Автор: Г.С. Яицких (Консорциум «НХПС»), Г.А. Сюняева, В.Г. Яицких (ЗАО «ИПН»).
Опубликовано в журнале Химическая техника №8/2014
Большинство установок первичной переработки нефти (АТ, АВТ) на российских нефтеперерабатывающих заводах построены в период с 1950 по 1980 годы. В процессе эксплуатации на установках периодически производились текущие и капитальные ремонты: замена изношенных трубопроводов, технологического оборудования, а также по необходимости ремонт строительных конструкций. Тем не менее, учитывая «почтенный» возраст установок и несоответствие их требованиям современных и весьма строгих норм промышленной, экологической и пожарной безопасности, руководители заводов вынуждены решать дилемму: проводить реконструкцию действующих установок либо сносить их и строить новые.
Вариант строительства новой технологической установки имеет ряд преимуществ:
- проектная документация выполняется с учетом всех актуальных требований промышленной безопасности, защиты окружающей среды;
- применяется современное надежное технологическое оборудование;
- для управления технологическим процессом используются автоматизированные системы (АСУ ТП);
- современное технологическое, энергетическое оборудование и схемные решения позволяют значительно снизить удельные расходы энергии, воды на переработку 1 т нефти, что, в свою очередь, позволяет снизить себестоимость товарной продукции.
К основным недостаткам этого варианта следует отнести:
- необходимость выделения дополнительной площади под новую установку;
- необходимость привлечения кредитов в больших объемах на длительный срок и под значительные проценты.
Нередко по тем или иным причинам собственник НПЗ не имеет возможности или не видит экономической целесообразности брать кредит на строительство новой установки.
В этом случае реализуется вариант модернизации действующего производства, при этом также зачастую увеличивается производительность технологической установки.
Порядок проведения реконструкции установки с целью продления срока эксплуатации
До принятия решения о техническом перевооружении (реконструкции) необходимо предварительно провести обследование строительных конструкций, технологических аппаратов и трубопроводов с целью определения их остаточного ресурса.
Затем необходимо разработать «Основные технические решения» (ОТР), в которых будут содержаться все необходимые мероприятия по реконструкции данной установки, а также инженерных сетей, связывающих ее с объектами общезаводского хозяйства предприятия.
Как правило, эти мероприятия включают:
- ремонт или замену ректификационных колонн (по необходимости);
- замену части насосов более мощными (в случае значительного увеличения производительности установки);
- замену старых теплообменников или монтаж новых;
- ремонт печей и дооснащение их новыми горелками;
- замену отбракованных участков трубопроводов;
- реконструкцию системы сброса на факел;
- организацию системы аварийного освобождения установки;
- реконструкцию системы пожаротушения;
- внедрение энергосберегающих технологий и оборудования;
- ремонт или реконструкцию системы электроснабжения;
- оснащение установки АСУ ТП;
- необходимый ремонт строительных конструкций.
На основании ОТР определяется прогнозируемая стоимость реконструкции и принимается решение о целесообразности реконструкции установки. Затем разрабатывается проектно-сметная документация, производится соответствующая экспертиза.
После реконструкции установка обретает «второе дыхание» на многие годы.
Возможности увеличения мощности действующих установок АТ, АВТ
Спроектированные в советское время технологические установки имеют, как правило, резервы по следующим показателям:
- мощности печей;
- диаметрам ректификационных колонн;
- диаметрам технологических трубопроводов;
- производительности большей части насосов;
- производительности части теплообменного оборудования;
- несущей способности строительных конструкций.
Эти резервы позволили на некоторых НПЗ России увеличить производительность установок первичной переработки нефти (по сравнению с проектными показателями), что принесло существенную дополнительную прибыль предприятиям.
Для соблюдения требований нормативных документов РФ при увеличении производительности установок необходимо выполнить ряд организационно-технических мероприятий, которые включают:
- разработку и утверждение «Программы опытного пробега установки при заданной повышенной производительности»;
- проведение опытного пробега;
- анализ полученных результатов, определение «узких мест» установки (недостаточная производительность отдельных технологических аппаратов и оборудования, недостаточный диаметр отдельных трубопроводов и т.п.); разработку мероприятий по техническому перевооружению установки с целью повышения производительности;
- разработку проектно-сметной документации (ПСД) для реализации вышеуказанных мероприятий;
- экспертизу ПСД;
- выполнение строительно-монтажных работ по техническому перевооружению установки;
- внесение соответствующих изменений в Технологический регламент установки.
Целесообразно разрабатывать и осуществлять единый комплекс мероприятий, позволяющий дать «вторую жизнь» установке при одновременном увеличении ее мощности.
