Автор: В.В. Кондратьев, С.М. Сивуха (ООО «Н-Пром Бюро»), В.Б. Сударев, М.В. Лакиза (ООО «Нева-Теплотехника»).
Опубликовано в журнале Химическая техника №11/2016
По оценкам ряда экспертов, для энергоемких производств, какими являются нефтеперерабатывающие предприятия, доля теплообменного оборудования в капитальных затратах может составлять 30%, а в эксплуатационных расходах доходить до 90%. Такая высокая доля в эксплуатационных расходах объясняется тем, что сразу после ввода в эксплуатацию в оборудовании неизбежно развиваются такие процессы, как коррозия и загрязнение теплообменных поверхностей, что ведет к уменьшению эффективности и снижению надежности.
Как правило, на этапе проектирования теплообменников разработчики закладывают в конструкцию некоторый запас по теплообменной поверхности. Это приводит к переразмеренности теплообменного оборудования, а значит, и увеличивает его стоимость. Согласно статистическим данным, увеличение площади поверхности от 30 до 40% может привести к росту капитальных затрат на 25%.
Запас по поверхности позволяет снизить негативный эффект от загрязнения поверхностей теплообмена, особенно на начальном этапе эксплуатации, но в процессе выработки ресурса теплообменного оборудования он становится недостаточным, чтобы обеспечивать заданную теплопроизводительность.
Периодические очистки требуют вывода из работы теплообменников, которые, как правило, работают в составе технологических установок непрерывного действия. Это часто вызывает падение производительности, сопровождается снижением надежности производства и сопряжено с достаточно большими материальными и временными затратами.
Дополнительные ежегодные расходы из-за загрязнения теплообменных поверхностей оборудования нефтеперерабатывающих заводов оцениваются экспертами в 4,5 миллиарда долларов.
В зависимости от механизма образования отложений различают: кристаллизационное и дисперсное загрязнения, загрязнение продуктами химических реакций, коррозионное и биологическое загрязнения. На практике обычно приходится иметь дело одновременно с несколькими механизмами образования загрязнений, которые почти всегда взаимно усиливают друг друга. Исключением является только сочетание дисперсного и кристаллизационного загрязнений, при котором другие механизмы становятся более слабыми.
Ниже приведены обобщенные данные, отражающие частоту проявления различных механизмов загрязнения, полученные на основании информации от ~1000 промышленных компаний, которые в своей деятельности сталкиваются одновременно с несколькими механизмами загрязнения:
Механизм загрязнения | Доля, % |
Коррозия | 32,4 |
Кристаллизация | 24,5 |
Дисперсный | 18,7 |
Биологический | 13,6 |
Замерзание/Затвердевание | 5,8 |
Химическая реакция | 5,0 |
Рост загрязнения является сложной функцией времени и в зависимости от доминирующих механизмов образования и удаления отложения может быть описан с помощью различных функций: линейной, асимптотической, пилообразной, с убывающей скоростью. Термическое сопротивление слоя загрязнения (отложений на поверхности теплообмена) равняется разности коэффициентов термического сопротивления пластины со слоем загрязнения и без него.
Скорость роста загрязнения зависит от многих параметров рабочих сред (теплоносителей): температуры, скорости движения жидкости, концентрации загрязняющих компонентов, свойств материала и состояния поверхности теплообмена. В таблице показано качественное влияние ряда факторов (параметров, свойств теплоносителей и состояния поверхности) на различные механизмы загрязнения.
Попытки разработать различные модели процесса образования загрязнения предпринимались неоднократно.
Качественное влияние ряда факторов на формирование загрязнений (отложений)
Сейчас существует большой ряд моделей для широкого спектра типов загрязнений, с помощью которых может быть учтено влияние загрязнений еще на стадии проектирования теплообменного оборудования. Следует отметить, что из-за трудностей перенесения результатов экспериментальных исследований по определению термического сопротивления загрязнений на натурные промышленные условия, большинство моделей позволяют дать лишь приблизительную оценку часто с малой степенью достоверности из-за тех допущений, которые принимаются при ее создании.
Для существенного повышения достоверности и применимости расчетных моделей для использования их в процессе создания нового теплообменного оборудования и повышения эффективности его эксплуатации необходимы экспериментальные исследования, максимально приближенные к реальным условиям промышленной эксплуатации.
