Автор: И. Кривошапка
Опубликовано в журнале Химическая техника №7/2017
Если перефразировать известное высказывание классика для химической отрасли, то оно может иметь такой смысл: все общие проблемы отрасли похожи, каждая локальная тема является актуальной по-своему. Значит, именно им стоит уделять гораздо больше внимания, чем общим вопросам.
Об этом, в частности, говорили участники конференции «Современные технологии и оборудование в производстве азотных и сложных удобрений (синтез, гранулирование, классификация, сушка)», которая прошла 14–15 июня на базе ООО «ФосАгро-Череповец».
Об этом, в частности, говорили участники конференции «Современные технологии и оборудование в производстве азотных и сложных удобрений (синтез, гранулирование, классификация, сушка)», которая прошла 14–15 июня на базе ООО «ФосАгро-Череповец».
«Нынешняя тема конференции обозначена отраслевым трендом в его широком понимании – «Современные технологии и оборудование в производстве азотных и сложных удобрений (синтез, гранулирование, классификация, сушка), – рассказал ведущий специалист управления развития химических производств «ФосАгро-Череповец» Юрий Горбунов. – Если образно представить градус охвата заинтересованных в этой теме участников, то можно смело говорить о 270 градусах из 360. Несмотря на то, что состав гостей и спикеров таких конференций постоянно меняется, мы часто встречаемся с постоянными посетителями. Стоит отметить, что в этом году в мероприятии участвовали более 80% новых гостей, в том числе и представителей иностранных компаний, намеренных сотрудничать с российской химической отраслью».
Соорганизатором мероприятия выступила компания «Инфохим» – традиционный инициатор подобных тематических встреч специалистов, где охватывается широкий спектр самых разных проблем, отраслевых вопросов и инновационных решений. Часто мероприятия «Инфохим» проходят на территории производств минеральных удобрений – возможно, неслучайно, в этом году такой площадкой стал «ФосАгро-Череповец».
«Мы ориентируемся на производителей продуктов. Когда на предприятии возникают проблемы, специалистам необходима дополнительная информация, поэтому мы предоставили право самому «ФосАгро-Череповец» выбрать тему, – сказал генеральный директор «Инфохим» Константин Чернышов. – В этой конференции участвовали производители удобрений из России и стран СНГ, отраслевые компании, научные специалисты и для них это хорошая площадка, чтобы высказать свое мнение по разным вопросам. Отмечу, что представители компаний из дальнего зарубежья охотно интересуются российским опытом и делятся своими технологиями с нами. Кстати, с введением экономических санкций количество иностранных компаний, проявляющих интерес к российским решениям в области химии, возросло в 2,5 раза».
В ходе конференции выступили 22 докладчика, которые представили свои доклады касательно перевооружения отечественных предприятий химической промышленности, новых технологий, решений и материалов, а также новых программ, методов и схем производства минеральных удобрений.
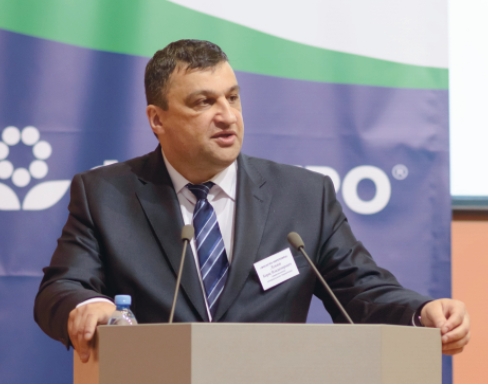
«Конференция совпала с важной вехой деятельности компании «ФосАгро-Череповец» – завершением строительно-монтажных работ и пусконаладки на новом, уже третьем крупнотоннажном агрегате по производству аммиака мощностью 2200 т в сутки, – открыл конференцию презентацией нового производства заместитель генерального директора АО «ФосАгро-Череповец» Борис Левин.
