Автор: А.В. Щербаков (ООО «НПО «Курс»).
Опубликовано в журнале Химическая техника №2/2015
В современных условиях отечественное машиностроительное предприятие сталкивается с большим набором проблем, преодолевать которые становится все труднее. Вот лишь неполный их перечень этих проблем:
- инфляция издержек, т.е. опережающий рост цен на сырье по сравнению с ростом цен на машиностроительную продукцию. За последние 4…5 лет произошел скачок цен практически на все сырьевые составляющие: на медь в 4 раза, на стальной прокат в 2,5 раза, на чугун в 3 раза, на бензин в 2 раза, на электроэнергию в 2 раза и т.д. Рост цен на продукцию машиностроения за этот же период составил 40–60%;
- отсутствие дешевых длинных кредитов, что лишает предприятия возможности технологического перевооружения для успешной конкуренции с импортом;
- катастрофическая ситуация с рабочей силой (Россия перестала быть страной с высококвалифицированными рабочими кадрами).
Кроме ряда «приоритетных» отраслей (авиастроение, судостроение, вагоностроение) машиностроение в целом никого из руководства страны не интересует. В то же время саморегулирование не работает в силу отсутствия исторического опыта, т.е. интересы отечественных обрабатывающих отраслей никто не отстаивает, что в условиях рыночной экономики неизбежно приведет к их стагнации.
Между тем даже в столь тяжелых экономических условиях находятся предприятия, которые умудряются не только выживать, но и создавать машиностроительную продукцию, успешно конкурирующую с самыми современными зарубежными аналогами. Это происходит в том случае, если на предприятии внедряется современная технология, опережающая по техническим возможностям технологии конкурентов (в том числе зарубежных).
Один из подобных примеров описан в данной статье.
В ООО «НПО «Курс» были освоены две самые современные технологии и внедрены в производство новые композиционные материалы. Благодаря этому компания «Курс» смогла освоить производство насосов, превосходящих по своим параметрам самые современные импортные образцы.
Прежде всего расскажем об уникальных материалах, используемых при создании самого современного насосного оборудования.
Новые технологии – новые материалы
Речь идет о линейном полифениленсульфиде, производимом фирмой «Тикона» (Германия), более известным под торговой маркой Фортрон. Этот материал сам по себе имеет уникальные свойства, а после армирования стеклянным или минеральным волокном приобретает удивительную прочность и стойкость против разного рода воздействий (климатические, химические и др.).
Одним из неоспоримых преимуществ фортрона является его термопластичность, т.е. широкая возможность переработки на термопластавтоматах и вторичное использование.
Когда мы говорим о применении композиционных материалов, то речь идет о применении самых современных смесевых композиций – стеклонаполненных, минералонаполненных, угленаполненных и т.д. Эта область практических знаний очень бурно развивается в последнее время, и ежегодно потребителям предлагаются современные материалы с принципиально новыми свойствами.
По прочности современные композиты мало уступают чугуну, что наряду с малым удельным весом делает детали из них конкурентоспособными со стальными или чугунными, но только в том случае, когда нагрузка преимущественно динамическая (например, от центробежных сил). В местах с большой статической нагрузкой композиционные детали можно армировать стальными закладными элементами, позволяющими перераспределять нагрузку и исключить деформацию и разрушение композитов, при этом они становятся пластичнее чугуна в ~7,5 раз.
С 2005 г. в ООО «НПО «Курс» была освоена новейшая технология получения цельнолитых пластмассовых колес из фортрона. Фортрон обладает всеми технологическими преимуществами термопластичных материалов и практически лишен их недостатков. Основные свойства фортрона:
- рабочая температура – от – 40 до +240°С;
- высокая прочность, сравнимая с чугуном (до 200 МПа);
- повышенный по сравнению с другими термопластичными материалами модуль упругости (до 20 ГПа);
- высокая химическая стойкость и одновременно нейтральность по отношению к окружающей среде, что дает возможность использовать его в контакте с продуктами питания;
- незначительное изменение механических свойств при изменении температуры;
- сохранение механических свойств в течение длительного времени (до 100 тыс. ч);
- предельно низкое водопоглощение (~0,02%).
Наряду со своими уникальными свойствами фортрон, наполненный стекловолокном, имеет достаточно высокую абразивную стойкость. Так, при сравнительных испытаниях изделия из фортрона показали в 4 раза более высокую стойкость против абразивного изнашивания, чем аналогичные детали из нирезиста.
Применение композиционных материалов, подобных фортрону, открывает широкие возможности по созданию конкурентных образцов различного рода машиностроительной продукции.
Литье композиционных материалов по выплавляемым стержням
Одним из основных преимуществ насосов, производимых ООО «НПО «Курс», является цельнолитое рабочее колесо, отлитое по технологии выплавляемых стержней.
