Авторы: А.М. Норов, С.В. Иванычев, Е.В. Козлова (АО «НИУИФ»).
Опубликовано в журнале Химическая техника №7/2018
Как уже неоднократно указывалось, развитие крупнотоннажного производства фосфорсодержащих удобрений на территории бывшего СССР за последние тридцать с лишним лет осуществлялось в основном за счет модернизации существующих мощностей [1, 2]. И хотя в настоящее время в ряде ведущих компаний России, Белоруссии, Казахстана, Литвы, Узбекистана, и других стран довольно активно прорабатываются вопросы проектирования и строительства новых производственных мощностей по выпуску комплексных фосфорсодержащих удобрений, техническое перевооружение и реконструкция действующих цехов по-прежнему будет иметь очень большое значение для развития отрасли. АО «НИУИФ» – старейший и единственный в России специализированный научно-исследовательский и проектный институт по фосфорсодержащим удобрениям за свою почти 100-летнюю работу накопил значительный опыт по этим вопросам.
Целями модернизации (или технического перевооружения) производства чаще всего являются [1, 2]:
- увеличение производительности;
- расширение ассортимента продукции;
- улучшение качественных показателей продукции;
- повышение надежности работы технологических ниток, снижение простоев;
- уменьшение себестоимости продукции, снижение расходных норм по сырью и энергоресурсам;
- улучшение экологических показателей;
- использование других видов сырья, различного рода добавок и пр.
- и другие.
Зачастую стараются достигнуть сразу нескольких целей из числа перечисленных, поэтому разрабатываемые технические решения по реконструкции должны носить комплексный характер. В основе комплексного подхода, применяемого АО «НИУИФ» при модернизации производств, лежит следующая схема (рис. 1).
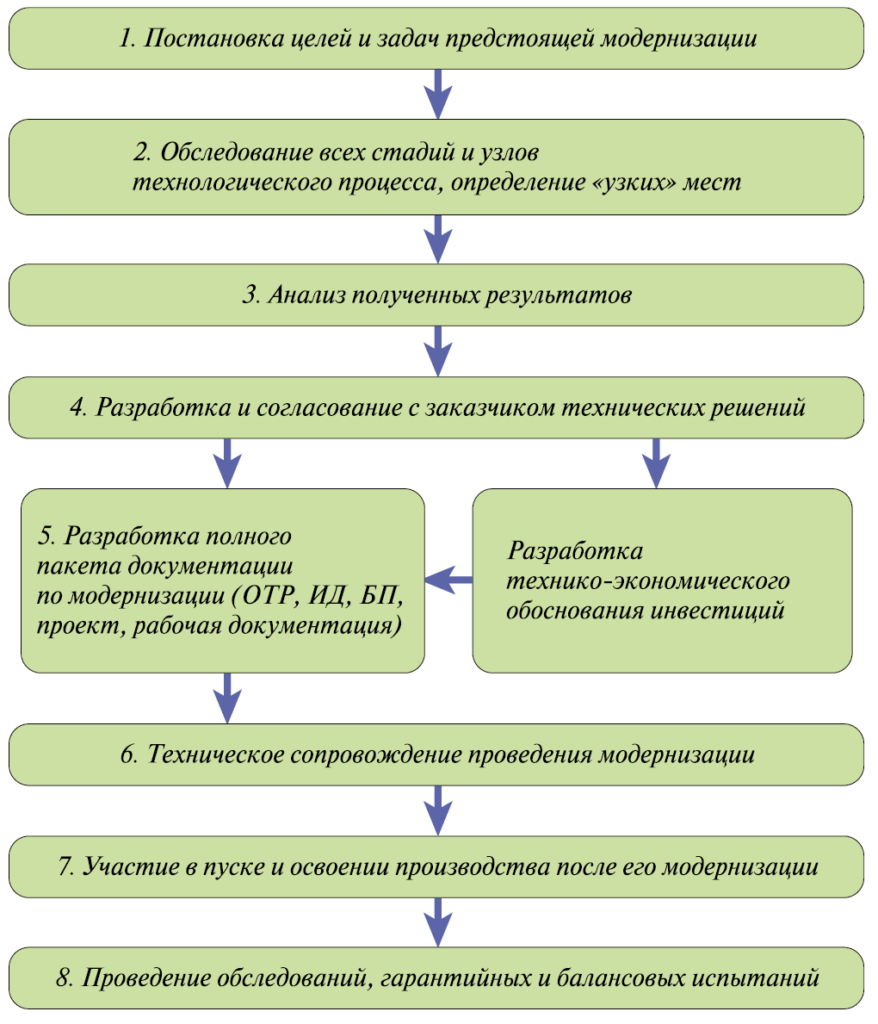
После определения целей и задач модернизации проводится комплексное обследование (аудит) всех стадий и узлов производства с целью выявления «узких» мест. Далее проводится анализ полученных результатов, на основании которого с учетом опыта работы наиболее эффективных предприятий отрасли и новейших научно-технических достижений разрабатываются и согласовываются с заказчиком технические решения. При подготовке решений очень важно учитывать тот факт, что в реальном технологическом процессе все стадии тесно связаны друг с другом, и изменения в какой-либо одной неизменно влекут за собой изменения во всех других стадиях. Поэтому при разработке технических решений эту взаимосвязь и взаимозависимость необходимо учитывать, не замыкаясь в рамках одной стадии, а наоборот, ясно представляя весь технологический процесс в целом. Именно это и является одной из составляющих комплексного подхода, реализуемого АО «НИУИФ» при разработке научно-технической продукции.