Он рассказал, что строительство началось около трех лет назад, в нем приняли участие российские, японские и датские компании. Идея создания нового производства возникла несколько лет назад, когда для производства азотных удобрений аммиак приходилось закупать за рубежом, и этих объемов сырья явно не хватало. С пуском нового агрегата в Череповце будут также производить новый вид удобрений – гранулированный карбамид, его химики планируют выпускать в больших объемах – до 500 000 т в год. Аграрии оценивают перспективы этого удобрения более чем оптимистично – в прошлом году спрос на него вырос на 30%. Новое производство удовлетворит существующий спрос на удобрение и создаст новые рабочие места. За счет этой линии площадка в Череповце станет ведущей в России по производству карбамида.
Ввод нового агрегата позволит также «ФосАгро-Череповец» реализовать намеченный план по увеличению объемов производства и расширению продукции в рамках стратегии развития до 2020 года, которая предусматривает дальнейшее освоение инновационных технологий и решений для создания новых добавок для производства удобрений.
Действительно, за последние два года Череповец серьезно продвинулся в развитии бизнес- направлений. Об этом рассказала генеральный директор АНО «Инвестиционное агентство «Череповец» Оксана Андреева.
В настоящее время агентство совместно с одним из ведущих градообразующих предприятий региона – ПАО «Северсталь» – активно содействует субъектам малого и среднего бизнеса. В современном бизнес-городе Череповце сегодня функционируют более 20000 субъектов малого и среднего предпринимательства. Кроме того, в соответствии с Постановлением Правительства РФ, городу будет присвоен статус территории опережающего социально-экономического развития, который даст множество преимуществ в части налоговых льгот, притока инвестиций, создания новых рабочих мест. Стратегической целью ближайших пяти лет стало формирование благоприятного инвестиционного климата и поддержки бизнеса. Уже сейчас в Череповце создан и работает индустриальный парк, предоставляющий земельные участки под промышленное производство. Часть данной инвестиционной площадки занимают предприятия «ФосАгро».
Оправданные инновации
Экономика зависит от новых решений, способных, если и не совершить революцию в отрасли, но существенно поднять ее уровень и нарастить объемы производства многих современных продуктов. О гибких технологиях фосфорсодержащих удобрений с использованием агрегатов БГС рассказал директор по промышленной технологии АО «НИУИФ» Андрей Норов.
«Гибкая технология позволяет производить широкий ассортимент удобрений на одной технологической линии, – отметил А. Норов. – Безусловно, затраты в данном случае будут несколько выше, чем под монопродукт, и плюс возникнет необходимость переработки переходных продуктов. Но в целом в условиях рыночной экономики эта технология себя оправдывает».
В доказательство сказанному спикер привел некоторые очевидные преимущества технологических линий, укомплектованных аппаратами БГС. Они позволяют получать гранулированные удобрения из пульп с высокой влажностью (40% и более); содержат меньшее число единиц оборудования, что, в свою очередь, снижает капитальные затраты на их создание, расход электроэнергии, на ремонт, а также повышает их надежность и увеличивает эффективный рабочий фонд времени; имеют сравнительно небольшой внешний ретур (в некоторых схемах он совсем отсутствует), что позволяет использовать транспортное оборудование меньшей производительности (и, соответственно, с меньшей стоимостью) и также снижает энергозатраты.
Автор также сравнил прежние аналоги технологических линий и инновационные разработки, представил подробную схему гибких технологических схем производства фосфорсодержащих удобрений с использованием аппарата БГС и схемы получения PKS- и NPKS-удобрений, подчеркнув, что универсальные, компактные и экономичные схемы, оснащенные БГС, совмещающие в одном аппарате процессы гранулирования и сушки, имеют хорошую перспективу и могут быть альтернативой традиционным схемам АГ-СБ.
О гранулировании азотных продуктов рассказал Тьерри Ламазере, представляющий компанию CFih, которая совсем недавно продемонстрировала свои возможности в производстве NPK удобрений посредством пуска завода ELIXIR-ZORCA в Сербии (от 700 до 1200 тонн в сути NPK/GSSP/GTSP) с возможность производства более 100 формул. По словам г-на Ламазере, это стало возможным за счет использования собственных технологий, таких как барабанный аппарат для вызревания и специфический реактор. Был также успешно реализован проект в нитрофосфатном производстве на заводе FATIMA 1200 т в сутки приллированных NP продуктов и специальных удобрений. Еще один проект – по производству водорастворимых NPK удобрений – был продемонстрирован на заводе ZUARU-ROTEM в Индии.
