Авторы: В.В. Антонова, Д.Е. Васильев, М.С. Трещева, Ю.П. Афромеев, О.Е. Алексеев (ПАО «НОРЭ).
Опубликовано в журнале Химическая техника №2/2016
Практически любой технологический процесс на химическом производстве не обходится без использования теплообменных аппаратов, в число которых входят котлы-утилизаторы, кипятильники, подогреватели, холодильники, теплообменники и конденсаторы высокого и низкого давления, скрубберы. В связи с этим возрастает важность проведения диагностики данного типа технических устройств, в частности определения технического состояния металла теплообменных труб в трубных пучках, так как выявление дефектов в каждой трубе является залогом безотказной работы комплекса оборудования технологической цепочки в целом. При проведении данного вида диагностики широкое применение нашел такой метод неразрушающего контроля, как вихретоковый.
На примере диагностики холодильника-конденсатора, эксплуатируемого в производстве слабой азотной кислоты, рассмотрим возможности вихретокового метода контроля для определения фактического состояния наружной и внутренней поверхности теплообменных труб и выявления в них дефектов различного вида и глубины.
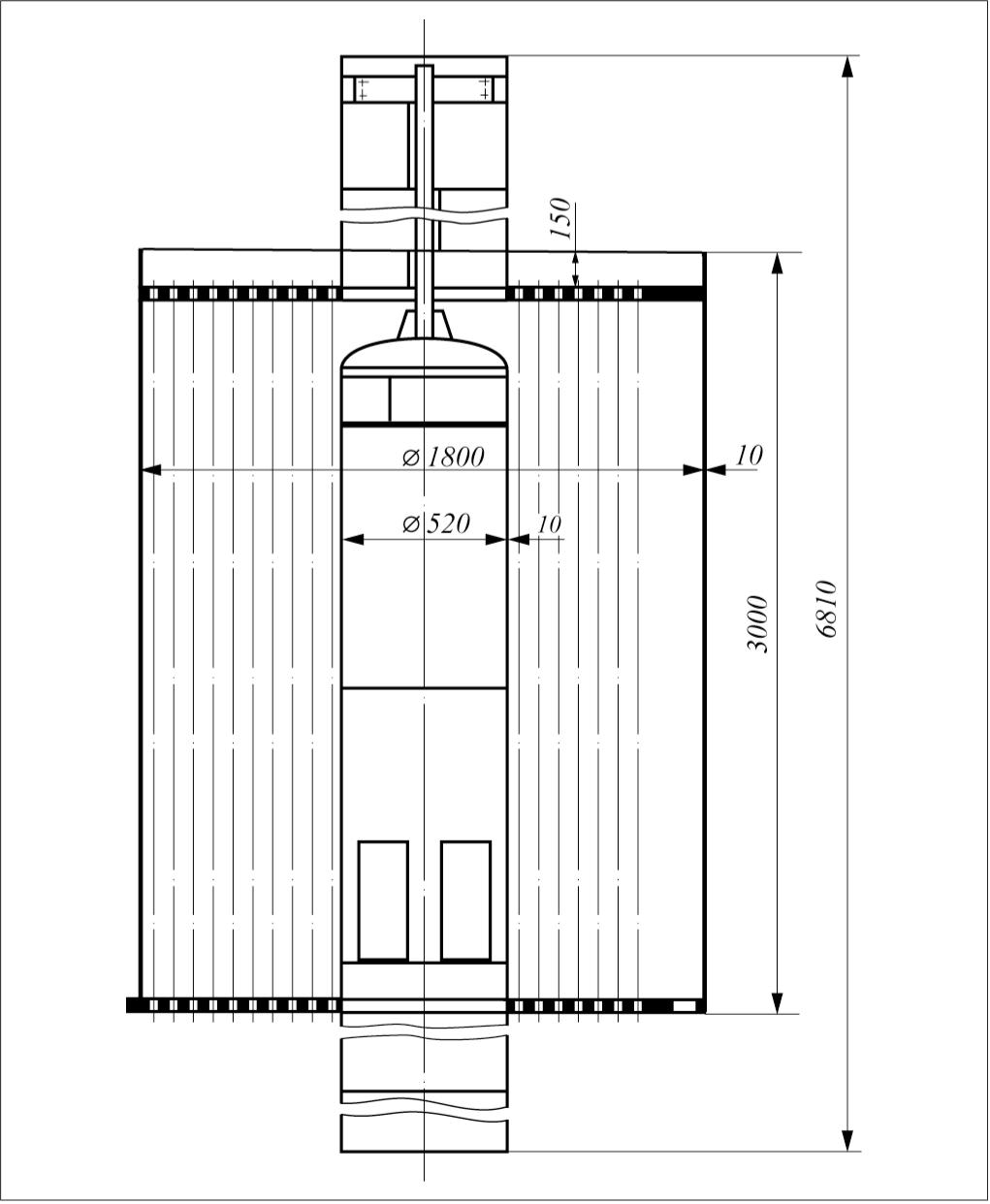
Холодильник-конденсатор (рис. 1) предназначен для охлаждения нитрозных газов, используемых для получения азотной кислоты, с частичной конденсацией кислоты из газовой фазы [1]. Охлаждение газа в холодильнике осуществляется оборотной водой, проходящей по трубам холодильника.
