Автор: Т.Н. Гартман, Ф.С. Советин, Д.К. Новикова, А.В. Панкрушина (РХТУ им. Д. И. Менделеева)
Опубликовано в журнале Химическая техника №8/2017
С применением комплекса программ CHEMCAD реализован эволюционный алгоритм синтеза энергосберегающих технологических схем ректификации. Разработаны компьютерные модели пяти различных вариантов установок ректификации ароматических углеводородов в производстве аренов из продуктов крекинга. Выбрана наиболее энергосберегающая ректификационная установка из пяти предложенных технологических схем.
Низшие ароматические углеводороды – бензол, толу-ол и кcилолы (БТК) – имеют важное значение для народного хозяйства. Из них получают красители, взрывчатые вещества, биомедицинские препараты и т.д. [1–4]. В последнее время БТК получают из легких алканов и продуктов крекинга методом ароматизации. Известны компании, разработавшие промышленные технологии получения ароматических углеводородов из легких алканов и продуктов крекинга, – Cyclar, Sanyo Petrochemical и «Алканар». Анализ технологий ароматизации приведен в работе [5], однако в данных работах недостаточно рассмотрен вопрос синтеза оптимальных технологических схем разделения БТК с позиции энергосбережения (в технологии компании Cyclar установлена одна ректификационная колонна для отделения легких углеводородов от БТК).
Разработка энергосберегающих технологических схем ректификации (ТСР) многокомпонентных смесей является важнейшей задачей в промышленности органического и нефтехимического синтеза [6]. Ректификация – процесс, получивший наиболее широкое применение для разделения смесей органических продуктов на отдельные фракции, но этот процесс обладает высокой энергоемкостью, и во многих случаях энергозатраты достигают 70% всех энергозатрат на производство в целом [7]. Из-за крупнотоннажности производств основного органического и нефтехимического синтеза, а также некоторых производств тонкого органического синтеза даже незначительное снижение энергопотребления может привести к получению существенного экономического эффекта для производства в целом.
Выбор оптимальной ТСР осложняется поливариантностью организации процесса ректификации [8]. Снижение энергоемкости подсистемы разделения требует применения комплексного подхода и совершенствования как рабочих параметров, так и структуры ТСР. Решению задач разработки алгоритма синтеза оптимальных ТСР посвящены работы [8–9]. Реализации разработанного алгоритма посвящены работы [10–11]. Разработке энергосберегающей подсистемы ректификации смеси ароматических углеводородов в производстве аренов из легких алканов посвящена работа [12].
В данной работе решается задача синтеза оптимальной технологической схемы ректификации многокомпонентной смеси ароматических углеводородов из продуктов крекинга. Состав смеси, подаваемой на ректификацию, мас. %: 0,77 – пропан, 1,62 – бутан, – 27,09 – бензол, 50,43 – толуол, 16,11– ксилолы, 3,98 – нафталин (производительность по сырью G = 10 т/ч). Данный состав исходной смеси был заимствован из работы [13].
Авторами были приняты следующие допущения:
1. Все схемы состоят из четырех последовательно соединенных колонн;
2. Все колонны – простые (без боковых отборов, боковых отпарных секций и потоков циркуляционного орошения);
3. Все колонны – тарельчатые, тип тарелок – ситчатые.
Для реализации указанной задачи был использован комплекс программ CHEMCAD, позволяющий создавать «виртуальные» химико-технологические системы (ХТС) [14].
Задача синтеза ТСР в настоящей работе решается
с использованием эволюционного метода синтеза химико-технологических систем. Эволюционный метод синтеза ХТС заключается в последовательной модификации аппаратурного оформления и структуры технологических связей некоторого исходного варианта ХТС с использованием методов математического моделирования [15].
с использованием эволюционного метода синтеза химико-технологических систем. Эволюционный метод синтеза ХТС заключается в последовательной модификации аппаратурного оформления и структуры технологических связей некоторого исходного варианта ХТС с использованием методов математического моделирования [15].
Были рассмотрены пять различных вариантов технологических схем.
Для реализации компьютерных моделей ТСР использованы модули строгого расчета ректификации с использованием алгоритма одновременного решения системы нелинейных уравнений методом Ньютона–Рафсона [16]. Отличие заключается только в порядке разделения компонентов.
