Автор: К.А. Олесевич, М.М. Гордиенко (ООО «МАН Дизель и Турбо Рус»).
Опубликовано в журнале Химическая техника №2/2015
Азотная кислота является одним из важнейших продуктов химической промышленности. Она широко применяется для получения минеральных удобрений, синтетических красителей, взрывчатых веществ, нитролаков, пластмасс, лекарственных синтетических веществ и других продуктов. Россия занимает первое место в мире по имеющимся мощностям и по объемам производства азотной кислоты. Также крупнейшими производителями азотной кислоты являются Северная Америка, Западная
Европа и Центральная Европа – вместе с Россией на их долю приходится около 80% мировых мощностей.
Основным оборудованием установки по производству азотной кислоты является турбокомпрессорный агрегат, в состав которого входят воздушный компрессор, компрессор нитрозного газа, детандер хвостового газа и паровая турбина.
Технологические процессы в производстве азотной кислоты
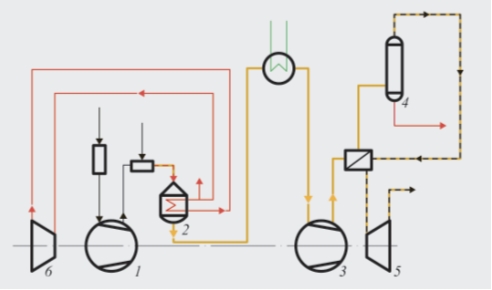
1 – воздушный компрессор; 2 – блок окисления аммиака;
3 – компрессор нитрозных газов; 4 – абсорбционная колонна; 5 – детандер хвостового газа; 6 – паровая турбина
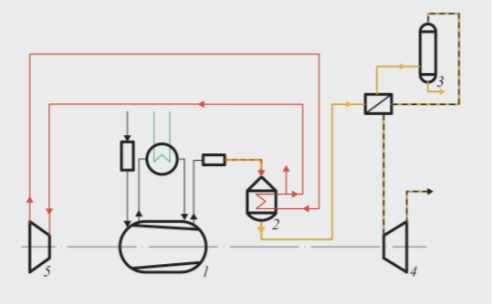
В производстве азотной кислоты различаются четыре базовых технологических процесса, характеризующиеся различными уровнями давления (рис. 1, 2): процесс с двумя давлениями (низкое/среднее), при котором окисление происходит при атмосферном давлении, а абсорбция – при давлении 0,4…0,6 МПа;
- процесс со средним давлением, при котором окисление и абсорбция происходят при давлении 0,4…0,6 МПа;
- процесс с двумя давлениями (среднее/высокое), при котором окисление происходит при давлении 0,4…0,6 МПа, а абсорбция при давлении 1,0..1,2 МПа;
- процесс с высоким давлением, при которым окисление и абсорбция происходят при давлении 0,8…1,3 МПа.
За последние 20 лет процесс с двумя давлениями получил признание в Европе и используется на крупных предприятиях с объемами производства азотной кислоты от 500 т в сутки. Предприятия с меньшей производительностью, в основном расположенные за пределами Европы, используют процесс с единым давлением (высоким или средним).
Основные компоненты турбокомпрессорного агрегата для производства азотной кислоты
Осевой воздушный компрессор
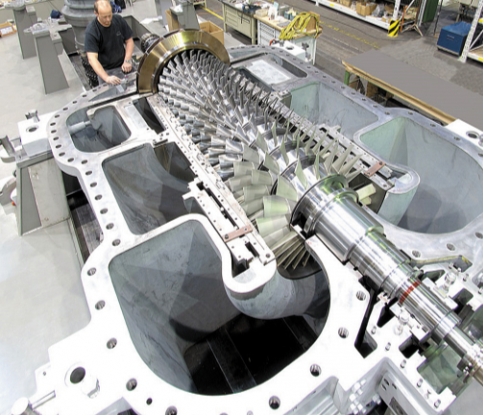
Осевой компрессор (рис. 3) без охлаждения, как правило, используется в процессах с двумя давлениями и со средним давлением. Для этой области применения компания «МАН Дизель и Турбо» разработала модель «AG» с 10…15 ступенями осевого типа и последней ступенью центробежного типа. Осевые компрессоры создаются из стандартизированных групп ступеней с различной степенью реактивности: от 70 до 80% в первых ступенях и до 100% в последних. Центробежная ступень замещает от двух до трех осевых ступеней и выпускной диффузор, а также обеспечивает повышение производительности и расширенный рабочий диапазон компрессора.