Азотная кислота является чрезвычайно активным коррозионным агентом в отношении большинства конструкционных материалов. Для изготовления оборудования, контактирующего с азотной кислотой, часто используют стабилизированную титаном аустенитную сталь 12Х18Н10Т как наиболее оптимальную по соотношению цена/коррозионная стойкость.
Причиной изнашивания труб и появления дефектов является конденсация нитрозных газов с образованием азотной кислоты в межтрубном пространстве холодильника-конденсатора. Интенсивность конденсации нитрозных газов определяет степень коррозионного поражения наружной поверхности труб. В начальной стадии поражение происходит практически равномерно в зоне расположения окон вытеснителя, затем зона поражения металла расширяется в основном за счет распространения ее в среднюю и верхнюю часть трубы. На трубах, имеющих протяженное наружное утонение стенки большой глубины (40–90% номинальной толщины стенки), за счет неравномерности поражения металла происходит образование отдельных язв. Дальнейший рост этих язв приводит к разрыву стенки трубы. Расположение на трубной доске труб, имеющих наружные дефекты, имеет зонный характер: большинство таких труб расположено в центральной части трубного пучка вокруг вытеснителя.
Кроме того, сталь 12Х18Н10Т может проявлять склонность к локальным коррозионным поражениям по типу межкристаллитной коррозии. Очагами коррозионных повреждений в таком случае становятся участки зоны термического влияния, локальные механические повреждения металла, зоны структурной и/или химической неоднородности металла, участки, соответствующие зазорам между трубами и трубными решетками и т.п.
Учитывая характер распределения дефектов по металлу трубного пучка и невозможность проведения осмотра наружной поверхности теплообменных труб, для разбраковки труб применяют вихретоковый контроль, позволяющий выполнять сканирование труб по всей длине.
Обследование производится с использованием системы, состоящей из универсального многочастотного вихретокового дефектоскопа «ПОЛИТЕСТ УВТП-4811», персонального компьютера типа Notebook и вихретоковых зондов типа ЗНС 01.18, специально разработанных для контроля теплообменных труб холодильникаконденсатора. Настройка дефектоскопа производится по имитаторам дефектов, изготовленных из аналогичных труб. Данным видом контроля на трубах холодильникаконденсатора надежно выявляются дефекты типа «наружное и внутреннее утонение стенки» глубиной не менее 10% номинальной толщины стенки и типа «малоразмерный дефект» (трещина, язва, раковина, закат и т.п.) глубиной не менее 15%. Погрешность при определении наружного утонения составляет ±10%, внутреннего утонения ±15%. Погрешность при определении глубины малоразмерных дефектов составляет ± 15%. Данным методом контроля не диагностируются сварные швы приварки труб к трубной доске и околошовная зона протяженностью 20 мм. Кроме того, на участке трубы в трубной доске в зоне вальцовки дефекты могут быть выявлены в местах, где нет механических задиров и наклепа металла.
