Автор: В.М. Давыдов, С.Д. Рязанов, Л.С. Алексенцева (ООО НПП «Механик»).
Опубликовано в журнале Химическая техника №2/2016
В Федеральном законе «О промышленной безопасности опасных производственных объектов» (116-ФЗ) приведено понятие «инцидент», которое характеризуется, в том числе как отклонение от режима технологического процесса. Организация, эксплуатирующая опасный производственный объект, обязана в случае инцидента в определенных условиях приостанавливать эксплуатацию, анализировать причины возникновения инцидента, принимать меры по устранению указанных причин и профилактике подобных нарушений; предоставлять в федеральный орган исполнительной власти информацию о числе аварий и инцидентов.
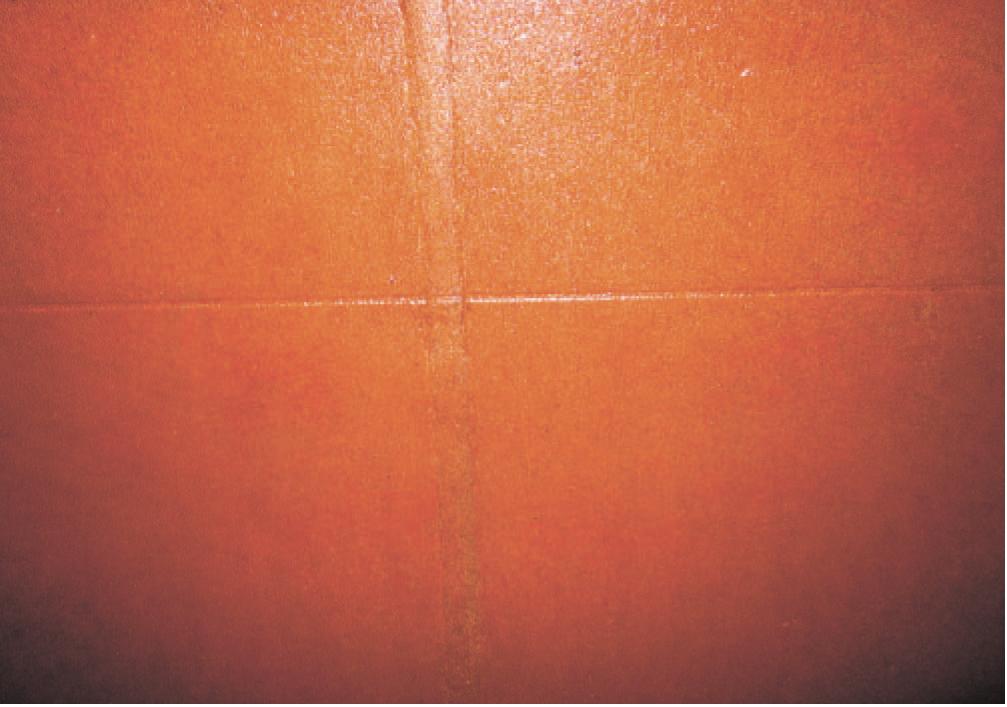
При выполнении работ по экспертизе промышленной безопасности и оценке остаточного ресурса оборудования, работающего в условиях воздействия агрессивных сред, наибольшие трудности связаны с определением расчетной скорости коррозии. Это осложняется возможными отклонениями технологического режима, которые вызывают ускорение процессов разрушения материалов несущих элементов конструкций. Приведем некоторые примеры.
На предприятиях водоподготовки для обеззараживания воды широко применяется технология хлорирования воды и, соответственно, организуются склады для хранения жидкого хлора. В 2012 г. при проведении экспертизы промышленной безопасности одного из танков при внутреннем осмотре была обнаружена горизонтальная замкнутая канавка глубиной до 2 мм и шириной 3… 4 мм (см. рисунок). Аппарат представляет собой горизонтально расположенную емкость вместимостью 40 м3, диаметром 2 200 мм, длиной 9 600 мм и толщиной стенок 14 мм. Рабочее давление – 1,6 МПа, материал – сталь 09Г2С-9.
Характер и расположение повреждения заставляют считать, что оно вызвано развитием интенсивной коррозии по линии раздела фаз. Углеродистые стали в чистом хлоре обладают достаточной стойкостью против разрушения, однако при появлении влаги образуется соляная кислота, что вызывает значительное увеличение скорости коррозии. Такой характер повреждения хлорных емкостей проявляется довольно редко, так как содержание влаги в жидком и газообразном хлоре жесткие ограничено.
