Авторы:
Е.И. Тескер, С.Е. Тескер (ООО «Агромаш»),
Л.В. Овчаренко, А.А. Захарьин, И.Г. Макаров, А.Ф. Пыщев (ОАО «ВНИИПТхимнефтеаппаратуры»),
Р.А. Семенов, В.В. Архипов, А.А. Колесов, В.Г. Евстафьев (ООО «РусЭкс»),
П.В. Кононов (ООО «Безопасность в промышленности»).Опубликовано в журнале Химическая техника №11/2015
Одним из перспективных методов получения поверхностных слоев с заданным комплексом механических и физико-химических свойств, учитывающих реальные условия эксплуатации конкретной детали, является электроконтактная наплавка (ЭКН) металлической лентой определенного химического состава. Эффективность применения разработанных технологий ЭКН как при восстановлении изношенных деталей, так и при изготовлении новых подтверждается длительной эксплуатацией насосно-компрессорного оборудования с модифицированными поверхностями.
Применение технологии ЭКН в ремонтном производстве при формировании однослойных защитных коррозионнои износостойких покрытий позволяет значительно повысить ресурс ответственных деталей химического и нефтегазового оборудования, например, роторов центробежных компрессоров и газовых турбин.
Однако при восстановлении рабочих поверхностей изделий с твердостью основного металла более 40 HRC было отмечено, что формируемая композиция наплавленный слой – матрица характеризуется наличием ряда дефектов, отрицательно влияющих на эксплуатационные характеристики деталей (несплавление наплавленного слоя с подложкой, поры, раковины, трещины и др.).
Оптимизация режимов ЭКН позволила исключить ряд таких дефектов, как несплавление, поры, раковины.
Однако наиболее опасные с точки зрения снижения конструкционной прочности материала дефекты в виде трещин, образующихся в наплавленном слое и распространяющихся через границу сплавления в основной металл, исключить не удалось. Было установлено, что в данном случае сказывается отрицательное влияние наплавляемой поверхности детали с высоким уровнем растягивающих напряжений, возникающих в результате предварительной упрочняющей обработки, например, объемной или поверхностной закалки.
Очевидно, снижение уровня остаточных напряжений на рабочей поверхности изделия позволит значительно улучшить качество модифицируемых слоев. Данная проблема может быть решена посредством введения в технологический процесс ЭКН предварительного нанесения на рабочую поверхность детали подслоя лентой из низкоуглеродистой конструкционной стали, например ВСт3кп.
В данной статье приведено описание свойств многослойной композиции поверхностный слой – основной металл, полученный при ЭКН рабочих поверхностей деталей с исходной высокой твердостью.
Исследования проводили на образцах, изготовленных из среднеуглеродистой стали 40, прошедшей объемную закалку и низкий отпуск. Электроконтактную наплавку осуществляли на специальной установке по специальной технологии, коррозионно-стойкой лентой 20Х13 толщиной 0,7 мм по предварительно нанесенному на рабочую поверхность деталей подслою из низкоуглеродистой конструкционной ленты ВСт3кп толщиной 0,5 мм.
Контроль качества наплавленной поверхности осуществляли методом цветной дефектоскопии (ОСТ 26-5–88).
Микростроение наплавленного слоя изучали на микроскопе МИМ-10 при 100-кратном увеличении. Микротвердость измеряли прибором ПИТ-3 при нагрузке 1 Н.
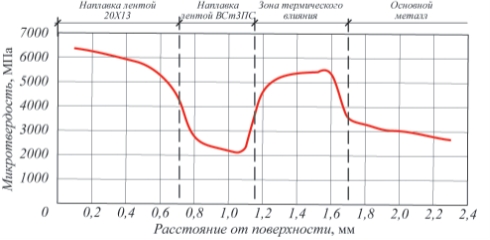
В результате металлографических исследований шлифов установлено, что после предварительной ЭКН на поверхность образца ленты из стали ВСт3пс из-за малой устойчивости переохлажденного аустенита в структуре наплавленного слоя не наблюдается образования мартенсита. Однако при высокоскоростном охлаждении в массе металла, характерном для технологии ЭКН, происходит сильное переохлаждение аустенита, образовавшегося при нагреве, что уменьшает количество свободного феррита и сопровождается образованием тонкой феррито-цементитной структуры, которая при относительно высокой прочности сохраняет и достаточную пластичность. При этом хорошая свариваемость стали ВСт3пс при наплавке обеспечивает прочную металлургическую связь с основным металлом. Благодаря низкому содержанию углерода в стали и высокой пластичности в наплавленном слое не происходит образования трещин при нагреве и охлаждении материала.
С целью формирования требуемых эксплуатационных свойств рабочих поверхностей деталей насосно-компрессорного оборудования на предварительно наплавленный слой осуществляли ЭКН лентой из стали 20Х13.
После двухслойной наплавки были проведены металлографические исследования и измерение микротвердости композиции поверхностный слой – основной металл.
Установлено, что в поверхностном наплавленном лентой из стали 20Х13 слое до глубины 0,4 мм в результате протекания полного γ ↔ α превращения формируется однородная мелкодисперсная структура мартенсита с равномерно распределенными карбидами хрома. Данная структура характеризуется высокой микротвердостью, которая составляет 6500…6100 МПа (см. рисунок).
С увеличением расстояния от поверхности до границы сплавления с подслоем из ленты ВСт3пс происходит плавное снижение микротвердости до 4500 МПа.
Данный эффект можно объяснить наличием в указанной зоне наплавленного слоя неоднородной структуры, состоящей из мартенсита, троостита и феррита, образовавшейся в результате металлургического перемешивания двух лент различного химического состава.
Микротвердость по толщине подслоя из ленты ВСт3пс составляет 2800…2100 МПа, что характерно для низкоуглеродистой стали с феррито-цементитной структурой.
В зоне термического влияния на глубине 1,15…1,7 мм в результате нагрева матрицы в процессе наплавки выше критической точки АС3 и последующего скоростного охлаждения происходит формирование мартенситной структуры, что сопровождается повышением микротвердости до 4700…5200 МПа, характерной для микротвердости среднеуглеродистой стали 40 после объемной закалки и низкого отпуска. С дальнейшим увеличением расстояния от поверхности микротвердость плавно снижается до значения 2500 МПа, характерного для нормализованной стали 40.
При металлографических исследованиях микрошлифов установлено, что в сформированной композиции полностью отсутствуют дефекты в виде трещин, пор и несплавлений между наплавленными слоями и основным металлом.
Следует отметить, что наплавленный слой из стали 20Х13 в результате образования мелкодисперсной структуры мартенсита с равномерно распределенными карбидами хрома должен обладать высокой износостойкостью. При этом вязкий подслой из ленты ВСт3пс с феррито-цементитной структурой может служить своеобразным демпфером при работе деталей в условиях контактных циклических нагрузок и препятствовать возможному распространению в основной металл возникающих в процессе эксплуатации трещин в результате их торможения при прохождении через структурные слои с различными физико-механическими свойствами.
Разработанная технология многослойной ЭКН внедрена в ремонтном производстве при восстановлении геометрических размеров и эксплуатационных свойств широкой номенклатуры деталей насосно-компрессорного оборудования и газовых турбин в ОАО «Каустик», ОАО «Химпром» и ОАО «Астраханьгазпром».