Контроль (сбор данных) производится со стороны верхней трубной доски. Вихретоковым зондом ЗНС 01.18 были обследованы (записаны сигналы) все трубы холодильника-конденсатора на всю длину. Далее проводится обработка и анализ данных вихретокового контроля теплообменных труб [2]. Обработка данных вихретокового контроля заключается в просмотре массива записанных данных и выявлении сигналов от дефектов на фоне сигналов от различных мешающих факторов. Анализ данных контроля заключается в оценке типа и величины дефектов, выявленных в процессе обработки данных вихретокового контроля. Анализ данных контроля основан на амплитудно-фазовом методе выделения информации, т.е. в качестве носителя информации используются амплитуда и фаза сигнала.
По результатам контроля обнаружено 988 труб с дефектами различной глубины, среди которых:
- 24 трубы с дефектом глубиной 90% толщины стенки и более;
- 21 труба с дефектом глубиной 80% толщины стенки;
- 27 труб с дефектом глубиной 70% толщины стенки;
- 38 труб с дефектом глубиной 60% толщины стенки;
- 41 труба с дефектом глубиной 50% толщины стенки;
- 64 трубы с дефектом глубиной 40% толщины стенки;
- 60 труб с дефектом глубиной 30% толщины стенки;
- 216 труб с дефектом глубиной 20% толщины стенки;
- 497 труб с дефектом глубиной 10% толщины стенки.
Основными дефектами теплообменных труб, выявленными в ходе обследования холодильника-конденсатора, являются протяженное и локальное наружное (на фоне протяженного) утонение стенки (рис. 2). Вид этих сигналов, фиксируемых вихретоковым дефектоскопом, показан на рис. 3.

а – протяженное наружное (сквозное) утонение;
б – локальное наружное утонение
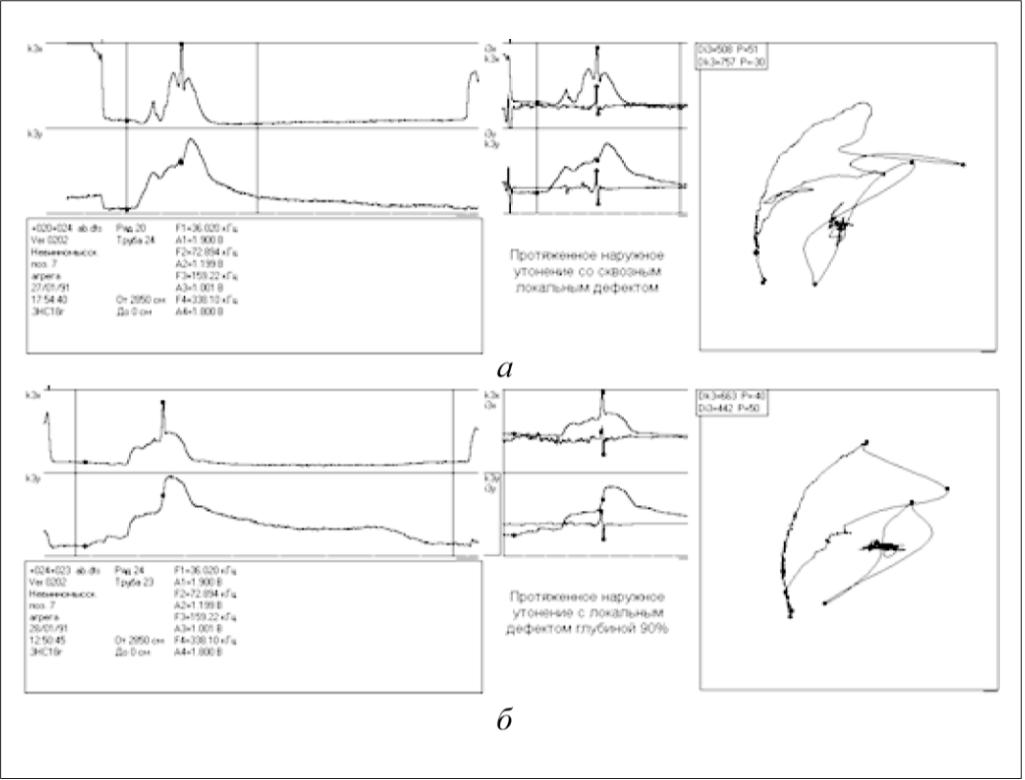
На трубах, имеющих протяженное наружное утонение стенки большой глубины (40–90% номинальной толщины стенки), за счет неравномерности поражения металла происходит образование отдельных язв. Дальнейший рост этих язв приводит к разрыву стенки трубы. Расположение на трубной доске труб, имеющих наружные дефекты, имеет зонный характер: большинство таких труб расположено в центральной части трубного пучка вокруг вытеснителя.
