Автор: С.В. Чамов (Компания ESAB).
Опубликовано в журнале Химическая техника №2/2016
Дуплексные (феррито-аустенитные) коррозионностойкие высоколегированные стали находят все большее применение в различных отраслях промышленности, в том числе в нефтехимической. Они включают широкую номенклатуру сталей (бюджетные с пониженным легированием, стандартные с 22% Cr, высоколегированные супери гипердуплексные) различного назначения. Все они сочетают высокую прочность с высокой коррозионной стойкостью, имеют двухфазную микроструктуру, состоящую из примерно 50% аустенита и 50% феррита. Дуплексные коррозионно-стойкие стали обычно обладают пределом текучести, в 1,5–2 раза превышающим предел текучести аустенитных сталей (рис. 1), и при этом имеют характерную для них высокую коррозионную стойкость, а также значительно менее чувствительны к коррозионному растрескиванию. Данные стали отличает относительно хорошая свариваемость, не требуется предварительный подогрев изделия и отпуск после сварки. Однако существует небольшой риск охрупчивания по зоне термического влияния из-за роста зерна, увеличения доли ферритной фазы и выпадения карбидов.
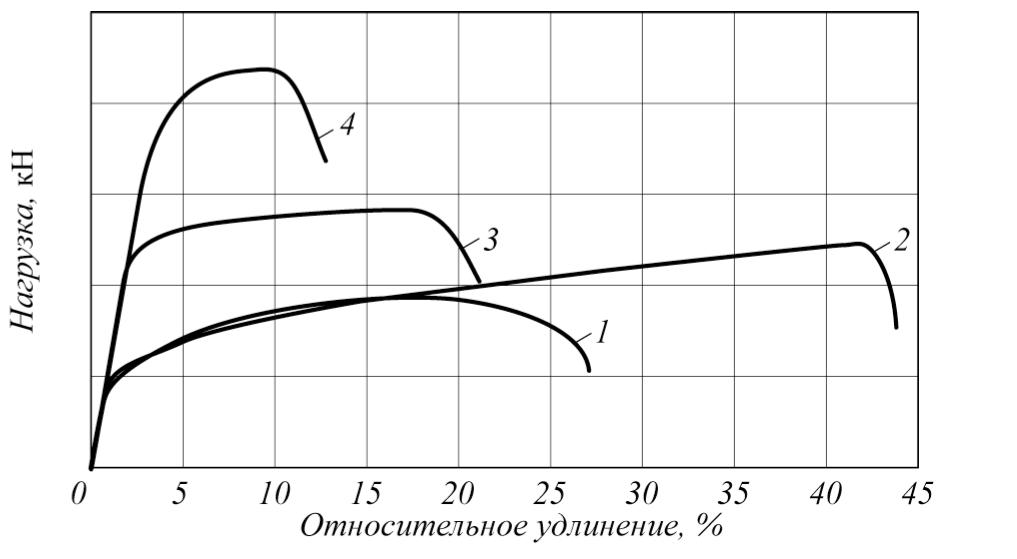
1 – ферритные стали; 2 – аустенитные стали; 3 – дуплексные стали; 4 – мартенситные стали после закалки и отпуска
Для нефтехимической промышленности наибольший интерес представляют стандартные дуплексные стали, легированные ~22% Cr, 5–6% Ni, ~3% Mo и упрочненные ~0,15% N, имеющие предел текучести ~550 МПа, при этом их сопротивляемость питтинговой коррозии даже выше, чем у сталей типа 1.4439 (AISI 317L). При подборе сварочных материалов для этих сталей необходимо руководствоваться двумя основными принципами:
- химический состав наплавленного металла должен несколько отличаться от химического состава основного металла, так как эквивалент сопротивляемости питтинговой коррозии (PRE = %Cr + 3,3 × %Mo + 16 × %N) сварного шва должен быть выше PRE основного металла не менее, чем на 20–25%;
- должен соблюдаться баланс между аустенитной и ферритной фазами (рис. 2). Это, как правило, достигается за счет более высокого (на 3–4%) содержания Ni в сварочном материале. Снижение содержания аустенитной фазы приведет к снижению коррозионной стойкости, а ферритной фазы – к снижению прочностных свойств наплавленного металла.
