Стирол является одним из важнейших продуктов нефтехимии, на его основе получают гликоли, полиуретаны, полистиролы и другие сополимеры [1–4]. Непрерывные технологические схемы получения стирола относятся к крупнотоннажным, а также энерго- и ресурсоемким, поэтому даже незначительное сокращение энерго- и ресурсопотребления может обеспечить существенный экономический эффект для производства в целом [2–4].
Большинство действующих крупнотоннажных производств стирола в Российской Федерации используют традиционные технологии получения данного продукта дегидрированием этилбензола на катализаторе, содержащем 55–80 % Fe2O3, 2–28 % Cr2O3, 15–35 % К2СО3 и некоторые оксидные добавки [4]. При этом разделение смесей продуктов реакций проводится ректификацией. Данные процессы являются одними из наиболее энергоемких процессов в химической технологии [5–6].
Проведение модернизации вышеуказанных производств с позиции энерго- и ресурсосбережения не представляется возможным без использования современных комплексов проблемно-ориентированных программ, позволяющих создавать компьютерные модели технологических схем, создавать так называемые «виртуальные» производства. Кроме того, применение современных комплексов программ позволяет без значительных материальных и временных затрат проводить вычислительные эксперименты на моделях химических производств в целом [7–9].
Работа [10] посвящена моделированию и оптимизации производства стирола. В указанной работе авторы составили математическое описание всех аппаратов указанного производства и провели оптимизацию и последующую коррекцию режимов работы технологической схемы получения стирола. В работе [11] автор провел оптимизацию режимов работы реакторного узла производства стирола и разработал систему управления реакторным блоком. Однако необходимо дополнительно рассмотреть вопрос применения комплекса проблемно-ориентированных программ CHEMCAD для разработки компьютерной модели химико-технологической системы получения стирола.
В рассматриваемой работе решена задача применения комплекса программ CHEMCAD для разработки компьютерной модели производства стирола из этилбензола методом каталитического дегидрирования.
Технологическая схема процесса непрерывного дегидрирования этилбензола
Стирол получают методом дегидрирования этилбензола. Описание технологической схемы данного процесса заимствовано из работ [2–4]. Технологическая линия данного процесса, реализованная в среде комплекса программ CHEMCAD, изображена на рис. 1.
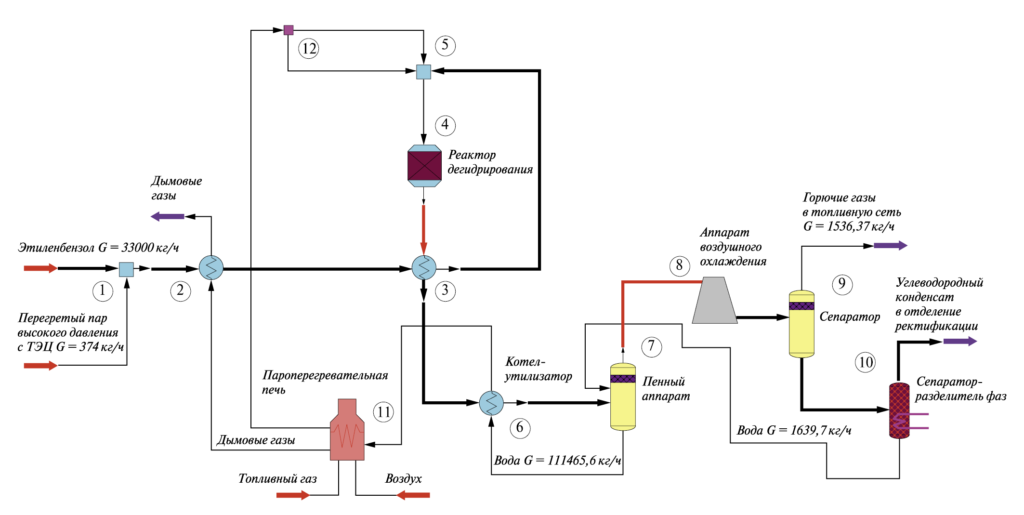
1, 5 – модули смесителей; 2, 3, 6, 8 – модули теплообменников; 4 – модуль равновесного реактора; 7, 9, 10 – модули сепараторов; 11 – модуль огневого подогревателя; 12 – модуль делителя потока
Исходный этилбензол смешивается с водяным паром (водяной пар необходим для увеличения степени конверсии этилбензола) и испаряется в теплообменнике-испарителе (см. рис. 1, модуль 2). При этом данный теплообменник обогревается дымовыми газами, выходящими из пароперегревательной печи (см. рис. 1, модуль 11). Затем пары перегреваются в теплообменнике. Перед входом в реактор пары этилбензола смешиваются с перегретым водяным паром, который генерируется в пароперегревательной печи (см. рис. 1, модуль 11), где сжигается топливо из заводской сети. Температура на входе в реактор составляет 600…640 °С. Процесс проводится на катализаторе на основе оксидов железа. В реакторе дегидрирования протекают следующие реакции:
C6H5C2H5 → C6H5C2H3 + H2; (1)
C6H5C2H5 → C2H4 + С6H6; (2)
C6H5C2H5 + H2 → C6H5CH3 + СH4; (3)
C6H5C2H5 + H2 → C6H6 + C2H6. (4)
Теплота контактных газов рекуперируется в теплообменнике (см. рис. 1, модуль 3) и котле-утилизаторе (модуль 6). Далее контактный газ поступает в пенный аппарат (модуль 7), где дополнительно охлаждается и очищается от катализаторной пыли. Охлаждение углеводородов контактного газа далее проходит в аппарате воздушного охлаждения (модуль 8). В сепараторе (модуль 9) газообразные продукты отделяются и направляются на сжигание. Углеводороды отделяются от воды в разделителе фаз (модуль 10) и направляются на ректификацию.