Особенности осевых компрессоров:
- Высокая производительность. При сниженной степени реактивности в первых ступенях скорость потока остается низкой при высоком расходе. Установка 100% реактивных лопаток на последних ступенях обеспечивает оптимальные формы межлопаточных каналов и относительно малые зазоры из-за увеличенной длины лопаток.
- Широкий диапазон эксплуатационных характеристик. Осевые компрессоры с системой регулирования частоты вращения (например, с приводом от паровой турбины) позволяют снижать производительность до 65% и ниже при приближении к точке помпажа. Для регулирования производительности компрессора при работе на постоянных оборотах достаточно оснастить треть общего числа ступеней регулируемым направляющим аппаратом, остальные 2/3 ступеней остаются нерегулируемыми.
- Низкая степень подверженности загрязнению и эрозии. Осевые компрессоры имеют высокую стойкость против воздействия загрязненных газов. Отложения в таких компрессорах возникают на неподвижных лопатках статора и снижаются от ступени к ступени в направлении потока. Поскольку в осевых компрессорах повышение давления в основном обеспечивается рабочими лопатками ротора, которые не подвержены загрязнению, использование загрязненных газов не влияет на характеристики работы компрессора даже после длительной эксплуатации. Твердые частицы, присутствующие в газе, не вызывают опасности эрозии осевого компрессора, так как конструкция лопаток обеспечивает незначительную степень закрутки потока, при которой твердые частицы проходят по линии тока газа без разгона до скоростей, приводящих к эрозии. В установках по производству азотной кислоты лабиринтные уплотнения наддуваются воздухом через промежуточную камеру, находящуюся между уплотнением и подшипником, что позволяет избежать попадания нитрозных газов в маслосистему.
Центробежный воздушный компрессор
Для небольших установок, где применяется технологический процесс с единым давлением, как средним (около 0,6 МПа), так и с высоким (0,7…1,5 МПа), наиболее экономически обоснованным решением на сегодняшний день являются многовальные компрессоры со встроенным редуктором (рис. 4). По сравнению с одновальными компрессорами многовальные компрессоры обладают рядом преимуществ, таких, как прямой привод и интегрированный детандер хвостового газа. Компания «МАН Дизель и Турбо» производит компрессоры модели «RG» с числом ступеней до 6.
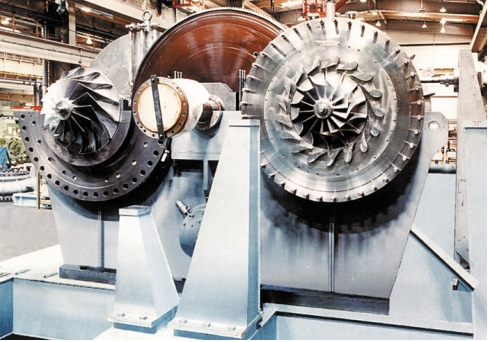
Необходимая температура газа на выходе из компрессора обеспечивается путем изменения числа промежуточных охладителей. Для установок со средним давлением возможно исполнение без промежуточного охлаждения.
Преимущество компрессоров со встроенным редуктором состоит в том, что в качестве его привода возможно использование электродвигателя или турбины как отдельно, так и совместно.
В агрегатах с электродвигателем главное колесо приводится в действие напрямую. Если в качестве привода компрессора используется турбина, то в компрессоре устанавливается дополнительный шестеренный вал, передаточное число которого выбирается таким образом, чтобы компрессор приводился в действие от детандера хвостового газа или от паровой турбины на оптимальной частоте вращения.
