Авторы: В.И. Федоров (ООО «Ладахим»),Ю.А. Желиба, Н.И. Гоголь, В.А. Чичелов (Институт холода, криотехнологий и экоэнергетики ОНАПТ; ООО НИО «Холод»).
Опубликовано в журнале Химическая техника №5/2014
В современных требованиях к технологическим установкам промышленных производств приоритеты отдаются энергоресурсосбережению, уменьшению потерь, повышению надежности обеспечения паспортной производительности и качества готовой продукции, компактности технологического оборудования. Однако на практике зачастую все выглядит иначе. Промышленные технологические установки эксплуатируются в течение длительного времени без каких-либо инноваций и реконструкций, расходуя большое количество исходного сырья и энергоресурсов.
Попытки модернизировать процессы в действующих установках предпринимаются, однако в общей массе технологические установки, в частности химических производств, мало чем отличаются от систем, которые проектировались и эксплуатировались еще в 80-х годах прошлого века.
В результате анализа эксплуатации производств гранулированных минеральных удобрений, в частности аммиачной селитры, было установлено, что технологические сбои производства определяются, в частности, ненадлежащим охлаждением продукта при формировании гранул.
Проблема усугубляется и тем, что температура наружного воздуха в летний период часто превышает расчетную проектную. Кроме того, относительная влажность воздуха в местах производств по разным причинам достигает 70–100% (пример – микроклимат из-за уноса воды из систем оборотного водоснабжения). Первоначальный поток жидкой флегмы продукта достигает температуры 150…170°С. Как следствие, на выходе из башен грануляции после аппаратов кипящего слоя температура продукта может доходить до 50…60°С, а содержание влаги в продукте превышать нормируемые 0,2–0,3%. Следствием этого является завершение модификационных переходных процессов в уже готовом продукте, который отправляется на фасовку и отгрузку, что значительно повышает слеживаемость аммиачной селитры, ведет к фактической потере товарного качества продукта.
Возможны и, наверное, неизбежны дополнительные остановы технологического процесса для очистки конусов и сеток от налипания селитры, что приводит к снижению производительности производства.
В конечном итоге это определяет непредвиденные дополнительные расходы энергоресурсов (пар, электроэнергия) либо приводит к увеличению расходов на технологический процесс для предотвращения подобных явлений.
Анализ технологической схемы производства аммиачной селитры ОАО «Куйбышев Азот» показал, что на нейтрализацию в аппараты ИТН направляется газообразный аммиак при давлении 0,15…0,35 МПа, что соответствует температурам кипения –25…–5°С. По технологическому регламенту жидкий аммиак испаряется в технологическом теплообменном аппарате при указанном давлении, затем пары аммиака подогреваются до температуры 45…50°С и направляются в реактор.
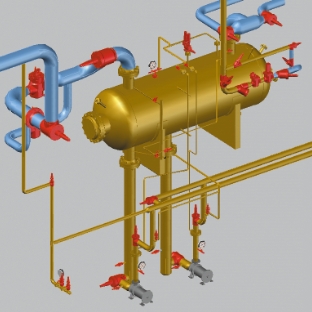
Было предложено использовать затратный процесс испарения аммиака, обратив его в полезный процесс испарения в воздухоохладителе-осушителе. Генерируемый искусственный холод при температуре 8°С и ниже предложено использовать для охлаждения направляемого в башню потока воздуха, ослабив влияние температурно-влажностных параметров наружного воздуха на процесс охлаждения гранулированного продукта в башне. Атмосферный воздух охлаждается в воздухоохладителе до температуры 12…14°С, теряя при этом значительное количество влаги.
В аппарате кипящего слоя, куда направляется охлажденный воздух (влажностью практически на пограничной кривой, но со значительно меньшим влагосодержанием), происходит охлаждение продукта и ассимиляция из него влаги. Продукт охлаждается до температуры, исключающей конденсацию на нем влаги из воздуха.
Для действующей установки производства гранулированного продукта аммиачной селитры предложена, спроектирована и реализована технология и система общей холодопроизводительностью 3,2 МВт (без остановки производственного процесса, что было принципиально важно).
