Авторы: А.Н. Иванова, Ф.С. Советин, Т.Н. Гартман, Э.А. Шакина, К.И. Шаталов (РХТУ им. Д. И. Менделеева).
Опубликовано в журнале Химическая техника №12/2018
С применением комплекса программ CHEMCAD реализован эволюционный алгоритм синтеза энергосберегающих установок ректификации. Разработаны компьютерные модели четырех различных вариантов технологических схем ректификации углеводородного конденсата в производстве стирола из этилбензола. Выбрана наиболее энергосберегающая установка ректификации из 5 предложенных.
Нефтехимическая промышленность – одна из важнейших отраслей экономики России. Продукты, производимые на нефтехимических предприятиях, востребованы как на отечественном рынке, так на зарубежных рынках. Стирол – один из наиболее значимых продуктов нефтехимии, который находит широкое применение в химической промышленности и является сырьем для производства самых различных материалов от полистирольных пластмасс до лакокрасочных материалов [1].
Основным методом получения стирола является каталитическое дегидрирование этилбензола. Однако в данном процессе наряду со стиролом образуются побочные продукты – бензол и толуол [2]. Разделение углеводородного конденсата на фракции и выделение целевого продукта производится в отделении ректификации.
Ректификация является одним из основных процессов химической, нефтехимической, нефтеперерабатывающей и смежных отраслей промышленности и характеризуется большой энергоемкостью из-за высоких энтальпий парообразования некоторых компонентов смесей. Снижение энергозатрат данного процесса на сегодняшний день остается важной и актуальной проблемой в химической технологии [3–6].
Для исследования любого химико-технологического процесса и химического производства в целом (в частности, технологической схемы дегидрирования этилбензола) немаловажным является создание его модели [7–10]. Проведение моделирования, исследования и разработок энергосберегающих технологий не представляется возможным без современных комплексов программ, которые позволяют оптимизировать режимы работы производства и решать технологические задачи в ходе их разработки [10–11]. Одним из них является комплекс программ CHEMCAD. Кроме того, в комплексе программ CHEMCAD имеется возможность проводить без материальных и временных затрат многократные вычислительные эксперименты на моделях технологических схем химико-технологических процессов в целом и разрабатывать наименее энергоемкие варианты технологий [11].
Таким образом, модификация технологической схемы ректификации сводится к разработке наименее энергозатратной установки сравнением суммарных тепловых нагрузок для различных вариантов технологического оформления данных схем [12–15].
Для разделения продуктов углеводородного конденсата на чистые компоненты существует пять различных вариантов технологического оформления процесса ректификации четырехкомпонентной смеси, отличающиеся порядком разделения компонентов [3]. В работе [16] разработана компьютерная модель одного из них (рис. 1). Суммарная тепловая нагрузка данной технологической схемы ректификации – 1 317 192,85 МДж/ч. Однако необходимо дополнительно проанализировать альтернативные варианты технологического оформления узла ректификации производства стирола из этилбензола и выбрать из них наиболее энергосберегающую технологическую схему ректификации.
