Авторы: Ф.И. Галушко (АО «МХК «ЕвроХим), C.И. Жданов (АО «НАК «АЗОТ»), А.Ф. Моисеенко (АО «МХК «ЕвроХим).
Опубликовано в журнале Химическая техника №12/2018
Cовременный ассортимент промышленных взрывчатых веществ (ВВ) состоит из простейших взрывчатых смесей (ПВС) двух основных классов: сыпучих и водосодержащих. ПВС типа аммиачной селитры – дизельное топливо (АС – ДТ) дешевле, но не всегда более экономичны. Простейшие водосодержащие взрывчатые смеси (ПВВС) более разнообразны по своему составу. Состав АС – ДТ не нов; он был известен с начала 60-х годов прошлого столетия, когда бризантные ВВ стали применять в промышленности. Новым в АС – ДТ было применение пористой аммиачной селитры (ПАС). Уникальность свойств и огромное промышленное значение АС – ДТ обусловливались физическими свойствами этих гранул [1].
Использование аммиачной селитры (АС) в качестве компонента промышленных взрывчатых веществ (ПВВ) обусловлено ее способностью к экзотермической реакции с выделением кислорода. АС широко применяется в качестве основного окислителя в простейших ВВ с дизельным топливом (АС – ДТ) и в эмульсионных ВВ в смесях с эмульсионной матрицей (АС – ЭМ). К АС в этих составах при их нахождении в скважине предъявляются следующие требования: физическая стабильность заряда АС – ДТ (отсутствие расслоения компонентов) и образование стабильной смеси с эмульсионной матрицей. Для этого АС должна обладать определенными свойствами и иметь необходимую структуру гранул. В зарубежной практике ведения взрывных работ широкое применение нашли простейшие взрывчатые смеси типа АС – ДТ на основе ПАС. В России до последнего времени эффективное применение в большом объеме таких смесей сдерживалось нестабильностью состава ВВ из-за применения «плотной» АС по ГОСТ 2–2013 [2]. В зарубежных источниках информации по данной тематике применяется также термин HDAN – High Density Ammonium Nitrate (Высокоплотная Аммиачная селитра).
В целях решения проблем, которые были обозначены горняками в части производства высококачественных ПВВ с применением качественных и сертифицированных сырьевых материалов, а также обеспечения сторонних горных предприятий, в 2015 г. АО «МХК «ЕвроХим» завершило строительство нового, сверхсовременного завода по производству ПАС (рис. 1). В зарубежных источниках информации по данной тематике применяется также термин LDAN – Low Density Ammonium Nitrate (Низкоплотная Аммиачная селитра). Завод располагается на территории АО «НАК «Азот» (г. Новомосковск). Новый продукт является уникальным для российского рынка тем, что впервые в России была использована европейская технология фирмы Espindesa (Испания). Данная технология позволяет получать продукт, обладающий рядом важных преимуществ перед другими технологиями ПАС в России [3].
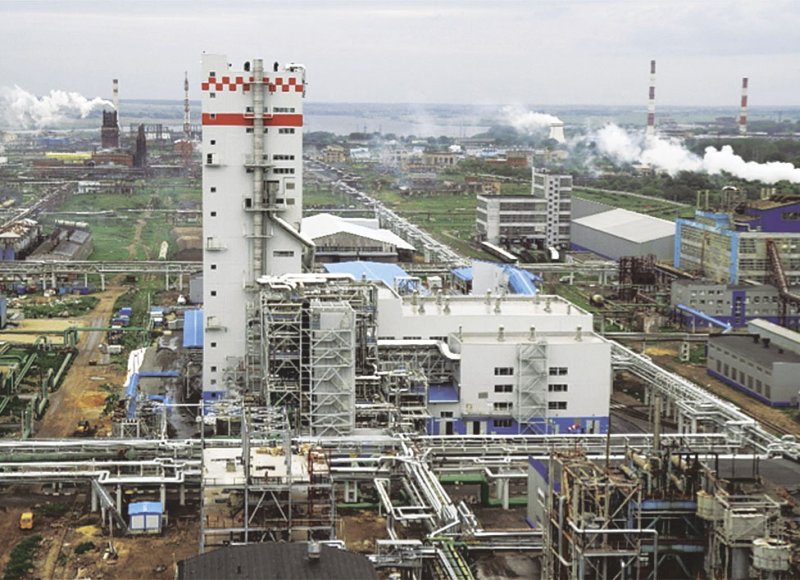
В части технологии производства пористой аммиачной селитры используется базовый подход по методу грануляции плава аммиачной селитры в башне приллирования [4]. Отделение производства аммиачной селитры (цех комплексных удобрений) АО «НАК «Азот» введено в эксплуатацию в 2015 г. Проект производства аммиачной селитры разработан по технологии фирмы «Espindesa» (Испания). Режим работы – непрерывный, круглосуточный (8000 ч в год). Проектировщик технологической части основного производства (оборудование) – АО «Хемопроект» (Чешская Республика). Проектировщик объектов инфраструктуры производства аммиачной селитры –ОАО «Тулагипрохим».
