Автор: Е.А. Бессонный, П.Д. Машковцев, А.В. Михайлов, В.М. Сидоров (ООО «ГК «ЛЕННИИХИММАШ»).
Опубликовано в журнале Химическая техника №2/2015
В газовой, нефтяной и других отраслях промышленности широкое применение нашли вертикальные аппараты: адсорберы, каталитические реакторы, зернистые фильтры и другое оборудование с центральным верхним вводом газового потока, внутренняя полость которых заполнена насыпным слоем рабочих тел зернистой структуры.
К недостаткам вертикальных аппаратов следует отнести сложность обеспечения равномерного поля скоростей газового потока в поперечном сечении аппарата на входе в насыпной рабочий слой при подаче перерабатываемого газа через центрально расположенный верхний штуцер, площадь сечения которого в 15–50 раз меньше площади поперечного сечения корпуса аппарата. В результате резкого расширения входящей через верхний штуцер струи газа в пространстве над насыпным слоем создается неравномерность, при которой поток газа заполняет только часть поперечного сечения, в то время как в остальной части сечения поступательное движение отсутствует.
Учитывая, что поступление газа в насыпной рабочий слой происходит из неравномерно распределенного по сечению аппарата газа, распределение газа, движущегося внутри слоя адсорбента, оказывается также неравномерным. Это приводит к снижению эффективности работы аппарата, а часто к локальному перегреву и запеканию зерен слоя в случае использования горячих газов.
Обеспечение равномерного распределения входного потока газа в поперечном сечении аппарата на входе в насыпной слой является весьма важной задачей для адсорберов при осуществлении в них процессов сушки и очистки углеводородных газов в газовой и нефтяной отраслях промышленности, имеющих дело с переработкой больших объемов газа при высоких давлениях – 8…10 МПа.
Для выравнивания газового потока в поперечном сечении аппарата до рабочего слоя в случае центрального ввода потока в аппарат на практике применяют различные распределительные устройства, размещаемые на выходе потока газа из верхнего штуцера. Установлено [1], что выравнивающее действие распределительного усройства в сильной степени зависит от отношения площади поперечного сечения корпуса аппарата Fа к площади поперечного сечения отверстия Fo, через которое поток газа поступает в полость аппарата перед рабочим слоем. Чем больше отношение Fа/Fo, тем выше требование к эффективности выравнивающего действия распределительного устройства.
На эффективность распределения потока газа большое влияние оказывает также значение коэффициента сопротивления распределительного устройства и относительное расстояние распределительного устройства (на выходе потока) до рабочего слоя.
Наиболее простые распределительные устройства включают плоский диск-экран, который установлен на некотором расстоянии от нижнего обреза верхнего штуцера. При этом диск-экран крепится к штуцеру либо с помощью специального каркаса [2], либо с помощью ребер, приваренных к расширительному патрубку штуцера [3] или непосредственно к верхнему днищу аппарата.
В распределительных устройствах с использованием плоского диска-экрана газовая струя, выходящая из центрально установленного верхнего штуцера, набегает на плоский экран и, растекаясь в радиальном направлении, движется в виде плоской струи в сторону вертикальной стенки корпуса аппарата.
Недостатком данного распределительного устройства (с помощью плоского диска-экрана в условиях движения с достаточно высокой скоростью плоской струи в радиальном направлении над рабочим слоем) является невозможность достижения эффективного выравнивания газового потока в поперечном сечении аппарата на входе в насыпной слой.
Промышленные обследования адсорбера, предназначенного для очистки природного газа с применением цеолита, который снабжен распределительным устройством, содержащим плоский диск-экран [3], и экспериментальные исследования на пилотной модели этого адсорбера подтвердили факт существования неравномерного распределения потока по сечению адсорбера. В результате этого около 30% поглотительной способности загруженного адсорбера не используется к моменту завершения цикла адсорбции.
Причина неэффективности использования экрана для выравнивания потока газа для случая набегания на плоский экран струи газа может быть объяснена на примере исследования процесса набегания струи газа на плоскую тонкостенную решетку, которая является более эффективным устройством по сравнению с плоским диском-экраном [1].
