Автор: В.В. Кравцов, Б.Х. Ишмухаметов (ФГБОУ ВПО УГНТУ).
Опубликовано в журнале Химическая техника №2/2014
Комбинированная защита внутренней поверхности стальных резервуаров от коррозионного действия паровоздушной среды, заключающаяся в использовании лакокрасочного покрытия в сочетании с летучим ингибитором, помещаемым в специальных контейнерах через люки на крыше резервуара, в настоящее время начинает находить распространение на предприятиях нефтегазового комплекса.
Недостаточно высокие защитные свойства лакокрасочных покрытий (ЛКП) можно объяснить постоянно возрастающим количеством дефектов в покрытии (пузыри) и площадью анодных участков (дно пор). Идея комбинированной защиты паровоздушного пространства состоит в создании дополнительного электрического сопротивления в столбике электролита, заполняющего пору. На рис. 1 показаны схемы коррозионных гальванических элементов при использовании ЛКП и комбинированной защиты [1].
Эффективность защиты во многом зависит как от качества ЛКП, так и от выбора ингибитора. Известно большое количество ЛКП со сроком защитного действия а внутренней поверхности резервуара 10…15 лет.
Так как большинство летучих ингибиторов выпускается в качестве средств временной защиты металлов в ограниченных по объему пространствах, их выбор из числа серийно выпускаемых промышленностью, особенно для защиты нефтяных и нефтепродуктовых резервуаров, имеющих большие паровоздушные пространства, ограничен. Одной из задач, поставленных в данной работе, явилась апробация нового летучего ингибитора коррозии на основе компонентов российского производства.
Исследовали летучий ингибитор на основе алкилимидазолинов в виде компаундов с другими добавками.
Алкилимидазолины как компонент представляют смесь алкилимидазолинов изостроения и выпускаются в качестве активной основы известного ингибитора коррозии ВИКОР-1 (по ТУ 39-1313–88). Их структурная формула
Давление насыщенного пара летучих ингибиторов коррозии металлов является одной из важнейших характеристик, определяющих длительность защитного действия, концентрацию паров ингибитора в замкнутом объеме, а также (частично) и эффективность защитного действия.
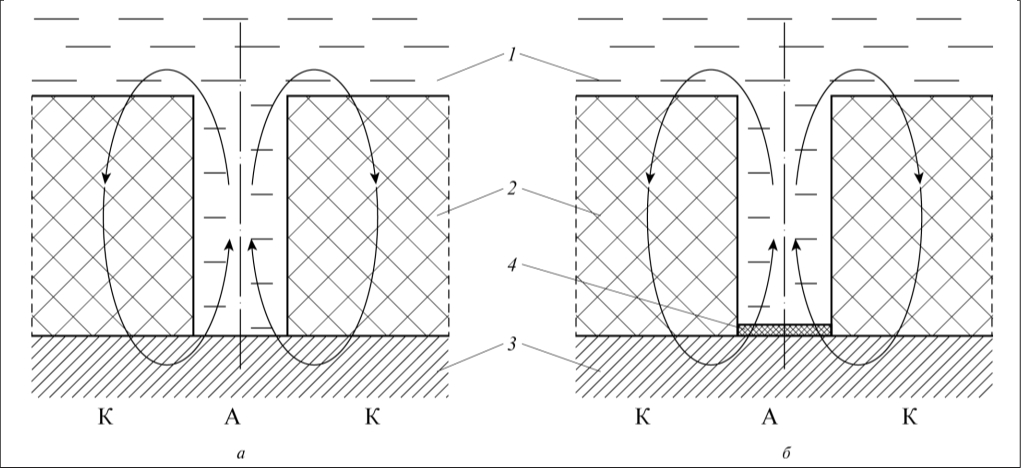
а – без ингибирования; б – с ингибированием; 1 – электролит; 2 – лакокрасочное покрытие; 3 – металлическая подложка;
4 – пленка ингибитора; К – катод; А – анод
В работе [2] предложена методика, представляющая собой усовершенствованный метод Стефана. Сходимость получаемых результатов достаточно убедительно аргументирована автором, поэтому данная методика принята нами для проведения исследований летучести ингибиторов.