Типичные «узкие» места установок
В результате опытного пробега технологической установки, как правило, выявляются следующие основные проблемы:
- температура нефтепродуктов (бензин, керосин, дизельное топливо и мазута), выводимых из установки, зачастую превышает регламентные значения;
- снижается температура нефти на входе в отбензинивающую колонну, вследствие чего необходимо увеличивать объем «горячей струи» (см. рисунок, поз. 15), разогревающей низ колонны;
- вследствие увеличения тепловой нагрузки на печь (увеличение объема «горячей струи» и потока отбензиненной нефти) температура ее змеевика и футеровки значительно превышает проектные значения.
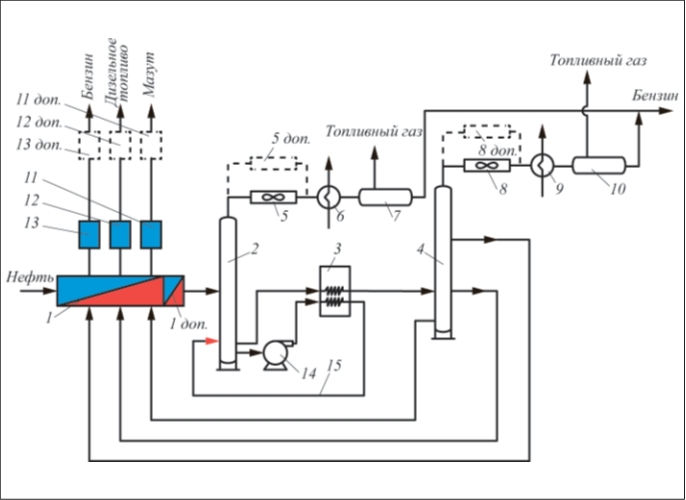
1 – группа теплообменных аппаратов для рекуперации теплоты керосина, дизельного топлива, мазута; 1 доп. – дополнительные теплообменные аппараты для рекуперации теплоты керосина, дизельного топлива, мазута;
2 – отбензинивающая колонна; 3 – печь; 4 – основная ректификационная колонна со стриппингами; 5, 8 – воздушные холодильники-конденсаторы паров бензина
на выходе из колонн; 5 доп., 8 доп. – дополнительные холодильники-конденсаторы бензина; 6, 9 – водяные холодильники бензина; 7, 10 – рефлюксные емкости;
11, 12, 13 – аппараты финишного охлаждения мазута, керосина, дизельного топлива; 11 доп.,12 доп.,13 доп. – дополнительные аппараты финишного охлаждения мазута, керосина, дизельного топлива;
14 – насос «горячей струи»; 15 – трубопровод «горячей струи»
Увеличение температуры нефтепродуктов на выходе из установки обусловлено недостаточностью площади поверхности теплообмена как рекуперативных теплообменников, так и холодильников (воздушных и водяных). Для решения этой проблемы, как правило, устанавливают дополнительные воздушные и/или водяные холодильники 5 доп., 8 доп., 11 доп., 12 доп., 13 доп. (см. рисунок).
При этом существенно увеличивается потребление электрической энергии, оборотной воды.
Увеличение мощности печи 3 обеспечивается сжиганием дополнительных сверхнормативных объемов топлива. Возможность эксплуатировать печь при повышенных (по сравнению с проектными) температурах руководство НПЗ обычно пытается узаконить посредством получения согласования у проектной организации. Необходимо отметить, что этот путь ведет к значительному сокращению срока службы печи.
По этой причине проектировщик печи часто не согласовывает регламент эксплуатации печи при чрезмерных температурных перегрузках ее элементов.
Более экономически и технически целесообразным вариантом является наращивание группы теплообменных аппаратов 1 доп. Как правило, во-первых, это позволяет исключить необходимость установки дополнительных аппаратов финишного охлаждения (5 доп., 8 доп., 11 доп., 12 доп., 13 доп.), при этом экономится электроэнергия, оборотная вода. Во-вторых, в значительной степени снижается тепловая нагрузка на печь. При этом экономятся большие объемы топлива, снижается негативное воздействие на окружающую среду, увеличивается срок службы печи.
При наиболее удачных схемных решениях теплообмена удается исключить «горячую струю» и применение оборотной воды.
Практические результаты
За последние шесть лет были проведены реконструкции семи технологических установок в ОАО «Московский НПЗ», ООО «КИНЕФ», ЗАО «Краснодарский НПЗ», ООО «Афипский НПЗ» и др.
Как показала практика, затраты на реконструкцию технологической установки с увеличением ее мощности на 10–50% обычно составляют не более 15–35% объема затрат на строительство новой установки такой же производительности.
В некоторых случаях заводы проводят реконструкцию в 2–3 этапа с целью использования только собственных финансовых ресурсов. Такая схема финансирования пользуется наибольшей популярностью у собственников НПЗ.