В части некоторых подробностей технологии спикер рассказал, что согласно схеме гранулирования CFIh, чистый сульфат аммония (AS), а также смешанный продукт карбамида и аммиачной селитры (UAS) гранулируются по классической схеме с помощью классического агломерационного барабанного гранулятора (оснащенного трубчатым реактором в случае использования серной кислоты), за которым устанавливается сушильный барабан. В случае производства UAS следует рассмотреть специальные условия в сушильном барабане из-за присутствия карбамида. Этот же процесс может использоваться для производства MAP/DAP/NPK, т.е. один цех может быть приспособлен для производства гранулированных AS и UAS.
Аммиачная селитра (AN), известково-аммиачная селитра (CAN) и сульфат нитрат аммония (ASN) гранулируются в едином барабанном грануляторе-сушилке, который имеет две секции: в первой секции производится непосредственно гранулирование с помощью напыления жидкой фазы через атомизирующие пистолеты на твердую фазу, образованную рециркулирующимися гранулами; во второй секции производится сушка гранул. Для удаления воды из плава или пульпы вводится горячий воздух в одном направлении с движением рецикла и распыления.
Свои разработки представили также специалисты «Полипласт Северо-Запад». Они рассказали о добавках производства компании – антислеживателей «Полиламин» и добавках, предназначенных для уменьшения количества ретура и увеличения крепости гранул при производстве минеральных удобрений методом прессования.
Директор по продажам в России и СНГ компании ROTEX Илья Гольдин представил вниманию гостей конференции грохоты для производств азотных и сложных удобрений. В частности, специалист рассказал о стандартах грохотов в производстве карбамида: оборудование одобрено всеми лицензиарами (Toyo, Stamicarbon, UFT, Saipem и т.д.). Максимальная производительность одной единицы оборудования –до 2300 т/сутки готового продукта. Степень извлечения товарного класса – 90%. Спикер отметил, что подавляющее большинство предприятий, выпускающих гранулированный карбамид,
и примерно 60% заводов, выпускающих приллированные удобрения, используют оснащение ROTEX.
и примерно 60% заводов, выпускающих приллированные удобрения, используют оснащение ROTEX.
Об энергоэффективном методе охлаждения минеральных удобрений, опыте применения охладителей Solex с референц-листом компании, а также сведениями о сотрудничестве Solex и производителями NPK в СНГ рассказал технический директор Solex Thermal Science inc Василий Вильдяев. В частности, он поделился опытом сотрудничества с Гомельским химическим заводом (ГХЗ) в 2006 г. Еще за три года до этого, в 2013 г. была доставлена в РФ Пилотная установка Bulkflow-Solex
и дважды проведены испытания в производственных условиях в июне и в ноябре. Результаты испытаний, в том числе охлаждение до указанных температур, стабильность движения сыпучего продукта, были признаны удовлетворительными. В апреле 2012 г. компания Solex организовала визит для представителей ГХЗ на предприятие AgroLinz в Австрии для ознакомления с условиями эксплуатации ранее установленных на данном предприятии двух охладителей NPK и охладителя CAN, разработанных и изготовленных компанией Bulkflow Technologies.
и дважды проведены испытания в производственных условиях в июне и в ноябре. Результаты испытаний, в том числе охлаждение до указанных температур, стабильность движения сыпучего продукта, были признаны удовлетворительными. В апреле 2012 г. компания Solex организовала визит для представителей ГХЗ на предприятие AgroLinz в Австрии для ознакомления с условиями эксплуатации ранее установленных на данном предприятии двух охладителей NPK и охладителя CAN, разработанных и изготовленных компанией Bulkflow Technologies.