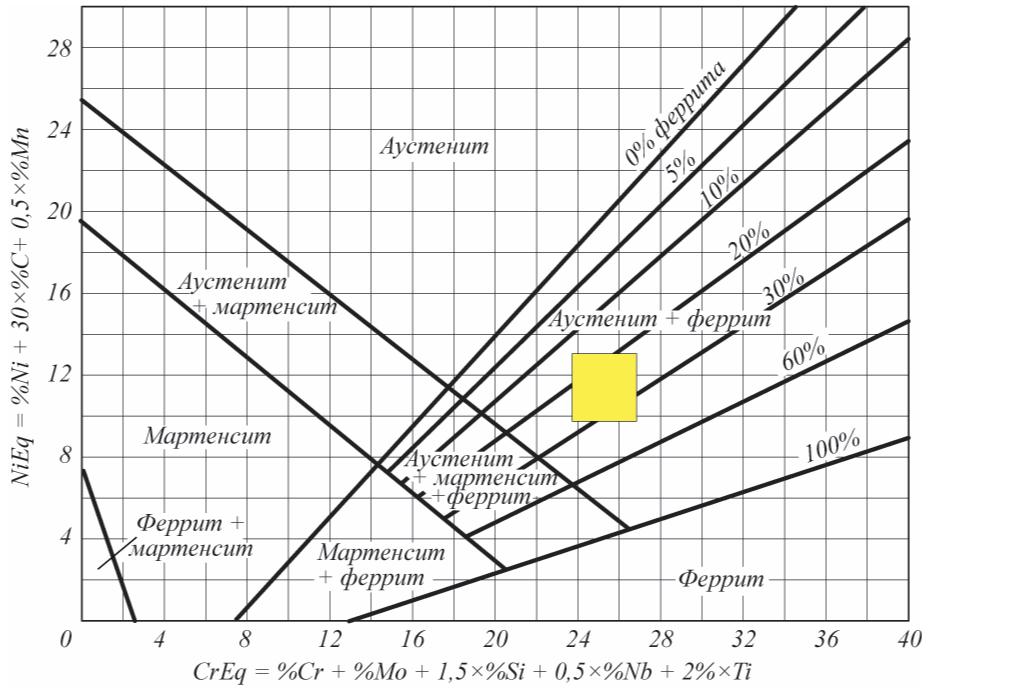
Несмотря на то, что данные стали являются хорошо свариваемыми, необходимо придерживаться ряда правил.
Перед сваркой:
- для обеспечения хорошего проплавления зазор в корне стыка и угол разделки кромок делаются чуть больше, чем для стандартной коррозионно-стойкой стали;
- стык и металл вокруг стыка необходимо тщательно очистить от загрязнений;
- для очистки стыка можно применять металлические щетки только из коррозионно-стойкой проволоки;
- электрод обязательно должен быть сухим.
В процессе сварки:
- не следует допускать слишком низких или излишне высоких тепловложений. Для стандартных дуплексных сталей удельное тепловложение следует выдерживать в диапазоне 0,5…2,5 кДж/мм, а межпроходную температуру – не выше 200°С;
- не допускать образования окалины на обратной стороне сварного соединения. Важно правильно подобрать газ для защиты корня шва. Обычно для этого применяют смесь высокочистого аргона с азотом или водородом;
- сварку должен выполнять специалист, обладающий достаточно высокой квалификацией, так как места прожогов имеют склонность к питтинговой коррозии и образованию трещин;
- для предотвращения насыщения наплавленного металла азотом необходимо избегать излишнего удлинения дуги и вылета электродной проволоки;
- во время сварки не рекомендуется делать излишне широких поперечных колебаний электрода. Это может привести к чрезмерно высокому удельному тепловложению.
После сварки:
- для обеспечения необходимой коррозионной стойкости наплавленный металл необходимо тщательно зачистить и полностью удалить остатки шлака и следы окисной пленки;
- зачистку выполнять вручную щеткой из коррозионностойкой проволоки. Механизированная зачистка дисковыми щетками может привести к образованию микронадрывов поверхности сварного шва;
- послесварочная термообработка обычно не требуется.
Однако в некоторых случаях дуплексные стали и их сварные соединения могут подвергаться термообработке (необходимо ознакомиться с рекомендациями производителя стали). Термического снятия сварочных напряжений следует избегать, так как это может привести к охрупчиванию основного и наплавленного металлов;
- допустима термическая правка деформированных листов при условии, что в рекомендациях поставщика стали отсутствуют на это ограничения.