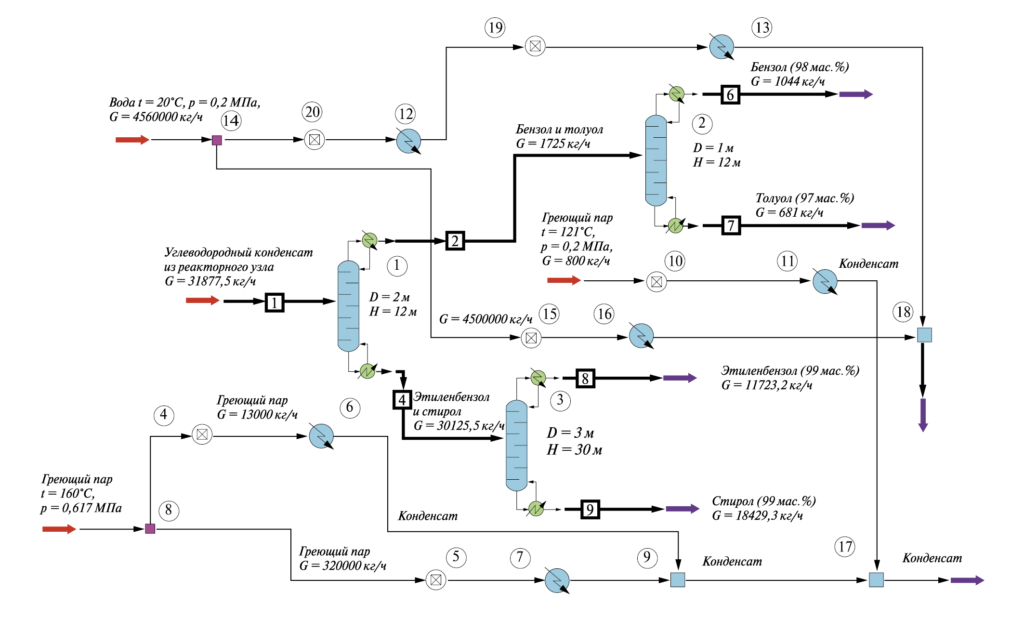
1, 2, 3 – модули ректификационных колонн; 4, 5, 10, 15, 19, 20 – модули статических контроллеров; 6, 7, 11, 12, 13, 16 – модули теплообменников; 8, 14 – модули делителей потоков; 9, 17, 18 – модули смесителей
Технологическая схема ректификации изображена на рис. 2. В колонне ¹1 отделяются бензол и толуол, которые в свою очередь разделяются на практически чистые компоненты в колонне ¹2. Этилбензол отделяется от стирола в колонне ¹3. Также следует отметить что возможны альтернативные варианты технологических схем ректификации [12]. Анализу различных вариантов технологических схем ректификации ароматических углеводородов посвящены работы [13–14].
Ход моделирования основных аппаратов и технологической схемы процесса непрерывного дегидрирования этилбензола
Реактор дегидрирования этилбензола моделируется модулем равновесного реактора (см. рис. 1, модуль 4). Для модуля равновесного реактора (модуль 4) указаны следующие условия: стехиометрические данные реакций (1) – (4), конверсии базовых реагентов, изотермический тепловой режим (температура 627°С). В табл. 1 представлены значения конверсий базовых реагентов, предлагаемые для моделирования процесса дегидрирования этилбензола, определенные по экспериментальным данным, заимствованным из работ [2–4].