В такой решетке распределение струи газа в рабочей зоне аппарата, несмотря на наличие распределительных отверстий, происходит аналогичным образом. При набегании узкой струи газа на плоскую решетку струя газа растекается радиально, проходит через отверстия, сохраняя радиальную направленность струек, и, двигаясь в виде плоской струи, достигает стенки корпуса аппарата.
Достигнув стенки, газовый поток изменяет свое направление на 90° и перемещается вниз вдоль стенки в виде прижатой к стенке кольцевой струи, проникая в слой адсорбента.
При этом в центральной части сечения ниже плоской решетки поступательная скорость газа равна нулю.
Вследствие турбулентного перемешивания поток газа, подходящий к стенке корпуса, увлекает за собой неподвижную часть газа из центральной части сечения. На освободившееся место из более удаленных от плоской решетки сечений поступают другие порции газа, в результате чего в центральной части сечений под решеткой возникают обратные токи, а профиль скорости газа под плоской решеткой будет иметь «перевернутую» форму по сравнению с начальным профилем потока.
Таким образом, в пространстве аппарата перед рабочим слоем существуют радиальные (или, иначе, поперечные) потоки газа в виде плоской струи. Один поток (прямой), образованный в результате радиального растекания входящей струи газа, движется в верхней части рабочей зоны в сторону стенки корпуса адсорбера. Другой поток (обратный) перемещается ниже прямого потока вблизи адсорбционного слоя в зону пониженного статического давления, расположенную под диском-экраном. Неравномерность распределения потока газа в плоскости аппарата над рабочим слоем обусловливает неравномерное поступление газа в слой адсорбента и соответственно неравномерное продвижение его вдоль слоя адсорбента.
Особенностью конструкции адсорберов, используемых на промышленных объектах переработки природного газа, является то, что сверху слоя адсорбента размещен через распределительную сетку слой керамических шаров. Сетка препятствует уносу частиц адсорбента с верха адсорбера с регенерационным газом, который движется на стадии регенерации адсорбента снизу вверх, а слой керамических шаров обеспечивает фиксацию сетки на слое адсорбента и способствует выравниванию входящего через верхний штуцер исходного потока газа.
Наличие в адсорбере слоя керамических шаров, расположенных над адсорбционным слоем через распределительную сетку, при применении направляющего устройства с плоским диском-экраном приводит к появлению дополнительных недостатков, обусловленных интенсивным перемещением потока газа в виде плоской струи над слоем керамических шаров. В связи с тем, что в насыпном слое керамических шаров отсутствуют разграничивающие поверхности, плоская струя со стенки корпуса не растекается перед фронтом насыпного слоя, а продолжает свое растекание постепенно вглубь слоя от сечения к сечению с выходом части газа из насыпного слоя в центральную зону с пониженным статическим давлением. Так как керамические шары не скреплены между собой и имеют небольшую массу, проникающий в слой поток газа вовлекает их в движение, вызывая колебания и перемещение с газовым потоком. При этом керамические шары газовым потоком вытесняются из пристенных слоев корпуса адсорбера вплоть до обнажения разделительной сетки и выносятся в центральную застойную зону, образуя купол в виде конуса с перемещающимися внутри него шарами. Обнажение защитной сетки приводит к нарушению плотности ее прилегания к слою адсорбента и возможной деформации отдельных звеньев сетки.
Это приводит к выносу частиц адсорбента из-под сетки и перемешиванию их с перемещающимися в потоке газа керамическими шарами.
Нарушение равномерности распределения слоя керамических шаров на защитной сетке ухудшает распределение газа на входе в адсорбционный слой, а перемешивание между собой керамических шаров и зерен адсорбента приводит к их истиранию и образованию мелких частиц, которые оседают в слое адсорбента, увеличивая его гидравлическое сопротивление.
В некоторых случаях для выравнивания потока газа в рабочей зоне адсорбера перед адсорбционным слоем используют распределительные устройства диффузорного типа, установленные на верхнем штуцере для центрального ввода потока в аппарат [4].