Компания ESAB обладает передовыми решениями в области технологий сварки и резки металла. Более чем столетний опыт и постоянное усовершенствование продукции и технологий позволяет нам идти в ногу с техническим прогрессом в каждом направлении, которым занимается компания ESAB. Наша компания предлагает своим клиентам широкую линейку сварочных материалов для всех видов дуговой сварки плавлением дуплексных сталей различных типов, таких, как бюджетные с пониженным легированием, стандартные и супердуплексные, и имеет возможность удовлетворить потребности даже самых крупных клиентов в любой точке мира. При этом мы гарантируем единое стабильно высокое качество продукции независимо от того, на каком из наших заводов она была произведена, что обеспечивается общей для всех системой контроля качества сырья, объемов и методов испытаний, менеджмента качества и соответствия ISO 14001 / OHSAS 18001. Для решения задач ремонта и монтажных работ на НПЗ наибольший интерес представляют покрытые электроды, проволоки сплошного сечения для дуговой сварки в защитных газах плавящимся и неплавящимся электродом, а также порошковые проволоки, применяемые для сварки стандартных дуплексных сталей.
Таблица 1
Тип электрода по стандарту | Тип покрытия | ||
EN ISO 3581-A | AWS A5.4 | Рутиловое | Основное |
E2293NLR32 | E2209-17 | OK 67.50 | – |
E2293NLR12 | E2209-16 | OK 67.53 | – |
E2293NLB22 | E2209-16 | – | OK 67.55 |
Компания ESAB выпускает электроды для сварки дуплексных сталей как с основной, так и с рутиловой обмазкой (табл. 1). Основное покрытие обеспечивает более высокие пластические свойства при низких температурах, быстротвердеющий шлак легко формирует обратный валик в различных пространственных положениях, наплавленный металл обладает наилучшей стойкостью против образования пор и горячих трещин. Однако электроды с рутиловым покрытием обладают гораздо лучшими сварочно-технологическими свойствами, характеризуются минимальным разбрызгиванием и легкостью отделения шлака, горят как на постоянном, так и на переменном токе. Данные электроды поставляются в упаковках типа ESAB VacPac™ (рис. 3), которые являются высокоэффективным решением для перевозки и хранения электродов, позволяющим не регламентировать климатические условия и исключить затраты на их сушку перед применением. В зависимости от диаметра используются упаковки трех типоразмеров.
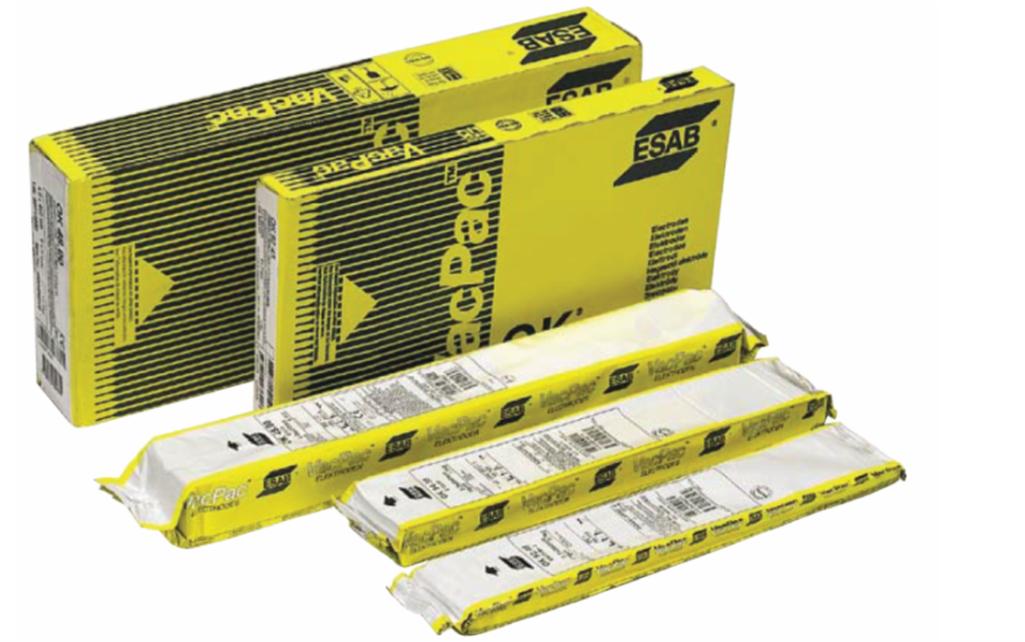
Их масса максимально адаптирована под стандартный расход электродов в течение одной смены.