Основными стадиями в производстве комплексных минеральных удобрений являются:
- прием, подготовка, складирование и подача в производства сырья;
- нейтрализация;
- гранулирование;
- сушка;
- рассев и дробление;
- охлаждение;
- кондиционирование;
- складирование, дообработка и отгрузка;
- очистка газов.
Предлагаемые АО «НИУИФ» технические решения по каждой из этих стадий изложены в работе [1], здесь же кратко рассмотрим наиболее значимые из них.
- Нейтрализация. В зависимости от концентрации исходных кислот и марок выпускаемых удобрений возможны различные варианты схемы нейтрализации:
- одностадийная;
- двухстадийная (в том числе и с промежуточной упаркой пульпы);
- нейтрализация с раскислением (смешиванием концентрированных кислот с пульпой или двух пульп с разной степенью нейтрализации).
Рис. 2. Универсальная (комбинированная) схема нейтрализации с использованием аппарата САИ Сравнительный анализ различных схем нейтрализации выполнен в работах [3, 4]. АО «НИУИФ» часто предлагает (особенно для гибких технологических схем) универсальные (или комбинированные) схемы нейтрализации, которые позволяют работать как в одностадийном, так в двухстадийном режиме. Пример таких схем приведен на рис. 2, 3.
Рис. 3. Универсальная (комбинированная) схема нейтрализации с использованием аппарата ПН На первой стадии обычно используют емкостные реакторы с перемешивающим устройством либо аппараты САИ (скоростные аммонизаторы-испарители), на второй – трубчатые (струйные) реакторы (ТР). Применение ТР в производствах минеральных удобрений при переработке концентрированных кислот позволяет получить пульпы влажностью 4–10%, что в свою очередь интенсифицирует технологический процесс, снижает ретурность и удельные расходы энергоресурсов, повышает производительность и т.д.
- Гранулирование и сушка. Технологии производства удобрений, разрабатываемые и модернизируемые в АО «НИУИФ», базируются в основном на схемах с аммонизаторами-грануляторами (АГ) и сушильными барабанами (СБ) либо на схемах с барабанными грануляторами-сушилками (БГС), в которых процессы гранулирования и сушки совмещены. АО «НИУИФ» обладает значительным опытом оптимизации и интенсификации гранулирования и сушки как на технологических нитках с АГ–СБ, так и оснащенных аппаратами БГС.
- Рассев, дробление. Узел рассева и дробления, хотя на первый взгляд и воспринимается как чисто механический, но очень тесно связан с работой узла гранулирования, а также от него сильно зависят качественные показатели продукции. Поэтому АО «НИУИФ» всегда проводил работы по совершенствованию этого узла.