Еще одним показательным этапом деятельности компании стал совместный с ПАО «Дорогобуж» проект. В июле 2006 г. компания Solex организовала визит для представителей Дорогобуж на канадские предприятия в Калгари и в Эдмонтоне для ознакомления с условиями эксплуатации ранее установленных охладителей карбамида и пористой аммиачной селитры, разработанных и изготовленных компанией Bulkflow Technologies.
Компания также представила специально для «Фос-Агро-Череповец» нагнетатель воздуха для создания воздушного затвора в загрузочном бункере с целью препятствования проникновения влажного горячего воздуха в зону охлаждения.
Представитель компании Aumund Fordertechnik GmBh – руководитель по развитию бизнеса Степан Хлопенков – рассказал о конвейерных решениях. В своем выступлении инженер по продажам центробежных компрессоров Howden Виктор Сафронов остановился на компрессорных технологиях компании, применяющихся в области основных процессов производства минеральных удобрений.
О специализированных технических решениях в расходомерах «ЭМИС» для производства азотных и сложных удобрений, эффективности использования, функциональных возможностях, а также об опыте поставок приборов на предприятия отрасли рассказал руководитель отдела регионального развития компании «ЭМИС» Дмитрий Бахмутов.
Решения для трудно фильтруемых растворов на производствах минеральных удобрений (свечные фильтры DrM) продемонстрировал технический специалист компании «ИнтраТул» по направлению фильтрации промышленных жидкостей Олег Баринов. Он, в частности, рассказал о решении по фильтрации промышленных растворов.
В данном случае речь шла о фильтре-установке на базе свечевых фильтров, производимых швейцарской компанией «Доктор Мюллер».
В данном случае речь шла о фильтре-установке на базе свечевых фильтров, производимых швейцарской компанией «Доктор Мюллер».
«Модельный ряд представлен двумя типами принципиально одинаковых фильтров – Fundabac и Contibac, – отметил Баринов. – В обоих случаях фильтр представляет из себя изолированную цилиндрическую емкость с коническим днищем, внутрь емкости подается загрязненная среда. Она продавливается сквозь фильтрующие элементы и отводится по трубной решетке регистра наружу».
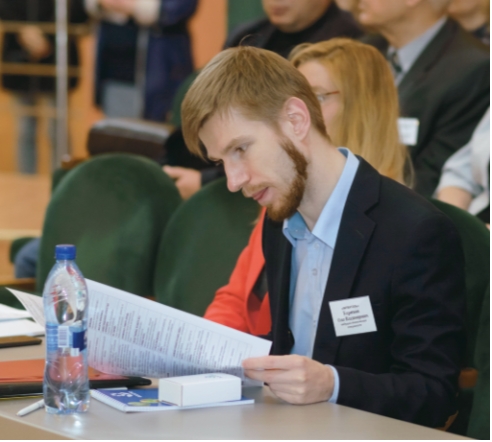
По словам эксперта, системы с данными фильтрами достаточно гибки в применении. При этом наиболее экономически выгодны эти системы при решении таких задач, как фильтрация токсичных и опасных рабочие среды, трудно фильтруемых сред. Примером реализации преимуществ представленных фильтров на производствах минеральных удобрений, по словам О. Баринова, может служить применение систем в процессах фильтрации экстракционной фосфорной кислоты. Так, в настоящее время проводятся испытания малотоннажной фильтр-установки на производстве в Польше. В ходе испытаний достигается цель получения чистого раствора ЭФК после одностадийной фильтрации с более тщательной отмывкой фосфогипса, чем ранее. При этом в отличие от традиционной схемы производства фосфогипс высушивают в фильтре и отправляют на утилизацию вместо возвращения обратно в процесс синтеза. В России пилотные испытания были проведены при очистке ЭФК дигидратного и полугидратного процессов. В результате была достигнута цель – получены чистые растворы ЭФК.