Использование в адсорбере распределительного устройства диффузорного типа улучшает равномерность распределения потока газа в поперечном сечении адсорбера по сравнению с диском-экраном за счет предварительного расширения потока в диффузоре, более плавного выхода и дальнейшего расширения его в надслойном пространстве при более благоприятном (уменьшенном) отношении Fa/Fo. Однако применение диффузора в качестве распределительного устройства не может обеспечить достаточно равномерное распределение потока газа в поперечном сечении аппарата, так как при повороте и расширении его в пространстве над рабочим слоем возникает возмущение потока, приводящее к образованию разности скоростей потока в различных точках поперечного сечения и появлению обратных токов газа в зонах с пониженным статическим давлением.
С целью улучшения распределения входящего через верхний штуцер потока газа в адсорбере [3] применено распределительное устройство, которое включает последовательно подсоединенные к расширительному патрубку входного штуцера по ходу движения газа два соосных металлических кольца разных диаметров и плоский диск-экран.
Кольца выполнены в виде плоского диска с отверстием в центре. Диаметры колец и плоского сплошного диска-экрана уменьшаются сверху вниз последовательно друг за другом, при этом их диаметры и расстояние между ними рассчитаны так, что обеспечивают разделение потока газа на три равные части. Дополнительно кольца и диск-экран снабжены с нижней стороны двадцатью постоянными магнитами.
Применение в адсорбере с центральным вводом исходного газа распределительного устройства, содержащего систему из двух последовательно соединенных соосных колец разных диаметров и плоского диска-экрана, позволило несколько улучшить эффективность распределения потока газа в поперечном сечении адсорбера. Дополнение конструкции кольцевой системы постоянными магнитами дало некоторое повышение эффективности работы распределительного устройства.
Однако распределительное устройство из системы двух соосно установленных последовательно друг за другом колец и плоского диска-экрана не может обеспечить достаточно высокую степень равномерности потока в поперечном сечении рабочей зоны адсорбера с верхним входом исходного газа, что и показывают результаты испытаний [3].
Это можно объяснить тем, что раздача входящей струи газа через центрально расположенный верхний штуцер происходит при растекании струи газа по двум соосным кольцам и диску-экрану с образованием трех параллельных плоских струй, которые движутся в радиальном направлении в сторону стенки аппарата, а после поворота перемещаются, смешиваясь между собой, в сторону центральной части аппарата в зону пониженного давления с образованием отдельных токов газа.
Некоторое улучшение распределения потока газа объясняется делением входящего потока на три части, что приводит к уменьшению скоростей перемещения прямых и обратных токов газа над слоем адсорбента и выравниванию в связи с этим поля скоростей газа в рабочей зоне.
К недостаткам этого распределительного устройства следует также отнести:
- сравнительно большую высоту распределительного устройства при четырехслойном (с учетом расширительного патрубка входного штуцера) размещении кольцевой системы устройства, что обусловливает необходимость увеличения надслойного пространства в адсорбере;
- усложнение конструкции распределительного устройства, требующее дополнительных съемных приспособлений для крепления устройства к корпусу адсорбера и крепления постоянных магнитов к кольцам и плоскому диску-экрану.
Обеспечение равномерности распределения входного потока в поперечном сечении аппарата в пространстве перед насыпным рабочим слоем при центральном верхнем вводе потока является актуальной задачей не только в адсорберах, но в других аппаратах (каталитические реакторы, зернистые фильтры, шахтные известковые печи и др.).
Для выравнивания потока в поперечном сечении подобных аппаратов до рабочего слоя применяется ряд способов, некоторые из которых приведены в монографии [1]. В качестве распределительных устройств были исследованы три системы кольцевых диффузоров, содержащие по три диффузора, установленных друг в друге по кольцу [1]. Системы отличались между собой углами наклона входящих в систему диффузоров, расстояниями между диффузорами, а также наличием дополнительных элементов (прямые участки на входе в кольцевой диффузор, конический отбойник на выходе из внутреннего диффузора или сферическая тарелка на выходе из кольцевого диффузора).
Распределительное устройство, содержащее систему кольцевых диффузоров, имеет определенное преимущество перед одиночным диффузором, так как при сохранении плавного выхода потока из устройства оно обеспечивает более высокую степень предварительного расширения в диффузоре, а, следовательно, и меньшее отношение Fа/Fo.
Это обусловливает меньшее возмущение потока при расширении его с поворотом в пространстве перед рабочим слоем.