Цех комплексных удобрений (отделение ПАС) АО «НАК «АЗОТ» производит следующие виды аммиачной селитры:
- аммиачную селитру высокой плотности по ГОСТ 2–2013;
- пористую аммиачную селитру по ТУ 2143-073-05761643–2013.
Проектная мощность производства позволяет производить продукцию по следующей номенклатуре и объемам:
- 1800 т/сутки раствора аммиачной селитры, что составляет 900 т/сутки приллированной ПАС по ТУ 2143-073-05761643–2013 или АС высокой плотности по ГОСТ 2–2013 и 900 т/сутки раствора АС концентрацией 85% (в пересчете на 100%-ное содержание аммиачной селитры)
- или 600 т/сутки приллированной ПАС по ТУ или АС по ГОСТ 2–2013 и 1200 т/сутки раствора АС концентрацией 85 % (в пересчете на 100%-ное содержание АС).
Производство состоит из следующих основных стадий:
- подготовки сырья (аммиака, азотной кислоты, порообразуюшей и антислеживающей добавок);
- получения водных растворов аммиачной селитры путем нейтрализации азотной кислоты газообразным аммиаком под давлением;
- упаривания раствора аммиачной селитры до состояния высококонцентрированного плава;
- приллирования аммиачной селитры;
- сушки, классификации и охлаждения готового продукта;
- очистки отработанного воздуха башни приллирования, сушки и охлаждения;
- оборотного водоснабжения;
- кондиционирования готового продукта;
- фасовки, складирования, и погрузки готового продукта.
Краткое описание стадий технологического процесса производства ПАС [5]:
Принципиальная технологическая схема производства ПАС представлена на рис. 2.
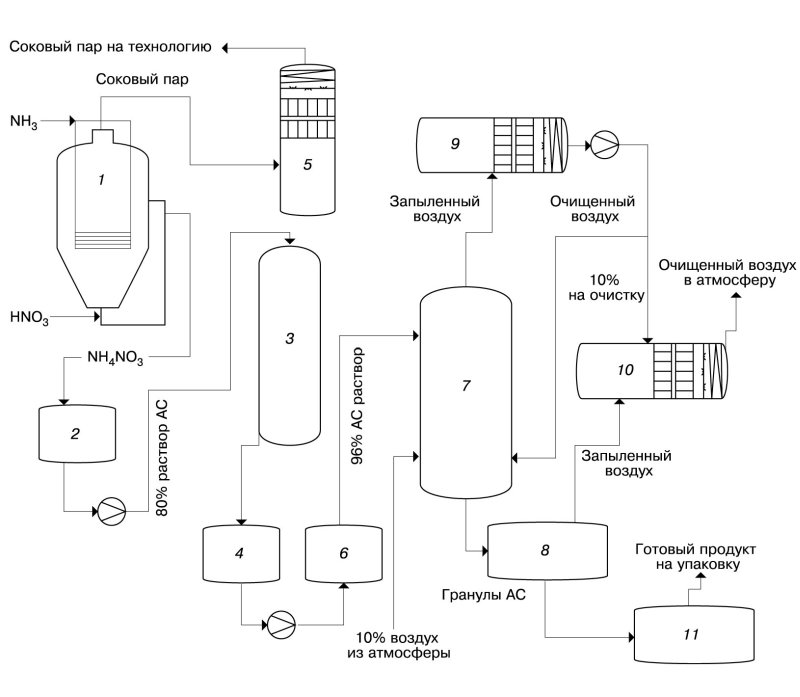
Аммиачная селитра (АС) производится путем нейтрализации под давлением неконцентрированной азотной кислоты газообразным аммиаком по следующей формуле:
NH3 + HNO3 → NH4NO3 + Q (1)
Реакция нейтрализации происходит в реакторе 1. Аммиак и азотная кислота взаимодействуют в реакторах согласно формуле (1), при этом реакция происходит в точном соотношении аммиака и азотной кислоты, что обеспечивает оптимальную эффективность реакторов. Возможна корректировка соотношения в зависимости от концентраций азотной кислоты и аммиака. Данная реакция нейтрализации – экзотермическая, при проведении которой выделяется большое количество тепла.
