Автор: Д.А. Шильников, Э.Р.Сафаров (компания CHIMEC).
Опубликовано в журнале Химическая техника №11/2016
Коррозия является наиболее частой причиной изнашивания оборудования в нефтеперерабатывающей и нефтехимической отраслях. Рассмотрим причины коррозии и решения компании CHIMEC по защите от коррозии на установках производства этилена.
Проблема коррозии и отложений в системе производства пара разбавления
Система производства пара разбавления (пар, направляемый в печи для турбулизации сырья пиролиза) в производстве этилена наиболее подвержена коррозии из-за относительно высокого содержания кислых веществ в газе, поступающего из печей пиролиза. Наиболее коррозионно-активны H2S, CO2 и органические кислоты (такие как CH3COOH). H2S и CO2 испаряются в испарителе технологической воды, в то время как CH3COOH и другие более тяжелые органические кислоты уносятся в систему производства пара разбавления.
Наиболее подвержены коррозии следующие узлы:
- шлемовая линия главной фракционирующей колонны: это линия, через которую доставляется газ пиролиза из главной фракционирующей колонны в колонну водной закалки. Здесь происходит конденсация первых капель воды, которые имеют низкий pH. Этот участок шлемовой линии можно обрабатывать комбинированным реагентом, который имеет нейтрализующее и пленкообразующее действие;
- колонна водной закалки: pH в сепараторе косвенно регулируется подачей раствора щелочи (NaOH) в поток закалочной воды, которая выводится из сепаратора. В то же время в колонне водной закалки происходит растворение кислых веществ из-за подачи в виде рефлюкса большого количества воды для промывки газа пиролиза. На заводах, которые вместо колонны водной закалки для конденсации пара разбавления и пиробензина используют холодильник, проблемы коррозии значительнее;
- отпарная колонна технологической воды: в верхней части этой колонны может происходить конденсация H2S и CO2, что приводит к коррозии. В нижней части колонны рН иногда регулируется подачей раствора щелочи (NaOH), но это не самое лучшее решение, потому что происходит унос щелочи в систему производства пара разбавления. Если концентрация ионов Na+ в системе производства пара разбавления велика, то может произойти унос ионов натрия вместе с паром разбавления в печи пиролиза, что вызовет щелочную коррозию (растрескивание). По этой причине большинство заводов заменили NaOH соответствующей антикоррозионной обработкой;
- узел производства пара разбавления: так как CO2 и H2S отгоняются в отпарной колонне технологической воды, основными коррозионно-агрессивными компонентами являются органические кислоты, такие как уксусная кислота. Хорошая антикоррозионная обработка обеспечивает регулирование pH как в дренажных стоках, так и в паре разбавления. Обычно используются антикоррозионные реагенты с разной летучестью для нейтрализации кислоты в жидкой и паровой фазе.
Применение NaOH нежелательно в связи с возможностью уноса ионов Na+ с паром разбавления в печи пиролиза.
Решения CHIMEC
Программа реагентной обработки состоит из трех реагентов.
CHIMEC1837M – реагент специально разработан для защиты от коррозии оборудования блока водной закалки и производства пара разбавления. Реагент содержит сильный нейтрализатор, подобранный для оптимального регулирования рН. Активное действие реагента CH1837M основано на защитном действии амина от коррозионной агрессивности кислот. Нейтрализующее действие амина, направленное на защиту от коррозионной агрессивности кислот и для оптимального регулирования, обеспечивает значения рН в испарителе в пределах 8,5…9,5. Использование СН1837М дает возможность оптимизировать подачу NaOH (исключить подачу) в систему, тем самым снизить колебания рН и улучшить разделение между водой и пиробензином, а также уменьшить содержание ионов натрия в паре разбавления.
СНIMEC1236 является мультифункциональным агентом, оказывающим три воздействия:
- нейтрализующее воздействие амина для защиты от коррозионной агрессивности кислот и для оптимального регулирования рН в сепараторе (вода/пиробензин) в пределах 5,5…6,5 – это обеспечивает наилучшее разделение между водой и пиробензином, снижая образование отложений в системе производства пара разбавления;
- поглощение кислорода, который может присутствовать в потоках (кислород может провоцировать коррозию оборудования и легко возбуждать реакцию свободно радикальной полимеризации олефинов);
- воздействие ингибитора полимеризации, который стабилизирует и блокирует радикалы для предотвращения реакции свободно-радикальной полимеризации олефинов.
CHIMEC3469 – это мультифункциональный антизагрязняющий агент, специально разработанный для предотвращения отложений в системе производства пара разбавления. Он оказывает диспергирующее действие на уже образованные отложения. Кроме того, CHIMEC3469 содержит стабилизатор и блокатор радикалов для предотвращения реакции свободно-радикальной полимеризации олефинов, что является основной причиной образования отложений в этой части установки. Применение реагента CHIMEC3469 обеспечивает защиту всего теплообменного оборудования системы производства пара разбавления.