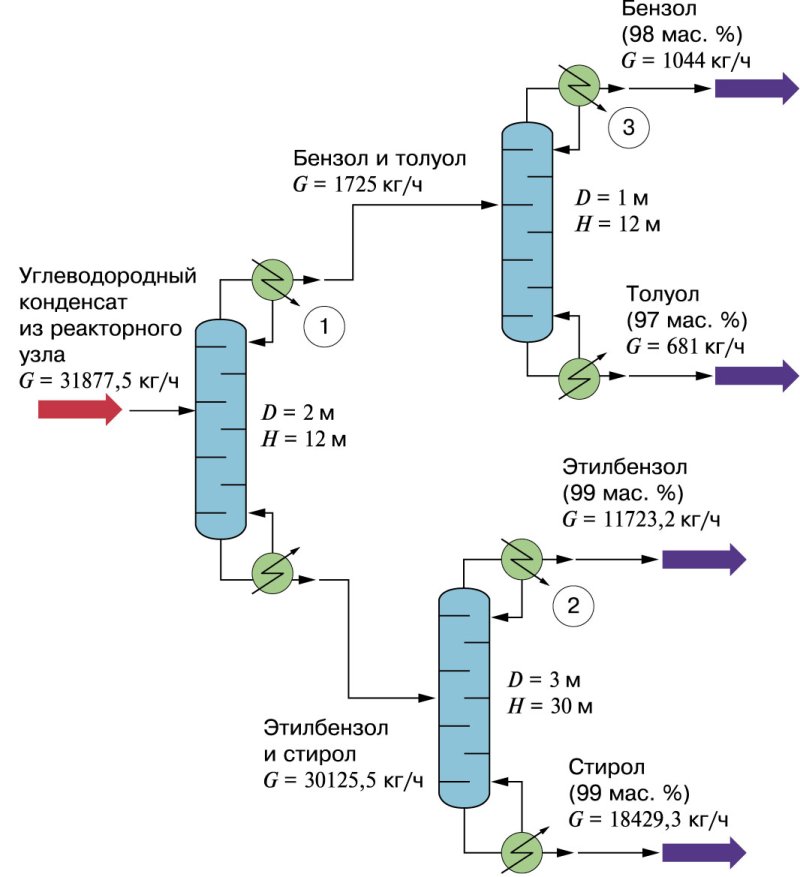
В рассматриваемой работе решается задача синтеза энергосберегающей технологической схемы ректификации многокомпонентной смеси аренов углеводородного конденсата в производстве стирола из этилбензола. Нами были разработаны и реализованы четыре альтернативных варианта.
Состав смеси, подаваемой на ректификацию: 57,6 мас. % стирола, 37,0 мас. % этилбензола, 2,2 мас. % толуола, 3,2 мас. % бензола (производительность по сырью G = 31 877,5 кг/ч). Данный состав исходной смеси был заимствован из работы [16].
При разработке компьютерных моделей было принято допущение, что все колонны простые (без боковых отпарных секций и потоков циркуляционного орошения), тарельчатые (тип тарелок – ситчатые) с последовательным соединением между собой. Во всех колоннах используются полные конденсаторы. Разработка и реализация компьютерных моделей технологических схем ректификации в данной работе проведена варьированием флегмового R или парового S чисел, а также расходов кубового остатка W или дистиллята D (табл.1). При этом были выделены чистые или практически чистые компоненты. Для моделирования процессов ректификации во всех тарельчатых колоннах используется алгоритм Inside/Out [17–18].
Таблица 1
Режимные параметры ректификационных колонн для различных вариантов технологических схем ректификации
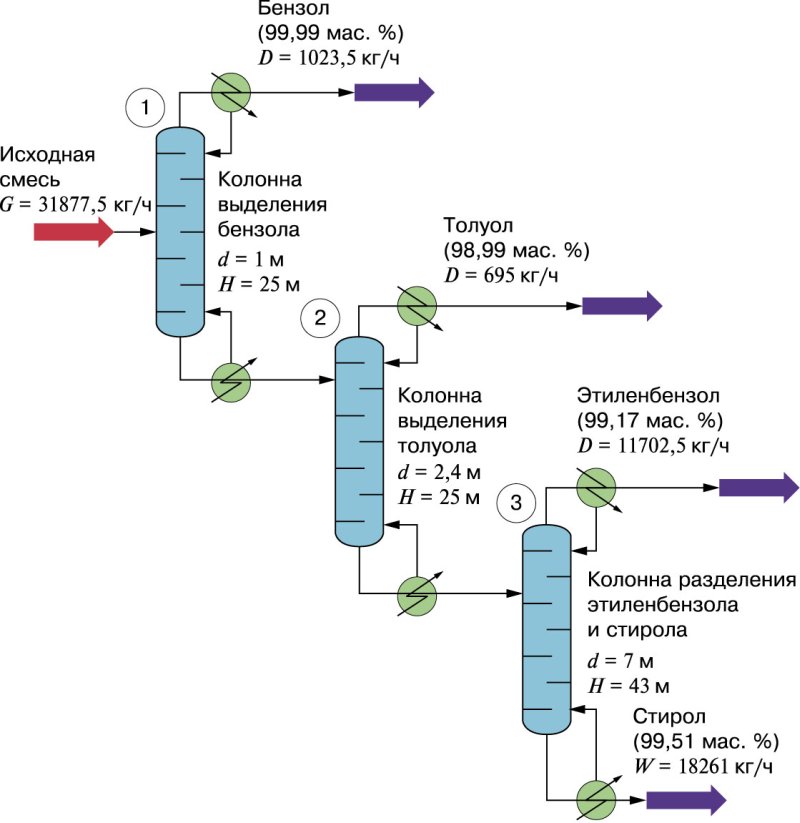
В технологической схеме №1 (рис. 2) исходный поток смеси поступает в колонну №1 (колонна выделения бензола), в которой происходит отделение бензола. Кубовый остаток колонны №1 поступает в колонну №2 (колонна выделения толуола), где от смеси отделяется толуол. Затем кубовый остаток колонны №2 поступает в колонну №3 (колонна разделения этилбензола и стирола), где происходит разделение на два жидких потока: дистиллят – этилбензол и кубовый остаток – стирол.