Раствор АС и соковый пар и полученный в результате реакции нейтрализации разделяются в реакторе. Полученный раствор АС с массовой долей не менее 80% NH4NO3 поступает в сепаратор раствора АС, где за счет снижения давления происходит вскипание раствора с повышением массовой доли NH4NO3 до 85%, и затем подается в сборник 2 неконцентрированного раствора аммиачной селитры. Соковый пар, который образовывается в реакторе и сепараторе, направляется на очистку в скруббер 5. Соковый пар после скруббера используется как теплоноситель для технологических нужд.
Из сборника неконцентрированного раствора аммиачной селитры насосом подается в выпарной аппарат 3, где происходит упаривание раствора до концентрации NH4NO3 не менее 96%. Выпарной аппарат пленочного типа работает под вакуумом. Концентрированный раствор/плав аммиачной селитры из сборника 4 насосом подается в бак с мешалкой 6, расположенный на башне приллирования 7, где смешивается с порообразующей добавкой (ПОД) и поступает на форсунки, обеспечивающие равномерное распределение капель плава АС по всему сечению башни. При свободном падении капли плава кристаллизуются с образованием приллов/гранул и с температурой около 80°С. поступают в сушильный барабан 8. Поток воздуха, отходящий из верха башни приллирования, очищается и охлаждается в скруббере запыленного воздуха 9 циркуляционным раствором аммиачной селитры, который улавлива-ет пыль. 90% очищенного воздуха возвращается в башню приллирования с помощью вентилятора, а 10% проходит дополнительную очистку в скруббере Вентури 10 и выбрасывается в атмосферу.
В сушильном барабане после удаления влаги и образования пор, приллы/гранулы аммиачной селитры поступают в классификатор, где удаляются крупная и мелкая фракция.
После отсева гранулы аммиачной селитры охлаждаются в аппарате «кипящего слоя» и поступают в финальный барабан 11, где на гранулы наносится антислеживающий реагент (АСР).
Готовый продукт по транспортерам поступает на стадию упаковки и отгрузки. Воздух на всех стадиях, где происходит образование пыли, очищается в скрубберах и выбрасывается в атмосферу.
Основные преимущества лицензионной технологии:
- цикличное использование тепла реакции (сокового пара);
- значительное снижение выбросов и стоков в окружающую среду;
- полная автоматизация производства на базе АСУ ТП;
- компактность и гибкость технологической схемы;
- возможность производства на одной установки ПАС и ГАС.
Основные контролируемые физические свойства ПАС по ТУ 2143-073-05761643–2013:
Суммарная массовая доля нитратного и аммонийного азота в пересчете на NH4NO3 в сухом веществе, % | Не менее 99,5 |
Массовая доля воды, определяемая методом Фишера, % | Не более 0,2 |
рH 10%-ного водного раствора, % | Не менее 4,5 |
Впитывающая способность по отношению к дизельному топливу, % | Не менее 11 |
Удерживающая способность по отношению к дизельному топливу, % | Не менее 10 |
Насыпная плотность, г/см3 | 0,7…0,8 |
Массовая доля нерастворимых в воде примесей, % | Не более 0,2 |
Рассыпчатость, без посторонних включений (сыпучесть) | 100% |
Основными характеристиками, определяющих эффективность применения ПАС в составе АС – ДТ, являются строение гранул со специфической «рыхлой» или «пористой» структурой и впитывающей способностью по отношению к дизельному топливу до 12–13% [6].