Цельнолитое рабочее колесо из фортрона – новое слово в насосостроении. Новая технология литья позволяет получать высококачественные колеса, не требующие балансировки, что обеспечивает равномерный и тихий ход. Кроме того, система отверстий малого диаметра в рабочем колесе уменьшает осевое усилие и тем самым снижает нагрузку на подшипники электродвигателя, что также ведет к повышению срока службы и надежности насоса. Такие колеса нельзя получить методом обычного литья, так как их геометрия настолько сложна, что отдельные внутренние элементы колеса просто невозможно получить ни с помощью разъемов, ни с помощью «знаков».
Суть метода литья по выплавляемым стержням заключается в следующем. Из специального металла отливают стержни, формирующие внутренние полости изделия.
Эти полости могут быть любой сложности и конфигурации. Затем стержни вставляют в пресс-форму в качестве закладных элементов и заливают композиционным материалом в термопластавтомате. Полученное изделие вместе со стержнями помещают в емкость со специальным разогретым до определенной температуры маслом. В этой среде происходит выплавление стержней, и изделие получает искомую форму.
Металл собирается из емкости с маслом и может быть использован вторично при изготовлении стержней.
Данная технология позволяет получить цельнолитое изделие с внутренними полостями любой формы, с точностью до 0,05 мм соответствующее исходной модели.
Подобная точность играет очень важную роль при изготовлении особо ответственных деталей (в нашем случае – рабочие колеса насоса). Именно точность при изготовлении рабочего колеса обеспечивает насосу высокий КПД и бесшумность работы.
Данная технология была разработана в СССР еще в 1960-х гг., но не нашла промышленного применения из-за отсутствия термостойких пластичных материалов.
И только в конце 1990-х гг. после появления материалов, подобных фортрону, технология литья по выплавляемым стержням обрела «второе дыхание» и получила промышленное применение.
Эта технология является уникальной не только для России; в мире в настоящее время есть очень немного предприятий, освоивших подобную технологию в серийном производстве.
Литье металла методом газифицированных моделей
Еще одним достижением ООО «НПО «Курс» стало внедрение в серийное производство технологии литья металла по газифицируемым моделям. Данная технология не является чем-то необычным.
Более того, на Ганноверской выставке в 2007 г. около половины предприятий, представлявших продукцию литейного производства, демонстрировали преимущества именно этого метода литья, т.е. речь не идет о некоем уникальном методе, а о технологии наиболее передовой и перспективной с точки зрения развития литейного производства.
Суть данной технологии заключается в следующем. С помощью вспененного полистирола создается модель один к одному соответствующая будущей отливке. Процесс получения модели состоит из двух этапов. На первом полистирол закладывают в специальную металлическую форму (наподобие пресс-формы). Затем форму помещают в автоклав, где происходит вспенивание полистирола и получение модели. Модель устанавливают в специальную опоку и заливают расплавленным металлом. Под действием высокой температуры полистирол сгорает, а образовавшиеся газы удаляют с помощью вакуума (отсюда и название – литье по газифицируемым моделям), а металл заполняет образовавшуюся пустоту.
После остывания получается деталь, соответствующая исходной модели с точностью до 0,1 мм. Таким образом, данная технология позволяет отливать изделия с высокой точностью и свести к минимуму (а в отдельных случаях и исключить) механическую обработку.
Основные преимущества метода:
- высокая точность отливки (до 0,1 мм);
- возможность получать детали практически из любого металла (чугун, сталь, медь, бронза, алюминий, титан и др.);
- исключение «человеческого фактора» при отливке – деталь точно соответствует модели, которая отливается в специальной форме;
- относительная простота и дешевизна технологии по сравнению с другими методами точного литья;
- высокое качество поверхности отливки, не требующее зачистки и специальной обработки.
С помощью технологии литья по газифицируемым моделям в ООО «НПО «Курс» получают все корпусные детали насоса (корпус, кронштейн и др.). Отлитый с помощью данного метода корпус не требует зачистки, подвергается минимальной механической обработке, а главное, его проточная часть полностью соответствует требуемой геометрии. Таким образом, в сочетании с цельнолитым колесом из фортрона, удается получить наилучшие характеристики насоса, в том числе высокий КПД и низкий шум.
Насосы КММ-Е нового поколения для нефтепродуктов и легко воспламеняющихся жидкостей
Насосы, перекачивающие нефтепродукты и другие легко воспламеняющиеся жидкости, в соответствии с ГОСТ Р 52743–2007 (EN 809:1998) «Насосы и агрегаты насосные для перекачки жидкостей. Общие требования безопасности» должны иметь ряд конструктивных особенностей. Особые требования предъявляются к деталям насоса, соприкасающимся с перекачиваемой средой. НПО «Курс» производит насосы КММ-Е (рис.1), полностью соответствующие требованиям ГОСТ Р 52743–2007 и имеющие Разрешение Федеральной службы по экологическому, технологическому и атомному надзору на применение оборудования на опасных производственных объектах.
