Автор: В.В. Клюев, Н.Р. Кузелев (ЗАО «НИИИН МНПО «СПЕКТР»).
Опубликовано в журнале Химическая техника №5/2015
В настоящее время сложилась парадоксальная ситуация, связанная с использованием на предприятиях различных отраслей промышленности, в том числе и оборонной, средств неразрушающего контроля импортного производства. В связи со сложившейся геополитической ситуацией, связанной в том числе с событиями на Украине и в Крыму, особенную актуальность приобретают вопросы, относящиеся к обеспечению крупных предприятий России высокотехнологичным оборудованием отечественного производства. Недопустимой является ситуация, когда качество выпускаемой продукции непосредственно связано с желанием или нежеланием фирм – резидентов стран, входящих в блок НАТО, обслуживать и поддерживать в рабочем состоянии свое оборудование. Участились случаи отказа фирм из США от выполнения их гарантийных и постгарантийных обязательств.
Оборудование стоимостью в несколько миллионов рублей превращается в металлолом по причине выхода из строя программного или аппаратного обеспечения, так как его восстановление становится невозможным из-за малого объема технической и ремонтной документации, передаваемой на заводы.
Данная ситуация усугубляется тем, что записанные в руководящих документах и допущенные к применению средства неразрушающего контроля, разработанные отечественными предприятиями еще во времена СССР, сняты с производства более 25 лет назад, а их аналоги, производимые в настоящее время, не закупаются и не включаются в технологический процесс по причине отсутствия финансирования.
В развитии машиностроения одной из актуальных задач является применение неразрушающего контроля (НК) и технической диагностики (ТД). Повышение контроля качества и надежности объектов эксплуатации требует оценки ресурса оборудования на всех стадиях его жизненного цикла и по всем входящим в него составляющим [1].
Широкий спектр последних достижений в области приборных, схемных и конструктивных решений и технических средств регистрации используется для повышения надежности тепломеханического оборудования, материаловедения и контроля металла, диагностики и продления срока службы объектов. Безопасность обеспечивают средства НК и ТД; персонал, на основе обучения и аттестации; нормативные документы по метрологии и сертификации (рис. 1).
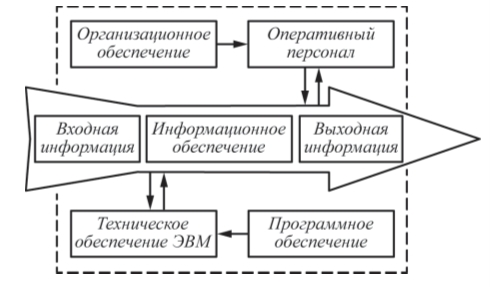
Для техногенной диагностики предназначены дефектоскопы, интроскопы, измерители размеров изделий, физико-механических свойств материалов, приборы для прогностики напряженного состояния, остаточного ресурса техногенных объектов и др.
Сегодня, несмотря на экономические проблемы, ЗАО «НИИИН МНПО «СПЕКТР» создает десятки типов современных конкурентоспособных приборов, проводит исследования, разработку, производство и обслуживание приборов и средств НК и ТД, активно взаимодействует с предприятиями ассоциации «Спектр-Групп», объединяющей 27 предприятий и производящей более 300 типов приборов НК и ТД [2]. Выпускаемые в настоящий момент приборы ни в чем не уступают, а зачастую и превосходят импортные аналоги.
Средства повышения информационности ультразвукового контроля
Ультразвуковые дефектоскопы широко применяются для контроля сварных швов деталей и узлов авиатехники.
Например, применение томографа А1550 IntroVisor существенно упрощает и ускоряет процедуру контроля.
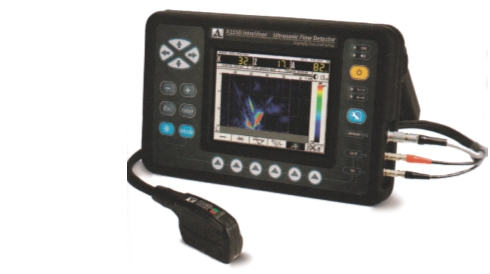
Для контроля используется 16-элементная широкополосная антенная решетка (АР) поперечных волн, обеспечивающая обзор в широком секторе, начиная от середины апертуры АР до эквивалентных углов ввода порядка 75…80° относительно нормали к краю апертуры.
Прибор внесен в Государственный реестр средств измерения [3].
