Автор: Д.Г. Давыдова, А.Н. Кузьмин (ООО «Стратегия НК»), В.И. Гроховский (ФГАОУ ВПО «УФУ им. Б.Н. Ельцина»), Р.Г. Ризванов (ФГБОУ ВПО «УГНТУ»), Е.Г. Аксельрод (Кельн, Германия).
Опубликовано в журнале Химическая техника №4/2014
В настоящее время чрезвычайно востребовано техническое диагностирование оборудования без вывода из эксплуатации. С одной стороны, при таком подходе существенно снижаются экономические затраты, связанные с необходимостью изменения рабочего цикла, а иногда – с полной остановкой производства.
С другой стороны, в этом случае проведение контроля не зависит от сроков плановых ремонтов и позволяет получать оперативные данные о техническом состоянии объекта в реальном времени. В связи с этим активно развиваются методы оценки состояния в режиме мониторинга.
Такие возможности, в частности, открывает акустико-эмиссионный (АЭ) контроль.
Необходимость внеочередного технического диагностирования осевых сильфонных компенсаторов была вызвана рядом инцидентов, связанных с аварийными ситуациями вследствие разрушения оборудования. Проведение контроля существенно осложнялось тем фактом, что рассматриваемые компенсаторы установлены на действующей производственной линии, кратковременная остановка которой возможна только при наличии резервирующих устройств. Кроме того, при проведении АЭ контроля термокомпенсирующих элементов трубопровода без изменения рабочего цикла присутствует большое число нестационарных шумов различной природы: пневматический и гидродинамический шум движения рабочей среды в объекте контроля, структурный шум (релаксационные процессы при локальных термомеханических возмущениях), высокоамплитудные импульсные электрические помехи, внешние механические и электромагнитные помехи, конструктивный шум (процессы трения при взаимном перемещении поверхностей скольжения металла в слоях гофры), релаксационные шумы после восстановительных или ремонтных работ.
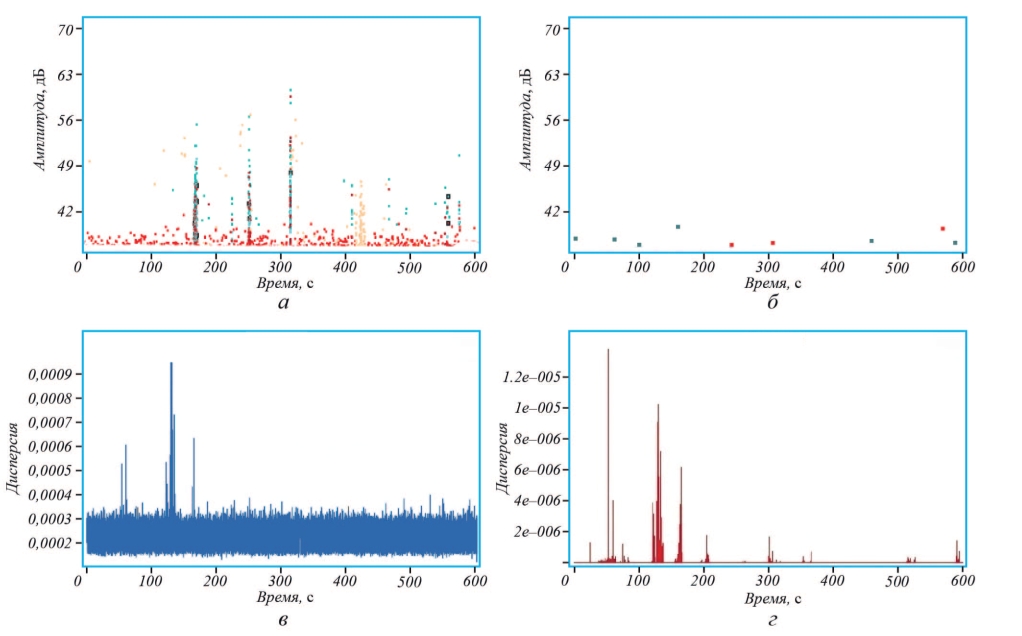
а, б – временные зависимости пиковых амплитуд АЭ сигналов, превышающих порог дискриминации (A-Line);