Таблица 1.
Значения заданных конверсий для базовых реагентов при моделировании реакторного процесса дегидрирования этилбензола
Базовый реагент | № Реакции | Конверсия, % |
C6H5C2H5 | 1 | 57 |
C6H5C2H5 | 2 | 2 |
C6H5C2H5 | 3 | 2,5 |
C6H5C2H5 | 4 | 2,5 |
Результаты компьютерного моделирования процесса дегидрирования этилбензола
Пенный аппарат (см. рис. 1, модуль 7) моделируется модулем фазового сепаратора. Заданы: температура (100°С) и давление (0,5 МПа).
Результаты компьютерного моделирования пенного аппарата
Сепаратор для отделения газов (см. рис. 1, модуль 9) моделируется модулем фазового сепаратора. Заданы: температура (25°С) и давление (0,1 МПа).
Результаты компьютерного моделирования сепаратора для отделения газов
Сепаратор-разделитель фаз (см. рис. 1, модуль 10) моделируется модулем сепаратора компонентов. Заданы: доля воды, отбираемая с низа, равная 1, температура (25°С) и давление (0,1 МПа). Результаты компьютерного моделирования процесса в данном сепараторе приведены в табл. 2. В этой же таблице проведено сравнение результатов рассчитанного потока углеводородного конденсата с экспериментальными данными, заимствованными из работы [2].
Таблица 2
Сравнение результатов расчетов процесса сепарации углеводородного конденсата с экспериментальными данными
Первая ректификационная колонна – колонна отгонки бензола и толуола (рис. 2, модуль 1) моделируется модулем строгого расчета ректификации TOWR с использованием алгоритма Inside/Out [12]. Число тарелок – 20, номер тарелки питания – 10, массовый расход дистиллята – 1725 кг/ч, паровое число – 10. Поток греющего пара, подаваемого в кипятильник колонны, моделируется модулем теплообменника (см. рис. 2, модуль 6). Процесс теплопередачи моделируется модулем статического контроллера (см. рис. 2, модуль 4), который передает расчетную тепловую нагрузку кипятильника колонны модулю теплообменника с учетом знака. Поток воды, подаваемой для охлаждения конденсатора колонны, моделируется модулем теплообменника (см. рис. 2, модуль 12). Процесс теплопередачи также моделируется модулем статического контроллера (см. рис. 2, модуль 20), который передает расчетную тепловую нагрузку конденсатора колонны модулю теплообменника. Применена процедура комбинирования стандартных модулей комплекса программ CHEMCAD для моделирования процессов ректификации, разработанная в работе [15].
Вторая ректификационная колонна – колонна отгонки бензола (см. рис. 2, модуль 2) моделируется модулем строгого расчета ректификации TOWR с использованием алгоритма Inside/Out. Число тарелок – 20, номер тарелки питания–10, массовый расход кубового остатка – 681 кг/ч, флегмовое число – 3. Поток греющего пара, подаваемого в кипятильник колонны, моделируется модулем теплообменника (см. рис. 2, модуль 11). Процесс теплопередачи моделируется модулем статического контроллера (см. рис. 2, модуль 15), который передает расчетную тепловую нагрузку кипятильника колонны модулю теплообменника с учетом знака. Поток воды, подаваемой для охлаждения конденсатора колонны, моделируется модулем теплообменника (см. рис. 2, модуль 13). Процесс теплопередачи также моделируется модулем статического контроллера (см. рис. 2, модуль 19), который передает расчетную тепловую нагрузку конденсатора колонны модулю теплообменника.
Третья ректификационная колонна – колонна отгонки этилбензола (см. рис. 2, модуль 3) моделируется модулем строгого расчета ректификации TOWR с использованием алгоритма Inside/Out. Число тарелок – 50, номер тарелки питания – 25, массовый расход дистиллята – 11 723,2 кг/ч, паровое число – 100. Поток греющего пара, подаваемого в кипятильник колонны, моделируется модулем теплообменника (см. рис. 2, модуль 7). Процесс теплопередачи моделируется модулем статического контроллера (см. рис. 2, модуль 5), который передает расчетную тепловую нагрузку кипятильника колонны модулю теплообменника с учетом знака. Поток воды, подаваемой для охлаждения конденсатора колонны, моделируется модулем теплообменника (см. рис. 2, модуль 16). Процесс теплопередачи также моделируется модулем статического контроллера (см. рис. 2, модуль 15), который передает расчетную тепловую нагрузку конденсатора колонны модулю теплообменника.