Рис. 4. Принципиальная схема узла рассева–дробления с возможностью регулирования процесса гранулирования:
1 – БГС; 2 – элеватор; 3 – конвейер ленточный ретура; 4/1, 4/2 – виброраспределитель; 5/1, 5/2 – виброгрохот; 6/1, 6/2 – дробилка цепная; 7 – конвейер ленточный готового продукта; 8 – автоматический анализатор грансостава; 9/1, 9/2, 10/1, 10/2 – шибер (заслонка) с дистанционным управлением; 11 – ретурные весыНа рис. 4 показана перспективная схема рассева–дробления, с помощью которой можно регулировать процесс гранулирования [5]. По данному способу шихта после БГС или СБ элеваторами подается на два виброраспределителя, с помощью которых равномерно распределяется по ширине сеток виброгрохотов, на которых рассеивается на фракции. Мелкая фракция из-под нижних сит поступает непосредственно в ретур, а товарная фракция заслонками с дистанционным управлением делится на две части: одна поступает на транспортер готового продукта и далее следует на охлаждение и т.д., вторая часть направляется в ретур. В свою очередь, направляемая в ретур часть товарной фракции заслонками с дистанционным управлением делится на два потока, один из которых напрямую направляется на ретурный конвейер, а второй предварительно измельчается в цепных дробилках, а затем также поступает в ретур. На эти же цепные дробилки поступает и крупная фракция с верхних сит грохотов, после измельчения подаваемая в ретур. Частота вращения роторов цепных дробилок (т.е. интенсивность измельчения) и количество товарной фракции, направляемой на дробление, автоматически регулируется частотными регуляторами и управляемыми заслонками на основании показаний автоматического анализатора грансостава, который фиксирует укрупнение или образование мелкой фракции.
Такая схема узла рассева–дробления позволяет регулировать и стабилизировать гранулометрический состав удобрений без вмешательства в основные технологические параметры процесса: температуру, степень нейтрализации и т.д., изменение которых может негативно влиять на другие показатели – производительность, качество продукта, экологические показатели и др. Следует подчеркнуть, что для реализации такой схемы необходимо выполнить предложенную выше схему установки: 1 грохот – 1 дробилка.
- Охлаждение и кондиционирование. В качестве охладителей готового продукта обычно используются либо конвективные аппараты (вращающиеся барабаны охладители, охладители кипящего слоя (КС)), либо кондуктивные аппараты, в которых охлаждение осуществляется водой через стенку охлаждающих элементов (обычно пластин или труб) из нержавеющей стали. Конвективные охладители имеют большую производительность, высокий коэффициент теплопередачи, в них одновременно происходит и обеспыливание продукта, выравнивается поверхность гранул и снижается пылимость. Однако они требуют значительных затрат на подачу и очистку теплоносителя (воздуха).Кондуктивные (водяные) охладители имеют значительно меньшие энергетические затраты на эксплуатацию, для них не требуется очистка больших потоков отходящих газов. Вместе с тем они более металлоемки, требуют организации водяного цикла с охлаждением, в них не происходит обеспыливания продукта. С нашей точки зрения, кондуктивные водяные аппараты следует применять для доохлаждения продукта после охладителей КС (или барабанов).В случае, когда для нейтрализации ЭФК может быть использован аммиак давлением не более 3 атм. (емкостные нейтрализаторы, аппараты САИ), целесообразно использовать холод от испарения жидкого аммиака для охлаждения воздуха, подаваемого в барабанный охладитель или охладитель КС в теплое время года [3, 4]. Холод от испарения аммиака можно использовать и для охлаждения воды, подаваемой в кондуктивный водяной охладитель. При этом испарение можно производить при более высоких температурах, газообразный аммиак будет иметь более высокое давление, и его можно перерабатывать не только через емкостные нейтрализаторы и САИ, но и через ТР.Каждый способ охлаждения имеет свои преимущества и недостатки, и выбор схемы охлаждения и типа аппарата зависит от многих факторов: свойств продукта, климатических условий, возможностей и состояния конкретного производства и т.д.