n – лоцируемые источники АЭ на дефектном объекте; в, г – локальные значения дисперсии АЭ сигналов (БРД)
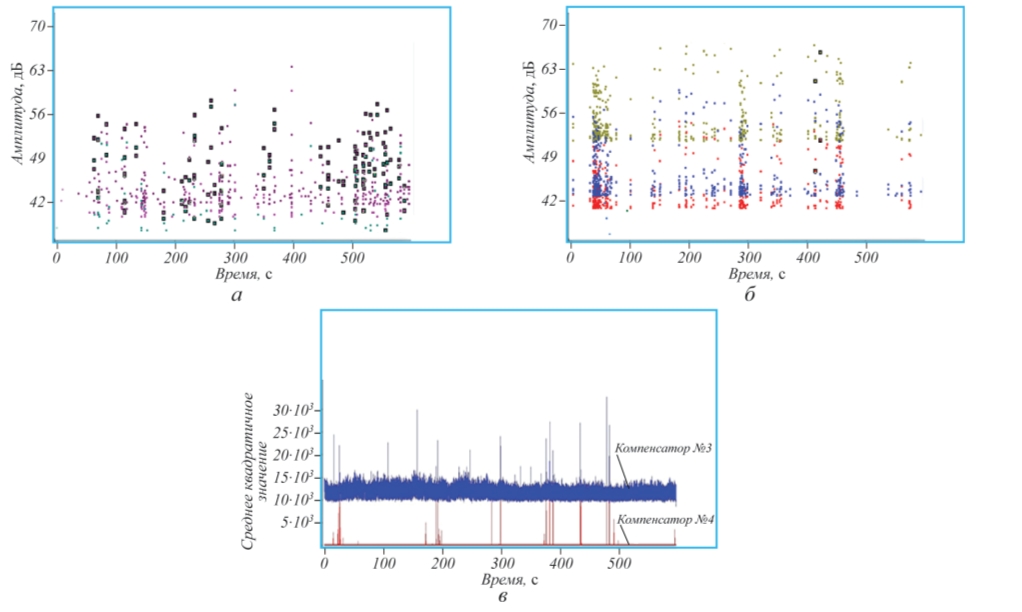
а, б – временные зависимости пиковых амплитуд АЭ сигналов, превышающих порог дискриминации (A-Line);
n –лоцируемые источники АЭ на дефектном объекте; в – локальные значения среднего квадратичного значения АЭ сигналов (БРД) обоих компенсаторов
Поскольку существующие системы АЭ контроля обладают низким уровнем помехозащищенности к такого рода шумам [1], а возможность проведения необходимого комплекса работ по снижению уровня шумов (согласно ПБ 03-593–03) отсутствует, высока вероятность появления ложных локаций АЭ сигнала, что в свою очередь влечет неверную трактовку результатов контроля.
Для оценки технического состояния компенсаторов без вывода их из эксплуатации впервые был использован подход, предполагающий одновременное использование двух независимых систем регистрации АЭ сигнала: стандартной АЭ системы (с выбором величины порога амплитудной дискриминации) и установки беспороговой регистрации данных (БРД). В ходе АЭ контроля с применением стандартной АЭ аппаратуры (A-Line 32D) были выявлены компенсаторы с источниками АЭ (рис. 1, а и 2, а). Обнаруженные источники АЭ соответствуют II (компенсатор №1, рис. 1, а) и III (компенсатор №3, рис. 2, а) классам опасности согласно ПБ 03-593–03, что свидетельствует о наличии опасных развивающихся дефектов. Для сравнения на рис. 1, б и 2, б приведены соответствующие амплитудно-динамические параметры и локационная диаграмма, полученные при контроле бездефектных компенсаторов (компенсаторы №2 и №4).
Принципиальное отличие системы беспороговой регистрации данных заключается в отказе от использования метода амплитудной пороговой дискриминации [2]. Устройство БРД была специально спроектировано для измерения и анализа АЭ сигнала на базе серийного модуля преобразователя напряжений L-Card Е20-10D (производство ООО «Л-КАРД», Москва). Цифровая обработка АЭ сигнала была реализована в программном комплексе MATLAB.