Насосы КММ-Е изготавливают с применением самых современных технологий. Так, корпусные детали получают методом литья металла по газифицированным моделям. Рабочие колеса насосов КММ-Е получают из токопроводящего композиционного материала методом литья по выплавляемым стержням. Кроме того, насосы КММ-Е имеют ряд конструктивных особенностей, повышающих их надежность и обеспечивающих безопасность при эксплуатации.
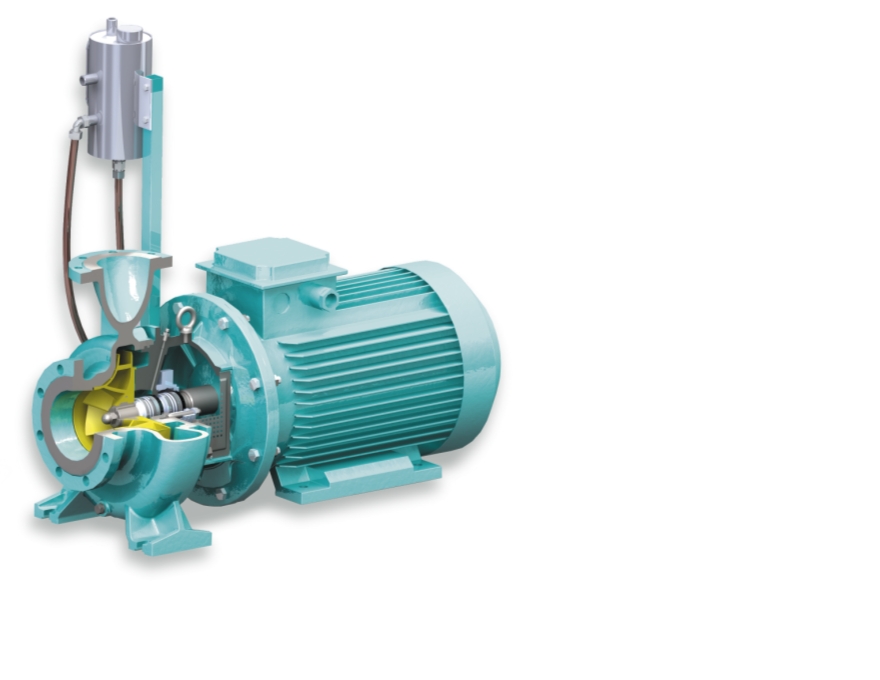
За счет чего удалось достичь столь высоких результатов? В конструкторском бюро ООО «НПО «Курс» при проектировании насосов КММ-Е применяется программное обеспечение, позволяющее формировать и оперативно модифицировать большое число вариантов рабочих каналов, рассчитывать с минимальными затратами времени гидродинамические параметры потоков и, таким образом, проектировать оптимальные проточные части насоса с уменьшенными энергетическими потерями при перекачивании жидкости (рис. 2, 3). Это программное обеспечение соответствует современному мировому уровню и может служить для создания насосов с максимальным КПД, пониженным шумом и вибрацией.
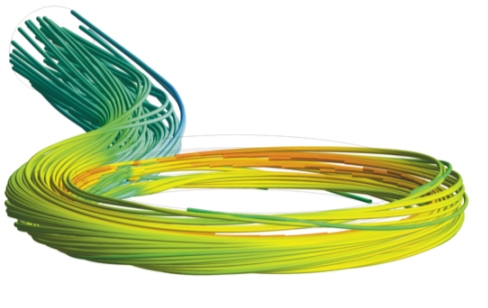
Применение современного моделирования позволило исключить вихреобразование в проточной части насоса. Но добиться этого в серийном производстве удалось только благодаря новым материалам и новым технологиям. Благодаря оптимизации формы рабочих органов насоса и применения композиционного материала для изготовления рабочего колеса в насосах практически незаметны шум и вибрация (находятся на уровне этих характеристик приводного электродвигателя).

Бескавитационное обтекание, рассчитанное с помощью компьютерного моделирования, реализовано на практике путем изготовления композиционного колеса, отлитого методом выплавляемых стержней, и металлического корпуса, литьем по газифицируемым моделям. Этот сплав уникальных технологий позволил создать гамму насосов, превосходящих по КПД и отечественные, и импортные аналоги. Т.е. с помощью описанных технологических новшеств был создан высоко конкурентный продукт с реальным энергосберегающим эффектом при его применении.
Отечественное машиностроительное предприятие может выжить в современных экономических условиях только в случае применения самых современных технологий, позволяющих создавать наукоемкую продукцию, успешно конкурирующую с лучшими мировыми аналогами.