Результаты исследования кольцевых диффузоров [1] показали, что наилучшее распределение потока обеспечивает вариант с диффузорами, установленными под разными углами в виде расходящихся лучей без дополнительных элементов. Две другие системы кольцевых диффузоров не обеспечивают даже удовлетворительной степени равномерности потока.
Для раздачи потока перед рабочим слоем в аппарате с центральным входом применяются и другие варианты газораспределительных устройств [1]. В одном из вариантов приведена схема аппарата с центральным входом и распределителем потока в виде утолщенной плоской решетки с диском-экраном в центральной части сечения аппарата, в котором достигается приемлемое выравнивание потока при определенных соотношениях геометрических параметров составных элементов аппарата.
В другом варианте используется центрально установленная перфорированная труба с проницаемыми стенками. При этом кольцевое пространство между перфорированной трубой и стенкой аппарата секционировано соосно установленными разновеликими цилиндрическими обечайками с заглушенными верхними торцами. К перфорированной трубе с обечайками, которые делят исходный поток на четыре параллельных потока, на выходном конце присоединена плоская решетка, перекрывающая все поперечное сечение аппарата.
Применение этого распределительного устройства позволило получить удовлетворительное распределение скоростей газа по сечению аппарата перед рабочим слоем.
В третьем варианте применена объемная решетка, контурные очертания которой повторяют внутренний контур стенок аппарата. Решетка установлена с зазором с внутренними стенками аппарата. Она снабжена сверху экраном и опирается на плоскую перфорированную решетку, перекрывающую все поперечное сечение аппарата. Входной поток набегает на экран и перемещается вниз по кольцевому пространству между объемной решеткой и стенкой аппарата. При этом часть потока поступает во внутреннюю полость решетки.
Обе части потока через перфорированную плоскую решетку направляются в надслойное пространство перед рабочим слоем.
Газораспределитель с использованием объемной решетки, как показали испытания, уступает по эффективности выравнивания газового потока перед рабочим слоем газораспределителю с вертикальной перфорированной трубой, секционированной разновеликими обечайками.
В следующем варианте приведена схема установки газораспределительного устройства из трех последовательно установленных плоских решеток. Ее применение в тех же сравнительных условиях, при которых проводилось испытание двух предыдущих вариантов газораспределительных устройств, позволяет обеспечить степень равномерности поля скоростей примерно такую же, как и в вертикальной перфорированной трубе.
Анализ эффективности работы известных распределительных устройств показывает, что они не могут обеспечить достаточно эффективного распределения потока газа, поступающего в аппарат через верхний центрально установленный штуцер.
Для полного выравнивания потока вместе с ними должны быть применены другие выравнивающие устройства, в первую очередь системы последовательно установленных плоских решеток.
К недостаткам большинства известных распределительных устройств следует отнести также наличие в конструкции, как правило, нескольких составных элементов большого размера, что требует увеличения надслойного пространства и усложняет их изготовление, монтаж и обслуживание внутри аппарата.
В ООО «ГК «ЛЕННИИХИММАШ» разработано эффективное распределительное устройство для равномерного распределения потока газа в поперечном сечении вертикальных аппаратов с насыпным слоем рабочих элементов и центральным верхним вводом газового потока в аппарат. Распределительное устройство выполнено в виде горизонтальной кольцевой перфорированной перегородки, в центре которой размещен расширяющийся кверху направляющий конический стакан.
Устройство устанавливается внутри аппарата над насыпным рабочим слоем.
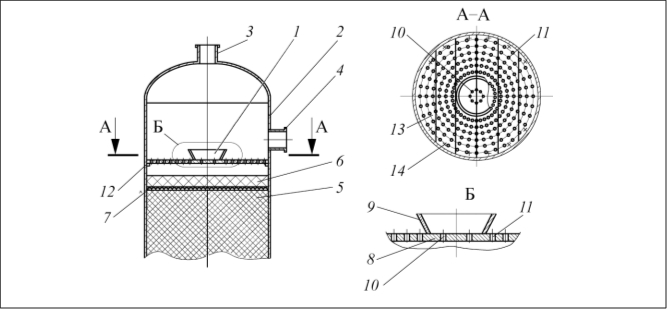
На рис. 1 представлено распределительное устройство 1, установленное в качестве примера в вертикальном адсорбере 2 с насыпным слоем адсорбента. Адсорбер содержит штуцер 3 для входа перерабатываемого газа, установленный по оси верхнего днища адсорбера, люк-лаз 4 для обслуживания аппарата, слой адсорбента 5, опирающийся на опорное устройство, которое смонтировано в нижней части адсорбера, и слой керамических шаров 6, размещенных на слое адсорбента через разделительную сетку 7.