Ключевой особенностью обработки АЭ данных БРД является использование подвижного временного окна, другими словами, расчетные операции выполняются внутри выбранного временного интервала, «скользящего» по временному ряду АЭ сигнала. Основным диагностическим признаком является текущее значение статистических характеристик случайного акустического шума в момент возникновения и развития источников АЭ. При возникновении источников АЭ сигнала, связанных с развитием дефектов в объекте контроля (развивающаяся трещина, коррозионные процессы), природа регистрируемого акустического шума существенно изменяется [3], а соответствующие статистические характеристики принимают нешумовой детерминированный характер.
В данной работе при обработке данных, полученных при беспороговой регистрации, вычислялись значения следующих статистических параметров временного ряда АЭ: дисперсия, среднее квадратичное значение, асимметрия, эксцесс.
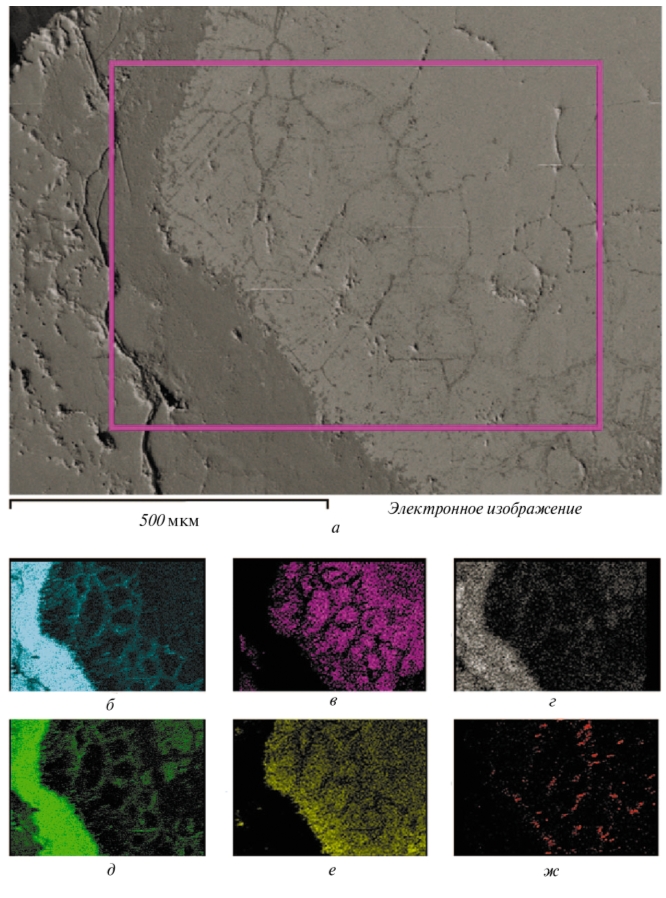
б – кислород; в –железо; г –марганец; д –хром; е – никель; ж –титан
Следует отметить, что в условиях БРД анализируются не интегральные характеристики АЭ сигнала, превышающего порог (амплитуда, энергия, длительность сигнала, интенсивность), а локальные (мгновенные) статистические параметры. Соответственно, отношение сигнал/шум в отличие от систем пороговой регистрации может быть в этом случае порядка или меньше единицы. Последнее условие для систем диагностического мониторинга является фактором, определяющим эффективность применения БРД.