Схема дозирования представлена на рис. 1.
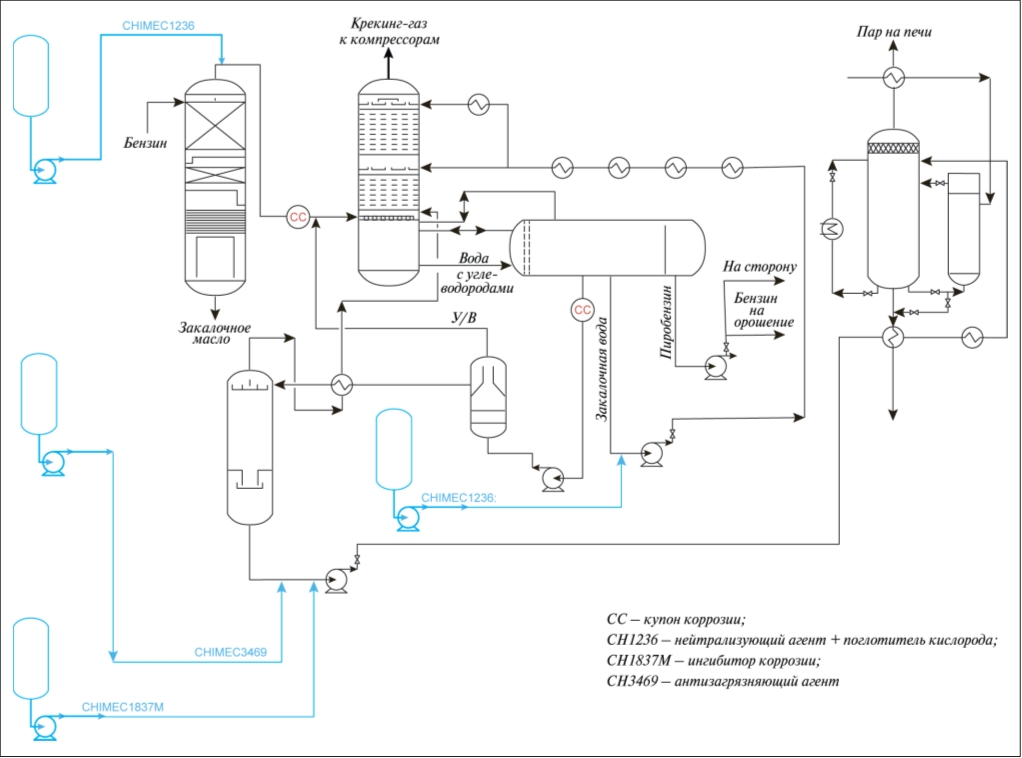
Результаты, достигнутые за счет применения реагентов компании CHIMEC: содержание железа не более 1 мг/дм3 (говорит об очень малой скорости коррозии – менее 0,1 мм/год); в разы снижено потребление щелочи; уменьшена стоимость реагентной обработки за счет применения мультифункциональных реагентов; стабильный рН в сепараторе (вода/пиробензин); снижено содержание натрия в паре разбавления; улучшено разделение в сепараторе (вода/пиробензин) за счет стабильного рН.
Система компримирования пирогаза
Пирогаз, поступающий на компримирование, содержит очень реакционно способные ненасыщенные соединения и соединения, интенсифицирующие процессы коррозии. Олефины и диены предрасположены к полимеризации при высокой температуре и/или в присутствии веществ катализаторов полимеризации, таких как кислородсодержащие соединения и металлы. Результатом могут стать последствия, показанные на рис. 2. Отложения внутри компрессора снижают эффективность компрессии и приводят к увеличению расхода пара в турбину, что может привести к снижению производительности или к сокращению пробега компрессора и всей установки.
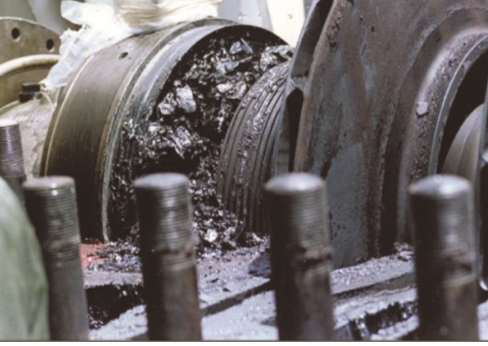
Решения CHIMEC
Специально для предотвращения полимерообразования в компрессоре пиролизных установок разработан реагент CHIMEC3939, который реагирует со свободными радикалами быстрее, чем происходит реакция полимеризации ненасыщенных соединений, таких как стирол, бутадиен и др. В присутствии кислородсодержащих соединений блокатор радикалов реагирует с пероксидами быстрее, чем радикал пероксида реагирует с радикалом углеводорода, тем самым предотвращая полимеризацию в присутствии кислорода. Применение реагента CHIMEC 3939 позволяет поддерживать максимальную нагрузку компрессора.