Нанесение на поверхность гранул кондиционирующей смеси для улучшения свойств удобрений – снижения слеживаемости и пылимости – рекомендуется производить в специальных барабанах-кондиционерах, но для этих целей можно использовать и барабанный охладитель, и охладитель КС [6].
- Очистка газов. Специалистами АО «НИУИФ» разработаны высоэффективные двух- и трехступенчатые системы очистки газов в производствах минеральных удобрений и фосфорной кислоты [7], где в качестве первых и вторых ступеней обычно используются полые башни и абсорберы Вентури с высокой плотностью орошения, а в качестве третьей ступени – абсорбер АПС (аппарат пенный скоростной) [8], высокоэффективный аппарат с внутренней циркуляцией жидкости и относительно небольшим гидравлическим сопротивлением. Абсорбер АПС может также использоваться в качестве пылеуловителя в системах аспирации; кроме того, он обладает хорошими брызгоулавливающими свойствами. На рис. 5 приведена принципиальная схема системы абсорбции после БГС в производстве минеральных удобрений.
Рис. 5. Принципиальная схема системы абсорбции после БГС в производстве минеральных удобрений:
25 – полый абсорбер; 26 – абсорбер АПС; 24 – абсорбер Вентури; 28, 28А – баки; 291,2,3, 29А – насосы; 27 – вентилятор
Особо следует отметить, что все разработки АО «НИУИФ», особенно за последние годы, изначально были ориентированы на соблюдение принципов наилучших доступных технологий (НДТ) с учетом обеспечения следующих показателей [9]:
- минимального негативного воздействия на окружающую среду;
- высокой степени использования сырьевых ресурсов;
- энергосбережения;
- экономической эффективности;
- использования передового оборудования;
- применения гибких технологий.
Все эти показатели тесно взаимосвязаны друг с другом, и для их достижения требуется комплексный подход.
Технические решения, разрабатываемые АО «НИУИФ» для производств удобрений, предусматривают:
- отсутствие твердых отходов;
- отсутствие стоков;
- наиболее полное использование тепла химических реакций;
- эффективную пылегазоочистку;
- высокую степень использования сырья, низкие потери;
- высокую производительность;
- оптимальный подбор современного передового энергосберегающего оборудования;
- переработку отходов;
- и др.
Соответствие принципам НДТ всегда было характерной особенностью работы АО «НИУИФ», даже в те времена, когда еще официально не существовало такого понятия.
Особо следует остановиться на гибких технологиях, под которыми обычно подразумевают процесс производства фосфорсодержащих удобрений на одной технологической линии, обеспечивающей любые потребности сельскохозяйственных производителей как на внутреннем, так и на внешнем рынках [10]. При этом также должны обеспечиваться:
- высокое качество производимых удобрений;
- отсутствие стоков и твердых отходов;
- эффективная очистка газов;
- высокая производительность;
- низкие энергозатраты;
- возможность переработки фосфатного сырья различных месторождений либо их смесей.
Основные преимущества гибких технологий:
- обеспечение выпуска широкого ассортимента продукции;
- возможность быстрой переналадки под выпуск любой марки удобрений из перечня освоенных.