В настоящее время фирма HTRI (Heat Transfer Research Inc., в России представлена компанией ООО «Нева- Теплотехника»), являясь лидером в исследовании загрязнений теплообменных аппаратов, проводит такие исследования, на базе которых формируются надежные численные модели, позволяющие очень точно рассчитывать скорость формирования и свойства отложений на поверхности теплообмена. Результаты этих исследований интегрированы компанией HTRI в мощный программный продукт SmartPM, который позволяет отслеживать состояние оборудования предприятий, моделировать их работу с предсказанием производительности и формированием рационального графика обслуживания (чистки, ремонты) теплообменного оборудования.
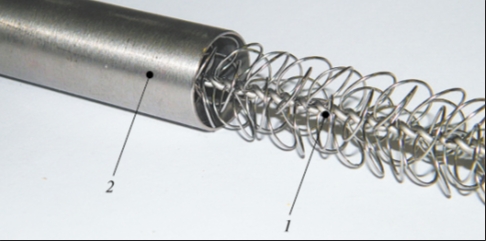
Встроенные в SmartPM динамические модели загрязнения в сочетании с возможностью ввода подробных данных по конструктивному устройству теплообменников, дают возможность прогнозировать изменение характеристик (параметров работы) теплообменников, в том числе связанных и с изменениями схемного решения сетей теплообменников (например, при модернизации и/или замене оборудования).
При внедрении SmartPM на нефтеперерабатывающих заводах персонал получает возможность лучше отслеживать технологические процессы, повысить их эффективность и снизить эксплуатационные расходы, а также уменьшить ущерб, наносимый окружающей среде, благодаря снижению энергопотребления.
Практический опыт показывает, что профилактика обходится значительно дешевле, чем лечение. Поэтому наилучший способ минимизировать потери, связанные с загрязнениями, – это вовсе предотвратить их появление. Загрязнение и коррозия теплообменников могут быть снижены благодаря продуманным проектным решениям, правильному выбору типа теплообменника применительно к заданным условиям его эксплуатации.
Применение специальных инженерных решений, например, внедрение интенсификаторов теплообмена, которые не только предотвратят появление загрязнений, но и существенно повысят эффективность теплообмена, также является действенным способом предотвращения загрязнения.
ООО «Н-Пром бюро» совместно с английской компанией CalGavin разработала и успешно применяет при решении задач, связанных с повышением надежности и эффективности теплообменного оборудования проволочные вставки-турбулизаторы типа hiTran (см. рисунок).
Вставки hiTran, геометрия и плотность которых варьируется в широких пределах, значительно увеличивают теплоотдачу внутри труб за счет направленного воздействия на течение теплоносителя в пристенных слоях, препятствуя при этом образованию загрязнений (отложений).
Системы интенсификации hiTran к настоящему времени установлены более чем в 15 000 трубчатых теплообменниках по всему миру, в том числе и в России.
Во многих случаях установка этих систем позволила существенно поднять эффективность действующих производств и/или значительно сократить капитальные затраты при создании новых, поскольку оборудование с внедренными системами hiTran существенно меньше по массе и габаритам при обеспечении заданной теплопроизводительности.
Для случаев, когда требуется непрерывная работа теплообменного оборудования при нагреве или охлаждении вязких сред при параметрах, вызывающих резкий рост загрязнений, ООО «Н-Пром Бюро» совместно с компанией HRS предлагает использовать специальные кожухотрубные скребковые теплообменные аппараты собственного производства. Данное оборудование существенно уменьшает отложения на стенках труб, повышает эффективность работы и увеличивает межремонтный период.
Применение в промышленности для оценки загрязнений современных методов и средств, основанных на обширных исследованиях, позволяет в настоящее время говорить о возможности существенного снижения запасов по поверхности, традиционно принимаемых при проектировании теплообменного оборудования.
Возможность достоверного предсказания скорости развития и свойств слоя отложений (загрязнений) в процессе эксплуатации при использовании проверенного практикой программного продукта диагностики и мониторинга SmartPM обеспечивает повышение надежности эксплуатируемого теплообменного оборудования, эффективности его использования, способствует снижению эксплуатационных расходов.
Внедрение систем hiTran в трубном пространстве теплообменников нефтеперерабатывающих и химических заводов позволит добиться одновременно существенного снижения загрязнения теплообменных поверхностей оборудования и увеличить его тепловую эффективность.
Применение специальных скребковых теплообменных аппаратов уменьшает отложения на стенках труб, повышает эффективность работы оборудования и увеличивает межремонтный период.