Автор: А.В. Солдатов, Н.А. Шестаков (ОАО «НИИК»)
Опубликовано в журнале Химическая техника №7/2017
Последние несколько лет для рынка минеральных удобрений были непростыми. Строительство во всем мире новых агрегатов по выпуску карбамида и реконструкции, связанные с наращиванием мощностей существующих производств, привели к серьезному усилению конкуренции на мировом рынке, что обусловило значительное снижение цен на удобрения. В сложившейся ситуации привлечение существенных инвестиций в строительство новых производств могут позволить себе немногие производители.
Рассмотрим опыт ОАО «НИИК», как в минимальные сроки и при минимальных капитальных затратах можно спроектировать и построить совершенно новое эффективное и конкурентоспособное производство карбамида.
Необходимо отметить, что новое производство карбамида ориентировано на выпуск раствора карбамида с концентрацией не менее 72%, предназначенного для последующей его переработки в КАС (карбамидно-аммиачная смесь). В последнее время жидкое азотное удобрение КАС на основе водных растворов карбамида и аммиачной селитры получает все более широкое распространение, что подтверждает динамика роста производства и экспорта КАС в России.
Причина популярности КАС заключается прежде всего в его уникальности – это единственное удобрение, которое содержит в своем составе три формы связанного азота, а именно амидную, аммонийную и нитратную.
Помимо этого, среди преимуществ для потребителей можно отметить, что раствор КАС можно использовать практически в любых климатических зонах, в том числе и засушливых. При его использовании обеспечивается более равномерное внесение и сокращаются технологические затраты благодаря возможности совмещения внесения КАС с внесением пестицидов и других жидких минеральных удобрений.
Если говорить о преимуществах для производителей, то нельзя не отметить, что при проектировании новых производств и реконструкции действующих, которые ориентированы на выпуск КАС, нет необходимости включать в технологическую схему дорогостоящие узлы выпаривания, грануляции и очистки сточных вод. Это в значительной мере снижает капитальные затраты и расход энергоресурсов, а также минимизирует атмосферные выбросы и стоки, обеспечивая высокую экологичность производства.
Основными предпосылками к созданию нового агрегата послужило желание предприятия расширить производство по выпуску КАС, наличие на производстве дополнительных объемов жидкого аммиака и резерв компрессии диоксида углерода после проведенной реконструкции, а также наличие резервной колоны синтеза карбамида.

Ни для кого не секрет, что зачастую цеха производства карбамида, работающие по технологии с полным жидкостным рециклом, имеют несколько агрегатов и резервную колонну синтеза карбамида. Колонна синтеза – это основной и самый дорогостоящий аппарат технологической схемы. Это единственный аппарат высокого давления в данной схеме, и его стоимость составляет существенную часть от общей стоимости агрегата карбамида.
Подробнее рассмотрим проектируемый агрегат карбамида. В его основу положена технология ОАО «НИИК» URECON®2006, которая создана для агрегатов карбамида АК-70 и представляет собой усовершенствованную схему с полным жидкостным рециклом. Технология основана на многолетнем опыте в проведении реконструкций агрегатов карбамида с полным жидкостным рециклом и использует принципиально новые аппараты и устройства с оптимизированной гидродинамикой движения потоков внутри аппаратов и высокой эффективностью тепло- и массообмена.
Одним из основных преимуществ схемы является наличие всего одного аппарата высокого давления – реактора синтеза карбамида. Синтез протекает при давлении 200 атм и температуре 190…195°С. В реакторе устанавливается комплект внутренних устройств (КВУ), что позволяет получить максимальную степень конверсии сырья в карбамид в интенсивных условиях протекания процесса. Плав синтеза из реактора последовательно проходит две ступени дистилляции: среднего и низкого давления. Каждая ступень дистилляции состоит из одного аппарата – дистиллятора, совмещающего колонну дистилляции, стриппер и сепаратор. Применение высокоэффективной дистилляции позволяет уменьшить рецикл воды в реактор. Для возврата в узел синтеза избыточного аммиака установлен узел рецикла аммиака, включающий промывную колонну, аммиачные конденсаторы и концевой абсорбер. После второй ступени дистилляции раствор карбамида поступает в рекуператор форвыпарки. Окончательное концентрирование раствора карбамида происходит на двухступенчатой выпарке с пониженным потреблением водяного пара, а полученный высококонцентрированный плав карбамида направляется в отделение получения товарных форм.
Агрегат по схеме URECON®2006 имеет современные технико-экономические показатели: расходный коэффициент по NH3 – 567…570 кг/т; по СО2 – 734…750 кг/т; по пару – 0,80…0,85 Гкал/т.
Реконструкции по данной технологии уже реализованы на многих производственных площадках России и СНГ на агрегатах мощностью менее 1000 т/сутки. В данном случае при проектировании нового агрегата учтен весь имеющийся опыт эксплуатации существующих агрегатов данной технологии и применены меры, направленные
на повышение надежности и простоты эксплуатации.