Несмотря на то, что затраты на создание гибкой технологической схемы могут быть несколько выше, чем предназначенной под выпуск монопродукта, гибкие технологии в большей степени способствуют достижению целей и принципов НДТ. Производство востребованного ассортимента различных марок удобрений на одной технологической нитке по гибкой технологии, безусловно, обусловливает меньшие капитальные затраты, меньшее воздействие на окружающую среду и меньшие энергозатраты, чем выпуск их на нескольких специализированных под монопродукты производственных мощностях. Типичным примером гибкой технологии является представленная на рис. 6 схема производства комплексных нитратсодержащих удобрений [11]. В завершение еще раз хочется сказать, что для АО «НИУИФ» стратегия комплексного подхода является основополагающей при решении научно-производственных задач и составляет отличительную особенность института. Это проявляется на нескольких уровнях (рис. 7):
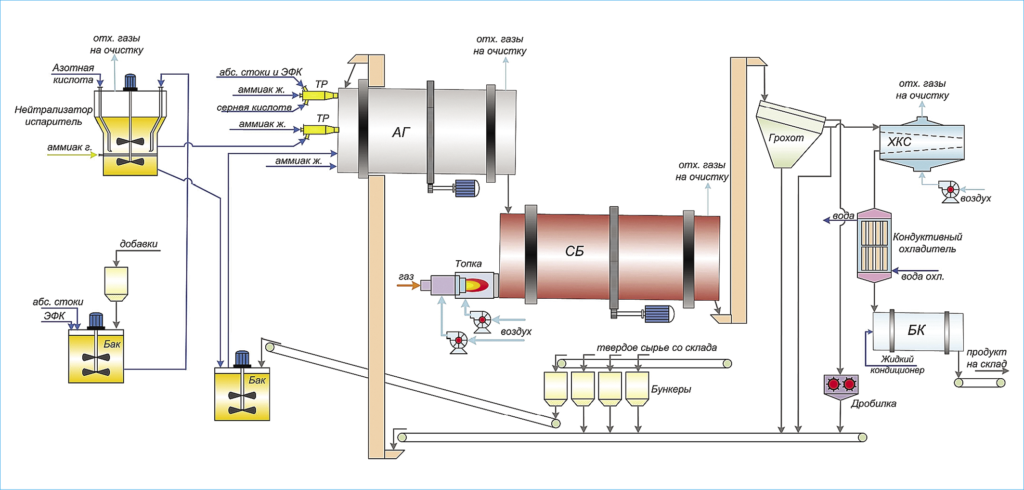
- Учет тесной взаимосвязи и взаимозависимости всех стадий и показателей технологического процесса при разработке технических решений. Это достигается благодаря квалифицированному персоналу, многолетнему опыту, накопленному в институте и передающемуся от старшего поколения к младшему, наличия фонда трудов, в котором сосредоточены результаты научных исследований и технических разработок за многие годы, наличию собственной научно-исследовательской базы, тесной взаимосвязи с ведущими научными учреждениями и университетами России и зарубежья, постоянной работе с предприятиями отрасли, постоянному обучению и повышению квалификации кадров, освоению смежных профессий и подготовке универсальных кадров, участию в международных конференциях, выставках, семинарах и других мероприятиях. В принципе здесь можно говорить о сложившейся научно-производственной школе АО «НИУИФ»;
- Наличие высококвалифицированных специалистов по всем ключевым производствам: добыча и обогащение сырья, серная кислота, экстракционная фосфорная кислота, минеральные удобрения, кормовые, технические очищенные соли, переработка фтористых соединений, переработка и размещение отходов и др. Это позволяет заниматься в рамках одного института комплексным развитием предприятий отрасли;
- Сочетание в одном институте высококвалифицированных научных и проектных кадров позволяет комплексно выполнять широкий спектр работ: проведение научно-исследовательских и поисковых работ, разработка и модернизация технологий (физико-химические основы, основные технические решения, исходные данные для проектирования, базовые проекты), проведение обследований и опытно-промышленных испытаний, разработка проектной и рабочей документации, участие в пуске и освоении производства и пр.