С учетом скорости испарения определены рабочие концентрации алкилимидазолинов в паровоздушном пространстве:
Температура,°С | Концентрация, кг/м3 |
5 | 0,028 |
10 | 0,031 |
15 | 0,034 |
20 | 0,036 |
25 | 0,038 |
По своему определению летучий ингибитор коррозии имеет склонность к адсорбции на металлической поверхности с образованием защитной пленки. Адсорбционные свойства ингибиторов, являющиеся одной их основных его характеристик, достаточно полно изучены в ряде работ (например, [3, 4]).
Предстояло выяснить характер взаимодействия тучего ингибитора коррозии с лакокрасочными покрытиями и его влияние на свойства и защитную способность лакокрасочных покрытий.
В случае комбинированной защиты, описываемой в настоящей статье, металлическая поверхность перекрыта лакокрасочным покрытием. Для определения возможности сорбции ингибитора лакокрасочным покрытием и изменения некоторых свойств (прочность, пластичность) покрытий, влияющих на образовании дефектов (пузыри) и оголение металла при их разрушении, одну часть образцов в виде свободных пленок исследовали на изменение массы и прочностных показателей, а другую – на кинетику образования дефектов (пузыри).
Испытания лакокрасочных покрытий проводили в климатической камере (40°С, влажность 100%, соляной туман) на стальных пластинах размерами 100⋅50⋅3 мм из стали СтЗпс и стеклянных пластинах (с последующим отделением для получения свободных пленок) [5].
Половину образцов испытывали в ячейках с ингибиторами. Одну часть свободных пленок ЛКМ подвергали взвешиванию, другую – растяжению на разрывной машине РМИ-5 для определения предела прочности при разрушении и относительного удлинения при разрыве.
Ход кривых, отражающих кинетику изменения массы пленок при экспозиции в среде, приведен на рис. 2.
На основе полученных данных рассчитаны коэффициенты сорбции паров ингибитора в лакокрасочные покрытия. Определение коэффициентов проводилось с учетом рекомендаций ГОСТ 12020–72:
Z = Δmmax/V0,
где Z – коэффициент сорбции; Δmmax – максимальное приращение массы образца в процессе его набухания за счет сорбируемых компонентов среды; V0 – начальный объем образца.
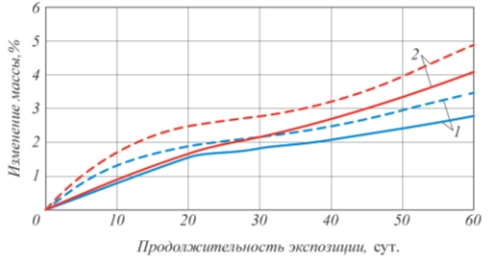
лакокрасочных пленок после экспозиции в средах
(40°С, относительная влажность 100%, соляной туман):
– без ингибитора; – – – – с ингибитором;
1 – ЭП-00-10; 2 – ХС-720
Величину Δmmax для каждого вида лакокрасочной пленки определяли путем решения системы уравнений:
m1 = mmax(1 – e–γτ1)
m1 = mmax(1 – e–γτ2)
где m1, m2 – масса образца после выдержки в рабочей среде в течение времени соответственно τ1, τ2; mmax – масса образца в установившемся равновесном состоянии; γ – bкоэффициент, постоянный для данных материала, температуры и условий испарения.
Приняв τ1 = 0,5τ2, получим выражение для определения коэффициента γ:
γ = –ln[(m2/m1 – 1)/τ1].
Максимальное приращение массы образца находили по формуле:
mmax = m1(1 – e–γτ1).