Над слоем керамических шаров 6 размещена горизонтальная кольцевая перфорированная перегородка 8, перекрывающая поперечное сечение корпуса адсорбера. Центральная часть перегородки выполнена в форме расширяющегося кверху направляющего конического стакана 9. В основании конического стакана предусмотрены отверстия 10 для выравнивания перепада давлений газа в сечениях над перфорированной перегородкой и ниже ее в зоне основания стакана. С целью повышения равномерности распределения газа на входе в слой адсорбента в перфорированной перегородке на площади от конического стакана до корпуса адсорбера выполнено соответствующее число отверстий 11 разных диаметров с различными расстояниями между ними. Перфорированная перегородка опирается на опорное кольцо 12, которое приварено к обечайке корпуса адсорбера. Перегородка выполнена из отдельных съемных секций 13, прикрепленных к опорным кольцам с помощью болтовых соединений 14.
Монтаж и демонтаж секций распределительного устройства производится через люк-лаз 4, который используется также для загрузки адсорбента. Выгрузка адсорбента осуществляется через нижний люклаз, установленный на нижнем днище корпуса аппарата.
В данном техническом решении одним из составных элементов распределительного устройства для выравнивания потока газа на входе в рабочий слой является горизонтальная кольцевая перфорированная перегородка – плоская решетка, обладающая выравнивающим действием с помощью рассредоточенных по ее сечению отверстий, создающих сопротивление прохождению потока газа. Однако в силу специфических свойств плоской решетки, как было рассмотрено ранее, в условиях полной неравномерности потока, т.е. в случае набегания на нее узкой струи газа, плоская решетка не способна обеспечить равномерное распределение потока в поперечном сечении аппарата. Так как причиной существования неравномерности потока газа в поперечном сечении адсорбера в рабочей зоне перед адсорбционным слоем является радиальное растекание потока газа, обусловленное прохождением струек газа через отверстия решетки под значительным наклоном к поверхности решетки, задача устранения радиального растекания потока газа и исключения «перевертывания» профиля скорости заключалась в максимальном уменьшении доли поперечных составляющих и соответственно в увеличении доли нормальных составляющих скоростей газовых струй при прохождении их через отверстия решетки.
Получение нужного эффекта было достигнуто в результате постепенного расширения потока газа с обеспечением равномерного заполнения всего пространства над адсорбционным слоем газом без застойных зон, в результате чего резко снижается скорость поперечного перемещения потока над перфорированной перегородкой. При этом значительно улучшаются условия входа струек газа в отверстия перегородки.
Первоначальное расширение и, следовательно, снижение скорости струи газа, выходящей из входного штуцера, осуществляется за счет увеличения расстояния между нижним обрезом верхнего штуцера и перфорированной перегородкой, которая установлена вблизи адсорбционного слоя, покрытого слоем керамических шаров. Последующее расширение потока и соответственно снижение его скорости происходит при набегании струи газа на расширяющийся кверху конический стакан, установленный в центральной части перфорированной перегородки. Стакан предотвращает непосредственное набегание струи газа на перфорированную перегородку и растекание ее в виде плоской струи в радиальном направлении в сторону стенки корпуса, приводящее к неравномерному распределению потока. Конический стакан выполняет роль направляющего экрана, который формирует направление радиального растекания набегающей на него струи газа вверх под углом в сторону стенки корпуса адсорбера в виде радиальной расширяющейся плоской струи.
Схему распределения потока газа в верхней зоне адсорбера над распределительной кольцевой перфорированной перегородкой с коническим стаканом получают на основе компьютерной программы расчета газодинамических процессов течения рабочих сред. С помощью компьютерного моделирования геометрических параметров конического стакана и набора отверстий в перфорированной перегородке при принятых конструктивных параметрах адсорбера для данного расхода и давления газа находят режим течения потока газа, при котором обеспечивается его равномерное распределение на входе в адсорбционный слой.