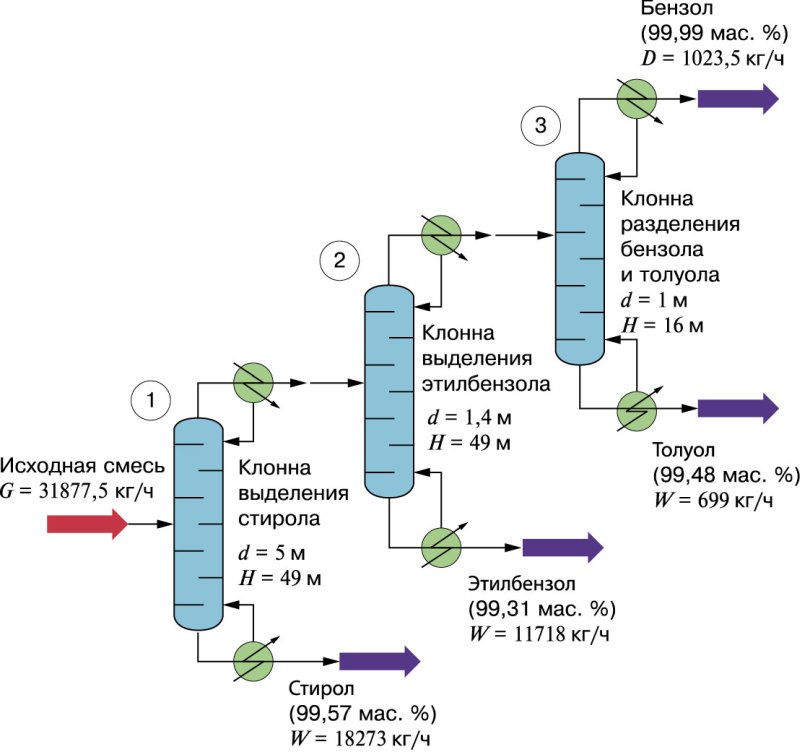
В технологической схеме №2 (рис. 3) исходный поток смеси поступает в колонну №1 (колонна выделения стирола), в которой происходит отделение стирола в виде кубового остатка. Дистиллят колонны №1 поступает в колонну №2 (колонна выделения этилбензола), где в кубе колонны от смеси отделяется этилбензол. Затем дистиллят колонны №2 поступает в колонну №3 (колонна разделения бензола и толуола), где происходит разделение легколетучих компонентов исходной смеси на два жидких потока: дистиллят – бензол и кубовый остаток – толуол.
В технологической схеме №3 (рис. 4) исходный поток смеси поступает в колонну №1 (колонна выделения бензола), в которой происходит отделение бензола. Кубовый остаток колонны №1 поступает в колонну №2 (колонна выделения стирола), где от смеси отделяется самый высококипящий компонент – стирол. Затем дистиллят колонны №2 поступает в колонну №3 (колонна разделения толуола и этилбензола), где происходит разделение на два жидких потока: дистиллят – толуол и кубовый остаток – этилбензол.