Впитывающая и удерживающая способность гранулы ПАС по отношению к дизельному топливу напрямую зависит от кристаллической структуры самой гранулы. Для детального изучения структуры и морфологии гранулы ПАС были проведены исследования в лаборатории электронной микроскопии Московского Политехни-ческого Университета. Исследования были выполнены с использованием автоэмиссионного сканирующего электронного микроскопа JSM-7500F (Jeol) в режиме детектирования вторичных электронов с использованием нижнего детектора (режим LEI) при ускоряющем напряжении 1 кВ.
Исследованию подвергались гранулы, полученные при разных параметрах технологического процесса с применением различного соотношения ПОД и АСР. Результаты исследования (рис. 3) подтвердили, что гранулы ПАС имеют сложную структуру и морфологию с наличием комплексной системы пор. Именно степень пористости позволяет грануле ПАС впитывать и впоследствии удерживать необходимое количество дизельного топлива для достижения требуемого стехиометрического соотношения таких ПВС, как смеси АС – ДТ [7].
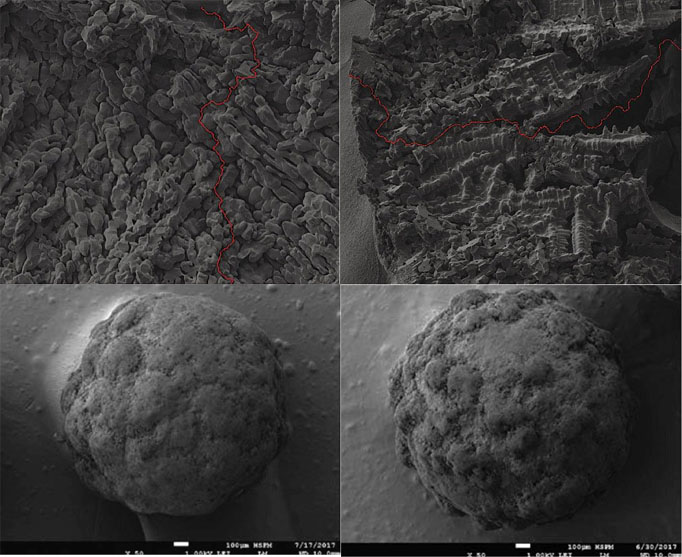
ПАС, выпускаемая по ТУ 2143-073-05761643–2013, имеет высокие показатели качества, а самое главное, не уступает по структуре и физическим показателям зарубежным и российским аналогам, что было подтверждено серией лабораторных и полигонных испытаний.
Список литературы
- Кук М.А. Наука о промышленных взрывчатых веществах. М.: Недра, 1980. 453 с.
- Черных В.А., Тогунов М.Б., Соснин В.А., Елин О.Л. Особенности применения пористой аммиачной селитры производства МХК «Еврохим» для изготовления ВВ//Научно-технический сборник «Взрывное дело» ¹115/72. 2016. С. 161–171.
- Ф.И. Галушко, А.С. Назаров. Пористая селитра компании «Еврохим» –залог повышения экономики и качества взрывных работ//Золото и технологии. ¹2. 2017.
- Олевский В.М. Технология аммиачной селитры. М.: Химия, 1978.
- Постоянный технологический регламент отделения производства аммиачной селитры цеха комплексных удобрений, ¹27. НАК «АЗОТ».
- Старшинов А.В., Костылев С.С., Куприянов И.Ю., Жамь-ян Ж., Р.А. Гильманов. Влияние структуры частиц аммиачной селитры на детонационную способность смесевых взрывчатых веществ//Горная промышленность. ¹5. 2017.
- Morhard, Robert C. Blasting/Explosives and Rock by Blasters Tool & Supply Co, 1987. ISBN 10: 0961628405/ISBN 13: 9780961628406.м