Режим течения газа в верхней зоне адсорбера над перфорированной перегородкой с коническим стаканом отслеживается путем получения визуальной общей картины распределения потока или графическим методом по распределению струек газа в поперечном сечении аппарата на выходе из перфорированной перегородки. Получаемая на компьютере схема распределения потока газа в верхней зоне адсорбера представлена на рис. 2.
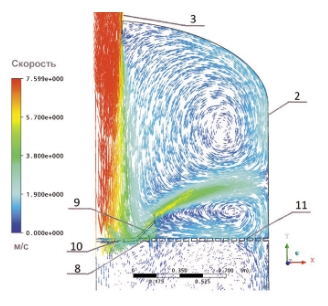
над перфорированной перегородкой
с направляющим коническим стаканом
Достигнув стенки корпуса, расширяющаяся струя разворачивается и делится на два потока, которые продолжают передвигаться в двух направлениях.
Один поток, расширяясь, передвигается вверх вдоль стенки корпуса, а затем – вдоль стенки верхнего днища до соприкосновения в центре адсорбера с движущейся вниз газовой струей. Газовая струя, имея более высокую скорость за счет эффекта эжекции, увлекает за собой поток газа, поднимающийся вверх, заставляя его разворачиваться и двигаться в обратном направлении.
Эжектирование масс газа из поднимающегося вверх потока происходит на протяжении всего пути его перемещения. В результате в верхней зоне адсорбера с нижней границей по линии кольцевой струи газа образуется циркуляционный контур с достаточно равномерно распределенными токами газа без застойных участков.
Другой поток, расширяясь, движется вниз вдоль стенки корпуса и на границе с адсорбционным слоем разворачивается и перемещается вдоль него к коническому стакану до соприкосновения со струей, выходящей из конического стакана. Газовая струя эжектирует подходящие к стакану газовые массы и увлекает в свое движение вверх под углом к оси адсорбера в сторону вертикальной стенки корпуса. В результате в нижней зоне адсорбера с верхней границей по линии радиальной струи газа образуется второй циркуляционный газовый контур с достаточно равномерно распределенными токами газа без застойных участков.
Таким образом, применение расширяющегося кверху конического стакана, установленного в центре кольцевой перфорированной перегородки, позволяет обеспечить равномерное распределение токов газа без застойных зон во всем объеме адсорбера, расположенном выше перфорированной перегородки, в результате образования двух циркуляционных газовых контуров, которые перемещаются широким фронтом за счет эжектирующего действия кольцевой струи, выходящей из конического стакана, в сторону стенки корпуса адсорбера. На подходе к стенке корпуса общий поток газа делится на два потока, которые передвигаются в противоположном направлении друг от друга, каждый по своему контуру до следующего соединения между собой.
Вследствие значительного расширения исходного газа при равномерном распределении потока во всем объеме пространства адсорбера над перфорированной перегородкой обеспечивается значительное снижение скорости движения токов газа, перемещающихся широким фронтом по замкнутым контурам.
Поступление в этом случае газа в адсорбционный слой через отверстия в перфорированной перегородке происходит из равномерно распределенного потока, который перемещается над перфорированной перегородкой широким фронтом при значительно уменьшенной скорости. Это улучшает условия входа струек газа в отверстия перегородки и позволяет повысить равномерность распределения потока газа в адсорбционном слое. Для повышения степени выравнивания потока, поступающего на перегородку, она снабжена неравномерно распределенными по сечению отверстиями.
Число отверстий, их диаметры и расстояния между ними определяется в зависимости от степени неравномерности поля скоростей газа, поступающего на перфорированную перегородку.
Адсорбер с вновь разработанным распределительным устройством работает следующим образом. Исходный поток газа поступает на осушку в адсорбер через штуцер 3, из которого в виде газовой струи движется вниз и набегает на дно конического стакана 9. Растекаясь по стакану в радиальном направлении, газовая струя переме-щается под углом к поперечному сечению корпуса адсорбера, зависящим от угла наклона конической поверхности стакана, в виде кольцевой радиальной струи в сторону вертикальной стенки цилиндрического корпуса адсорбера 2.