Другим примером использования фильтр-установки в производствах минеральных удобрений стал процесс фильтрации раствора магнезиальной добавки для приготовления неслеживаемой аммиачной селитры на польском заводе в Пылавы. Магнезиальная добавка представляет из себя раствор нитрата магния, получаемый при растворении в азотной кислоте ископаемого магнезита. Далее кислый раствор нейтрализуют. Затем его необходимо отфильтровать от побочных продуктов и солей, выпавших в осадок в ходе нейтрализации. Если по ошибке раствор довести до щелочной реакции, то сложность фильтрации многократно возрастает, так как осадок принимает желеобразную клейкую консистенцию. Применение автоматического фильтра позволило отказаться от применения отстойника и фильтр-пресса, при этом степень чистоты повысилась до требуемого значения.
Впервые в отраслевой конференции участвовала чешская компания VINXIA Engineering a.s.. Ее представитель Олда Микуш рассказал о компании, которая стала результатом совместной договоренности между Tecnimont S.p.A., Stamicarbon B.V. и Unis a.s. и была основана в Праге как партнер, ориентированный на клиента по вопросам оптимизации уже существующих заводов и разработки новых возможностей для более крупных проектов реконструкции в промышленности удобрений в странах СНГ и Восточной Европе, в том числе касающихся инжиниринга (консультационные и технико-экономические услуги, базовое проектирование, рабочая документация), закупок оборудования; строительства и/или управления строительством; (суб)лицензирования процесса на индивидуальной основе для всех технологий Stamicarbon.
В своем выступлении О. Микуш также подробно остановился на описании процесса и оборудования для гранулирования карбамида с добавкой серы.
Оборудование и аппараты компании «Кремсмюллер» для химической промышленности – от расчетов, проектирования и изготовления до монтажа на месте – представил региональный директор компании Виктор Биленький, остановившийся на истории компании и современных проектах.
Дополнительные бонусы программы
В рамках деловой программы конференции выступили также представители компаний сопутствующих отраслей и направлений, продукция которых используется для производства минеральных удобрений. Так, в своей презентации коммерческий директор АМС, эксклюзивного представителя компании GEMACO S.A. (Бельгия) Максим Васильченко рассказал о трубопроводной продукции из коррозионно-стойких марок стали в различных товарных формах: листы, круглый прокат, поковки, трубы и фитинги.
Поясняя специфику производства карбамида и азотной кислоты с точки зрения коррозии и применяемых материалов, спикер рассказал, что может предложить компания Gemaco в зависимости от потребностей заказчика и требований к тому или иному материалу.
«При участии химиков-технологов различных заводов мы можем оказать помощь в выборе материала в зависимости от рабочей среды, – сказал М. Васильченко. – Мы предлагаем полную гамму трубной продукции во многих товарных и производственных формах и являемся таким образом единым поставщиком, совмещающим преимущества заводского производства с гибкостью складских поставок, таким образом, значительно сокращая сроки поставки. Наша компания работает с европейскими заводами, утвержденными и прошедшими квалификацию (суб)подрядчиками, способными выполнить самые разнообразные специфические требования и обладающими производственными мощностями, возможностью осуществить послесварочную термообработку, травление и пассивацию».
Двухдневная программа конференции включала также экскурсию по фосфорному комплексу «ФосАгро-Череповец». Под руководством представителя управления развития химических производств «ФосАгро-Череповец» Андрея Шибнева гостям показали четыре технологические нитки производства серной кислоты. В продолжение знакомства с заводом участникам продемонстрировали технологические нитки производства фосфорной кислоты, а также новый цех по производству фторида алюминия – это совместный проект «ФосАгро-Череповец» и РУСАЛ мощностью 43 000 т продукции в год, и это почти половина потребности всего РУСАЛА во фториде алюминия. Далее гости увидели промышленный порт, с которого осуществляется транспортировка удобрений заказчикам, с которыми может быть только морское и речное сообщение. Как рассказал А. Шибнев, в настоящее время ежегодные объемы производства предприятия – около 5,5 млн. т удобрений, из них 1,6 млн. – азотные, остальное – фосфорные. На этот год планируется производство порядка 6 млн. т удобрений, 70 % которых поставляется на российский рынок.
На конференции прозвучало много интересных выступлений и были представлены любопытные решения. По мнению Бориса Левина, часто на таких мероприятиях находятся решения текущих задач компании. Есть также идеи, которые, возможно, очень скоро трансформируются в темы новых научных разработок.