Следующей группой дефектов теплообменных труб, выявленных при проведении обследования холодильника-конденсатора, являются протяженные и локальные внутренние утонения стенки (рис. 4).
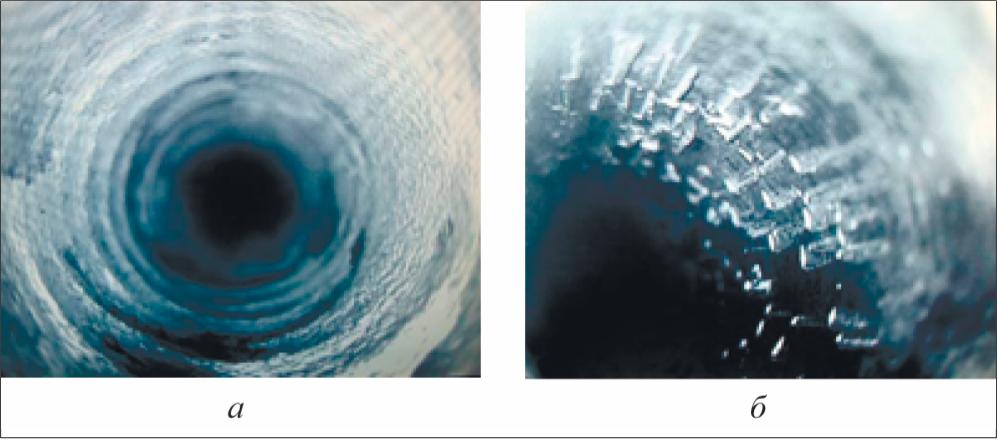
а – довальцовка (перевальцовка) труб в трубной доске;
б – внутренние механические повреждения
Как правило, на практике причиной появления внутренних дефектов (утонений) являются нарушение технологии раскатки труб на заводе-изготовителе, механические повреждения в процессе очистки труб от настенных отложений. Максимальная глубина выявленных внутренних утонений стенки составляет 30% толщины стенки трубы. Трубы с данными дефектами расположены на трубной доске беспорядочно.
Сигналы от данного вида дефектов, фиксируемые вихретоковым дефектоскопом, выглядят следующим образом (рис. 5).
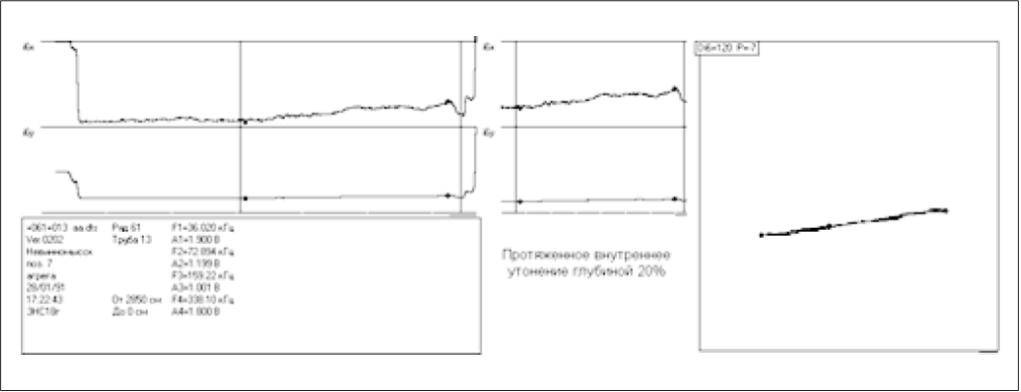
Расположение на трубной доске всех дефектных теплообменных труб с указанием максимальной глубины дефектов, показано на картограмме (рис. 6).