Появление воды в хлорном танке возможно только в период его периодического освидетельствования или экспертизы в процессе гидроиспытаний. Тогда либо сосуд долго находится частично заполненным водой, либо после проведения испытаний не бывает тщательно осушен и заполняется жидким хлором при наличии пароводяной подушки. В обоих случаях образующаяся на границе раздела фаз соляная кислота вызывает довольно значительные поверхностные повреждения. Время воздействия этих факторов в данном случае установить не удалось, но, определенно, оно было непродолжительным.
Другой пример связан с хранилищем концентрированной серной кислоты, работающим под атмосферным давлением (вместимость – 1700 м3, диаметр – 15 м, высота – 18 м). Материал емкости – сталь ВСт3сп.
При проведении внутреннего осмотра также обнаружены множественные протяженные коррозионные канавки глубиной 3…5 мм, расположение которых повторяет воображаемую границу раздела фаз. Скорость коррозии материала несущей конструкции в концентрированной серной кислоте не превышает 0,1 мм/год. Однако причиной увеличения коррозии послужило появление сквозных свищей в кровле, стекание атмосферных осадков внутрь по обечайке емкости с образованием зон разбавления кислоты по ватерлинии. Агрессивность серной кислоты существенно возрастает со снижением концентрации.
Принимая во внимание множественность таких повреждений при технологических колебаниях уровня, можно предположить, что суммарная глубина и скорость коррозии достаточно высоки. В связи с этим по результатам экспертизы кроме ремонта кровли была выдана следующая рекомендация: не выдерживать хранилище длительное время при постоянном уровне заполнения.
В производстве азотной кислоты произошло разрушение корпуса нагнетателя нитрозных газов. Нагнетатель является одним из элементов газотурбинной установки, в которую также входят высокотемпературная приводная газовая турбина, осевой воздушный компрессор и пусковая паровая турбина, механически связанные между собой. Конструкция представляет собой двухкорпусный четырехступенчатый центробежный компрессор, внутренний корпус которого с направляющим аппаратом размещен в несущем цилиндрическом корпусе, нагруженном давлением нагнетания. Характеристика нагнетателя: давление на входе – 0,35 МПа, давление на выходе – 1,1 МПа, частота вращения – 5 000 об/мин, температура на входе и выходе соответственно 65 и 180°С. Материал несущего корпуса – сталь 12Х18Н10Т, толщина стенки корпуса – 24 мм.
В результате технологического нарушения в работе влагоотделителя во всасывающую линию нагнетателя произошел заброс капельных включений слабой (60%) азотной кислоты. При сжатии нитрозных газов в четырех ступенях происходит повышение температуры корпуса, в котором сепарируется кислота. С повышением температуры скорость коррозии в азотной кислоте значительно увеличивается в зонах концентрации напряжений, в первую очередь таких, как сварные швы. В результате развития ножевой коррозии в зоне сплавления шва с основным металлом появились повреждения глубиной 4…6 мм. Время наработки с момента предыдущего внутреннего осмотра составило два года, однако реальное время воздействия агрессивной среды не установлено.
Следует отметить, что значительной коррозии на поверхности основного металла не отмечалось.
После ремонта в условиях производства не удалось качественно произвести термообработку сварных швов, в последующем после устранения технологических нарушений процесс ножевой коррозии с меньшей скоростью сохранился.
Агрессивность кислот значительно изменяется в зависимости от температуры, концентрации, а также от наличия других компонентов, изменяющих свойства рабочей среды. Часть таких инцидентов может иметь скрытый характер, т.е. некоторые изменения технологического процесса не квалифицируются как отклонения от режима.
В связи с этим при оценке остаточного ресурса оборудования, работающего в условиях воздействия агрессивных сред, наибольшие трудности связаны с определением скорости и времени воздействия при отклонениях технологического режима. Очевидно, что при выполнении работ по экспертизе промышленной безопасности химического оборудования анализ технической документации как обязательный этап программы обследования должен содержать изучение фактических параметров работы технических устройств, их возможные отклонения. В расчет допускаемого срока дальнейшей эксплуатации должна быть заложена скорость коррозии с учетом возможного влияния изменения технологического процесса.