Особенности компрессоров со встроенным редуктором:
- высокая производительность за счет оригинальной конструкции рабочего колеса, оптимальной частоты вращения и промежуточного охлаждения;
- низкая стоимость эксплуатации благодаря высокой производительности и минимальному техническому обслуживанию;
- высокая производительность при неполной нагрузке;
- высокая степень эксплуатационной готовности;
- простота эксплуатации благодаря полностью автоматизированному управлению и наличию системы мониторинга;
- прочная и компактная конструкция.
Компрессор нитрозного газа
Для компримирования нитрозного газа в процессах с двумя давлениями, как правило, применяется центробежный компрессор (рис. 5). В установках, где окисление происходит при очень низком давлении, возможно использование осевого компрессора. В компрессорах нитрозного газа используются рабочие колеса, обеспечивающие высокий расход; при необходимости возможна установка рабочих колес с большими рабочими углами.
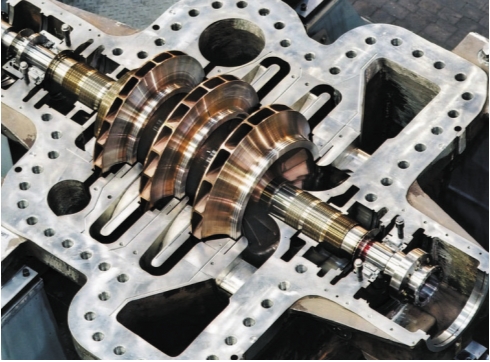
Необходимо учитывать, что данные компрессоры работают в сложных условиях: нитрозный газ образует нитрит аммония, нитрат аммония и азотную кислоту, является ядовитым веществом; вызывает сильную коррозию и вступает в химические реакции в процессе сжатия.
Образование отложений нитрата аммония, которые в некоторых случаях могут быть взрывоопасны, предотвращается благодаря отсутствию мертвых зон в компрессоре, а отложения в проточной части компрессора, удаляются в ходе его периодической промывки. Промывка производится путем впрыска парового конденсата через форсунку во время пуска агрегата. Кроме того, имеется возможность впрыска конденсата при работе компрессора в нормальном режиме в течение 5 минут каждые 8 ч. Форсунки для впрыска в поток газа воды под высоким давлением имеют специальную конструкцию, обеспечивающую равномерное и точное распределение воды с последующим быстрым испарением. Описанная процедура является оптимальной: она обеспечивает мягкую очистку проточной части компрессора и не влияет на расход технологической среды, поскольку впрыскиваемый объем воды очень мал.
Из-за токсичности нитрозного газа необходимо предотвратить его утечку из компрессора. Для этого используются следующие средства:
- камеры двойного уплотнения на главном валу агрегата. Во внутренние камеры подается уплотняющий воздух (от воздушного компрессора), а наружные камеры имеют выход в атмосферу. В случае утечки газ отводится за пределы помещения, в котором установлен компрессор. Для предотвращения попадания нитрозного газа в маслосистему в каждом корпусе подшипника предусмотрена дополнительная уплотняющая камера;
- нанесение специального герметизирующего вещества на соединительные поверхности фланцев корпуса. При этом затяжка болтовых соединений корпуса производится гидравлическим инструментом, обеспечивающим точное соблюдение значений крутящего момента.
Для предотвращения коррозии все детали, вступающие в контакт с газом, изготавливаются из хромоникелевой стали. Кроме того, при проектировании компрессора следует принимать во внимание химические реакции, которые возникают в процессе сжатия нитрозного газа: диссоциации N2O4 до NO2, при которой происходит значительное поглощение тепла, а также окисления NO до NO2, при которой тепло выделяется. При проектировании компрессора учитывается количество выделяемого и поглощаемого тепла для каждой ступени, что необходимо для расчета геометрии проточной части.
Детандер хвостового газа
Утилизация энергии, содержащейся в остаточном газе после абсорбции, обеспечивает рекуперацию 30–100% приводной мощности компрессора.