Для холодоснабжения воздухоохладителей предложено использовать испаряющийся аммиак в насосно-циркуляционной системе с нижнейподачей жидкогоаммиакав бескомпрессорную систему охлаждения с отбором в дальнейшем паров аммиака на производственный процесс (рис. 1). Применение насосноциркуляционной системы позволяет использовать один емкостной сосуд одновременно для группы (четыре) аппаратов обработки воздуха, равномерно распределить подачу аммиака как между воздухоохладителями, такипосекциям,обеспечить высокую кратность циркуляции аммиака и достаточно высокую эффективность работы теплообменников.
Жидкий аммиак подается от общезаводского магистрального трубопровода и дросселируется в горизонтальный циркуляционный ресивер, который выполняет функции отделителя жидкости и сосуда, обеспечивающего надежную работу циркуляционных аммиачных насосов.
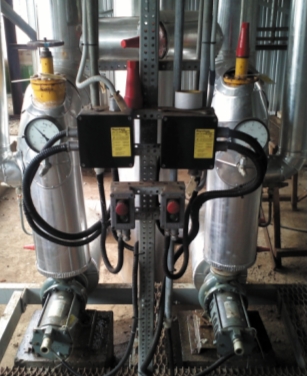
Моторизированный регулирующий вентиль на линии подачи жидкого аммиака обеспечивает плавное регулирование и поддержание уровня аммиака в циркуляционном ресивере и позволяет адаптировать систему под переменные тепловые и влажностные нагрузки в течение суток.
Для защиты насосов от режимов кавитации горизонтальный сосуд оборудован стояком для поддержания напора на всасывании в центробежные насосы.
Жидкий аммиак температурой до –8°С (давление 0,315 МПа) всасывается центробежным насосом (рис. 2) и направляется в аппараты обработки воздуха – воздухоохладители (рис. 3) через регулирующие вентили с расчетной кратностью циркуляции. Парожидкостная смесь аммиака, образовавшаяся в результате теплообмена с воздухом в аппаратах обработки, возвращается в циркуляционный ресивер, где жидкая и парообразная фракции разделяются.
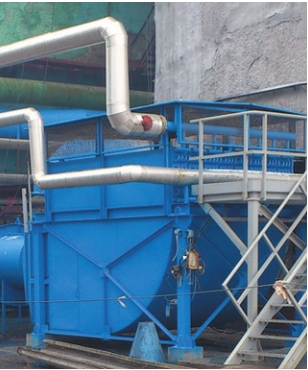
Парообразный аммиак отбирается либо в заводской коллектор паров аммиака, либо направляется в реакторы нейтрализации предварительно подогретый. Поддержание и регулирование давления в ресивере осуществляется бескомпрессорным способом путем сброса газообразного аммиака расчетной производительности в технологический процесс с помощью приборов автоматики прямого действия с регуляторами давления испарения до себя. Движущаяся сила процесса холодоснабжения – перепад давлений в магистральных трубопроводах.
Наружный воздух, проходя через специально сконструированные теплообменные пучки аппаратов охлаждения воздуха, охлаждается, осушается и направляется в аппараты кипящего слоя башни грануляции существующими центробежными вентиляторами, расположенными у основания грануляционной башни.
При этом воздух, частично подогреваясь, понижает относительную влажность. Дальнейшее его перемещение в полости башни, после прохождения аппаратов кипящего слоя, обеспечивается осевыми вентиляторами самой башни, которые создают некоторое разрежение внутри ствола башни.
Поток относительно «холодного» воздуха смешивается со «свежим» потоком, поступающим в башню через вентиляционные окна, дополнительно охлаждает падающий поток продукта внутри самой башни. В дальнейшем воздух выбрасывается верхними осевыми вентиляторами башни в атмосферу вместе с потоком влаги, ассимилированным из продукта.