на повышение надежности и простоты эксплуатации.
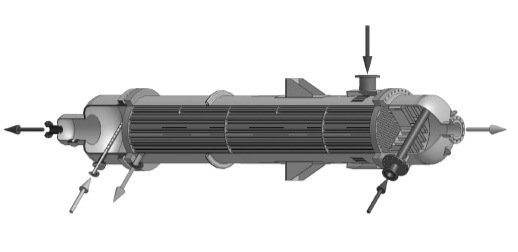
Производительность проектируемого агрегата составляет 600 т/сутки (на чистый карбамид) и ограничена объемом существующей резервной колонны синтеза. Проектная производительность данной колонны составляла не более 270 т/сутки.
С учетом установки в колонну синтеза высокоэффективных внутренних устройств конструкции ОАО «НИИК», позволяющих максимально эффективно использовать объем реактора синтеза, производительность составила 600 т/сутки при сохранении значения степени конверсии, близкого к равновесному значению. Комплект внутренних устройств включает массообменные тарелки, способствующие приближению режима в реакторе к режиму идеального вытеснения как наиболее благоприятного для протекания процесса синтеза карбамида, а также насадку продольного секционирования и вихревой смеситель, которые обеспечивают эффективное смешение исходных компонентов.
В вихревом смесителе происходит первоначальное диспергирование газа и образование газожидкостной смеси. Его задача – организовать на входном участке реактора эффективный контакт фаз в режиме, по возможности близком к идеальному смешению, без образования застойных зон и обеспечить интенсивное диспергирование газа для создания однородной мелкопузырьковой структуры газожидкостного потока и развитой межфазной поверхности.
Вихревой смеситель работает по принципу ступенчатой вихревой камеры с тангенциальным вводом реагентов и крепится к штуцерам ввода реагентов в реактор. Особенностями данной конструкции являются, во-первых, большой угол раскрытия выходной струи, во-вторых, интенсивное диспергирование газа за счет использования эффекта потери гидродинамической устойчивости закрученной газожидкостной струи, в-третьих, отсутствие эрозионного износа смесителя вследствие локализации газа у оси закрученной струи.
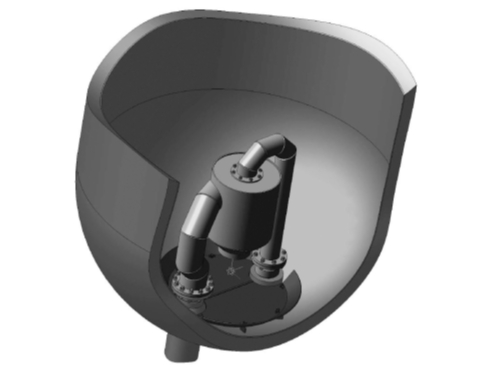
Насадка продольного секционирования служит для максимального связывания исходных реагентов в карбамат аммония. Высокая скорость и полнота связывания газообразного сырья в жидкофазный карбамат аммония обеспечивают приближение общего гидродинамического режима в реакторе синтеза к оптимальному.
Насадка – разборная и состоит из секций, которые размещают на общей опорной раме, подвешенной на кронштейнах. Каждая секция состоит из вертикальных контактных устройств, выполненных из труб. Газожидкостная смесь через входные отверстия поступает в подъем-ные элементы, где газовая и жидкая фазы контактируют в узких каналах в условиях восходящего прямотока. Далее газожидкостной поток выходит из контактных устройств над опорной решеткой и поступает в зону протекания реакции образования карбамида, которая оборудуется массообменными тарелками.
Тарелки препятствуют продольному перемешиванию реакционной смеси по высоте колонны, а также способствуют дополнительному диспергированию реакционной смеси через отверстия в полотне тарелки.
Несмотря на снижение времени пребывания компонентов в колонне синтеза с ростом производительности более чем в 2 раза от проектного значения комплект внутренних устройств позволяет интенсифицировать процесс образования карбамида и обеспечивает стабильную работу агрегата при отсутствии повышенной нагрузки на узлы возврата непрореагировавших компонентов.
Ключевыми аппаратами технологической схемы URECON® 2006 являются высокоэффективные пленочные аппараты дистилляции среднего и низкого давления, которые объединяют три аппарата: подогреватель, массообменную колонну и сепаратор. Конструкция аппаратов позволяет снизить число единиц технологического оборудования в схеме и минимизировать расход пара при повышении степени отгонки непрореагировавших компонентов.
