Автор: В.А. Земляничкин, В.И. Баженов, П.С. Горбунов, Д.И. Ометов (АО «ИркутскНИИхиммаш»).
Опубликовано в журнале Химическая техника №9/2015
Рассмотрена проблема оценки технического состояния стволов промышленных дымовых труб. Применение одного из современных методов неразрушающего контроля – тепловизионной диагностики – позволяет обнаружить дефекты на самой ранней стадии их появления без вывода трубы из эксплуатации. Своевременный ремонт дымовых труб существенно повышает их надежность и безопасность работы.
Экспертиза промышленной безопасности дымовых труб показывает, что большинство из них эксплуатируются по 50–60 лет, давно отработав нормативный срок. Износ дымовых труб является результатом их эксплуатации в непроектном режиме, вызванном снижением производственных мощностей или переходом на другой вид топлива с уменьшением объема и температуры дымовых газов. В ряде случаев износ дымовых труб обусловлен низким качеством строительства. В условиях нестабильной экономической ситуации в России в промышленном секторе ждать глобальной замены оборудования, отработавшего ресурс, не приходится.
Экспертам, проводящим экспертизу промышленной безопасности, становится все сложнее принимать решения при назначении очередного срока безопасной эксплуатации опасного производственного объекта. Понимание ответственности потребовало принятия ряда мер, способствующих более объективной оценке технического состояния объектов: увеличения объема контроля строительных конструкций, освоения новых методов и приборов, которые позволяют получить более достоверную картину технического состояния.
Многолетний опыт работы, собранная и систематизированная за это время информация по эксплуатации и ремонту дымовых труб подтверждают, что основными признаками возникновения дефектов и повреждений является низкое качество строительства и неправильная эксплуатация труб.
Отклонение режима работы трубы от проектных параметров приводит к образованию дефектов, которые зачастую нельзя обнаружить визуально, а скрытые процессы развития таких дефектов могут привести к аварийному состоянию трубы.
Снижение температуры дымовых газов ниже температуры точки росы, происходящее, как правило, из-за подсоса холодного воздуха через неплотности в подводящих газоходах в местах примыкания к стволу трубы или между узлами соединения и швами конструкций газоходов, а также в местах разрушения или отсутствия теплоизоляции и футеровки, приводит к выпадению конденсата. Взаимодействие влаги с агрессивными составляющими дымовых газов вызывает коррозию в бетоне и кирпиче, в результате чего ствол трубы получает повреждения, что ухудшает его техническое состояние и несущую способность.
При отсутствии со стороны эксплуатирующей организации должного контроля над состоянием конструкции дымовой трубы развитие внутренних дефектов со временем может достичь угрожающих масштабов, при этом дефекты могут оставаться не обнаруженными [1–3].
В настоящее время на помощь экспертам пришла инфракрасная техника. Применение одного из современных методов неразрушающего контроля, в данном случае тепловизионного контроля, при правильном подходе позволяет выявить скрытые дефекты в газоотводящем тракте и стволе дымовой трубы во время ее эксплуатации [4, 5].
В АО «ИркутскНИИхиммаш» тепловизионная техника и специализированное программное обеспечение известного мирового производителя – компании Flir – используются для диагностики зданий и дымовых труб с 2005 г.
Снимок ствола дымовой трубы, сделанный при помощи тепловизора, несет информацию о всем температурном поле ее поверхности. Требуется правильно расшифровать тепловое изображение, так как каждая область температурного поля отмечена соответствующим цветом, что свидетельствует о наличии ряда различных дефектов и повреждений.
Определяя тип дефекта на термограмме, следует обратить внимание, не вызвана ли аномалия различием в коэффициентах излучения участков поверхности, в коэффициентах теплообмена или в других возможных факторах, оказывающих влияние на температуру поверхности обследуемого объекта. Необходимо также исключить попавшие в поле зрения тепловизора температурные поля посторонних предметов, чтобы не допустить ложного толкования результатов съемки.
С помощью тепловизионного контроля могут быть выявлены следующие дефекты: поверхностное разрушение бетона с оголением (или без оголения) арматуры, трещины на поверхности стенки, пониженное сопротивление газопроницанию футеровки, разрушение футеровки, отсутствие теплоизоляции в прослойке между стволом и футеровкой, разрушение швов бетонирования, скопление золовых отложений. Примеры таких дефектов изображены на рис. 1, 2.
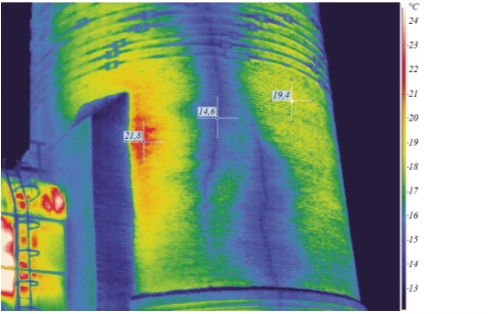
При обследовании дымовой трубы тепловизионный метод чаще всего является предшествующим этапом диагностики, по результатам которого определяют области конструкции для детального инструментального контроля.
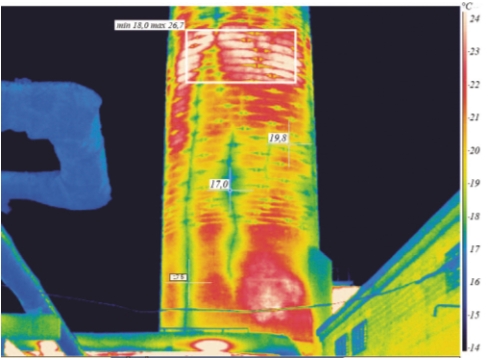
Для служб эксплуатации постоянный тепловизионный мониторинг позволяет выявить дефекты на самой ранней стадии их появления, что существенно повышает надежность и безопасность работы дымовых труб, предотвращает внеплановые потери и простои на производстве.
Список литературы
- Федеральный закон от 21.07.1997 №116-ФЗ (ред. от 02.07.2013). О промышленной безопасности опасных производственных объектов. 1997.
- Федеральный закон от 30 декабря 2009 г. №384-ФЗ (с изменениями от 2 июля 2013 г.) «Технический регламент о безопасности зданий и сооружений».
- ГОСТ 31937–2011. Здания и сооружения. Правила обследования и мониторинга технического состояния.
- ГОСТ Р 54852–2011. Здания и сооружения. Метод тепловизионного контроля качества теплоизоляции ограждающих конструкций.
- Вавилов В.П. Инфракрасная термография и тепловой контроль. М.: Изд. дом «СПЕКТР», 2009.