Поскольку при реализации задачи синтеза ТСР необходимо получить чистые компоненты (или практически чистые), при моделировании ТСР задают такие параметры работы ректификационных колонн, при которых данное разделение будет осуществимо. Исходя из состава входного потока, необходимо задавать расходы дистиллятов (или кубовых остатков), а также выбирать типы конденсаторов. С позиции энергосбережения целесообразно выбирать парциальные конденсаторы, однако с позиции экономики ТСР с такими конденсаторами будут более дорогими по сравнению с ТСР с полными конденсаторами [17].
Для реализации эволюционного метода синтеза для различных ТСР варьировались типы конденсаторов (полный или парциальный), а также флегмовые числа R и расходы кубового остатка W (паровые числа S и расходы дистиллята D) (табл. 1).
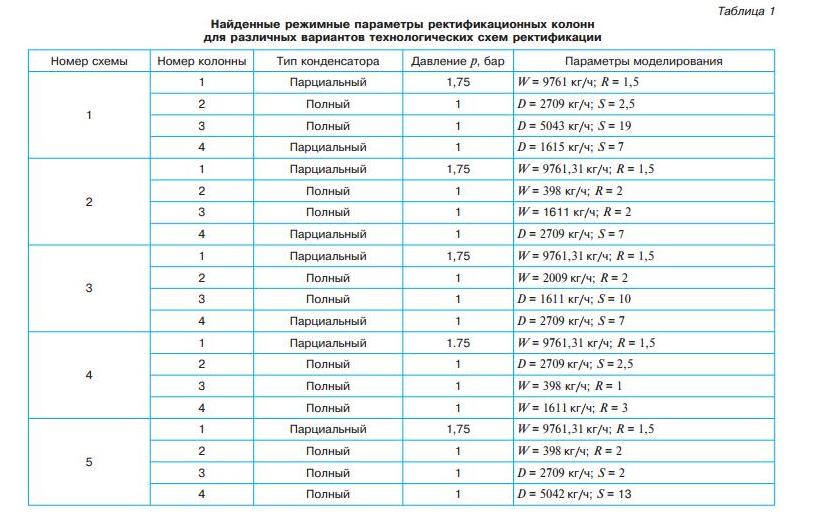
В схеме №1 – две колонны с парциальными конденсаторами и две колонны с полными конденсаторами. Жидкостной поток смеси поступает в колонну №1 (число тарелок – 10), в которой от него отделяются пропан и бутан. Кубовый остаток колонны №1 поступает в колонну №2 (число тарелок – 20), где от смеси отделяется бензол. Затем кубовый остаток колонны №2 поступает в колонну №3 (число тарелок – 20), где происходит отделение толуола. Кубовый остаток колонны №3 поступает в колонну №4 (число тарелок – 30), где разделяется на два потока: дистиллят – пары ксилола и кубовый остаток – жидкий нафталин.
В схеме №2 – две колонны с парциальными конденсаторами и две колонны с полными конденсаторами. Жидкостной поток смеси поступает в колонну №1 (число тарелок – 10), в которой отделяются пропан и бутан. Кубовый остаток колонны №1 поступает в колонну №2 (число тарелок – 10), где смесь разделяется на два потока: нафталин (жидкий поток) и дистиллят – фракция БТК. В колонне №3 (число тарелок – 20) от нее отделяется жидкий ксилол. Смесь бензол–толуол поступает в колонну №4 (число тарелок – 20), в которой происходит разделение смеси на пары бензола и жидкий толуол.
В схеме №3 – две колонны с парциальными конденсаторами и две колонны с полными конденсаторами. Жидкостной поток смеси поступает в колонну №1(число тарелок – 10), в которой от него отделяются пропан и бутан. Кубовый остаток колонны №1 поступает в колонну №2 (число тарелок – 30), где разделяется на смесь ксилол–нафталин и смесь бензол–толуол. Кубовый остаток колонны 2 – смесь ксилол–нафталин – поступает в колонну №3 (число тарелок – 20), где она разделяется на ксилол и нафталин. Смесь бензол–толуол поступает в колонну №4 (число тарелок – 20), где она разделяется на жидкий толуол и пары бензола.
В схеме №4 – все колонны с полными конденсаторами, за исключением колонны №1. Жидкостной поток смеси поступает в колонну №1 (число тарелок – 10), в которой от него отделяются пропан и бутан. Кубовый остаток колонны №1 поступает в колонну №2 (число тарелок – 20), где от смеси отделяется бензол. Кубовый остаток колонны №2 поступает в колонну №3 (число тарелок – 30), в которой отделяется нафталин. Дистиллят колонный №3 – смесь толуол–ксилол поступает в колонну №4 (число тарелок – 20), где разделяется на толуол и ксилол.