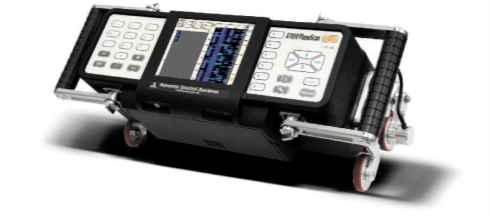
Сканер-топограф А1050 PlaneScan (рис. 3) предназначен для обнаружения дефектов обшивки самолета методом поверхностного прозвучивания с использованием ультразвуковых преобразователей с катящимся сухим точечным контактом (КСТК). 12-элементная линейная АР, состоящая из преобразователей с КСТК, обеспечивает непрерывное сканирования больших поверхностей обшивки самолета без дополнительных подготовленных операций.
Вихретоковый контроль остаточного ресурса металлопроката
Идет совершенствование теории вихретокового и магнитного методов контроля сортового, трубного и листового металлопроката с целью повышения достоверности автоматизированного обнаружения дефектов и их идентификации; создания приборов и средств вихретокового и магнитного методов НК для диагностики технического состояния металлопроката и оценки его остаточного ресурса [4].
Автоматизированная система вихретокового НК для контроля металлопроката в потоке производства.
В настоящее время выпуском трубного металлопроката занимаются не только крупные металлургические заводы, но и большое число малых предприятий, имеющих в своем оснащении небольшие производственные линии. В связи с этим вырос спрос на системы поточных вихретоковых дефектоскопов, удовлетворяющих требованиям действующих международных и национальных стандартов и созданных для модернизации устаревших систем вихретоковой дефектоскопии отечественного или импортного производства. Для решения задач повышения эффективности производства разрабатываются гибкие производственные системы, приспособленные к переналадке под обширный сортамент проката; системы автоматизированного документирования результатов контроля, собирающие статистику для анализа производственных показателей.
Отделом электромагнитной технической диагностики металлоизделий научно-исследовательского института интроскопии МНПО «СПЕКТР» был разработан современный высокопроизводительный автоматизированный дефектоскоп ВД-41П для неразрушающего контроля труб, проката, проволоки, изделий из металлопроката в процессе их производства и при входном контроле (рис. 4). Прибор может применяться для широкой номенклатуры диаметров и марок материалов (ферромагнитные и нержавеющие стали, цветные и тугоплавкие металлы и сплавы). Дефектоскоп предназначен для использования на трубных заводах в линиях непрерывных электросварных агрегатов, в линиях отделки горячекатаных и холоднотянутых труб и проката, в отдельно стоящих транспортных рольгангах; при входном контроле на заводах машиностроительного профиля (автомобильных, авиационных, сельхозмашиностроительных и др.); трубных базах нефтяных и газовых компаний.
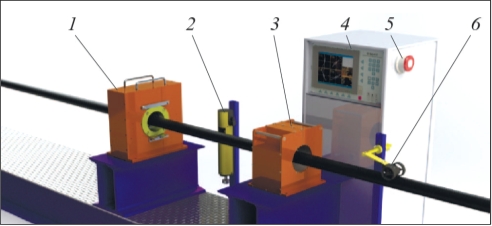
1 – блок преобразователей; 2 – краскоотметчик;
3 – демагнетизатор; 4 – стойка с электронным блоком;
5 – сирена; 6 – датчик пути
Дефектоскоп ВД-41П может быть интегрирован в любую поточную производственную линию. Гибкая наладка модулей измерения и электроники позволяет настроить прибор на контроль металлопроката в широком диапазоне форм и диаметров (от 3 до 120 мм в базовой комплектации). Возможность подключения ряда периферийных устройств, таких, как демагнетизатор, краскоотметчик, датчик пути, светозвуковая сигнализация, позволяет создать ячейку НК, удовлетворяющую требованиям как малого, так и крупного производства. Полное документирование результатов контроля и сбор статистики позволяет снизить издержки на ликвидацию брака и повысить конкурентоспособность продукции металлопроката.
Портативный вихретоковый дефектоскоп для работы в полевых условиях. Изделия металлопроката повсеместно применяются в различных географических поясах и в разное время года, в том числе в зимний период в областях вечной мерзлоты. Для решения задачи диагностики металлоконструкции во время эксплуатации в полевых условиях при отрицательных температурах создан современный портативный вихретоковый дефектоскоп, приспособленный для проведения контроля при переменном зазоре, который может быть представлен наледью или слоистыми массивами из немагнитных веществ на поверхности объекта контроля.