Схема обработки приведена на рис. 3.
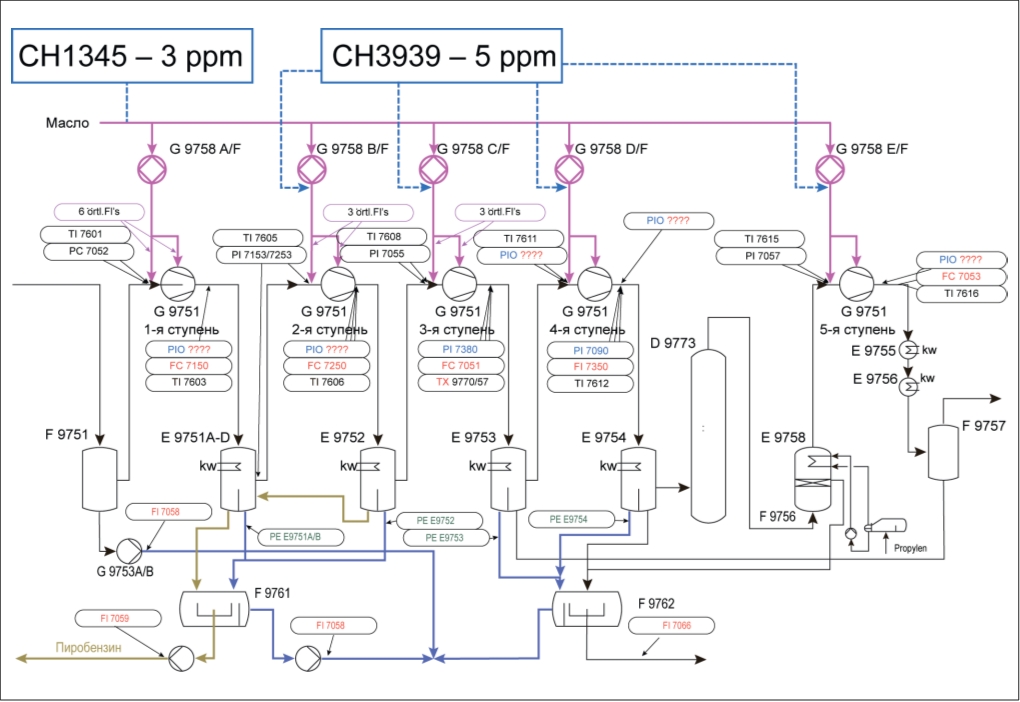
Ингибитор коррозии CHIMEC 1345 образует защитную пленку, которая позволяет защитить систему компримирования пирогаза от его агрессивных компонентов и снизить явление коррозии.
Проблема коррозии на установке производства бензола
В шлемовом оборудовании колонн разделения установки производства бензола наблюдалась сильная коррозия. Данная коррозия может быть вызвана сернистыми соединениями (в том числе H2S), а также низким значением рН. На рис. 4 изображен график степени коррозии в зависимости от рН (углеродистая сталь в среде, содержащей H2S, NH3, HCl, H2O, без ингибиторов).
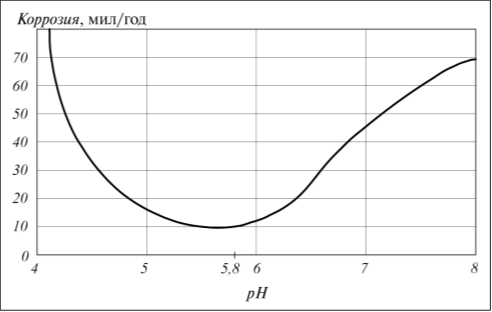
Решения CHIMEC
CHIMEC1839 – пленкообразующий ингибитор коррозии. С помощью электростатической адгезии сложные молекулы могут образовывать защитный слой на поверхности металла любого устройства в верхней части колонны. Такие вещества способны отделять металл от водной фазы и благодаря этому исключать появление коррозии. Типичные молекулы этого семейства состоят из двух боковых структур, одной полярной направленности (металл) и другой – нейтральной углеводородной хвостовой (гидрофобной) структуры.
При этом исключается проникание водорастворимых коррозионно-активных компонентов, но этот процесс должен регулироваться в сочетании с синергетическим эффектом сильного химического нейтрализатора для оптимального снижения процесса коррозии.
CHIMEC 1839 обладает стойкостью (даже в сухих зонах) против коррозии, возникновение которой обусловлено воздейтвием HCl, H2S, O2, органических кислот, CO2, HCN.
CHIMEC 1839 применяется в разных видах антикоррозионной обработки и гарантирует экстремально низкие скорости коррозии (меньше 0,1 мм/год) при малой дозировке реагента СН1839. Явление коррозии проявляется на различных узлах по-разному, и компания
CHIMEC анализирует каждую проблему индивидуально и разрабатывает максимально эффективные для решения данной проблемы реагенты.