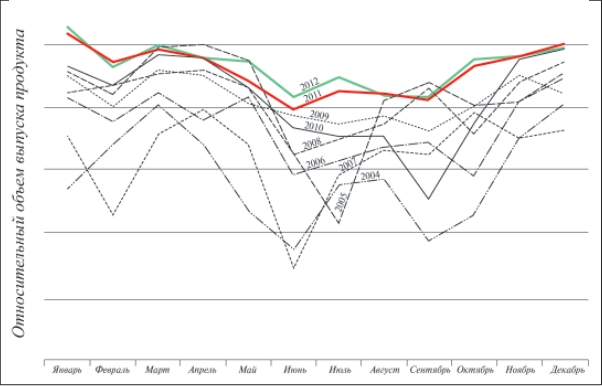
Важными элементами системы охлаждения являются аппараты обработки воздуха, индивидуально разработанные под технологический процесс с учетом допустимых потерь давления на всасывании в существующие центробежные вентиляторы. Изготовленные аппараты включают набор оребренных теплообменных труб, собранных в секции, опорную конструкцию, воздуховод, сепаратор влаги. Теплообменная поверхность аппарата изготовлена известным способом литья под давлением, биметаллическая ребристая поверхность с круглым литым ребром обеспечивает низкие потери давления (менее 100 кПа) в аппарате по ходу охлаждаемой среды. Аппарат изготовлен и испытан на производственных мощностях компании «Ладахим». Как уже отмечалось, для модернизируемого производственного процесса изготовлено и обвязано четыре аппарата обработки наружного воздуха, подаваемого в башни.
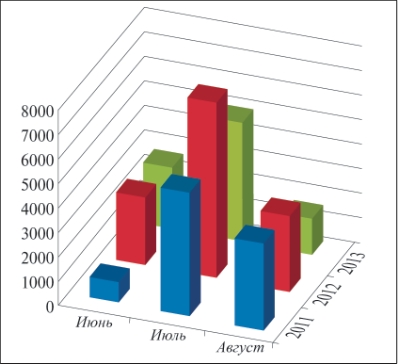
Насосно-циркуляционная система охлаждения с четырьмя аппаратами, горизонтальным циркуляционным ресивером, двумя аммиачными циркуляционными насосами, запорнорегулирующей арматурой и КИПиА смонтирована в действующем производстве аммиачной селитры и подтвердила свою работоспособность и эффективность. Воздух, подаваемый в аппараты кипящего слоя после аппарата охлаждения и осушения, в летний период минимум на 14…15°С ниже температуры при обычных условиях. Температура продукта на выходе из башни составляла 35…45°С, что соответствовало требования технологического регламента.
Следует отметить, что полученные производственные выгоды достигнуты практически без использования энергетических ресурсов.
Единственным дополнительным потребителем электроэнергии является один рабочий герметичный аммиачный насос установленной мощностью 7,5 кВт (система оборудована также и одним резервным насосом для обеспечения требуемой надежности технологического процесса).
К достоинствам предложенного решения можно отнести относительно низкие капитальные вложения на реализацию проекта, использование эффективного по термодинамическим показателям и экологически безопасного природного холодильного агента, расположение всего оборудования системы на открытых производственных площадках. Единственным сдерживающим фактором широкого внедрения технологии является обязательное наличие жидкого аммиака требуемых технологических параметров и возможность его дальнейшего производственного потребления в технологических производствах. В случае отсутствия такой возможности для реализации процесса охлаждения авторы предлагают использовать искусственных холод, полученный с помощью абсорбционных холодильных машин, утилизирующих вторичные энергетические ресурсы производства. Более детально технические и технологические особенности такого подхода предполагается рассмотреть в следующей публикации.
Уменьшение потерь продукта от нарушения регламентов производственного процесса, повышение качества продукта, снижение удельной энергоемкости процесса вследствие внедрения технологии дополнительного охлаждения с помощью искусственного холода корректно оценить сложно, да и в рамках данной публикации не нужно. Количественные показатели выработки селитры показаны на рис. 4; 5. Важно обратить внимание специалистов, прежде всего, на увеличение производственной мощности предприятия в летний период. Расчетный срок окупаемости инвестиций в предложенную и реализованную технологию не превышает одного года.