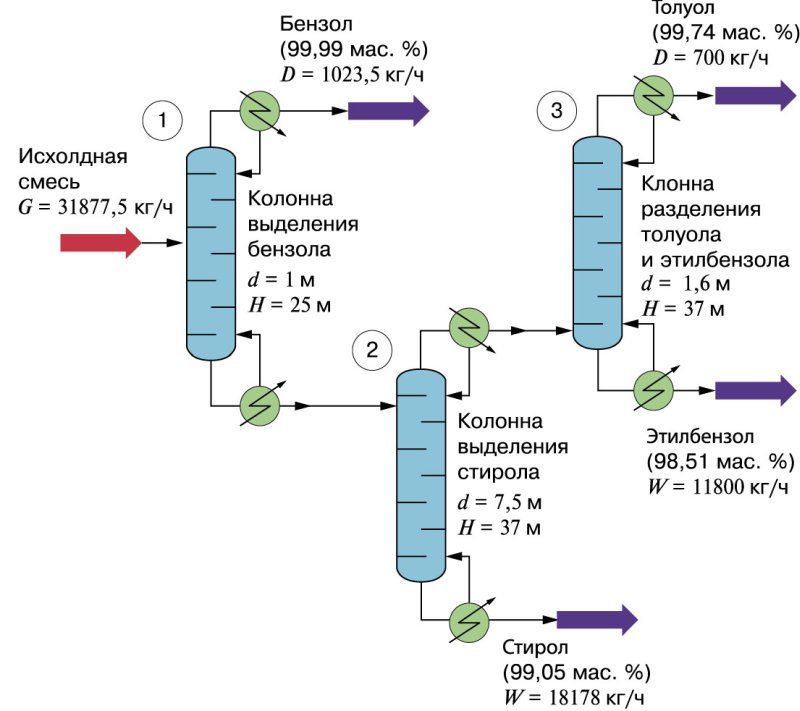
В технологической схеме №4 (рис. 5) исходный поток смеси поступает в колонну №1 (колонна выделения стирола), в которой происходит отделение стирола в виде кубового остатка. Дистиллят колонны №1 поступает в колонну №2 (колонна выделения бензола), где от смеси отделяется бензол в виде дистиллята. Затем кубовый остаток колонны №2 поступает в колонну №3 (колонна разделения толуола и этилбензола), где происходит разделение на два жидких потока: дистиллят – толуол и кубовый остаток – этилбензол.
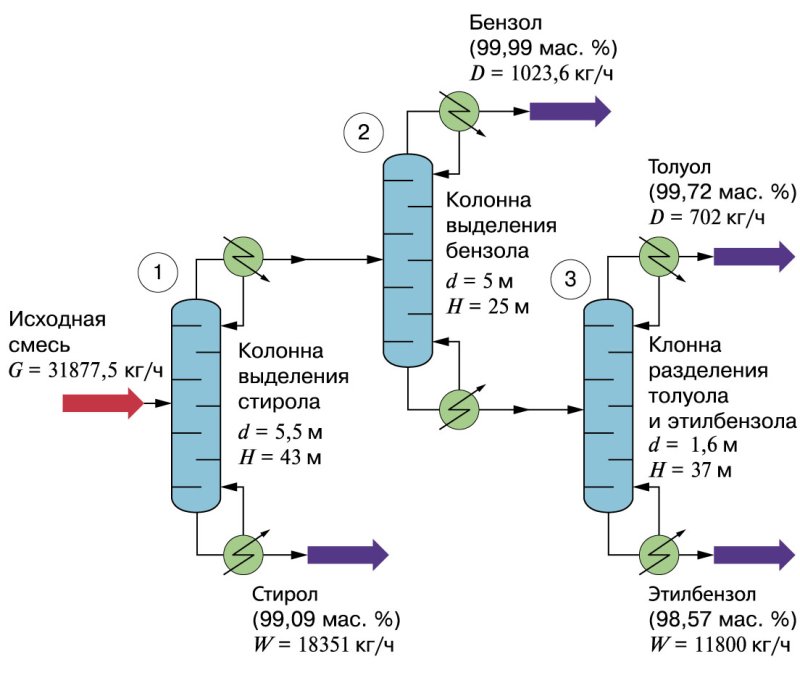
В табл. 2 приведено сравнение суммарных тепловых нагрузок для четырех различных вариантов технологического оформления узла ректификации углеводородного конденсата в промышленной химико-технологической системе получения стирола. Эти данные также были сопоставлены с тепловой нагрузкой технологической схемы ректификации данных продуктов, рассчитанной в работе [16]. Результаты расчетов показывают, что для практической реализации наиболее энергосберегающей является технологическая схема №4.
Таблица 2.
