Авторы: М.С. Трещёва, В.А. Платонов, С.В. Панченко, Ю.Н. Тюрин, С.В. Дьяконов (АО «НОРЭ»).
Опубликовано в журнале Химическая техника №11/2015
Одним из вариантов хранения жидкого аммиака, используемого в качестве сырья для производства минеральных удобрений, является хранение жидкого аммиака под избыточным давлением в горизонтальных хранилищах различной емкости.
Специалистами АО «НОРЭ» было проведено обследование резервуарного парка химического предприятия после 35 лет эксплуатации. Были обследованы 40 хранилищ жидкого аммиака вместимостью 100 м3. Обследование было выполнено в объеме, рекомендованном РД 03421–01 [1].
Хранилище жидкого аммиака представляет собой горизонтальный сосуд, работающий под давлением. Корпус выполнен из горячекатаного проката сталей 09Г2С и 16ГС по ГОСТ 5520 со стенкой толщиной 20,0 мм. Корпус хранилища опирается на седловые опоры и оборудован наружной тепловой изоляцией. Параметры работы хранилищ – разрешенное давление 1,6 МПа, температура продукта – до 40°С. Часть хранилищ оборудована паровым подогревателем. Изготовитель всех хранилищ – Первомайский завод химического машиностроения. Хранилища изготовлены и пущены в эксплуатацию в 1980 г.
На трех хранилищах были обнаружены расслоения основного металла обечайки, не выходящие на поверхность металла или сварные швы. Максимальная площадь расслоения – 7250 см2. Во всех случаях расслоения были обнаружены в нижней части корпуса. Глубина залегания расслоений – от 5 до 16 мм от внутренней поверхности корпуса.
Проектный расчет хранилищ был выполнен в соответствии с ГОСТ 14249, действовавшим на момент их проектирования. Обечайка хранилища была рассчитана как тонкостенная цилиндрическая оболочка, работающая под внутренним давлением.
Для тонкостенных цилиндрических оболочек, работающих под внутренним давлением, наибольшим является растягивающее окружное напряжение σt. Радиальное напряжение σr от внутреннего давления существенно ниже окружного и, кроме того, является сжимающим по отношению к металлу стенки и не может вызывать появление расслоений (рис. 1).
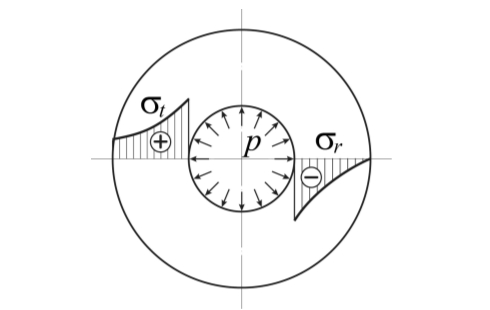
Очевидно, что появление расслоений связано с влиянием неучтенного при расчете силового фактора или иного воздействия. Было сделано предположение, что причиной появления расслоений может быть стесненность тепловых деформаций при нестационарном режиме. Режим эксплуатации хранилищ подразумевает периодический (~2 раза в год) вывод их из эксплуатации для осмотра, освидетельствования, ревизии арматуры, проверки предохранительных клапанов и т.п. Во время остановок аммиак из хранилищ полностью удаляется, а давление внутри корпуса становится равным атмосферному.
Последующее заполнение хранилищ жидким аммиаком производится наливом, при этом в первоначальный момент времени из-за разницы между давлением жидкого аммиака в подающем коллекторе (в среднем до 1,2 МПа) и давлением внутри корпуса (равного атмосферному), происходит интенсивное испарение аммиака. Подача аммиака в корпус производится через штуцер, срез патрубка которого находится в нижней части корпуса.
Весьма вероятно, что при контакте жидкого аммиака с металлом корпуса и его последующем испарении происходит локальное захолаживание металла. Внутренние холодные слои металла оказываются сжатыми относительно теплых наружных, возникает напряжение сдвига на локальном участке стенки хранилища, которое и приводит к появлению расслоения. В дальнейшем, при выравнивании давления аммиака в корпусе и коллекторе, испарение прекращается, металл стенки по всей толщине приобретает температуру, близкую к температуре хранимого жидкого аммиака, напряжение сдвига исчезает.
Отличия в локализации и глубине залегания расслоений для трех хранилищ связаны, скорее всего, с технологическими особенностями изготовления проката.
Для листового проката характерными являются технологические дефекты, которые образуются в результате несплавления при раскатке листа имеющихся в нем несплошностей: неметаллических включений, структурных неоднородностей, газовых пузырей, внутренних разрывов и т.д. Плоскость дефектов, как правило, параллельна поверхности листа. Наиболее часто указанные раскатанные несплошности представляют собой совокупность отдельных дефектов, расположенных на разных уровнях по толщине стенки на небольшом расстоянии друг от друга.
Естественно, что развитие расслоения происходит в наименее прочных зонах по сечению листа.
Расслоение является трещиноподобным дефектом (дефект с острым краем в зоне роста дефекта), который является концентратором напряжений. В соответствии с требованиями п.6.5. РД 03-421–01, для оценки возможности продления эксплуатации оборудования с дефектами такого характера, необходимо выполнить оценку трещиностойкости конструкции с обнаруженным дефектом.