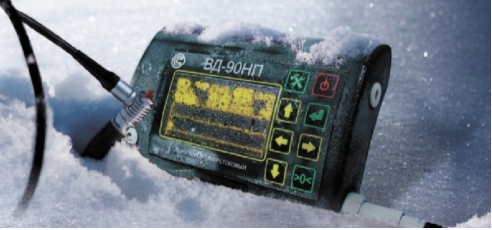
Вихретоковый дефектоскоп ВД-90НП (рис. 5) предназначен для обнаружения поверхностных и подповерхностных трещин в деталях из ферромагнитных и немагнитных материалов. Дефектоскоп разработан для эксплуатации как в полевых условиях, в том числе при значительных отрицательных температурах, так и в цеховых условиях различных отраслей промышленности. Данные контроля могут передаваться в режиме реального времени посредством радиоканала. Кроме классических накладных вихретоковых преобразователей для ВД90НП разработан магнитно-вихретоковый преобразователь для выявления внутренних дефектов типа трещина и коррозия при контроле сварных соединений, труб, баков, деталей из листового проката и других протяженных объектов.
Обоснование остаточного ресурса элементов АЭС
Для обеспечения безопасной работы, долгосрочного прогноза, увеличения срока службы АЭС проводится большой комплекс технических измерений и исследований для обоснования более длительных сроков дополнительной эксплуатации на основе контроля физико-механических свойств на АЭС
Активно разрабатываются и внедряются различные приборы и системы для диагностики оборудования и трубопроводов реакторных установок. Кроме того, разрабатываются и методики проведения неразрушающего контроля целостности металла, оценки результатов контроля и выработки рекомендаций по устранению выявленных дефектов [5]. Внедряются методики, приборы и системы на действующих объектах, производится обучение персонала реакторных установок, непосредственно участвующих в проведении контроля целостности металла.
В связи с обнаружением массовых дефектов металла в настоящее время проводится ревизия существующих штатных методик УЗК, разрабатываются новые методики контроля трубопроводов Ду300 из аустенитной стали с использованием автоматизированных систем УЗК.
Комплексный мониторинг оборудования на основе систем КОМПАКС

Система КОМПАКС® (рис. 6) контролирует состояние оборудования различных типов на единой программноаппаратной платформе. Система имеет открытую архитектуру, возможность наращивания до 8192 измерительных каналов в соответствии с требованиями заказчика и интеграции с системами АСУ ТП посредством ПО COMPACS®-OPC Server [6]. КОМПАКС® – система Компьютерного Мониторинга,
Предупреждения Аварий и Контроля Состояния – это программно-аппаратный комплекс для мониторинга и диагностики технического состояния в реальном времени, который использует любые методы (виды) неразрушающего контроля и технической диагностики.
Таким образом, повышение контроля качества и надежности объектов эксплуатации объектов требует оценки ресурса оборудования на всех стадиях его жизненного цикла. Подавляющее большинство современного оборудования для НК и ТД построено на базе цифровых технологий, что позволяет не только тиражировать результаты контроля, но и анализировать их.
Ясно, что недопустима зависимость от поставок оборудования зарубежного производства, как при обеспечении безопасной эксплуатации опасных промышленных объектов, так и в отраслях, обеспечивающих обороноспособность страны. Стимулирование инновационного развития производителей средств НК и ТД для обеспечения крупнейших нефтегазовых проектов сегодня обостряется и требует конкретной координации.
Список литературы
- Неразрушающий контроль/Под общ. ред. В.В. Клюева и др. М.: ИД «СПЕКТР», 2012.
- Неразрушающий контроль. Справочник: в 8 томах/Под общ. ред. В.В. Клюева. М.: Машиностроение, 2008.
- Бакунов А.С., Ефимов А.Г., Кудрявцев Д.А. Использование средств неразрушающего контроля при строительстве и ремонте магистральных трубопроводов//Территория NDT. 2012. №3.
- Бакунов А.С., Ефимов А.Г., Шубочкин А.Е. Применение современных средств вихретоковой дефектоскопии для контроля различных промышленных объектов//Контроль. Диагностика. 2011. №4.
- Клюев В.В., Кузелев Н.Р., Артемьев Б.В, Ефимов А.Г. Интеллектуальные системы неразрушающего контроля и технической диагностики – основа безопасной эксплуатации АЭС//Контроль.Диагностика. 2013. №1.
- Костюков Б.Н., Бойченко С.Н., Костюков А.В. Автоматизированные системы управления безопасной ресурсосберегающей эксплуатацией нефтеперерабатывающих и нефтехимических производств (АСУ БЭР КОМПАКС®). М.: Машиностроение, 1999.