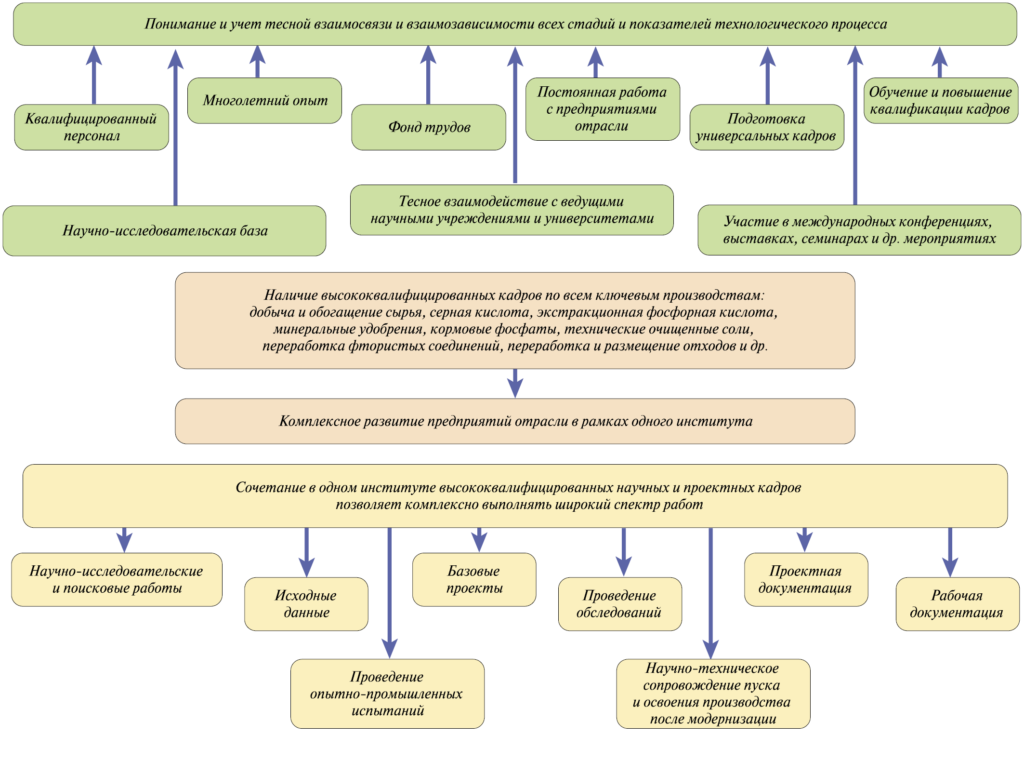
В совокупности это и составляет основу стратегии комплексного подхода к решению научно-производственных задач АО «НИУИФ».
В таблице показаны некоторые из работ АО «НИУИФ» в области производства минеральных удобрений, выполненных за последние годы.
АО «НИУИФ» всегда готово сотрудничать на взаимовыгодных условиях.
Список литературы
- Норов А.М., Малявин А.Г., Цикин М.Н. Модернизация и развитие производства комплексных фосфорсодержащих удобрений//Материалы международной научно-практической конференции «Современные тенденции в производстве и применение фосфорсодержащих удобрений и неорганических кислот». М.: НИУИФ, 2015. С. 12–25.
- Норов А.М. Развитие производств фосфорсодержащих минеральных удобрений и создание гибких технологий//Химическая техника. 2017. № 2. С. 30–32.
- Давыденко В.В., Норов А.М., Гришаев И.Г. и др. Опыт технического перевооружения производства удобрительных фосфатов аммония на ООО «Балаковские минеральные удобрения»//Бюллетень «Мир серы, N, P и K. 2011. Вып. 2. С. 4–11.
- Черненко Ю.Д., Норов А.М., Гришаев И.Г. и др. Возможности интенсификации производства комплексных фосфорсодержащих удобрений//Химическая техника, № 10. 2011. С. 10–15.
- Пат. РФ № 2545328. Способ регулирования процесса гранулирования фосфорсодержащих удобрений.
- Гришаев И.Г. Новое в технике и технологии фосфоросодержащих удобрений//Труды НИУИФ. М., 2014. С. 375–382.
- Евграшенко В.В., Норов А.М. Разработка схем абсорбции в производстве минеральных удобрений//Химическая промышленность сегодня. 2012. № 12. С. 45–47.
- Пат. РФ № 2201277. Аппарат для проведения тепломассообменных процессов.
- Норов А.М., Пагалешкин Д.А., Федотов П.С., Колпаков В.М., Евграшенко В.В. Создание и внедрение наилучших доступных гибки технологий комплексных фосфорсодержащих удобрений//Химическая техника. 2017. № 5. С. 38–42.
- Седельников В.П. Гибкая технология производства фосфорсодержащих удобрений. Дис. … канд. техн. наук. М.: НИУИФ, 1996.
- Пат. РФ № 2541641. Способ получения комплексного удобрения.