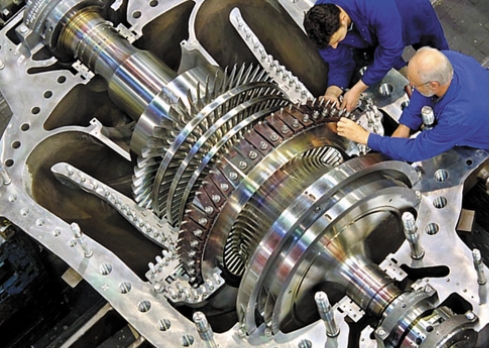
В детандерах хвостового газа (рис. 6) могут использоваться как импульсные, так и реактивные турбины с одной или несколькими ступенями. Регулируемый входной направляющий аппарат имеет ряд преимуществ: плавное регулирование во всем рабочем диапазоне и повышение производительности благодаря использованию только реактивных лопаток.
Для предотвращения коррозии все детали, вступающие в контакт с газом, изготавливаются из хромоникелевой стали. Внешние лабиринтные уплотнения оснащены двумя промежуточными камерами, которые уплотняются воздухом, применяемым также для продувки компрессора нитрозного газа.
Рабочие лопатки детандера по возможности оснащаются бандажными полками для лучшего уплотнения между лопатками и статорами. Такая конструкция также способствует гашению вибраций лопаток и повышению производительности агрегата. Сопловые лопатки детандера устанавливаются в обойме и крепятся в корпусе турбины посредством соединения, компенсирующего термические расширения. Лопатки в регулируемом сопловом аппарате устанавливается в нужное положение с помощью электродвигателя или гидравлического привода.
Паровая турбина
На паровую турбину (рис. 7), как правило, подается пар, производимый в технологическом процессе. В некоторых случаях этот технологический пар используется для других целей, а паровую турбину заменяют электродвигателем.
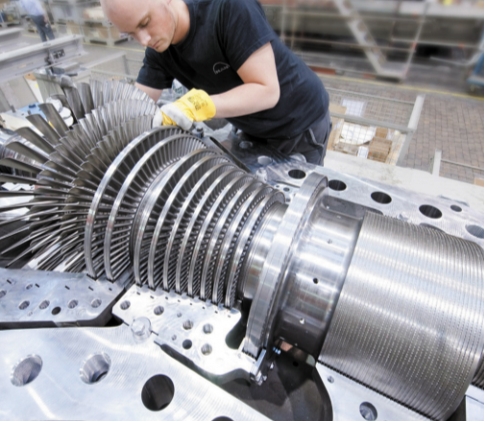
В установках по производству азотной кислоты паровая турбина должна не только обеспечивать достаточную приводную мощность, но и пусковую мощность турбоагрегата HNO3, поскольку при запуске установки детандер хвостового газа не является источником энергии. Пусковая мощность может в 2 раза превышать мощность, которая требуется для работы агрегата в нормальном режиме.
Кроме того, в процессе проектирования паровых турбин необходимо предусмотреть в конструкции отвод определенного количества пара для технологических нужд или для привода вспомогательного генератора.
В агрегатах для производства азотной кислоты применяются конденсационные паровые турбины реактивного типа с функцией отбора/впуска пара, а также без нее.
Для важных узлов паровых турбин «МАН Дизель и Турбо», таких как корпусы подшипников, регулирующие клапаны, сопловые блоки, корпусы регулирующих ступеней, выхлопные камеры, а также для соединительных элементов применяется принцип модульной компоновки в соответствии с определенными типоразмерами.
Комбинирование различных модулей обеспечивает гибкую адаптацию агрегата к разным условиям эксплуатации путем выбора оптимального конструктивного решения.
Во избежание вибрационного резонанса лопаток в активной части турбины во всем диапазоне частот вращения используется толстый каплевидный профиль с бандажом.
Преимуществом данного профиля являются повышенная прочность и возможность его применения в широком диапазоне угла установки и шага лопаток.
Рабочие лопатки переменного сечения с закруткой по высоте и соответствующие им лопатки статора с переменным сечением выбираются из стандартных типоразмеров. Роторы изготавливаются из цельной заготовки, а затем проходят балансировку в облопаченном состоянии в вакууме на рабочей частоте вращения.