Проволоки сплошного сечения для GMAW-сварки стандартных дуплексных сталей поставляются на 300милиметровых каркасных катушках, не требующих применения адаптеров, массой по 15 кг или в упаковках MarathonPac, не требующих дополнительных разматывающих устройств массой по 250 кг. Прутки для TIGсварки поставляются в пеналах по 5 кг мерной длины 1000 мм. Марки проволок сплошного сечения ESAB для сварки стандартных дуплексных сталей представлены в табл. 2. GMAW-сварку этими проволоками, предпочтительнее выполнять на оборудовании, поддерживающем режим пульсирующей дуги (MIG-puls).
Таблица 2
Вид сварки | Тип проволоки по стандарту |
Марка проволоки |
|
EN ISO 14343 | AWS A5.5 | ||
В защитном газе плавящимся электродом |
G2293NL |
ER2209 |
OK Autrod 2209 |
В защитном газе неплавящимся электродом |
W2293N L |
ER2209 |
OK Tigrod 2209 |
Для стабилизации дуги, улучшения текучести наплавленного металла и улучшения смачиваемости кромок в качестве защитного газа необходимо применять аргон с добавкой 2–3% кислорода или углекислоты. При выборе диаметра сварочной проволоки предпочтение надо отдавать диаметрам, меньшим, чем при сварке аналогичных соединений из черных сталей. TIG-сварку выполняют в чистом аргоне или аргоногелиевой смеси.
В качестве неплавящихся электродов рекомендуется применять вольфрамовые прутки, легированные церием или лантаном. При сварке с полным проплавлением необходимо обеспечивать качественную защиту корня шва.
Таблица 3
Тип наплавленного металла по стандарту |
Защитный газ по EN ISO 14175 |
Пространственное положение при сварке |
Марка проволоки |
|
EN ISO 17633-A | AWS A5.22 | |||
T2293NLPM212 | E2209T1-4 | М21 (Ar основа + 15–25% CO2) | Всепозиционное (кроме вертикали на спуск) | Shield-Bright 2209 |
Газозащитная рутиловая порошковая проволока для FCAW-сварки стандартных дуплексных сталей поставляется на 300-миллиметровых каркасных катушках массой по 15 кг или 200-миллиметровых пластиковых катушках массой по 5 кг, поставляемых в вакуумных упаковках (табл. 3). Проволока отличается великолепными сварочно-технологическими свойствами и позволяет обеспечить более высокую производительность сварки с сравнении с проволокой сплошного сечения. Сварку рекомендуется выполнять в стандартных аргоновых смесях типа 82%Ar + 18%CO2, при этом в качестве источников питания можно применять обычные трансформаторные выпрямители. Шов формируется гладкий и светлый при полном отсутствии брызг, шлак отделяется сам (рис. 4). Во всем диапазоне режимов сварка происходит в струйном процессе. Однако надо помнить, что для избежания образования зашлаковок сварку необходимо выполнять «углом назад». Также не рекомендуется сваривать толщины менее 4 мм (для тавровых соединений менее 2 мм).
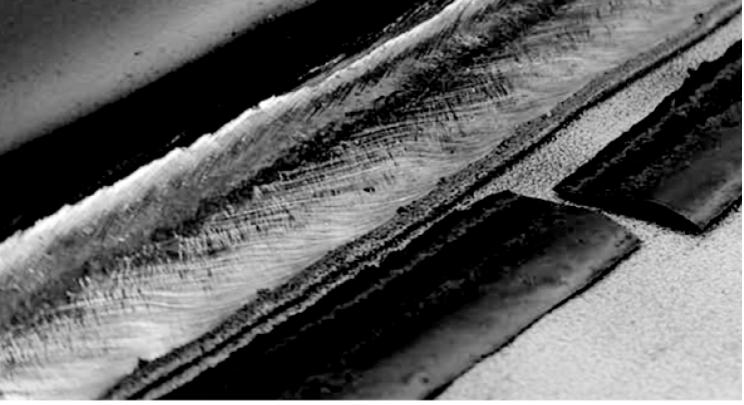
С точки зрения компании ESAB, качество – это непрерывно развивающийся процесс, который является сутью нашего производства в международном масштабе. Производственные мощности во всех странах мира, местные представительства и международная сеть независимых дистрибьюторов гарантируют нашим клиентам высокое качество и богатый опыт ESAB в области производства материалов и технологий, независимо от того, где находятся наши клиенты.