Расчет на трещиностойкость требует построения аналитической модели напряженно-деформированного состояния с учетом всех действующих факторов и их взаимного влияния, что в нашем случае нестационарного режима с неопределенными значениями изменения температурных полей и внутреннего давления весьма затруднительно.
Рекомендуемый РД 03-421–03 нормативный расчет представлен в нормах прочности для атомных энергоустановок [2]. Однако методика ПНАЭ Г-7-002–86 применима лишь для оценки отдельной изолированной трещины I типа (нормальный отрыв) и не содержит нормативных рекомендаций по оценке влияния на прочность трещин III типа (продольный сдвиг, к которому относится расслоение), а также не рассматривает сложные варианты термомеханического нагружения.
Кроме того, определение значения критического коэффициента интенсивности напряжений для материала хранилища, находившегося в эксплуатации 35 лет, требует проведения испытаний, связанных с вырезкой образцов из корпуса хранилища и экспериментального определения расчетных величин, поскольку фактические свойства состаренного металла могут существенно отличаться от справочных в сторону разупрочнения [3].
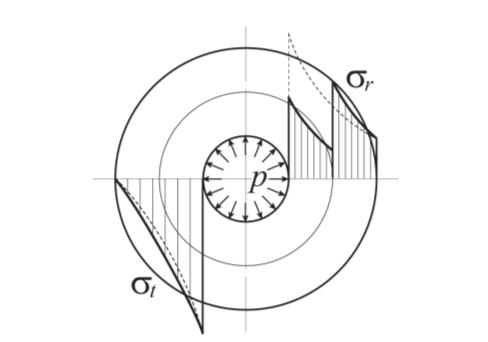
– – – – линия эпюры напряжения для однослойной оболочки
Для оценки возможного влияния имеющихся расслоений на прочность сосуда в установившихся рабочих условиях была рассмотрена модель распределения напряжений по толщине стенки в двухслойной обечайке (см. рис. 2). Из приведенной схемы видно, что в условиях многослойной обечайки происходит перераспределение растягивающих окружных напряжений σt, возникающих от действия внутреннего давления, по слоям. При этом существенно снижается пиковое напряжение на внутренней поверхности внутреннего слоя. Таким образом, металл двухслойной обечайки оказывается более равномерно нагруженным по всему сечению.
Однако оценивать расслоение как упрочняющий фактор было бы не вполне правильно. Рассмотренная модель не отражает в полной мере условия работы металла в зоне расслоения, поскольку не учитывает влияние локальных концентраторов напряжения, создаваемых расслоением. В зоне расслоения вполне могут присутствовать микронадрывы различного направления, ступеньки и другие дефекты поверхности внутри расслоения.
Наибольшую же опасность может представлять зона концентрации напряжения по фронту подрастания расслоения. Направление фронта роста трещины определяется направлением действия эквивалентного напряжения.
И, если при появлении расслоения из-за переохлаждения металла направление действия эквивалентного напряжения близко в к нормальному относительно поверхностей цилиндрической оболочки, то при установившемся режиме работы под внутренним давлением напряжение является окружным.
Если значение рабочих напряжений в зоне концентрации превысят предел прочности материала, то произойдет рост расслоения. При этом направление роста трещины будет близко к нормальному относительно поверхности и приведет к сквозному разрыву обечайки.
Для определения условий, при которых воздействие расслоения может влиять на прочность обечаек дефектных хранилищ, был выполнен акустико-эмиссионный контроль хранилищ в условиях гидравлического испытания. Контроль проводился с использованием 32-канального акустико-эмиссионного комплекса Эксперт 2000.
Специалистами было установлено, что во всех трех случаях расслоения были зафиксированы как источники АЭ 2-го класса при испытательном давлении 1,2…1,4 МПа.
Подъем давления был продолжен до 1,8 МПа, при этом активность источников АЭ оставалась на уровне 2-го класса по классификации ПБ 03-593–03 [4]. Источники 2-го класса – это активные источники, соответствующие процессам пластической деформации в металле, которая может быть связана с явлениями подрастания расслоения в металле. Было принято решение о снижении разрешенного давления ниже значения, при котором возникает опасность подрастания расслоения.
По согласованию с заказчиком разрешенное давление в хранилищах с расслоением обечайки было установлено равным 1,0 МПа (что соответствует температуре паров аммиака ~23°С).
Было рекомендовано перед заполнением хранилищ жидким аммиаком во избежание возможного захолаживания металла выполнять подъем давления в корпусе хранилища до рабочего значения, используя общую для всех хранилищ линию газообразного аммиака. Кроме того, было рекомендовано оборудовать отдельную линию сброса с предклапанов для дефектных хранилищ с давлением приемника не более 1,0 МПа. Рекомендован также ремонт с заменой дефектных участков обечайки по окончании назначенного срока эксплуатации.
Список литературы
- РД 03-421–03. Методические указания по проведению диагностирования технического состояния и определению остаточного срока службы сосудов и аппаратов.
- ПНАЭ Г-7-002–86. Правила и нормы в атомной энергетике. Нормы и методы расчета на прочность оборудования и трубопроводов атомных энергетических установок.
- Чувильдеев В.Н., Вирясова Н.Н. Деформация и разрушение конструкционных материалов: проблемы старения и ресурса.
- ПБ 03-593–03. Правила организации и проведения акустико-эмиссионного контроля сосудов, аппаратов, котлов и технологических трубопроводов.