В схеме №5 – все колонны с полными конденсаторами, за исключением колонны №1. Жидкостной поток смеси поступает в колонну №1 (число тарелок – 10),
в которой из нее отделяются пропан и бутан. Кубовый остаток колонны №1 поступает в колонну №2 (число тарелок – 10), где разделяется на два потока: нафталин и смесь БТК. Затем дистиллят колонны №2 поступает в колонну №3 (число тарелок – 20), где отделяется бензол, кубовый остаток – смесь толуол–ксилол поступает в колонну №4 (число тарелок – 20). В колонне №4 происходит разделение смеси на толуол и ксилол.
в которой из нее отделяются пропан и бутан. Кубовый остаток колонны №1 поступает в колонну №2 (число тарелок – 10), где разделяется на два потока: нафталин и смесь БТК. Затем дистиллят колонны №2 поступает в колонну №3 (число тарелок – 20), где отделяется бензол, кубовый остаток – смесь толуол–ксилол поступает в колонну №4 (число тарелок – 20). В колонне №4 происходит разделение смеси на толуол и ксилол.
Задачу разделения продуктов основного органического и нефтехимического синтеза осложняет поливариантность системы, поэтому для ее решения выбирается критерий эффективности, в соответствии с которым будет выбрана одна из нескольких технологических схем. В данном случае для выбора наиболее рентабельной схемы процесса используются критерий эффективности «суммарная тепловая нагрузка ректификационных колонн».
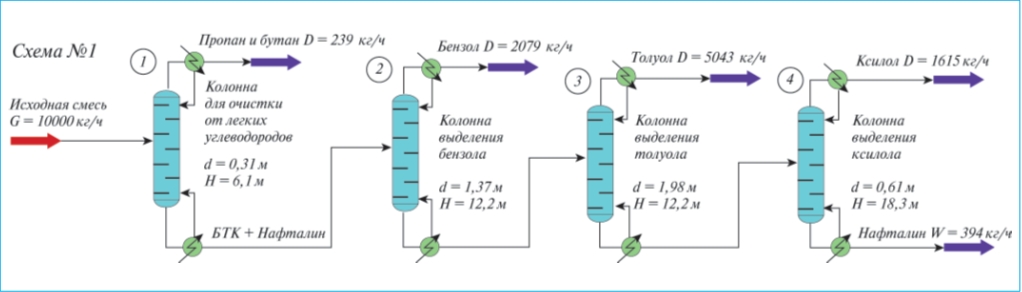
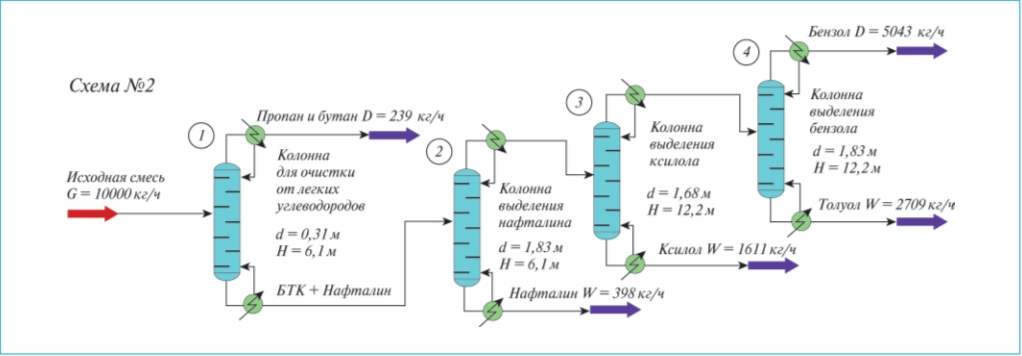
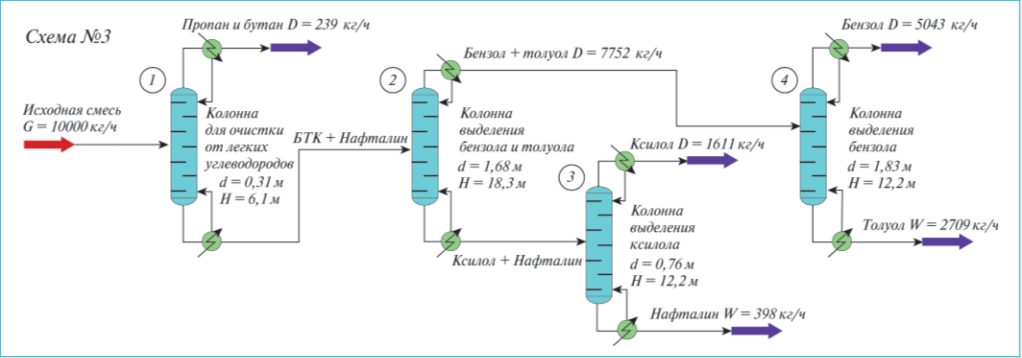
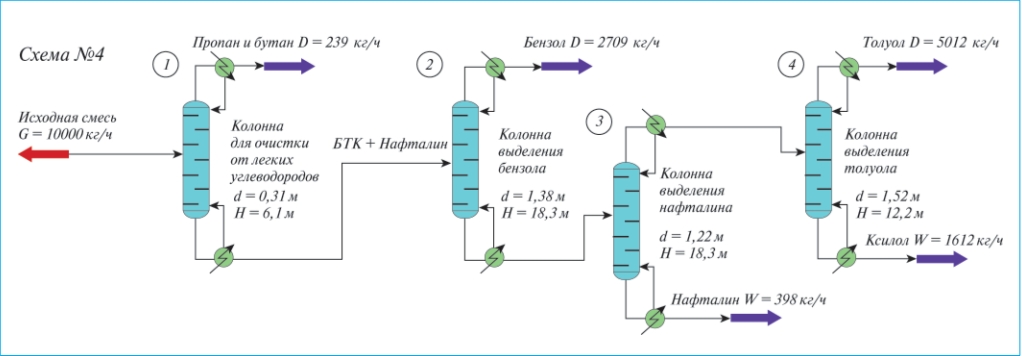
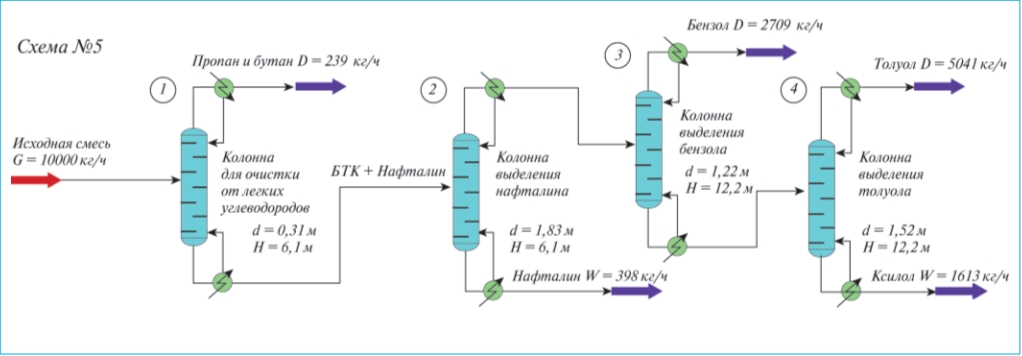
В табл. 2 приведено сравнение суммарных тепловых нагрузок для пяти вариантов технологического оформления процесса непрерывной ректификации смеси ароматических углеводородов в производстве аренов из продуктов крекинга. Расчетные исследования показывают, что для практической реализации оптимальной является схема №4.
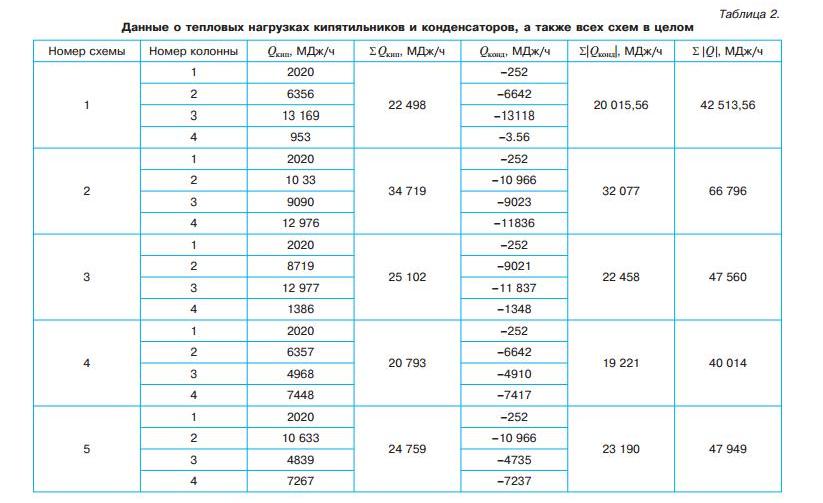
С применением комплекса программ CHEMCAD проведено компьютерное моделирование пяти различных вариантов технологических схем ректификации ароматичес-ких углеводородов с простыми колоннами и определе-
ны их технологические и конструкционные параметры. Выбрана наиболее энергосберегающая технологическая схема ректификации из пяти предложенных систем разделения.