На рис. 1, в, г и 2, в приведены статистические параметры АЭ сигналов при контроле компенсаторов с применением БРД. Практическая значимость анализа рис. 1, в, г и 2, в заключается в том, что появляется возможность выявить наличие нестационарной высокоамплитудной помехи, «подстраивающейся» под вид «полезного» сигнала АЭ. Так, на рис. 1, в, г отклонения статистических характеристик от фонового шума оказались идентичными, что свидетельствует о наличии высокоамплитудной помехи, приходящей на оба измерительных канала одновременно. Это позволило сделать вывод о бездефектной природе зарегистрированных в ходе АЭ контроля источников АЭ II класса опасности (компенсатор №1). Косвенно этот факт был подтвержден в ходе повторного контроля данного компенсатора, где источники АЭ не были выявлены. Как видно, на рис. 2, в (компенсатор №3) присутствуют ярко выраженные дополнительные максимумы отклонений от шума, отсутствующие при контроле компенсатора №4. Последнее подтвердило результаты контроля с применением АЭ системы A-Line о дефектной природе компенсатора №3.
Дополнительно для исследования макрои микроструктуры металла были подготовлены образцы из внутреннего и наружного слоев гофры компенсатора. Результаты, полученные при металлографическом исследовании материала компенсатора, представлены на рис. 3, а, где видна характерная структура окисления вдоль границ зерен, при этом нарушается механическая связь между соседними зернами.
Такая картина имеет место при межкристаллитной коррозии коррозионно-стойких сталей [4]. При такой разновидности коррозии вдоль границ зерен выделяются фазы, обогащенные хромом, главным образом, карбиды на основе хрома (Cr23C6).
Эти карбиды концентрируются на границах зерен, иногда образуя сплошную цепочку. При этом участки, непосредственно окружающие карбиды Cr23C6, оказываются существенно обедненными по хрому (менее 12%) и становятся электрохимически активными. Характерно, что в данном случае межкристаллитной коррозии подвержен как внутренний слой гофры осевого компенсатора, непосредственно соприкасающийся с транспортируемой средой, так и наружный слой гофры, доступ рабочей среды к которому исключен.
На подготовленных образцах дополнительно был проведен электронно-зондовый микроанализ. Микроанализ выполнен с использованием сканирующего электронного микроскопа FE-SEM Zeiss ΣigmaVP.
В ходе исследования получена информация о локальном химическом составе межзеренных пространств в материале компенсатора. Результаты электронно-зондового микроанализа приведены на рис. 3. Распределение хрома позволяет сделать предположение о выделении карбидов хрома по границам зерен и обеднению (обезлегирование) по хрому приграничных областей. Эти процессы характерны для межкристаллитной коррозии. Высокое содержание кислорода в межзеренном пространстве (см. рис. 3, б) свидетельствует о наличии прокорродировавшей зоны вдоль границ зерен металла (оксиды металлов). Таким образом, электронно-зондовый микроанализ подтвердил ранее высказанное предположение о том, что основным механизмом разрушения материала компенсатора является межкристаллитная коррозия. Кроме того, межкристаллитная коррозия объясняет как непрерывный характер локаций при контроле с применением пороговой АЭ системы, так и постоянные колебания локальных статистических характеристик при анализе результатов БРД.
По результатам комплексного технического диагностирования сильфонных трубопроводных компенсаторов установлено, что традиционный метод акустико-эмиссионного контроля, а также метод, основанный на беспороговой регистрации, являются взаимодополняющими и могут применяться одновременно, что позволяет исключить ложные локации, возникающие при работе стандартной пороговой АЭ системы в условиях интенсивных нестационарных помех.
Список литературы
- Баранов В.М., Гриценко А.И., Карасевич А.М. Акустическая диагностика и контроль на предприятиях топливноэнергетического комплекса. М.: Наука, 1998. 304 с.
- Аксельрод Е.Г., Давыдова Д.Г., Кузьмин А.Н. Помехоустойчивый метод обнаружения полезного сигнала в системах акустико-эмиссионного мониторинга опасных производственных объектов//Технадзор. 2013. №5(78). С. 86–89.
- Юдин А.А., Иванов В.И. Стохастическая теория акустической эмиссии при пластической деформации. Сообщение 1. Мощность и энергетический спектр сигнала А3//Диагностика и прогнозирование разрушения сварных конструкций. 1987. №5. С. 24–29.
- Колотыркин Я.М., Княжева В.М. Итоги науки и техники. Сборник. Сер.: Коррозия и защита от коррозии. М.: ВИ- НИТИ, 1974. Т. 3. С. 5–83.