«Есть проектные задачи, решить которые может объединение участников с их компетенциями, – отметил Б. Левин. – И даже несмотря на то, что это не всегда готовые решения, они созревают. У нас сформировано ядро, которое постоянно наполняется новым содержанием, а информационное поле дает толчок к дальнейшим решениям задач».
Конференция традиционно проводится на разных площадках. Где она пройдет в следующий раз, пока не известно. Но представили «ФосАгро-Череповец» надеются, что через год–два на предприятии будут введены новые мощности, и тогда возникнут новые задачи, значит, и новая конференция будет обеспечена тематикой.
Мнения участников
Илья Гольдин, директор по продажам в России и СНГ, ROTEX:
«Наша компания несколько раз участвовала в этих конференциях, и в этом году мы представляем решения для классификации сухих сыпучих материалов по размеру. Мы представляем зарубежного производителя, которому уже 170 лет, он владеет богатым опытом, которым может поделиться. У нас есть достаточно уникальные решения для российского рынка. Например, технология, позволяющая сократить переналадку грохота до 6…7 минут, и это поистине революционная технология. Это оборудование достаточно легко адаптируется к существующему производственному циклу – его уже приобрели коллеги из «Уралхима», ГК «Акрон», Дорогобужа.
Что касается тематики конференции, то хочу отметить, что ее организаторы – очень искушенные люди в науке, различных аспектах производства, поэтому
на этих конференциях тема четко выражена и является актуальной всегда.
на этих конференциях тема четко выражена и является актуальной всегда.
В качестве предложения могу отметить, что есть компании, заводы в СНГ, которые производят подобные продукты, и можно было бы расширить круг участников, пригласив специалистов заводов.
Есть разные виды удобрений, разных текстур и составов, но проблемы всегда одни и те же – как сделать предприятия более эффективным, как увеличить производительность труда, как тратить меньше электроэнергии в единицу времени. Все это вопросы производительности и эффективности предприятия, и они важны, потому что потери кроются в разных точках, значит, задача конференции и состоит в поиске и «расшивании» этих спорных точек, получении более совершенного производства, способного сэкономить для бюджетов компаний десятки и сотни миллионов рублей в год. Это возможно за счет использования комплекса мер, включая правильные технологии, правильный подбор оборудования.
Павел Амосов, начальник цеха «Ангарский азотно-туковый завод»:
«Конференция дает возможность пообщаться с коллегами из родственных предприятий, поделиться существующими проблемами и путями их решения. Мы также можем узнать новинки из мира технологий, «примерить» их к своему производству. На таких мероприятиях всегда завязываются полезные знакомства. И в целом такие конференции служат толчком к развитию многих проектов, совершенствующих азотную промышленность».
Роман Захаров, руководитель группы развития отдела технического развития Кемеровского АО «Азот»:
«Участвуя в конференции, мы узнаем о новых разработках, потому что в этой сфере постоянно появляется что-то современное и, если никуда не выезжать, то невозможно узнать об инновациях. Кроме того, такие встречи позволяют наладить связи, перенять опыт коллег. А посещение промплощадки чрезвычайно полезно для технических специалистов, здесь можно посмотреть, как работают производства, узнать, довольны ли специалисты работой. Нам интересен их опыт. Основная проблема большинства заводов – старые технологии, в основном все агрегаты 1970-х годов, и проблема модернизации мощностей – общая для всех. Конференция позволяет ознакомиться с решениями, которые позволяют повысить эффективность производства и, возможно, внедрить новое оборудование. Мы всегда ориентируемся на заказчика и стараемся удовлетворить запросы клиентов. Сейчас, например, строим установку короткой тепловой абсорбции для получения водорода – в этом году она должна быть запущена. К 2018 г. ожидаем запустить производство карбамидно-аммиачной смеси – это комплексные жидкие удобрения, сочетающие несколько форм азота, при этом они начинают работать сразу и лучше усваиваются, чем гранулированные удобрения. Линия будет мощностью 150 000 т в год с возможностью увеличения за счет роста спроса на продукцию. И пока этот спрос есть».