Значения коэффициента сорбции Z для некоторых систем ЛКП приведены в табл. 1.
Таблица 1.
Показатели сорбции летучего ингибитора коррозии лакокрасочными материалами (размеры образцов 100⋅50⋅3 мм)
Наименование ЛКМ | Начальная масса образца, г |
Плотность отвержденной пленки, г/см3 |
Z, г/см3 |
Краска ХС-720 | 20,118 | 1,34 | 0,075 |
Краска ЭП-755 | 26,703 | 1,78 | 0,102 |
Краска ХС-717 | 20,421 | 1,36 | 0,321 |
Эмаль ЭП-56 | 26,709 | 1,78 | 0,102 |
Лак 976-1 | 25,821 | 1,72 | 0,022 |
Эмаль ХС-710 | 20,112 | 1,34 | 0,088 |
Эмаль ЭП-140 | 27,061 | 1,80 | 0,093 |
Шпатлевка ЭП-00-10 | 27,753 | 1,85 | 0,076 |
Часть образцов с покрытиями исследовали на срок до образования пузырей и характер их изменения в ходе испытаний. Для определения склонности покрытий к образованию пузырей проведена визуальная оценка зарождения и развития дефектов (таблица 2).
Таблица 2.
Продолжительность стадий образования дефектов в ЛКМ при действии ингибированных и не ингибированных сред (40°С, влажность 100%, соляной туман, толщина пленки – 30 мкм)
Лакокрасочное покрытие | Наличие ингибитора | Время экспозиции, сут | |||||
30 | 60 | ||||||
Число пузырей | Средний диаметр, мм | Число лопнувших пузырей | Число пузырей | Средний диаметр, мм | Число лопнувших пузырей | ||
ЭП-00-10 | – | 10 | 7 | 1 | 16 | 9 | 6 |
+ | 3 | 6 | – | 12 | 9 | 4 | |
ХС-717 | – | 6 | 8 | 3 | 18 | 8 | 8 |
+ | 3 | 5 | 2 | 12 | 8 | 6 | |
ЭП-56 | – | 6 | 8 | 3 | 20 | 11 | 9 |
+ | 4 | 6 | 2 | 12 | 8 | 7 | |
ХС-710 | – | 8 | 9 | 3 | 20 | 12 | 9 |
+ | 6 | 6 | 2 | 14 | 8 | 5 |
Как видно, в ингибированной среде пузыри в обоих видах ЛКП образуются позже, чем в неингибированной.
Кроме того, интенсивность образования дефектов и их рост на всем протяжении эксперимента в ингибированной среде меньше, чем в неингибированной.
С учетом полученных данных, а также принимая во внимание, что при одностороннем воздействии поглощаемость компонентов среды практически в 2 раза меньше, чем при двухстороннем, определено количество летучего ингибитора, поглощаемого 1 м2 поверхности покрытия:
G = ZSδ/2,
где G – количество ингибитора, поглощаемого поверхностью ЛКП; S – площадь поверхности покрытия; δ – толщина покрытия.
Результаты расчета поглощаемого ингибитора
Покрытие | δ, мкм | G, г/м2 |
ЭП-00 | 100 | 37,5 |
ХС-717 | 120 | 6,1 |
ЭП-56 | 120 | 19,2 |
ХС-710 | 90 | 4,6 |
Приведенные о количестве поглощаемого ингибитора данные не могут существенно влиять на расход ингибитора, так как они соответствуют насыщенному состоянию.
Наличие сорбированного ингибитора в лакокрасочном покрытии повышает длительность действия защиты при случайных перебоях с поставкой ингибитора (например, при потерях за счет больших «выдохов»).
Часть свободных пленок после экспозиции подвергали механическим испытаниям на разрывной машине РМИ-5.