Окончательное концентрирование раствора осуществляется в узле форвыпарки, основным аппаратом которого является теплообменник-рекуператор, работающий за счет использования тепла газов дистилляции сред-него давления. Учитывая малый температурный напор, а также необходимость исключения образования биурета, процесс выпаривания раствора карбамида осуществляется в аппарате с падающей пленкой. Аппарат имеет цилиндрический вертикальный корпус, внутри которого установлен пучок вертикальных труб, закрепленных между трубными досками. Над верхней трубной доской расположена сепарационная камера. На верхних концах труб вертикального пучка установлены специальные устройства для формирования пленочного режима. Упариваемый раствор карбамида после дистилляции низкого давления вводится в распределительную камеру, где распределяется по теплообменным трубкам специальными устройствами и стекает тонкой пленкой по внутренней поверхности труб вертикального пучка. Благодаря пленочному режиму процесс упаривания протекает очень интенсивно даже при малой разнице температур и с большой скоростью. Горячие газы дистилляции через распределительную камеру направляются в нижнюю часть межтрубного пространства теплообменника.
Газожидкостная смесь, поднимаясь, омывает пучок вертикальных труб, отдавая тепло упариваемому раствору, протекающему по трубкам.
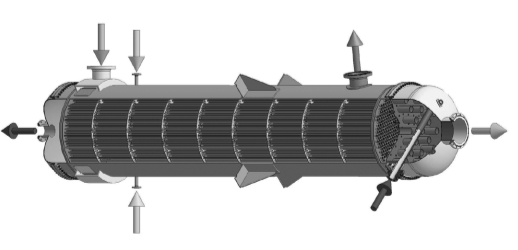
Процесс конденсации-абсорбции газов дистилляции среднего давления в большинстве цехов карбамида с жидкостным рециклом завершается в промывной колонне с выносным барботером, где выделяющуюся теплоту снимают оборотной охлаждающей водой.
Схема рекуперации тепла газов дистилляции и использование высокоэффективного тепло- и массообменного оборудования позволяет в значительной степени снизить энергозатраты на выпуск продукта. Расходные коэффициенты энергоресурсов на 1 т готового продукта с учетом отсутствия стадий выпаривания, грануляции и очистки сточных вод составляют: расход пара на технологические нужды – не более 0,74 Гкал/т, расход электроэнергии – не более 50 кВт/т.
Благодаря отсутствию в технологической схеме стадии выпаривания и конденсации образуется минимальное количество стоков, требующих очистки, которые перерабатываются в существующей на производстве системе очистки сточных вод.
Еще одной отличительной особенностью технологической схемы является отсутствие газообразных «сдувок» аммиака в смежные производства (производство аммиачной селитры или КАС).
В связи с закрытием «старых» цехов производства аммиачной селитры, а также учитывая текущую тенденцию регулирования и контроля за состоянием окружающей среды, поднимается вопрос о возможности работы «старых» цехов карбамида в автономном режиме (без передачи газовых сдувок в смежные цеха) и снижении вредного влияния производства карбамида на природу. Это возможно благодаря узлу абсорбции среднего давления (узел замыкания «сдувок»), позволяющему сконденсировать весь газообразный аммиак внутри агрегата. При этом степень улавливания аммиака находится на высоком уровне, несмотря на высокое количество инертов в газовой фазе.
Узел замыкания газовых «сдувок» обеспечивает автономность агрегата карбамида с возможностью работы независимо от смежных производств. Установка абсорбера и сепаратора после последнего по ходу газа конденсатора аммиака позволяет возвращать аммиачную воду в промывную колонну и далее в узел синтеза.
Несконденсировавшийся в конденсаторах аммиак и инерты из последнего по ходу конденсатора аммиака подаются в межтрубное пространство абсорбера через барботажные устройства.
Абсорбер состоит из кожухотрубного теплообменника, совмещенного с насадочной частью. Насадочная часть заполнена металлическими кольцами с целью сведения к минимуму свободного объема, в котором возможно образование взрывоопасной смеси из водорода и кислорода, входящих в состав инертов.
При строительстве агрегата с нуля мы имеем возможность реализовать сразу весь свой опыт и знания, а также применить весь спектр последних технических решений. При этом применяются современные технологические решения, отвечающие принципам надежности, ресурсо- и энергосбережения.
Наличие резервной колонны синтеза при отсутствии дополнительного оборудования высокого давления, а также отсутствие в схеме узлов выпаривания, грануляции, очистки сточных вод и сокращение единиц оборудования за счет установки объединенных высокоэффективных аппаратов позволили снизить капитальные затраты на строительство и сроки строительства агрегата до минимума.
При этом максимальное использование объема колонны синтеза, использование высокоэффективного оборудования и рекуперация тепла газов дистилляции позволяет обеспечить высокие технико-экономические показатели работы агрегата.
Стоит отметить, что агрегаты производства карбамида, построенные еще в 1970-х годах, работают на производственных площадках страны по сей день. Спроектированный ОАО «НИИК» новый агрегат с учетом многолетнего опыта работы в области карбамида, с применением современного оборудования и проверенных технических решений будет приносить прибыль и служить верой и правдой
не один десяток лет.
не один десяток лет.