Тепловая нагрузка кипятильников и конденсаторов, а также всех технологических схем ректификации в целом
Таким образом, с применением комплекса программ CHEMCAD проведено компьютерное моделирование четырех различных вариантов технологических схем ректификации углеводородного конденсата в производстве стирола из этилбензола, а также определены их технологические и конструкционные параметры. Выбрана наиболее энергосберегающая технологическая схема ректификации из четырех технологических узлов разделения, синтезированных в настоящей работе, и одного узла ректификации, компьютерная модель которого разработана в работе [16].
Список литературы:
- Семенов П.В. Промышленные технологии получения стирола//Молодой ученый. 2016. №5. С. 168–172.
- Орехов В.С., Дьячкова Т.П., Субочева М.Ю., Колмакова М.А. Технология органических полупродуктов. Тамбов: ТГТУ, 2007. 140 с. Ч. 1.
- Комиссаров Ю.А., Гордеев Л.С., Вент Д.П. Научные основы процессов ректификации/Под ред. Серафимова Л.А. В 2-х томах. М.: Химия, 2004. 270 и 415 с.
- Тимошенко А.В. Энергосберегающие технологии ректификации углеводородов//Мир нефтепродуктов. Вестник нефтяных компаний. 2005. №2. С. 18–23.
- Панкрушина А.В. Компьютерное моделирование сложных колонн с внутренней разделительной стенкой в статических и динамических режимах //Химическая промышленность сегодня. 2018. №4. С. 22–27.
- Тимошенко А.В., Анохина Е.А. Моделирование и оптимизация как инструмент разработки высокоэффективных технологических схем ректификации//Российский технологический журнал. 2017. Т. 5. №3 (17). С. 138–150.
- Тимофеев B.C., Серафимов Л.А., Тимошенко А.В. Принципы технологии основного органического и нефтехимического синтеза. М.: Высшая школа, 2010. 408 с.
- Кулов Н.Н. Гордеев Л.С. Математическое моделирование в химической технологии и биотехнологии//Теоретические основы химической технологии. 2014. Т. 48. №3. С. 243–248.
- Зиятдинов Н.Н. Моделирование и оптимизация химико-технологических систем//Теоретические основы химической технологии. 2017. Т. 51. №6. С. 613–617.
- Гартман Т.Н., Клушин Д.В. Основы компьютерного моделирования химико-технологических процессов. М: Академкнига, 2008. 415 с.
- Гартман Т.Н., Советин Ф.С. Аналитический обзор современных пакетов моделирующих программ для компьютерного моделирования химико-технологических систем//Успехи в химии и химической технологии. 2012. Т. 26. №11 (140). С. 117–120.
- Боровкова Е.А., Советин Ф.С., Рамазанова А.А., Гартман Т.Н. Разработка энергосберегающей подсистемы ректификации в производстве ароматических углеводородов из легких алканов//Химическая промышленность сегодня №8. 2015. С. 39–50.
- Гартман Т.Н., Советин Ф.С., Новикова Д.К., Панкрушина А.В. Разработка технологической схемы ректификации в производстве ароматических углеводородов из продуктов крекинга//Химическая техника. 2017. №8. С. 36–40.
- Советин Ф.С., Шаталов К.И., Гартман Т.Н., Асеев К.М., Шумакова О.П., Клушин Д.В. Разработка компьютерной модели промышленной технологической схемы процесса термоокислительной деструкции гудрона//Химическая промышленность сегодня. ¹8. 2017 С. 41–49.
- Советин Ф.С., Гартман Т.Н., Шакина Э.А., Шумакова О.П., Царёва Е.В. Алгоритм разработки компьютерных моделей сложных химических производств с применением комплексов моделирующих программ//Химическая промышленность сегодня. №2. 2018. С. 49–56.
- Советин Ф.С., Гартман Т.Н., Иванова А.Н., Шакина Э.А., Павлов А.С. Разработка компьютерной модели крупнотоннажной технологической схемы получения стирола//Химическая техника №10. 2018. С. 30–34.
- Гартман Т.Н. Анализ и синтез непрерывной ректификации на основе автоматизированного накопления и классификации информации. Дис. д-ра техн. наук. М., 2000.
- Голованов М.Л. Разработка энергосберегающей технологии ректификации продуктов каталитического крекинга. Дис. канд. техн. М.: МГАТХТ (МИТХТ), 2007.