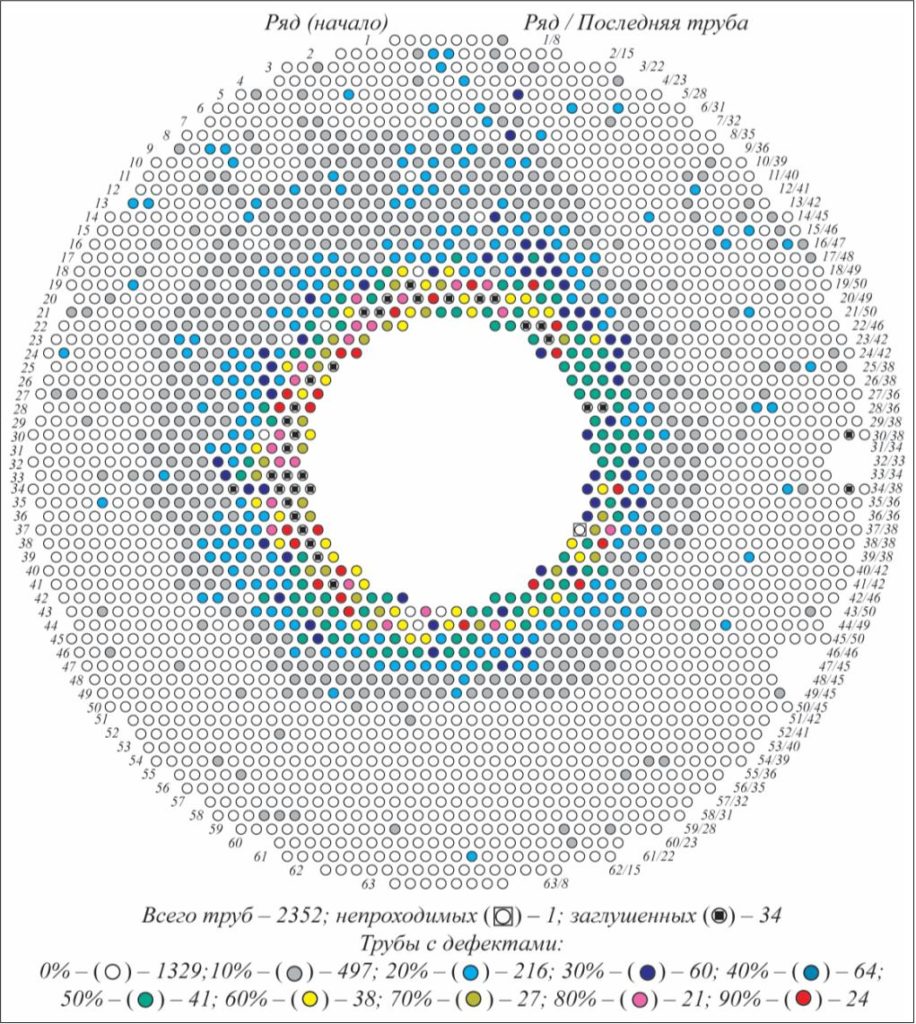
На основании заключения по результатам вихретокового контроля были выданы рекомендации по обязательному глушению 72 теплообменных труб, имеющих дефекты глубиной 70–90% номинальной толщины стенки трубы, и одной полностью непроходимой трубы 37-го ряда, а также по желательному глушению 79 теплообменных труб, имеющих дефекты глубиной 50–60% номинальной толщины стенки. Учитывая большое число выявленных критических дефектов и отсутствие данных о динамике их роста, заказчику рекомендовано провести вихретоковое обследование теплообменных труб холодильникаконденсатора через один год при соблюдении технологических режимов его эксплуатации.
Как видно из изложенного примера, вихретоковый контроль, безусловно, имеет ряд преимуществ перед гидравлическим испытанием теплообменника, связанным с большими затратами времени и усилий, а также не дающим гарантии, что через какое-то время в процессе эксплуатации не потекут другие трубы. При его использовании возможна частичная или полная замена труб в трубном пучке, не допускается протекание труб в процессе эксплуатации. При этом площадь теплообмена сохраняется, а, следовательно, соблюдаются и параметры технологического процесса. Периодический контроль вихретоковым методом обеспечивает мониторинг развития выявленных дефектов и, как следствие, дает возможность определить скорость изнашивания теплообменного оборудования в процессе эксплуатации и прогнозирование остаточного срока службы оборудования.
Список литературы
- Справочник азотчика. Под ред. Е.Я. Мельникова, Москва, «Химия», 1987г. 2. Методика вихретокового контроля теплообменных труб. 2-е изд. Обнинск: 2004.