При расчете технологической схемы непрерывного дегидрирования этилбензола для обеспечения сходимости рециклов используется метод простых итераций [16–18]. Также использовано методическое обеспечение для решения задачи компьютерного моделирования энерго- и ресурсоемких химических производств, разработанное в работе [19].
Таким образом, проведено компьютерное моделирование крупнотоннажной технологической схемы процесса дегидрирования этилбензола. Посредством созданной компьютерной модели можно выявить неоптимальные режимы работы как отдельных аппаратов, так и технологической схемы в целом.
Список литературы
- Семенов П.В. Промышленные технологии получения стирола//Молодой ученый. 2016. ¹5. С. 168–172.
- Бесков В.С. Общая химическая технология. М.: Академкнига, 2005. 452 с.
- Орехов В.С., Дьячкова Т.П., Субочева М.Ю., Колмакова М.А. Технология органических полупродуктов. Тамбов: ТГТУ, 2007. 140 с. Ч. 1.
- Тимофеев B.C., Серафимов Л.А., Тимошенко А.В. Принципы технологии основного органического и нефтехимического синтеза. М.: Высшая школа, 2010. 408 с.
- Гартман Т.Н., Клушин Д.В. Основы компьютерного моделирования химико-технологических процессов. М: Академкнига, 2008. 415 с.
- Панкрушина А.В., Гартман Т.Н. Технологический расчет сложных комплексов ректификационных колонн и оценка их эффективности с учетом колебания состава питания//Химическая технология. 2016. ¹8. С. 367–376.
- Гартман Т.Н., Советин Ф.С. Аналитический обзор современных пакетов моделирующих программ для компьютерного моделирования химико-технологических систем//Успехи в химии и химической технологии. 2012. Т. 26. ¹11 (140). С. 117–120.
- Кулов Н.Н. Гордеев Л.С. Математическое моделирование в химической технологии и биотехнологии//Теоретические основы химической технологии. 2014. Т. 48. ¹3. С. 243–248.
- Зиятдинов Н.Н. Моделирование и оптимизация химико-технологических систем//Теоретические основы химической технологии. 2017. Т. 51. ¹6. С. 613–617.
- Островский Г.М, Бережинский Т.А., Беляева А.Р. Алгоритмы оптимизации химико-технологических процессов. М.: Химия, 1978. 294 с.
- Крутилин В.И. Моделирование и управление реакторным блоком производства стирола. Дис. … канд. техн. наук. Л.: ЛТИ имени Ленсовета, 1984.
- Комиссаров Ю.А., Гордеев Л.С., Вент Д.П. Научные основы процессов ректификации/Под ред. Л.А. Серафимова В 2-х т. М.: Химия, 2004..
- Боровкова Е.А., Советин Ф.С., Рамазанова А.А., Гартман Т.Н. Разработка энергосберегающей подсистемы ректификации в производстве ароматических углеводородов из легких алканов//Химическая промышленность сегодня. 2015. ¹8. С. 39–50.
- Гартман Т.Н., Советин Ф.С., Новикова Д.К., Панкрушина А.В. Разработка технологической схемы ректификации в производстве ароматических углеводородов из продуктов крекинга//Химическая техника. 2017. ¹8. С. 36–40.
- Советин Ф.С., Гартман Т.Н. Логико-вычислительные процедуры разработки блочных компьютерных моделей реакторных и ректификационных процессов//Известия ТулГУ. Технические науки. 2011. Вып. 5. Ч. 3. С. 277–282.
- Литовка Ю.В. Получение оптимальных проектных решений и их анализ с использованием математических моделей. Тамбов: ТГТУ, 2006. 98 с.
- Дворецкий С.И., Кормильцин Г.С., Калинин В.Ф. Основы проектирования химических производств. М.: Машиностроение-1, 2005. 280 с.
- Пахомов А.Н., Коновалов В.И., Гатапова Н.Ц., Колиух А.Н. Основы моделирования химико-технологических систем. Тамбов: ТГТУ, 2008. 80 с.
- Советин Ф.С. Разработка и применение методического обеспечения блочного компьютерного моделирования энергоресурсоемких химико-технологических систем c применением инструментальных комплексов программ. Диссертация на соискание ученой степени кандидата технических наук. 05.13.18 и 05.17.08. М. РХТУ им. Д.И. Менделеева. 2011.