ны их технологические и конструкционные параметры. Выбрана наиболее энергосберегающая технологическая схема ректификации из пяти предложенных систем разделения.
Список литературы:
1. Орехов В.С., Дьячкова Т.П., Субочева М.Ю., Колмакова М.А. Технология органических полупродуктов. Ч. 1. Тамбов: ТГТУ, 2007. 140 с.
2. Гартман Т.Н., Боровкова Е.А., Советин Ф.С. Разработка компьютерной модели промышленной технологической схемы ароматизации легких алканов//Химическая техника. №5. 2016. С. 41–44.
3. Советин Ф.С. Гартман Т.Н. Применение комплекса программ CHEMCAD для разработки компьютерной модели технологического узла нитрования крупнотоннажного производства нитробензола//Химическая техника. №4. 2012. С. 44–45.
4. Медведев А.Ю., Советин Ф.С., Гартман Т.Н., Павлов А.С., Сеннер С.А. Компьютерное моделирование крупнотоннажной технологической схемы процесса алкилирования бензола этиленом//Химическая техника. №7. 2015. С. 44–47.
5. Карташёв И.Ю. Ароматизация легких алканов на промотированных высококремнеземных цеолитах. Диссертация на соискание ученой степени кандидата химических наук. М.: РГУНГ им. И. М. Губкина, 2005.
6. Гартман Т.Н., Клушин Д.В. Основы компьютерного моделирования химико-технологических процессов. М: «Академкнига», 2008. 415 с.
7. Панкрушина А.В., Гартман Т.Н. Технологический расчет сложных комплексов ректификационных колонн и оценка их эффективности с учетом колебания состава питания//Химическая технология №8. 2016. С. 367–376.
8. Викторов В.К., Малютин А.Ю. Метод синтеза химико-технологических систем ректификационных колонн//Изв. Санкт-петербургского государственного технологического института (технического университета). 2012. №14 (40). С. 97–101.
9. Малютин А.Ю. Синтез оптимальных теплоинтегрированных ректификационных систем. Дис. … канд. техн. наук. С.-Пб.: С.-Пб. ГТИ(ТУ), 2012.
10. Тимошенко А.В., Ахапкина О.А., Анохина Е.А., Аристович Ю.В. Энергосберегающие подсистемы ректификации бутанов и пентанов//Химическая технология. 2012. №11. С. 681–687.
11. Тимошенко А.В., Тимофеев В.С., Хахин Л.А., Иванов И.В., Трегер Ю.А., Розанов В.Н. Синтез и оптимизация энергосберегающей подсистемы разделения в процессе получения олефинов из природного газа//Химическая промышленность сегодня. 2013. №1. С. 40–52.
12. Боровкова Е.А., Советин Ф.С., Рамазанова А.А., Гартман Т.Н. Разработка энергосберегающей подсистемы ректификации в производстве ароматических углеводородов из легких алканов//Химическая промышленность сегодня. №8. 2015. С. 39–50.
13. Боровкова Е.А. Моделирование технологических схем процессов с газофазными гетерогенно-каталитическими реакциями в производствах синтез-газа и ароматических углеводородов. Дис. … канд. техн. наук.. М.: РХТУ им. Д. И. Менделеева, 2016.
14. Гартман Т.Н., Советин Ф.С. Аналитический обзор современных пакетов моделирующих программ для компьютерного моделирования химико-технологических систем//Успехи в химии и химической технологии. 2012. Т. 26. №11 (140). С. 117–120.
15. Кафаров В.В., Мешалкин В.П. Анализ и синтез химико-технологических систем. М.: Химия, 1991. 432 с.
16. Голованов М.Л. Разработка энергосберегающей технологии ректификации продуктов каталитического крекинга. Диссертация на соискание ученой степени кандидата технических наук. М.: МГАТХТ (МИТХТ), 2007. 203 с.
17. Гартман Т.Н. Анализ и синтез непрерывной ректификации на основе автоматизированного накопления и классификации информации. Дис. … д-ра технических наук. М., 2000. 514 с.