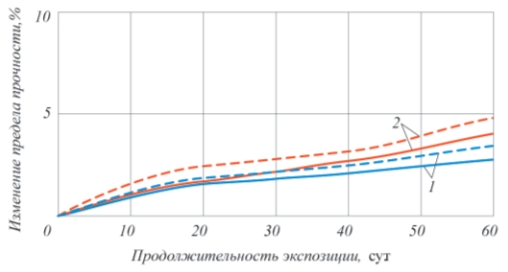
при растяжении лакокрасочных пленок после экспозиции
в средах (40°С, относительная влажность 100%, соляной
туман):
– без ингибитора; – – – – с ингибитором;
1 – ЭП-00-10; 2 – ХС-720
На рис. 3, 4 показаны кривые, характеризующие изменение предела прочности при растяжении и относительного удлинения при разрыве, для шпатлевки ЭП-00-10 и краски ХС-720 в ингибированной и неингибированной ячейках. Можно сделать заключение, что добавление ингибитора приводит к повышению пластичности покрытий, хотя прочность от этого незначительно снижается у всех исследуемых систем.
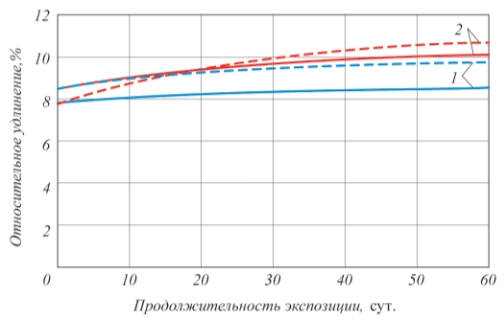
лакокрасочных пленок после экспозиции в рабочих средах
(40°С, отн. влажность 100 %, соляной туман):
– без ингибитора; – – – – с ингибитором;
1 – ЭП-00-10; 2 – ХС-720
Сопоставление полученных данных с кинетикой изменения механических свойств и массы пленок позволяет сделать вывод о пластифицирующей роли летучего ингибитора коррозии, сорбируемого лакокрасочным материалом (ЛКМ).
Основной причиной старения ЛКМ является, как правило, потеря пластификатора, который в течение эксплуатационного периода испаряется или вымывается из состава лакокрасочного покрытия. В результате этого покрытие снижает свои пластические свойства.
В последующем при пониженной способности к пластической деформации (при росте пузыря она довольно значительна) пленка покрытия, перекрывающая растущий дефект, лопается. В месте разрушения дефектов обычно и возникают очаги коррозии.
На основании результатов исследования можно сделать следующие выводы:
- летучий ингибитор частично сорбируется лакокрасочным покрытием;
- сорбция покрытием компонентов летучего ингибитора и коррозионной среды приводит к снижению предела прочности при растяжении и одновременно к повышению пластичности;
- повышение пластичности покрытия способствует увеличению инкубационного периода начала образования пузырей в покрытии и общего срока защитного действия комбинированной защиты; l экспериментально обоснована возможность повышения ресурса стальных резервуаров применением комбинированной защиты паровоздушного пространства.
Список литературы
- Красиков Д.В., Кравцов В.В. Проблемы и перспективы комбинированной защиты резервуаров для хранения нефти и нефтепродуктов//Прикладная синергетика II: Сб. науч. тр. Уфа: Изд. УГНТУ, 2004. Т.2.
- Голяницкий О.И. К вопросу о давлении насыщенных паров летучих ингибиторов коррозии//Защита металлов. Вып. 5. 1977. Т. XIII.
- Гафаров Н.А., Кушнаренко В.М., Бугай Д.Е. и др. Ингибиторы коррозии. Диагностика и защита от коррозии под напряжением нефтегазопромыслового оборудования. М.: Химия, 2002. Т. 2.
- Иванов Е.С. Ингибиторы коррозии металлов в кислых средах. М.: Металлургия, 1986.
- ГОСТ 14243–78. Материалы лакокрасочные. Методы получения свободных пленок.