Система управления и защиты
К турбокомпрессорным агрегатам для производства азотной кислоты предъявляются жесткие требования в отношении систем управления и защиты. При проектировании таких систем должны учитываться все требования технологического процесса, а также должна быть реализована поддержка всех функций от пуска до аварийного останова агрегата или процесса.
Антипомпажная защита. Граница помпажа – это линия, разделяющая стабильную и нестабильную работу компрессора. Снижение объемного расхода ниже границы помпажа сопровождается отрывом потока от лопаток, что приводит к периодическому изменению направления потока газа в проточной части компрессора. Это явление называется помпажом компрессора. Необходимо избегать чрезмерных нагрузок и колебаний температуры компонентов, вступающих в контакт с нитрозным газом.
В задачу антипомпажной системы входит управление запорно-регулирующей арматурой для поддержания расхода в стабильной зоне рабочих характеристик.
Регулирование частоты вращения. Система управления и защиты также отвечает за регулирование частоты вращения и, следовательно, параметры давления и расхода в агрегате. Применяемая система управления превосходит требования спецификации Национальной ассоциации заводов по производству электротехнической продукции (NEMA) SM 23, класс D. В зависимости от конкретных требований она используется для следующих функций:
- резервного контроля частоты вращения турбины;
- резервной защиты от превышения частоты вращения;
- полной функциональной проверки всех контуров аварийной защиты во время работы в нормальном режиме;
- пуска турбины из полностью остановленного состояния с регулированием частоты вращения;
- комбинированного контроля частоты вращения и давления отбора;
- контроля противодавления;
- контроля давления на входе;
- контроля мощности;
- контроля частоты.
Прочие компоненты турбокомпрессорного агрегата
Опорная рама/стальное основание. Если позволяют условия на площадке, то турбокомпрессорный агрегат целиком устанавливается на единой опорной раме или на стальном основании. Такая компоновка обеспечивает ряд серьезных преимуществ:
- все монтажные и сборочные работы, включая устройство трубопроводов и кабельных соединений, могут выполняться на заводе-изготовителе;
- простота обращения с оборудованием при испытаниях и транспортировке;
- сокращение сроков монтажа;
- упрощение работ на участке.
Маслосистема. Маслосистема для подачи масла в подшипники и гидравлические устройства управления может быть выполнена на основании стандартов «МАН Дизель и Турбо» или на основании стандарта 614 Американского нефтяного института (API), а также учитывать технические условия конкретного проекта.
Редуктор, муфты. Редуктор, используемый в турбокомпрессорном агрегате, обеспечивает выбор оптимальной частоты вращения для каждой единицы оборудования. Как правило, используется одноступенчатый редуктор с прямозубой передачей. Компоненты агрегата соединяются посредством зубчатых или диафрагменных муфт. Все компоненты агрегата оснащены опорными подшипниками, что обеспечивает их гибкое разделение и предоставляет следующие преимущества:
- минимальное воздействие от соседних роторов в широком диапазоне условий эксплуатации;
- гибкость выбора компоновки агрегатов в технологической линии;
- возможность работы при значительном угловом смещении, например, при длительной эксплуатации.
Испытания турбокомпрессорных агрегатов
Производственные мощности компании «МАН Дизель и Турбо» оснащены различными испытательными стендами для проведения заводских приемочных испытаний турбокомпрессорных агрегатов. Агрегаты с производственной площадки поступают на испытательный участок как в сборе, так и в виде отдельных узлов. Здесь они устанавливаются на стальное основание длиной 44 м и подключаются к постоянным трубопроводам для подачи пара, воздуха, воды, масла. В соответствии со стандартами DIN/VDI/ASME/API проводятся все необходимые испытания:
- механические испытания отдельных единиц оборудования;
- механические испытания турбокомпрессорного агрегата в сборе;
- термодинамические испытания с использованием воздуха или газов в системах с открытым или замкнутым контуром.
В качестве привода для испытаний могут использоваться паровые турбины или электродвигатели различной мощности. Возможно также одновременное проведение испытаний трех комплектных агрегатов.