Достигнув стенки корпуса, расширяющаяся радиальная струя разворачивается, образуя два потока, один из которых движется, расширяясь, вверх вдоль стенки корпуса и верхнего днища, другой перемещается вниз вдоль стенки корпуса, а затем после поворота – вдоль поверхности плоской перфорированной перегородки в направлении конического стакана. При своем перемещении потоки соприкасаются со струями газа, которые увлекают их в свое движение. В результате в верхней зоне адсорбера над перфорированной перегородкой образуются два циркуляционных контура с равномерно распределенными токами газа без застойных участков во всем объеме верхней зоны.
За счет того, что поток газа нижнего циркуляционного контура перемещается над перфорированной перегородкой равномерно распределенным широким фронтом при значительно уменьшенных скоростях создаются благоприятные условия входа струек газа в отверстия перегородки.
Дополнительно повышение степени выравнивания потока газа происходит при прохождении струек газа через отверстия 11 в перфорированной перегородке. В зависимости от степени неравномерности поля скоростей в потоке газа, поступающего на перегородку, выравнивающие отверстия на ней выполнены с разной степенью живого сечения на различных ее участках или, иначе, с разным числом отверстий, их диаметров и расстояний между ними. После прохождения через отверстия перегородки выровненный поток газа продолжает свое движение сверху вниз, проходя последовательно через слой керамических шаров 6 (см. рис. 1), размещенных на разделительной сетке 7 и слой адсорбента 5, и выходит из адсорбера через штуцер, установленный на нижнем днище.
Благодаря применению распределительного устройства в виде горизонтальной кольцевой перфорированной перегородки с направляющим коническом стаканом выровненный поток газа после перфорированной перегородки входит плавно через слой керамических шаров в слой адсорбента и равномерно в нем распределяется. При этом обеспечивается устойчивое положение керамических шаров в слое без выноса их из слоя с газовым потоком, что позволяет использовать слой керамических шаров не только для фиксации сетки на слое адсорбента, но и для повышения равномерности распределения потока газа в адсорбционном слое. При этом исключаются неполадки в работе адсорбера, связанные с выносом керамических шаров из слоя потоком входящего через верхний штуцер газа. Таким образом, в результате поэтапного выравнивания потока газа в надслойном пространстве аппарата перед входом его в адсорбционный слой и равномерного распределения потока в слое адсорбента значительно повышается степень использования поглотительной способности адсорбента, загруженного в аппарат.
Важным преимуществом разработанного распределительного устройства является то, что его конструкция достаточно проста, занимает мало места в надслойном пространстве аппарата, удобна для монтажа и демонтажа внутри аппарата через люклаз, так как выполнена из отдельных съемных секций.
Конструкция распределительного устройства позволяет обеспечить равномерное распределение потока газа в поперечном сечении вертикальных аппаратов с насыпным рабочим слоем и верхним центральным вводом потока, отличающихся геометрическими размерами, расходом и давлением перерабатываемого газа. Необходимый режим течения газа в верхней зоне аппарата для обеспечения равномерного распределения потока в конкретном аппарате с принятыми диаметрами корпуса и верхнего штуцера, а также расстояния от штуцера до перфорированной кольцевой перегородки достигается подбором соответствующих геометрических параметров распределительного устройства (диаметры нижнего и верхнего оснований конического стакана, его высота и необходимый набор отверстий на перфорированной кольцевой перегородке). Указанные геометрические параметры распределительного устройства определяются методом компьютерного моделирования на основе программы расчета газодинамических процессов течения рабочих сред в элементах аппарата с учетом расхода и давления перерабатываемого газа. При этом расстояние между верхним штуцером и горизонтальной кольцевой перфорированной перегородкой в аппаратах принимается таким, чтобы было можно удобно разместить люк-лаз для проведения монтажа и демонтажа распределительного устройства рабочим персоналом, а также для проведения работ по загрузке и выгрузке насыпного рабочего слоя.
Распределительные устройства (см. рис. 1) применены в адсорберах для осушки попутного нефтяного газа, введенных в эксплуатацию на газоперерабатывающих заводах северных месторождений газа.
