что конструкция и исполнение манжет отечественного производства защищена патентами РФ, следовательно, обладает патентной чистотой.
Существенным преимуществом МПЭ является отсутствие залипания уплотнений при остановке оборудования, так как тело манжеты изготавливается из полимерного материала, имеющего низкий коэффициент трения и адгезию к металлическим поверхностям. Необходимо также отметить присущую МПЭ в силу конструктивных особенностей стойкость к декомпрессии.
На наш взгляд, манжеты с подпружинивающим элементом, несмотря на уже сорокалетнюю историю, благодаря появлению новых материалов и технологий переработки, остаются перспективным типом уплотнений, применение которых позволяет решать сложные технические задачи.
Список литературы
- Зерщиков К.Ю. Характеристики и особенности применения полимерных манжет с подпружинивающим элементом//ТПА. 2016. №3 (84). С. 28–30.
- Материалы фирмы Saint Gobain 2015. www.saint-gobain.ru
- Материалы фирмы James Walker 2015. www.james-walker.ru
- Материалы фирмы Effecieme Group 2015. www.effeciemmegroup. com.
- Уплотнения и уплотнительная техника. Справочник/под ред. Голубева А.И., Кондакова Л.А. М., Машиностроение, 1986.
- Zershchikov. K.Yu. Performance parameters of encapsulated sealing rings//Valve World Vol. 21. 2016. Issue 1. P. 70–73.