Основные показатели адсорберов с этим распределительным устройством: давление газа – 8 МПа, расход перерабатываемого газа – 169 284 кг/ч, диаметр корпуса адсорбера – 2 600 мм, диаметр верхнего входного штуцера – 500 мм, диаметр нижнего основания конического стакана – 600 мм, диаметр верхнего основания конического стакана – 900 мм, расстояние между перфорированной кольцевой перегородкой и верхним входным штуцером – 1 900 мм, общее число отверстий разных диаметров в диапазоне 24…38 мм в перфорированной перегородке на площади между коническим стаканом и корпусом адсорбера – 1 680, число отверстий диаметром 16 мм на нижнем основании конического стакана – 36.
Параметры работы адсорбера соответствуют требованиям технического регламента производства.
Конструкция вертикального адсорбера, в котором над слоем адсорбента размещено распределительное устройство, представляющее собой горизонтальную кольцевую перфорированную перегородку с отверстиями разных диаметров и расстояний между ними, центральная часть которой выполнена в форме расширяющегося кверху конического стакана, защищена патентом РФ №2530112 (правообладатель – ООО «ЛЕННИИХИММАШ»).
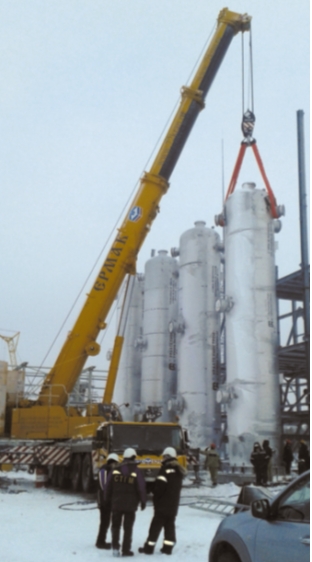
на площадке Вынгапуровского ГПЗ в рамках реализации проекта
«Расширение Вынгапуровского ГПЗ. Строительство установки переработки газа №2 (УПГ-2)»
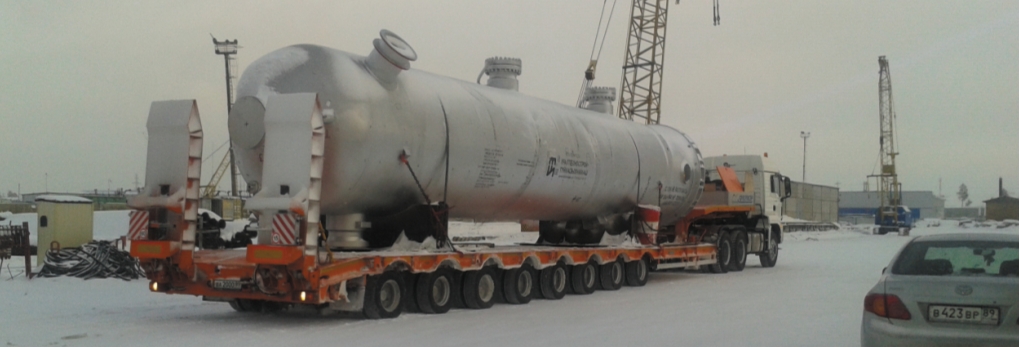
Вертикальные адсорберы с собственной запатентованной конструкцией (рис. 3, 4) применены Группой Компаний «ЛЕННИИХИММАШ» в технологических линиях в рамках разработки проектов по строительству Вынгапурского ГПЗ производительностью 2,1 млрд. м3/год и по строительству новой линии по переработке 2,0 млрд. м3 углеводородного газа Южно-Балыкского ГПК по заказу ОАО «СибурТюменьГаз», а также в текущих проектах компании («Расширение Вынгапуровского ГПЗ. Строительство установки переработки газа №2 (УПГ-2)»).
Список литературы:
- Идельчик И.Е. Аэродинамика технологических аппаратов. М.: Машиностроение, 1983.
- Серпионова Е.Н. Промышленная адсорбция газов и паров. М: Высшая школа, 1969 г.
- Искалиева С.К., Пивоварова Н.А. и др. Увеличение срока службы адсорбента на установках осушки обессеренного газа//Газовая промышленность. 2012. №1.
- Ремизов В.В., Зайнуллин В.Ф., Чугунов Л.С., Михайлов Н.В. Особенности работы установок адсорбционной осушки газа на месторождениях крайнего Севера. Серия: Подготовка и переработка газа и газового конденсата. Обз. инф. М.: ИРЦ Газпром, 1995.